A printer 3D with industrial parameters
Traditionally englobadas inside the Rapid Prototiping (RP), the technicians of ‘additive manufacturing' (AM) can classify in function of the initial state of the material used for the manufacture of the prototype: based in liquids, solids or dust. The systems RP whose initial state of the material is the liquid achieve through curing (cured) that the liquid was converted to solid state, like sucede in the Stereolithographt Apparatus (SLA). The systems RP based in solids engloban all the technicians with materials of game in shape of thread, roll, plates, dust, etc. Technical as for example the selective sintering by laser (Selective Laser Sintering or SLS), use a laser to melt small grains of plastic, ceramic, glass, metal and other materials in layers of a structure 3D.
Together with the evolution of the materials employed and the reduction of his cost, the vencimiento of some patents related with these technologies contributes to the big expansion that these technologies are experienced in the actuality. From among them, the impressesion 3D, directly related with the technology FDM (Fusion Deposition Modeling), is doing tremendously popular. To this contributes the movement ‘RepRap' that, in addition to keeping a code of open control for the controllers, preconiza the principle of ‘self construction' through the cual a printer can build constitutive pieces of a new printer.
Industrial requirements for a printer 3D
One of the limitations of the technology FDM is that it needs a very precise calibration so that the result of the pieces was the wished. The most popular solutions (RepRap) base in technology of control in open loop, through the employment of motors step by step, that can affect to the quality to measure that produce small changes in the calibration.
Besides, since these machines build pieces through the superposición of successive layers, an error in an inferior layer inevitably will propagate in the following layers. The result of a failure of characteristic calibration is the unwanted inclination of a vertical face. This problem involves the frequent need to refuse pieces badly built and the recalibración of the machine through the construction of pieces of proof. All this supposes a cost of material, power and time. Besides, with areas of work and high speeds increases the incidence of the propagation of errors of positioning been due to defects of calibration.
These were, is essence, the requirements of the printer 3D designed by the professor and student of the Master of Mecatrónica of the University of Vigo to participate in the first contest MachineStruxure of Schneider Electric. The scope of the project includes the mechanical design, electrical and of the software for a printer of pieces of plastic PLA in three dimensions. The aim is to create an able machine to realizar pieces of big size without defects caused by the propagation of errors of paths and with a consumption of time the most adjusted possible to the new dimensions. This machine has to solve the problematic of calibration and give-calibration through the utilisation of technology of positioning in enclosed bow that translates in the employment of servomotors. The use of servomotors, besides, favourable the fast positioning, what allows to reduce time to the hour to manufacture several pieces in a same batch in a clearly industrial use. Of this way, pretends reduce the generation of pieces refused and of pieces manufactured for assistance in the phases of recalibración. All this redunda in a saving of costs of material and of consumption of power and time. Besides, the printer 3D is conceived to allow the exact and automatic calculation of the cost that supposes the realisation of each piece.
Structure of the machine
From the mechanical point of view, the machine is a configuration of three axles cartesianos (Schneider Electric), more a fourth synchronous axis with regard to the speed of advance and that commissions of the extrusion of the thread of plastic.
The structure cartesiana realizar movements interpolados in the axles XYZ. This structure commissions to position and move the extrusor of the material, that consists of an axis and a generator of heat (resistance) controlled to keep a constant temperature (with the purpose of the smelting of the thread of plastic, 210º for the thread of PLA). Said thread of plastic is rolled up in a coil and is unrolled by the action of a fourth engine (Figure 1).
Each one of the axles XYZ are moved by servomotors (Schneider Electric) that are connected to the corresponding ServoDrives. The extrusor uses a servomotor type ICLA (engine with servo integrated ). All this connected through CanMotion and CanOpen to a controller LMC058 of Schneider Electric. They complete the hardware the devices for the thermal sensors control of the extrusor, a measurer of electrical consumption connected through Modbus, and a tactile screen for the IHM of control of impressesion.
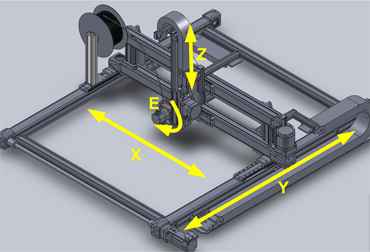
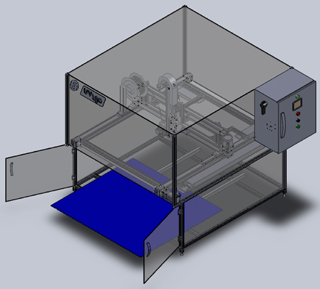
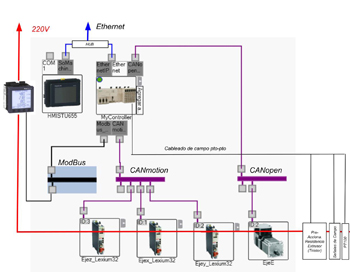
Control of the machine
With this configuration implements a manufacture or impressesion in layers (layer manufacturing), that consists in going depositing the thread melted in a series of parallel layers. Each layer realizar through movements interpolados 2D (with the axles X and And) of the extrusor, of such form that realizar paths that delimit the outline of this piece in this height Z and of paths in the interior with a form and a spaced that depends on the robustness that want to him give to this layer. Typically, for example, the first layers and last have a density of 100% whereas the rest espacian of agreement to an initial parameter of factor of robustness or density wished, so that the interior of the piece tends to structure in shape of cells to end to save in material and time of impressesion.
