Proceso robusto de mecanizado de piezas de turbomaquinaria
La industria aeronáutica es un sector en rápida expansión y de gran peso en la economía mundial. Así lo confirman las predicciones realizadas sobre el mercado aéreo para las próximas décadas. Se prevé que en las próximas dos décadas el tráfico aéreo de pasajeros anual y transporte crezca en torno a un 5%. Esta demanda va a requerir la fabricación de más de 30.000 aviones de transporte de pasajeros y alrededor de 800 de carga. El coste de estos pedidos alcanza los 5.200 millones de dólares. Casi un 40% de estos nuevos aviones de pasajeros se utilizaran en la renovación de la actual flota de aeronaves.
Las compañías fabricantes de aviones se enfrentan al continuo reto de ofrecer aeronaves cada vez más avanzadas. Por un lado se busca reducir los costes de fabricación, mejorar la aerodinámica y la utilización de componentes más ligeros, robustos y que faciliten la reparación y el mantenimiento. Por otro, se requieren mejorar la eficiencia en el consumo de combustible y reducir las emisiones y ruidos. Todo esto implica una enorme inversión en investigación y desarrollo en toda tecnología relacionada con el diseño, funcionamiento y fabricación de las aeronaves.
Los 10 mandamientos del mecanizado de la pieza rotativa
- Quién controle el proceso global en la etapa de CAM será el que domine el mercado
- Mecanizar con el flanco reduce tiempo
- Evitar las vibraciones no es cuestión de suerte ni de máquina, es de condiciones de corte
- Titanio e Inconel son muy diferentes, sólo les une el mecanizado y su habitual negocio
- La fresa cónica es la solución para muchas geometrías
- Medir en máquina es la llave de la fiabilidad
- Alta presión o criogenia, la robustez de lo probado frente a las posibilidades del frío
- El CAM debe ayudar al usuario, en geometría simulación y en fuerzas de corte
- El primero que integre fuerzas de corte en el CAM tendrá un gran negocio
- Los grandes del mundo ya están en esta línea…desde hace años
Entre los diferentes campos de investigación se encuentra el motor del avión. El turbofan es el tipo de motor más extendido en las aerolíneas actuales. Se trata una variación del motor de turbina de gas básico. El turbofan se caracteriza por disponer de un ventilador, denominado fan, en la entrada del motor. Del aire entrante en el fan parte penetra en el núcleo del motor (aire primario) y el resto se deriva por un conducto concéntrico con el núcleo del motor (flujo derivado o secundario). En los motores con alto índice de derivación (high by-pass ratio), el flujo derivado llega a producir hasta el 80% del empuje del motor. Este tipo de motores consume menos combustible, por lo que produce menos contaminación, y reduce el ruido ambiental debido a su mayor masa de flujo y menor velocidad total de salida.
La función del motor es obtener la propulsión necesaria utilizando el aire como fluido de trabajo. Este objetivo se consigue aumentando la energía cinética o velocidad del flujo de aire que pasa a través del motor. A lo largo del motor principal el aire pasa por diferentes etapas antes de ser expulsado. Inicialmente el aire a presión atmosférica pasa a través de un proceso de compresión. Posteriormente en la cámara de combustión se aumenta su temperatura a presión casi constante. Los gases resultantes de la combustión se expanden en la turbina y por último son expulsados otra vez a la atmosfera obteniéndose un flujo propulsor. Además parte de la energía generada en la expansión de los gases es convertida en energía mecánica por la turbina, haciendo girar los ejes que mueven los compresores y el ventilador.
