El hormigón y el mar
6 de mayo de 2011
El hormigón es uno de los materiales de construcción más utilizado en todo el mundo. Esto se debe a sus buenas propiedades estructurales, facilidad de fabricación y bajo coste. Sin embargo, hay algunas deficiencias importantes en las propiedades del hormigón, como la baja resistencia a la tracción y la porosidad. La aparición de poros internos en el hormigón se debe a la naturaleza del mismo. Se trata de un material que es producto directo de los procesos de hidratación que implican la reacción entre el agua y el cemento. En todos los casos, los restos de agua en el hormigón, una vez endurecido, se convertirán en poros de diversos tamaños, que en gran parte serán poros capilares. Estos poros están conectados entre sí, ya sea directamente o a través de los poros de gel.
Un volumen alto de poros determina una mayor capacidad de transporte de fluidos como el agua o gases, así como también por otras sustancias químicas normalmente transportadas por los anteriores, y que son potencialmente perjudiciales para el hormigón. De esta forma puede iniciarse un proceso más o menos lento de deterioro de las estructuras compuestas por este material.
La distribución del tamaño de los poros está relacionada fundamentalmente con el tipo y velocidad de los mecanismos de transporte y de fijación, en relación con el agua. El rango del tamaño de poro comprende varios órdenes de magnitud en la pasta de cemento, pudiendo clasificarse en poros de compactación, poros de aire ocluido, poros capilares y poros de gel [5].
El hormigón expuesto al agua de mar puede deteriorarse debido a varios factores: la agresividad química de los constituyentes de la misma sobre los productos de hidratación del cemento, en especial sulfato y magnesio, a expansiones debidas a la reacción álcali-árido, si hay árido reactivo, a la presión de cristalización de sales en el hormigón, a la acción del hielo en climas fríos, a la corrosión de las armaduras y a la erosión física debida al oleaje. Estas acciones producen un aumento de la permeabilidad del hormigón, retroalimentando el proceso [6].
La permeabilidad en el hormigón
La permeabilidad es la propiedad que mide la facilidad que tiene un material de ser atravesado por un fluido debido a la existencia de un gradiente de presión entre dos caras del mismo. En el caso del hormigón, y en el caso particular del ambiente marino, donde hay una gran concentración de agresivos químicos en medio acuoso, la permeabilidad representa un riesgo potencial de deterioro importante. Por lo tanto, con el fin de reducir la probabilidad de ser atacado por sustancias agresivas, se debe reducir la permeabilidad del hormigón, relacionada intrínsecamente con la porosidad del mismo. Esta deseada reducción se puede conseguir de varias formas, ya sea bajando el volumen total de los poros, o bien disminuyendo el volumen de aquellos poros de mayor tamaño (poros permeables). Los materiales suplementarios como el humo de sílice o cenizas volantes son muy bien conocidos por su capacidad de reducir de forma efectiva el volumen total de los poros.
En este sentido, la Instrucción Española de Hormigón Estructural EHE–98 [7] exige, para el ambiente marino, utilizar hormigones de relación agua/cemento inferior a 0,5, contenido de cemento superior a 325 kg/m3, el empleo de un cemento de características resistentes a este tipo de ambiente (MR o SR) y un recubrimiento superior a 45 milímetros. Los requisitos de otras normativas son similares o incluso más restrictivos. De esta forma se presupone un hormigón suficientemente impermeable y durable a las acciones agresivas del ambiente marino.
El objetivo del trabajo es estudiar con contrastación experimental cual es la variación de la distribución porosa que se produce en distintos hormigones al aportarle varias adiciones al cemento, así como investigar la influencia que la porosimetría tiene en el comportamiento del material frente al transporte provocado por un gradiente de presión.