The majority of the machines of RP work with designs in shape of files STL (Triangulation tessellated). A model STL contains a group of triangular flat surfaces. The big majority of systems CAD 3D commercial are able to convert models of solids in this format. From this representation, other algorithms convert the design in layers (Slice) parallel horizontals (horizontal sections), and linear paths to visit the surface in code G (ISO). Applications like ‘Cure' (of free access), allow to realizar this type of conversion.
This file of paths in code G is finally transferred to the controller. This controller will be the attendant to execute the interpolation cartesiana in three axles XYZ according to the paths described in the file. Besides, the controller synchronises the movement of the fourth axis (axis of the extrusor) that moves to constant speed depending on the path that was executing in each moment.
So much this program of control like the interface IHM have developed with the platform SoMachine of Schneider Electric. The system complete with an application of configuration and management for PC, quese connects road OPC with the controller. In this PC is, besides, the application of preprocesado to convert the design 3D in a code executable ISO.
Energetic efficiency
One of the requirements of the machine is the register of the consumption of time, power and prime matter that consume in the realisation of each piece with two aims: can realizar a ‘turnover of the manufacture of piece' adjusted to these parameters, and can analyse the result that, on these parameters, have the decisions taken in the phase of design and manufacturing, for like this can decide the design of optimum piece having the criterion of cost of manufacture.
Therefore, in addition to the register of the time employed and of the material consumed, will register the energetic consumption total along the manufacture of a piece, and for this employ the FB's of the bookshop of Energetic Efficiency of Schneider Electric. The values accumulated of all these parameters put to disposal of the PC of design and management at the end of the process. With the resources of energetic efficiency provided by the surroundings of development, no only is possible to obtain a value of the total consumption, but also access to the individual consumption by axis and by path. This is definitely the functionality that, from the university perspective, will be more interesting since it will be the one who use in the frame of the line of investigation of the Department of Engineering of Systems and Automatic of the University of relative Vigo to ‘new strategies and algorithms of control for the impressesion 3D'.
The contest
In 2013, Schneider Electric Spain summoned the 1ª Competition MachineStruxure, allocated to students and professors of engineering of Spanish universities. It proposed the design of a machine employing the new tool of development of systems of automation SoMachine of Schneider Electric and, between other things, valued the employment of the resources for available energetic efficiency through said surroundings of development. Finamente, from among eleven proposals resulted chosen the project ‘Design of a printer 3D with industrial parameters', signed by July Garrido Fields and Jaime Meadow Cambeiro, professor and student respectively of the master of mecatrónica given in the School of Industrial Engineers of Vigo.
The contest, endowed with a prize of 15.000 euros in equipment for the implantation of a classroom ‘MachineStruxure', and 4.000 euros to disposal of the winning team to implement, in accordance with Schneider Electric, the winning solution. This already has translated in the classroom MachineStruxure of the Department of Engineering of Systems and Automatic of the University of Vigo, that has been instrumented with eight places formed, respectively, by a controller LMC058 and a HMI (and his corresponding licences SoMachine), in addition to a configuration cartesiana of axles Schneider with the corresponding servomotors and servodirives (three LXM32). These axles constitute the plant of proof for the eight places, but are also the base on which will build the printer with the rest of the endowment of the prize, in what they already are working jointly the winning team and Schneder Electric Spain.
The project ‘RepRap'
The project ‘RepRap' (of replicating rapid prototyper) proposes the open development of printers 3D that they can print the majority of his own components. All the designs and software generated by the project are distributed freely. His capacity of autorreplicación is contributing to his popularity, since these printers can print mechanical elements to generate to his new time printers.
The project was cream in 2005 in the University of Bath (United Kingdom) of the hand of the professor Adrian Bowyer. This year set up the corresponding blog, and from 2007 began to implement the first printers. Since these have not left to grow and extend. The printer RepRap uses the technology FFF (Fuser Filament Fabrication), where a thread of plastic (ABS or PLA, for example) is heated until his melting-point in a cabezal or ‘extrusor', conforming the piece layer after layer. Like platform of control employs the popular Arduino with additional plates to control the motors step by step and the extrusor.
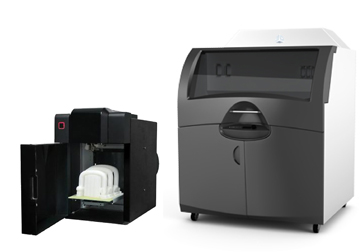
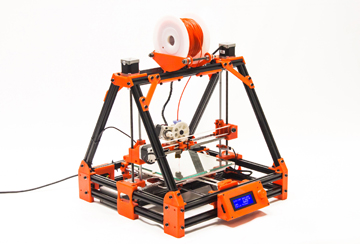
Appears 5: Printer 3D RepRap.
References:
- Protectia, patents and marks. Art. ‘Caducous the key patent for impressesion 3D'. Francesca Nandolini. March 2014
- Machine design. Art. ‘How designer can get the most out of additive manufacturing'. Ziad About, vice-president and general director of Quicpart Solutions. October 2013.
- RepRap. Place official:
http://reprap.org/wiki/reprap