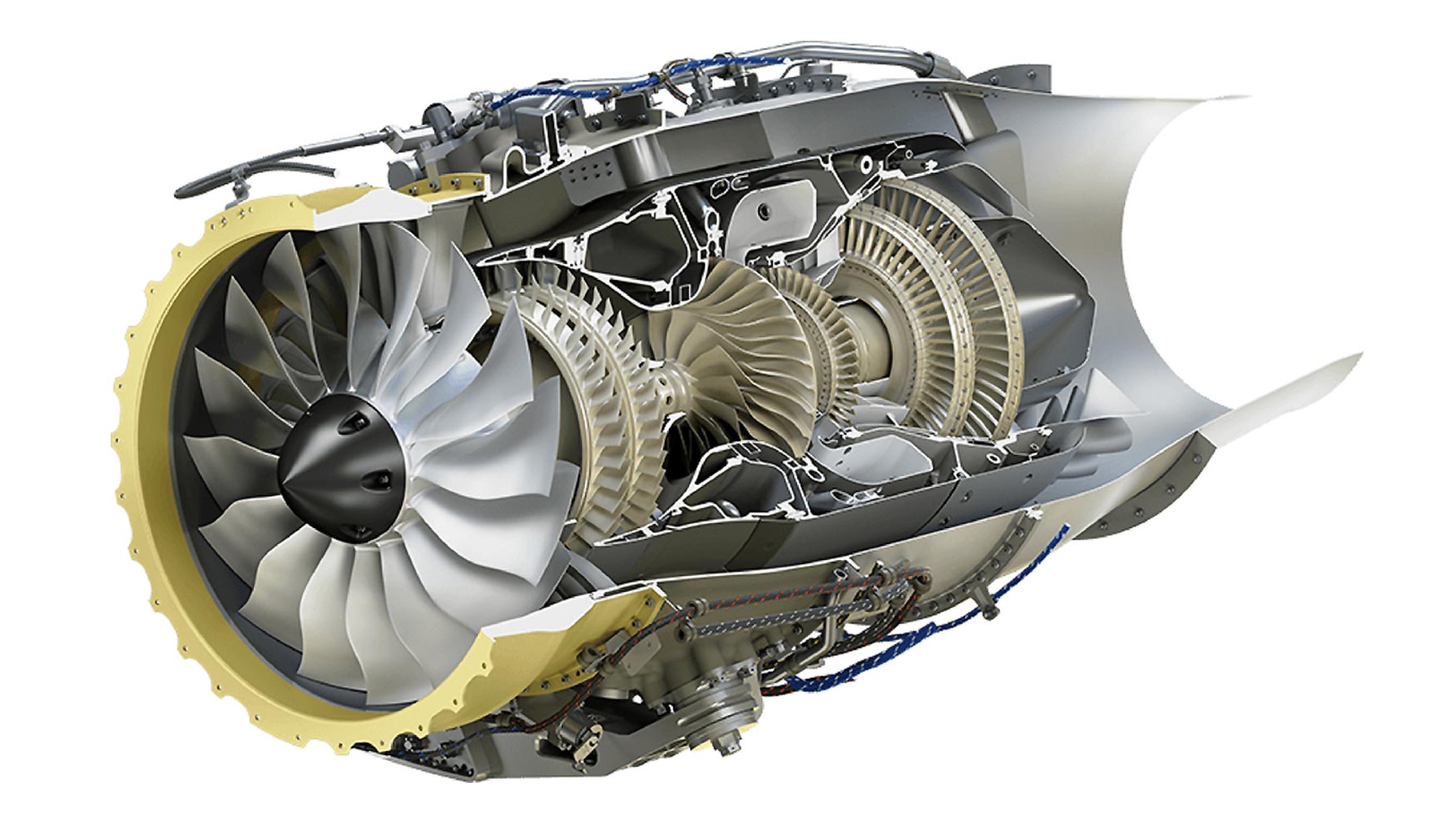
El diseño y fabricación de los álabes y conductos por los que circula el flujo de aire es de gran importancia. Cualquier interferencia en el flujo puede provocar una pérdida de la eficiencia o vibraciones debido a turbulencias en el flujo. Estas vibraciones a su vez pueden ocasionar roturas en los componentes. Los rotores de álabes integrados, denominados integrally o integrated bladed disc (IBR), están siendo cada vez más utilizados en los compresores de los motores aeronáuticos. Se tratan de discos rotativos con álabes, fabricados en una sola pieza. Se elimina por tanto la necesidad de ensamblar álabes al disco, disminuyendo el número de componentes y elementos de unión. De esta manera se elimina una posible fuente de iniciación de fractura por fatiga en las uniones. Las principales ventajas de los IBR-s respecto a los rotores ensamblados, son la reducción del rozamiento, el aumento de la eficiencia de compresión y la reducción de peso.
Entre este tipo de componentes podemos destacar como elementos de referencia los blisks (bladed disk) e impellers. Los blisk se utilizan en los compresores axiales. Los compresores de flujo axial son unidades multietapa compuesta por discos de álabes rotativos intercalados con vanos estáticos. Por otro lado los compresores centrífugos son unidades de compresión compuestas de una o dos etapas empleando impellers. Los impellers son discos rotativos de compresión que cambian la dirección del flujo de axial a radial. Los motores formados por compresores axiales son capaces de producir un mayor empuje comparado con los centrífugos para una misma área frontal. Además en un compresor axial existe la posibilidad de aumentar la presión alcanzada añadiendo más etapas. Por estos motivos la mayoría de los motores en la actualidad se diseñan con compresores axiales. Por otro lado los centrífugos son utilizados en motores más pequeños debido a su robustez.