Método experimental
Materiales utilizados
En este estudio los hormigones se fabricaron con dos tipos de cemento sulforresistentes: cemento Pórtland puro CEM I 42,5 R/SR (CPRS) y cemento con escoria de alto horno CEM III/B 42,5 L/SR (EAH). Estos dos cementos se utilizaron en la dosificación de cuatro hormigones, uno por cada tipo de cemento, más otros dos utilizando CEM I 42,5 R/SR (CPRS) junto con adiciones, una en la que el cemento fue sustituido parcialmente por 20% de cenizas volantes (CV) y otra en la que se utilizó un 10% de humo de sílice (HS), dentro de los límites que permite la normativa actual de hormigón estructural [7]. Las propiedades químicas y físicas de los materiales utilizados se muestran en la Tabla 1. El árido fino empleado fue arena silícea de río mientras que el árido grueso fue calizo machacado con un tamaño máximo de 20 mm. Con el fin de lograr una adecuada trabajabilidad se incorporó a la mezcla superplastificante de alto rendimiento (Sika Viscocrete 3425).
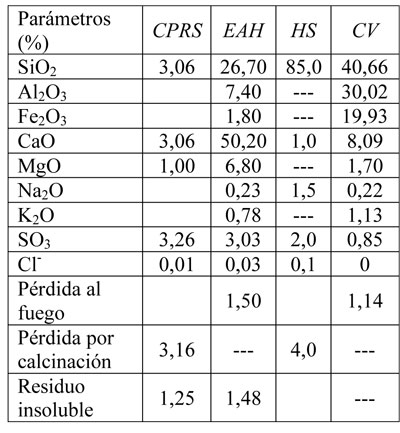
La dosificación y preparación de las probetas
Los hormigones se dosificaron utilizando el método de la Peña. En todas las mezclas, se utilizó un contenido de cemento de 380 kg/m3 y una relación agua/cemento 0,45. En el caso de los hormigones con adición de humo de sílice y cenizas volantes se siguieron las recomendaciones de la EHE-98 [7] para las adiciones, sustituyendo el contenido de cemento C por C+KF, así como la relación A/C por A/(C+KF), siendo F el contenido de adición y K es el coeficiente de eficacia de la misma. Como coeficiente de la eficacia utilizado ha sido K = 2 para el humo de sílice y K = 0,3 para las cenizas volantes. La relación agua/material cementicio resultante es baja, y para conseguir una adecuada consistencia se añadió superplastificante en una cantidad variable entre 0,6 y 2%, según el caso. En la Tabla 2 se muestran los detalles de las dosificaciones establecidas en el plan de ensayos.
Para la fabricación de todas las mezclas de hormigón se siguió el procedimiento descrito en la norma ASTM C 192 [8]. Para cada tipo de hormigón se hicieron cuatro amasadas, y de cada una de ellas se moldearon 14 probetas cilíndricas de 150 milímetros de diámetro y 300 de altura.
Resultados
Características del hormigón en estado fresco
La Tabla 3 muestra la consistencia, el contenido de aire ocluido y el peso específico de cada una de las cuatro amasadas de hormigón. Los valores de la consistencia son indicativos de la trabajabilidad de la mezcla. Debido a la baja relación agua/material cementicio, y especialmente en el caso de sustitución de parte del cemento por adiciones, las mezclas salían muy secas, por lo que en distintas pruebas de laboratorio se aportó un aditivo superfluidificante hasta ajustar las dosificaciones con una adecuada trabajabilidad. La reducción de trabajabilidad por aportación de adiciones fue más pronunciada en la amasada de CPRS+ 10% HS que en el resto, por lo que hubo que incorporar en este caso mayor cantidad de superplastificante. Esto se debe a la mayor superficie específica de las partículas de humo de sílice, respecto a la de las cenizas volantes o a las mismas partículas de cemento.
