Desarrollo optimizado de una parrilla para bicicleta en material termoplástico
(Lea Artibai Ikastetxea)15/10/2003
Fases del proyecto
Tras la realización del estudio preliminar de parrillas existentes en el mercado, se analizaron los posibles materiales a utilizar en el diseño de plástico, teniendo en cuenta los requerimientos resistentes que debía soportar. En este caso se estipuló que la parrilla debía soportar un peso de 25 Kg con un índice de seguridad de n=2. Las parrillas se utilizan a la intemperie, por lo tanto el material debe soportar lluvia, barro, altas o bajas temperaturas, etc. A su vez debía poder ser coloreada para hacerla más atractiva. La pieza se diseñó pensando en un proceso de fabricación de inyección, por tratarse del método que mejor se adapta a las necesidades de procesado y menor coste.
Teniendo en cuenta estos datos se hizo una lista preliminar de posibles materiales especificando todas sus características para, de este modo, poder compararlas. Se decidió analizar las poliolefinas, poliamidas, policarbonatos y poliacetales, debido a su alto módulo de elasticidad, alta tensión de fluencia y posibilidad de coloreado.
Tras estudiar diferentes posibilidades se decidió trabajar con una selección preliminar de cinco materiales:
- PP 50% fibra de vidrio
- PA 66 35% fibra de vidrio
- PP 40% fibra de vidrio
- Poliaramida 30% fibra de vidrio
- PC 40% fibra de vidrio
En un principio, y debido sobre todo a su menor precio, se comenzó el estudio basándose en PP 40 por ciento fibra de vidrio:
PP 40% Fibra de vidrio | |
Módulo elástico (fibras orientadas longitudinalmente) | 5500 MPa |
Módulo elástico (fibras orientadas transversalmente) | 3000 MPa |
Coeficiente de Poisson | 0.45-0.48 |
Tensión a la rotura (= sf por comportamiento lineal) | 110 MPa |
Deformación a la rotura | 2% |
Contracción | 0.15-0.25% |
Densidad | 1.13 g/cm3 |
Tª de procesado | 120-160 ºC |
Diseños alternativos
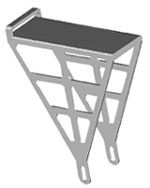
A la hora de realizar los análisis estructurales se estudiaron dos situaciones extremas. La primera es la correspondiente a la bicicleta en posición vertical. De este modo, toda la carga se aplica verticalmente en la superficie de la placa plana. Se aplicaron 50 kilogramos, los 25 requeridos multiplicados por el coeficiente de seguridad correspondiente (2).
La segunda situación es la que toma en cuenta los esfuerzos sufridos por la parrilla en el caso de que se tumbe la bicicleta con las alforjas cargadas en los laterales de la misma. En este caso se ha aplicado una presión de 25 kilogramos en uno de los lados de la parrilla.
En las siguientes figuras se pueden observar las tensiones equivalentes de Von-Mises resultantes en las dos posiciones estudiadas.
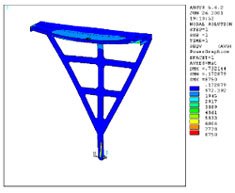
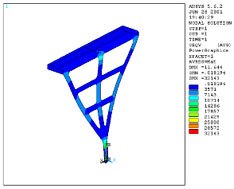
La tensión de fluencia del material empleado es de 110 Mpa, es decir, de 11.000 N/cm2. En la posición horizontal, la tensión de fluencia se superaba con creces. Por lo tanto era necesario realizar modificaciones en los diseños.
En las siguientes figuras se pueden observar alternativas de diseños posibles. El primero, con tirantes en doble T. El segundo, con tirantes en U y el último con nervios cruzados.
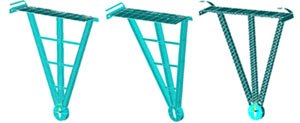
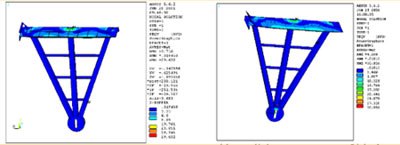
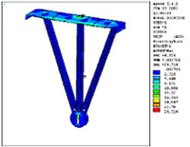
Como se observa en los gráficos, las tensiones resultantes más altas se encuentran en los amarres y en la zona donde se juntan los tirantes con la base superior de la parrilla. En el resto las tensiones son bajas, por lo tanto la utilización de nervios no parecía importante.
Atendiendo a los resultados, se optó por la parrilla de tirantes en U. Al haberse comprobado que las tensiones existentes eran bajas, se decidió modificar el diseño de la pieza y el material a utilizar.