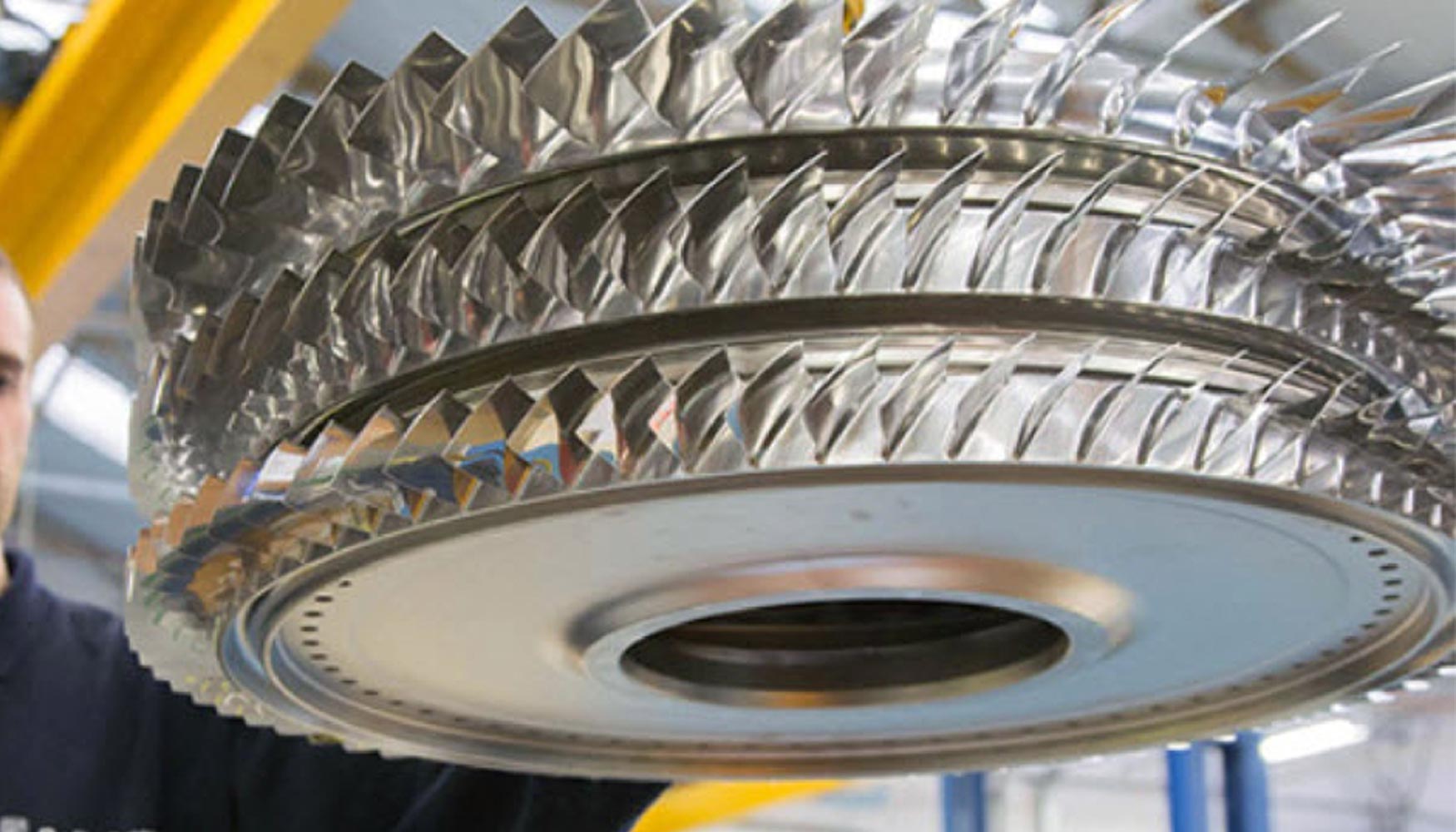
Mecanizado de cinco ejes de rotores de álabes integrados de motor aeronáutico
En los últimos años los rotores de álabes integrados de motores aeronáuticos se han convertido en piezas de referencia del mecanizado en cinco ejes. La fabricación de componentes como blisks e impellers de manera fiable y eficiente sigue siendo un campo con amplio desarrollo y mejora. Estos turbocomponentes están diseñados para obtener una transformación de los parámetros de flujo lo más eficiente posible. De este diseño se obtiene superficies complejas, para cuyo mecanizado se requiere una gran flexibilidad en la orientación de la herramienta de corte.