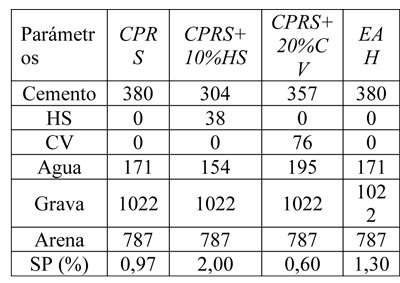
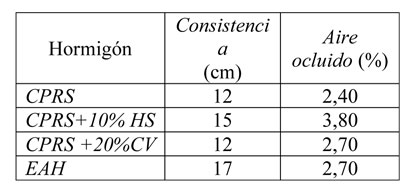
Resistencia mecánica
En la Figura 1 se muestra el desarrollo de la resistencia a compresión de los distintos hormigones a las edades de 7 y 28 días. El ensayo se realizó según la norma UNE-EN 12390-3:2003. En los 7 primeros días se observa en la amasada con humo de sílice un desarrollo de resistencia a compresión sensiblemente mayor que en el resto de amasadas. Esto indica que el humo de sílice mejora la resistencia a compresión a edades tempranas, dato que está en consonancia con las propiedades que universalmente se le atribuyen a esta adición. Esta mejora además se mantiene a los 28 días ya que sigue siendo mayor la resistencia de la mezcla con humo de sílice, seguida por el hormigón con escoria de alto horno. La explicación radica en la actividad puzolánica de estas adiciones. En la mezcla de cenizas volantes se observa un desarrollo resistencias más lento que en cualquier otra, debido a que la actividad puzolánica de las cenizas volantes es lenta. Es importante señalar que un período de 28 días puede que no sea suficiente para el desarrollo de la máxima resistencia para mezclas con adiciones minerales, en comparación con el cemento de control (cemento Pórtland puro), especialmente en el caso de las cenizas volantes.
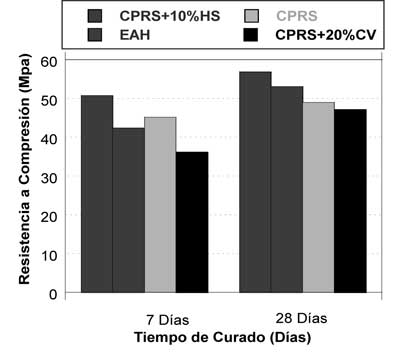
Profundidad de penetración de agua bajo presión
Con objeto de comprobar la facilidad de introducción de agua en los distintos hormigones se realizó el ensayo de profundidad de penetración de agua bajo presión sobre dos probetas por dosificación según la norma UNE-EN 12390-8:2001. Según la EHE [7] la profundidad media de penetración de agua debe ser menor o igual a 15 m, a la vez que la profundidad máxima de penetración de agua debe ser menor o igual a 25 m. En todos los ensayos se cumplieron estas limitaciones, por lo que todos los hormigones se pueden calificar de suficientemente impermeables de acuerdo con dicha norma.
Los resultados del mismo se presentan en la Figura 2. En todos los casos, la profundidad de la penetración de agua en las probetas fabricadas con humo de sílice y EAH fue más baja que en el resto. Los hormigones estudiados se agrupan en su respuesta a la penetración de agua bajo presión del mismo modo que lo hacen para la resistencia a compresión.
Permeabilidad al oxígeno
Para comprobar la permeabilidad de los hormigones a gases se realizó el ensayo de permeabilidad al oxígeno según el método recomendado por la Rilem. De acuerdo con el mismo se prepararon dos lonchas cilíndricas de 150 milímetros de diámetro y 50 de altura. Estas lonchas se cortaron de la parte superior y de la parte inferior de una probeta de 150 milímetros de diámetro y 300 de altura con el fin de ser capaces de apreciar posibles diferencias debidas a la compactación dentro de la misma probeta. Los valores medios resultantes del ensayo sobre probetas de 3 meses de edad se muestran en la Figura 3. De acuerdo con el método Rilem Cembureau9, el coeficiente de permeabilidad al oxígeno, debe ser no mayor de 3 x 10-16 metros cuadrados, lo cual se cumple también en todos los casos Los resultados obtenidos en este ensayo siguen una tendencia parecida a los de penetración de agua bajo presión, siendo el hormigón con adición de humo de sílice el que dio el menor coeficiente de permeabilidad.