Primeramente se realizaron unos orificios en la parte superior de la parrilla y se comprobaron los resultados.
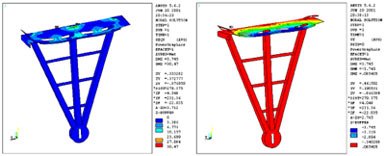
Al no detectarse problema alguno, y ver que aún nos encontramos lejos de las tensiones máximas admisibles del material, se decidió probar con otro material más barato, como el PP con talco en lugar de fibra de vidrio.
PP con 20% de talco | PP con 40% de talco | |
Módulo de elasticidad | 2700 MPa | 3200 MPa |
Tensión de fluencia | 19MPa | 29MPa |
Coeficiente de Poisson |
0.38 | 0.38 |
Deformación de rotura | 3% | 5% |
Sin embargo, con estos materiales se comprobó que la parrilla alcanzaba la tensión de fluencia. Por lo tanto se desecharon estos materiales y se volvió al refuerzo con fibra de vidrio.
Al comprobar los resultados se opta por reducir material y reducir el porcentaje de fibras de vidrio del PP. Se realiza un diseño reduciendo el espesor de los tirantes a la mitad y suprimiendo los tirantes transversales. Estos tirantes transversales sólo afectaban estéticamente a la parrilla, con lo cual prescindimos de ellos para reducir volumen y consecuentemente, peso.
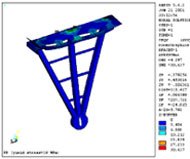
El siguiente paso consistió en reducir la cantidad de fibras del material. Se escogió un PP con 30 por ciento de fibra de vidrio. En la siguiente tabla podemos ver sus características:
PP 30% Fibra de vidrio | |
Módulo elástico (fibras orientadas longitudinalmente) | 4200 MPa |
Módulo elástico (fibras orientadas transversalmente) | 2500 MPa |
Coeficiente de Poisson | 0.44 |
Tensión a la rotura (= sf por comportamiento lineal) | 61 MPa |
Deformación a la rotura | 3% |
Contracción | 0.15-0.25% |
Densidad | 1.13 g/cm3 |
Tª de procesado | 200-280 ºC |
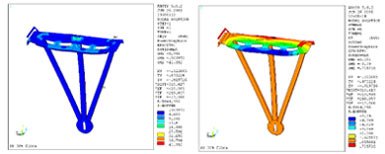
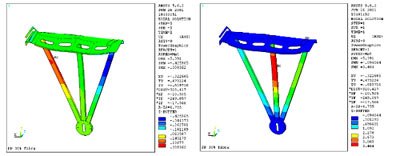
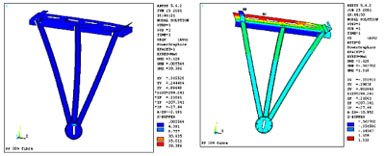
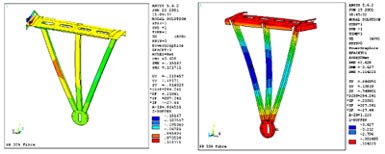
Estudio de procesabilidad de la parrilla diseñada
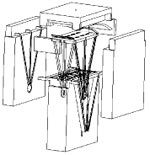
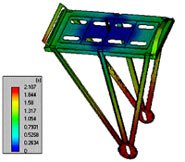
- Tiempo de inyección: 2.107 s
- Gradiente de temperaturas en masa al final del llenado: 16 ºC
- Presión de inyección necesaria: 60,84 MPa
- Tiempo de ciclo estimado (1ªfase + 2ªfase + enfriamiento): 70 s
- Fuerza de cierre requerida: 420 Tn
Dada la complejidad del molde necesario, se consideró oportuno buscar un diseño alternativo de la parrilla. Las tres opciones que se barajaron fueron:
- Moldeo de la pieza en partes separadas y la posterior unión de de las mismas por clipaje
- Moldeo de la pieza en partes separadas y la posterior unión por tornillos
- Moldeo de la pieza en partes separadas y la posterior unión por soldadura de ultrasonidos
De las tres opciones, se optó por la última, ya que una soldadura adecuada posee la misma resistencia que si la pieza fuese moldeada en una sóla. En la siguiente figura se puede apreciar cómo sería la disposición de los insertos para el moldeo de una de las dos partes de la parrilla.
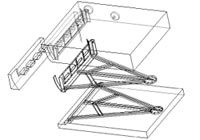