A esto hay que añadir que los materiales utilizados para fabricar estas piezas son de muy altas prestaciones. Sus propiedades mecánicas se han de mantener a las elevadas temperaturas, presiones y los ambientes corrosivos a los que son sometidos en el motor. Por lo tanto, la alta resistencia en estos materiales, no se ve afectada prácticamente por el aumento de las temperaturas durante el mecanizado. Esta combinación de alta temperatura en la herramienta y altas fuerzas de corte, da lugar a una baja maquinabilidad. A esto hay que añadir que los materiales típicamente utilizados, como las aleaciones de Titanio y Níquel, son materiales de poca conductividad térmica. Por lo tanto las altas temperaturas generadas en el mecanizado no se disipan a la pieza, sino que se concentran en la zona de corte. La demanda actual en el sector aeronáutico se centra en el diseño de aleaciones avanzadas que mejoren las propiedades mecánicas a mayores temperaturas. Esto se debe a que a mayor temperatura alcanzada en la cámara de combustión, mayor es la expansión realizada por los gases y por tanto mayor es la eficiencia del proceso.
Todo esto implica que el proceso de creación de operaciones de mecanizado conlleve complejos cálculos y se hagan necesarios diferentes análisis y simulaciones del proceso para optimizarlo. Para mecanizar álabes integrales de rotores, como los impellers o blisks, se parte de una preforma de revolución. En esta preforma se realizan las operaciones de desbaste, semiacabado y acabado mediante operaciones de fresado hasta obtener la pieza final.
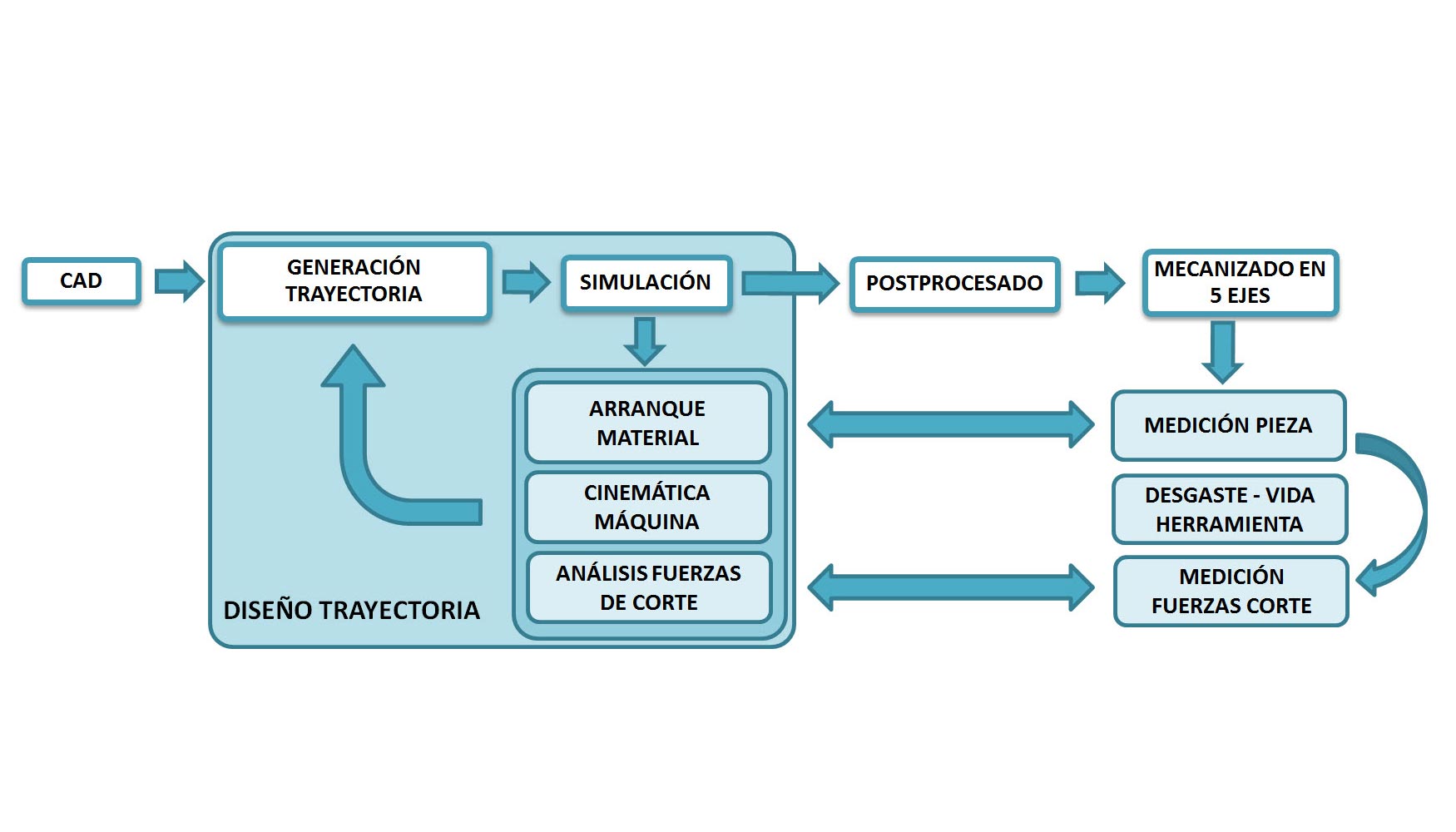
El proceso de mecanizado en cinco ejes de piezas integrales de turbinas parte de una geometría CAD 3D que ha sido diseñada para maximizar el rendimiento del proceso. Conocidos el material inicial, los utillajes necesarios y las herramientas de corte a utilizar se inicia el diseño de trayectorias de mecanizado con la ayuda de un software CAM. El proceso de obtención de una trayectoria óptima requiere de un proceso cíclico de dos subprocesos. Por un lado se genera la trayectoria de la operación configurada por el usuario. Posteriormente se ha de simula y analiza la trayectoria generada para verificar su idoneidad o en caso contrario modificar la operación.