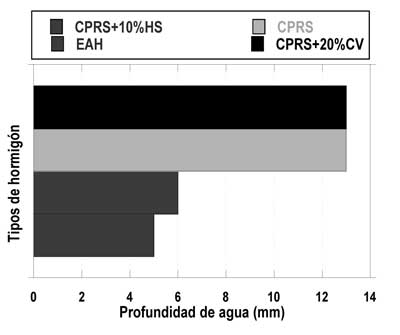
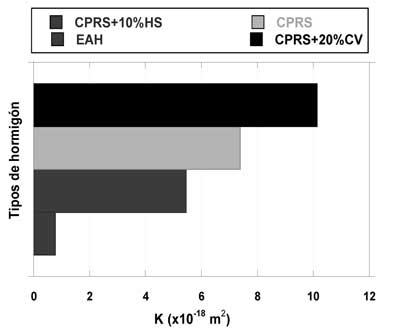
Estructura porosa
La porosidad total, así como la distribución de tamaño de poro se ha estudiado por porosimetría de intrusión de mercurio (MIP) en un rango de 0,006 a 175 µm, que nos permite evaluar los poros de aire y capilares. Los poros capilares presentan tamaños comprendidos entre 30-0,002 µm [9]. En la zona superior de este rango, los poros influyen negativamente en la resistencia mecánica del material y en la durabilidad. Los poros interlaminares o de gel CSH son los menores de 18 A, este tamaño se encuentra fuera de la posibilidad de valoración con porosímetro de mercurio y sólo se pueden estudiar por isotermas de adsorción-desorción de gases. En cualquier caso su presencia no es negativa ni para la resistencia, ni para la durabilidad del material.
Para el ensayo se prepararon muestras con un peso comprendido entre 2 y 4 gramos, que fueron secados al vacío para desgasificar la estructura porosa. Estas muestras fueron mantenidas en estufa a una temperatura de 40 ºC hasta el momento de ensayar.
Los resultados a 28 y 90 días se muestran en las Figuras 4, 5, 6, 7 y 8 para todos los tipos de hormigón estudiado. Como se puede apreciar, en todos los casos, al aumentar el tiempo de hidratación, disminuye la porosidad total, a la vez que la distribución porosa se desplaza hacia valores inferiores de diámetro del poro medio.
La porosidad total, en la dosificación que contenía cenizas volantes, es sensiblemente superior que en todas las demás amasadas. Esto se debe al retraso en la reacción puzolánica que va cerrando los poros con el tiempo. En la amasada con adición de humo de sílice se observa la menor porosidad total, junto con el menor diámetro de poro en todas las edades. En la Figura 9 se relacionan los valores de la porosidad total y la resistencia a compresión a 28 días.
