Sistemas HMI en la transformación y almacenaje alimentario
Un proceso, por bien pensado que sea, falla cuando se somete a manipulación por medio de operarios de frecuentemente baja cualificación. Si sumamos a esto la temporalidad de los puestos de trabajo, nos encontramos que hasta un 35% de las incidencias o factores causantes de un bajo ‘KPI’ (Key Performance Indicator) en máquinas y procesos podrían haberse evitado si los operarios hubieran entendido lo que “la máquina” les decía, o si la máquina hubiera entendido lo que el operario quería hacer. Y esto es básicamente un problema de comunicación entre el operario y la máquina. Los responsables de esta “traducción” de intenciones-órdenes, son los HMI. Pantallas pulsadores, indicadores, sustituyen ahora a los nonios, palancas y dispositivos mecánicos de antes. Todo debería ser más claro ahora, tenemos mejores medios, y más intuitivos. ¿Por qué entonces seguimos teniendo esta elevada incidencia de fallos de “comunicación hombre-máquina”?
La respuesta pasa por analizar los requisitos que debe cumplir un eficiente sistema HMI en general, y más específicamente para ser usado en la industria de transformación y almacenaje alimentario. Pero como preámbulo, digamos que no valen las grandes pantallas, ni los más detallados gráficos de proceso, si no han sido “ideados” para la mentalidad del operador. Muchas de las instalaciones y máquinas de procesado de alimentos son realizadas por empresas extranjeras, por personal que no habla nuestra misma lengua, y que se entiende menos aún con los operarios que manejan nuestras máquinas. Es muy frecuente encontrarse en conocidas empresas del sector con aplicaciones donde las pantallas o rótulos de selectores, tienen términos en inglés o alemán, y cuando están traducidas, lo están tan mal que desvirtúan su significado.
Requisitos de un sistema HMI dedicado a la industria alimentaria
Un eficiente sistema HMI debe cumplir con requisitos que en primera instancia podemos dividir en dos grandes grupos: factores constructivos y factores de seguridad.
En el primer caso, cuando hablamos de un sistema HMI para ser usado en industria alimentaria, hablamos de equipos instalados en ambientes donde las condiciones de higiene son controladas. El equipo debe ser por ello fácilmente limpiable, debe impedir la entrada a su interior de elementos que permitan la proliferación de bacterias. Su forma exterior debe diseñarse evitando en todo momento las superficies o rebordes horizontales, responsables a menudo de crear zonas de acumulación de líquidos y frecuente caldo de cultivo para microorganismos.
En su construcción, el acero inoxidable es el material más utilizado, aunque algunos polímeros se comienzan a utilizar con éxito. Existen además bastantes consideraciones sobre la porosidad de las superficies, juntas, tapas, grietas etc., que obligan a extremar los detalles constructivos.
Sumado a todo ello, estos sistemas han de soportar (durante el proceso de limpieza) la exposición directa a chorros de agua de alta presión y a detergentes clorados o ácidos.
Podemos resumir que, constructivamente, un HMI adecuado para ser usado en instalaciones alimentarias, debería ser una caja de material inoxidable, poco poroso, de superficies horizontales inclinadas, con un frontal liso, a ser posible sin salientes, y con una protección mínima grado IP65 (protegido a la entrada de sólidos, polvo y a chorros de agua en cualquier dirección).
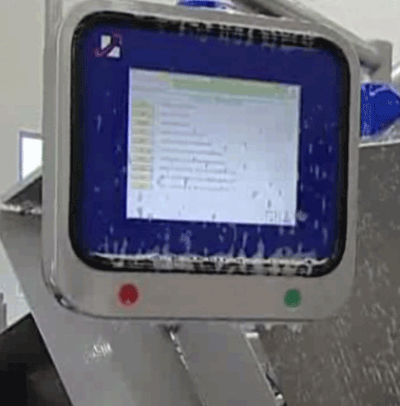
En cuanto a los factores de seguridad, la trazabilidad es un requisito cada vez más solicitado en todos los procesos, pero más aún en todos los relacionados con la alimentación humana. Cada vez más la sociedad requiere alimentos semi-elaborados, que tengan menos conservantes, y que se cocinen o se calienten muy rápido, y esto aumenta el riesgo de supervivencia o crecimiento de organismos peligrosos para la salud. Sonados son los casos de salmonelosis que se presentan en productos semi-elaborados o los casos de intoxicación por bromatos en agua mineral.
Aunque las medidas aplicadas al control de la producción son grandes, esto no hace más que reducir las posibilidades de error, por ello todo el sistema de producción debe ser “tolerante a fallos”. Y, aquí es donde el HMI juega su papel más importante, no solo el propio equipo, sino la aplicación misma, debe ser capaz de identificar qué lote fue producido, en qué condiciones, en qué horas, qué lotes de materia prima se usaron, qué operario intervino en el proceso, proporciones, parámetros físicos, etc. Toda esta información debe ser recuperable de forma eficiente, y debe almacenarse, como mínimo, un tiempo comparativamente grande respecto al ciclo de uso del producto elaborado (a su fecha de caducidad por ejemplo). Todo esto requiere del HMI, no solo características físicas y capacidades adecuadas, sino y más importante aún, de una aplicación claramente estructurada y basada en el concepto de trazabilidad.
Sistemas anteriores y actuales
Como citamos inicialmente, el HMI es el responsable del “diálogo” entre el operario y la máquina. Se hace uso básicamente de la imagen para enviar información al operador y el tacto para recibir las ordenes de este. Antes se usaban botoneras con rótulos, controladores con pulsadores discretos para determinadas magnitudes o palancas de accionamientos mecánicos con textos. Evidentemente todos los requisitos de higienización chocan con estas tecnologías.