En las últimas décadas se han desarrollado un gran número de investigaciones para desarrollar algoritmos de generación de trayectorias y posicionamiento de la herramienta con una orientación libre de colisiones. En la actualidad se pueden encontrar numerosos softwares CAM comerciales para el diseño de trayectorias de mecanizado en 5 ejes de superficies complejas. Debido a la complejidad y demanda de piezas como blisks e impellers, muchoss de estos softwares han ido incluyendo módulos específicos para generar operaciones típicas de mecanizado para este tipo de turbocomponentes. Estos módulos destacan respecto a las operaciones multieje generales, en la facilidad con la que se define la geometría de pieza y se pueden generar operaciones complejas. Sin embargo todavía están en proceso de mejora y de aportar mayor flexibilidad de configuración al usuario.
Selección de estrategias de mecanizado
Un aspecto importante del proceso de diseño de trayectorias son las estrategias de desbaste y acabado que se van a utilizar. Entre las estrategias utilizadas para realizar el desbaste se puede destacar el ranurado ('slot milling'), el fresado trocoidal y el fresado en penetración ('plunge milling', 'dive milling') (ver figura 2). El ranurado es una estrategia donde la profundidad radial es igual al diámetro de la herramienta. Se utiliza como estrategia inicial de corte con los patrones habituales de trayectorias tipo zig o zig-zag. En estos casos se toma como referencia las intersecciones con la geometría a determinados niveles para generar las trayectorias curvas entre los álabes. Lo habitual es que estos niveles sean superficies paralelas a una de las superficies de revolución de la pieza o una interpolación entre ambas. La superficie de revolución interior se denomina hub y la exterior shroud. A pesar de la alta tasa de arranque de viruta de esta estrategia, se generan altas fuerzas de corte radial. Para reducir los esfuerzos sobre la fresa se puede dividir el ranurado de un nivel en varias pasadas.
El fresado trocoidal consiste en la combinación del movimiento de avance de la herramienta con el de trayectorias circulares. La principal ventaja respecto al 'slot milling' es la generación de menores fuerzas de corte radiales, pudiéndose utilizar velocidades de corte y profundidades de corte axial superiores. Por contra, el diseño y generación de trayectorias trocoidales en cinco ejes adaptándose a la geometría de la pieza requiere un mayor coste. Además, exige mayores capacidades dinámicas de la máquina herramienta. Por último en el fresado en penetración o plunge milling el mecanizado se realiza con el filo secundario de la fresa, en vez de realizarse con el filo principal. En esta estrategia las fuerzas de corte predominantes son en dirección axial. En general, el 'plunge milling' es un método alternativo cuando no se puede utilizar fresado lateral debido a la vibración. Por ejemplo, si el voladizo de herramienta es elevado, en caso de ranurado profundo o en general si la estabilidad es deficiente.