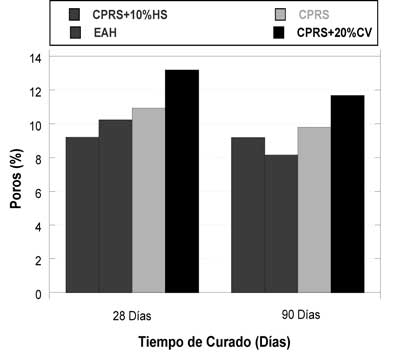
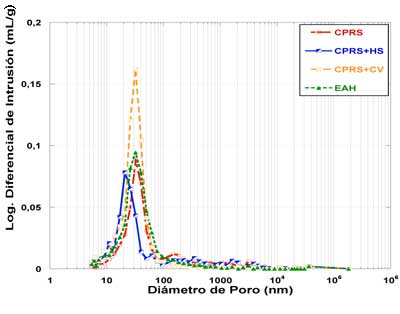
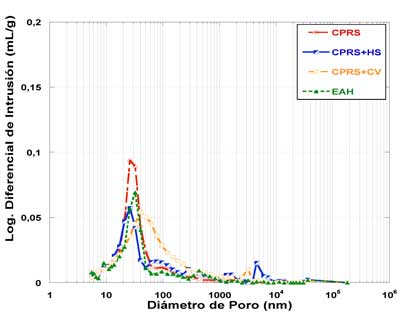
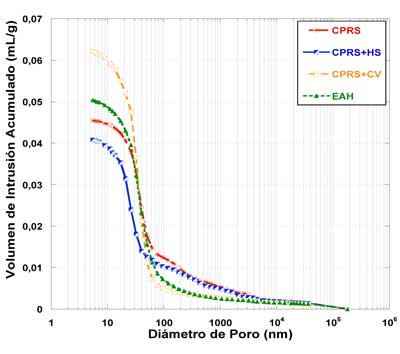
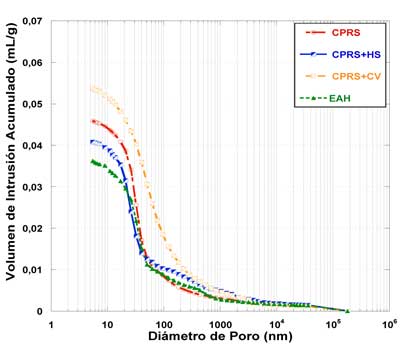
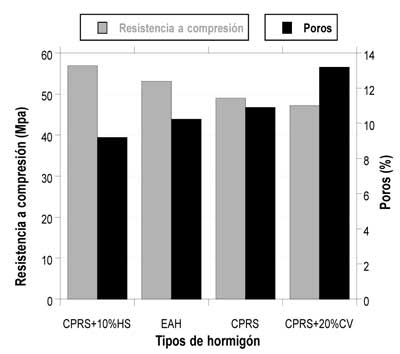
Conclusiones
Comparando los resultados obtenidos con los distintos tipos de hormigones utilizados en la experimentación, se ha encontrado que la dosificación que contiene un 10% humo de sílice ha dado una indudable mejor resistencia que los demás. Esto era esperable a priori, sin embargo, haría falta profundizar en la investigación de otras características mecánicas, resistencia a tracción y módulo de elasticidad, que en principio no es tan evidente que sigan la misma tendencia.
La distribución de tamaño de poro en los hormigones cambia con el tipo y el contenido de cemento, relación agua/cemento, tipo de aditivos y adiciones, así como con la compactación del hormigón. Las Figuras 5 y 6 muestran las curvas de intrusión de mercurio de las mezclas estudiadas y la derivada del volumen de intrusión respecto al diámetro, respectivamente. En casi todas las mezclas (CPRS+10%HS, CPRS y EAH), la gran mayoría de los poros están concentrados en un estrecho intervalo de diámetros comprendidos entre 6 y 50 nm, 7 y 95 nm, y 6 y 95 nm respectivamente, mientras que en la mezcla de CPRS+20%CV el intervalo de diámetros se incrementa, dando lugar a una distribución de poros más amplia, comprendida entre 11 y 120 nm. Con la utilización del humo de sílice decrece el volumen de intrusión de mercurio según se puede observar en las Figuras 5 y 6. Este dato está en concordancia con los resultados de menor permeabilidad tanto al agua como gases que se han obtenido con la mezcla compuesta por humo de sílice. Ahora queda investigar si esta mejora que introduce el humo de sílice se plasma también en una mayor resistencia al ataque químico debido a los agresivos presentes en el agua de mar.
Es importante destacar que con el humo de sílice se obtiene a las primeras edades una estructura muy compacta, que no sufre modificaciones importantes cuando avanza el grado de hidratación. No es así en el caso de las otras adiciones donde las reacciones puzolánicas cambian significativamente la distribución porosa del material.