Las pantallas táctiles son los elementos actualmente más vistos, con mucha o poca inteligencia, pantallas u ordenadores táctiles plasman en una imagen lo que quieren decir al operario, y este se expresa pulsando en determinados sitios de la pantalla.
No cualquier sistema de pantalla táctil es adecuado para el uso en la industria alimentaria. Según los requisitos expresados antes, un frontal liso es lo ideal, con lo que inicialmente descartamos ya a una buena parte de los existentes. Además, la mayoría de estas pantallas utilizan cristales táctiles de tecnología resistiva, que tienen por concepción un ciclo útil de pulsaciones o vida limitada.
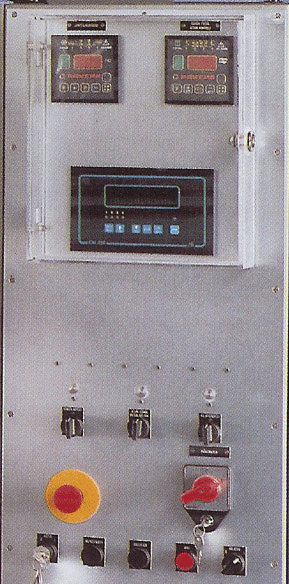
Sistemas HMI A&R
En base a los criterios anteriores, A&R desarrolla sistemas HMI mixtos, pensados específicamente para enriquecer el “diálogo” con el operario. Estos sistemas de concepción modular integran una pantalla táctil de 7, 10, 15 pulgadas o mayores, y además una pulsantería luminosa de tipo capacitivo, todo en un mismo frontal sin rebajes ni salientes. El uso de los pulsadores luminosos permite que el manejo más frecuente o prioritario del proceso-máquina, se haga por estos pulsadores, eliminando la necesidad de reiteradas pulsaciones en la pantalla y aumentando además la vida de la misma. Cada pulsador incorpora una banda luminosa exterior en amarillo, verde, rojo o azul, que puede rotar a derecha o a izquierda, rápido o lento, ponerse intermitente rápido o lento, indicar direcciones, quedarse encendido, etc.
También otorgan la posibilidad de integrar mandos pseudo-analógicos, como son los diales rotativos o lineales de activación capacitiva e iluminación. Estas posibilidades de visualización, son enormemente didácticas para el operario y reducen notablemente los riesgos de error de operación, al asociar estados luminosos a funciones o disfunciones de la máquina.
Las pantallas de estos HMI, se ofrecen en formato tradicional 4:3, y opcionalmente, en formato 16:9, lo que permite una reproducción eficiente de videos en formato original.
La retro-iluminación de las pantallas se hace por tecnología LED, lo que otorga un brillo superior, minimizando los problemas de falta de claridad (problema habitual en las pantallas tradicionales al envejecer la lámpara). De forma opcional estos HMI pueden incorporar lectores RFID, para una identificación rápida y segura del operario y partidas. Los sistemas HMI de A&R son personalizables y van dedicados a fabricantes de máquinas e instalaciones que busquen destacar en calidad e imagen.
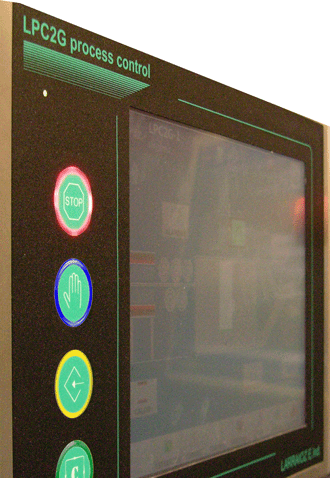
Aplicación y software
Como citamos inicialmente, no bastan grandes pantallas para hacer el proceso de comunicación eficiente. Las formas y la metodología a la hora de asignar imágenes y asociar símbolos a estados, hacen que una aplicación sea fácilmente entendible e intuitiva. Sumado a esto la posibilidad de visualizar videos de ayuda o asistencia en pantalla, otorgan al programador-integrador, las posibilidades de hacer un sistema amigable. La premisa de trazabilidad debe mandar sobre toda la aplicación. Desde un principio, pantallas o estados de manejo deben planificarse con accesos restringidos que se memoricen convenientemente. Por ello es bastante frecuente el uso de SQL, en registros y almacenamientos de estados e incidencias.
Pero todo ello, sin perder de vista que quien maneja la máquina no es el programador. Es habitual en los programadores-integradores, dar por sentado cuestiones básicas que en muchos casos no lo son para los operarios. En estos casos una técnica que está otorgando excelentes resultados, es integrar en la aplicación, un pequeño video de introducción, que aclare los conceptos con que fue creada la aplicación.
Futuro y tendencias
Esto es lo que viene:
· HMI cada vez más grandes y visuales, parece de momento el método mejor para la entrada de información al operador, pantallas e indicadores de estado más gráficos y luminosos.
· En el sentido opuesto, los pulsadores y mando de tipo capacitivo están cada vez más ayudando a los táctiles. Su diversidad y versatilidad crece exponencialmente.
· Táctiles con capacidad de pulsación en más de un sitio simultáneamente (doble touch o multitouch) otorgan ya enormes nuevos recursos para la entrada de datos y órdenes.
· Cámara integrada en el HMI, es otra forma de entrada de datos nada desdeñable, desde reconocimiento automático de operadores, hasta entrada de códigos gráficos interpretados por la misma cámara, o almacenamiento de imágenes y situaciones.