La Figura 9 muestra la relación entre la porosidad total del material y la resistencia a compresión. En todos los hormigones estudiados se observa una tendencia inversa en estas variables acorde con los datos existentes en la bibliografía.
Con base en los resultados obtenidos hasta la fecha en la campaña experimental, se puede afirmar que tanto la resistencia como el comportamiento del hormigón frente al transporte de fluidos vienen determinados por la estructura porosa del material. Este trabajo se engloba dentro de un estudio más amplio que tiene como objetivo valorar la influencia de la composición del hormigón frente al ataque de los iones presentes en el agua marina, identificando y evaluando las posibles sinergias existentes entre ellos. Atendiendo a esta aplicación y considerando que el contacto con el medio agresivo se produce a las pocas horas de la fabricación del material se podrían resumir las siguientes conclusiones:
- Los datos obtenidos en todas las dosificaciones estudiadas muestran la relación directa entre la capacidad de transporte del material y la distribución porosa del mismo.
- Los resultados observados para los hormigones estudiados se agrupan en dos comportamientos diferenciados. Los hormigones CPRS y CPRS + 20%CV, presentan un comportamiento similar, menores resistencias, y mayor permeabilidad a los fluidos. Por otro lado los hormigones CPRS + 10%HS y EAH presentan un comportamiento también análogo, con mayor resistencia y menor capacidad de transporte de fluidos.
- El coeficiente de permeabilidad al oxigeno resulta más sensible para caracterizar las diferentes dosificaciones estudiadas en función de su capacidad de transporte.
- Es muy importante destacar la distinta evolución de la distribución porosa con la hidratación, en los hormigones estudiados. Una selección basada solo en el comportamiento del material a los 90 días podría determinar graves perjuicios en durabilidad, al permitir la penetración inicial de los agresivos.
Agradecimientos
Los autores agradecen al Ministerio de Fomento y al Ministerio de Educación y Ciencia las ayudas económicas concedidas a través de los proyectos MFOM-2004/9 y BIA2005-09250-CO3-02, así como a través de una beca FPU para Safwat Mahmoud Abdelkader.
Bibliografía
[1] Shannag, M. J., Hussein, A. S. ‘Sulfate resistance of high-performance concrete’, Cement & concrete composites, 25, pp. 363-369 (2003).
[2] Lee, S. T., H. Y., Swamy, R. N. ‘Sulfate attack and role of silica fume in resisting strength loss’, Cement & concrete composites, 27, pp. 65-76, (2005).
[3] Ganjian, E., Pouya, H. ‘Effect of magnesium and sulfate ions on durability of silica fume blended mixes exposed to the seawater tidal zone’, Cement and concrete research, 35, pp. 1332-1343 (2005).
[4] Sezer, G., Ramyar, K., Karasu, B., A. B., Sezer, A. ‘Image analysis of sulfate attack on hardened cement paste’, Materials and Design, 29, pp. 224–231, (2008).
[5] Menéndez, E. ‘Procesos expansivos del hormigón: Ensayos árido-álcali, ataque por sulfatos y ataque por hielo-deshielo. Sistema de prevención y actuaciones’, Instituto de ciencias de la construcción Eduardo Torroja (CSIC), Curso de estudios mayores de la construcción.
[6] Bermúdez M.Á., Alaejos, P. ‘Permeabilidad a los cloruros del hormigón armado situado en ambiente marino sumergido’, Ingeniería de construcción, 22 Nº 1, pp. 15-22 (2007).
[7] EHE-98 ‘Instrucción Española de Hormigón Estructural’, Ministerio de Fomento, (1998).
[8] ASTM C 192 ‘Making and curing concrete test specimens in the laboratory’.
[9] Lorenzo, M. P. ‘Influencia de dos tipos de cenizas volantes españolas en la microestructura y durabilidad de la pasta de cemento hidratada’, Universidad Complutense de Madrid, Facultad de Ciencias Químicas, España, (1993).