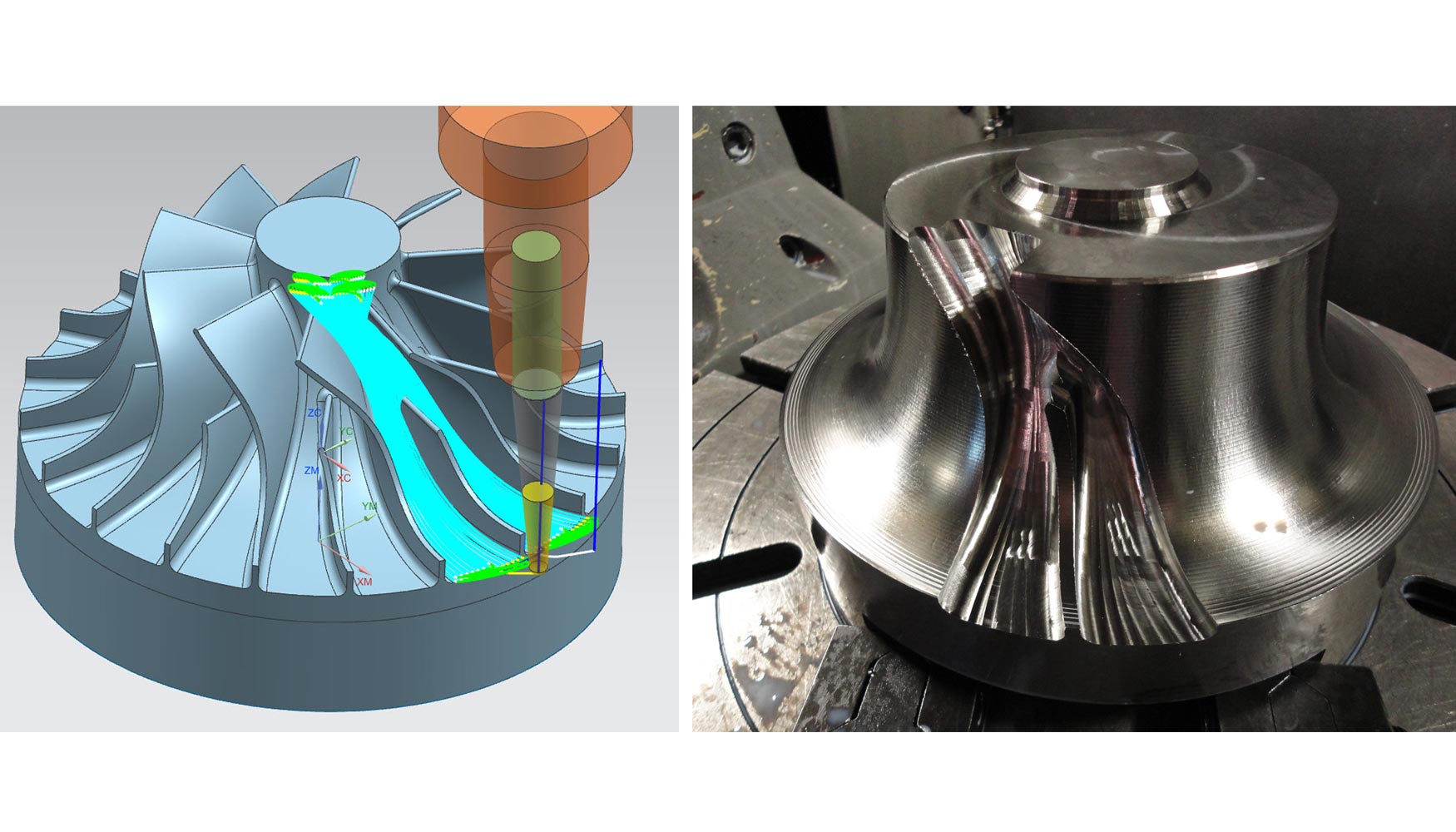
En cuanto a las operaciones de acabado, las técnicas de fresado se diferencian en función de la parte de la herramienta que realiza el contacto con la pieza durante el mecanizado. Podemos destacar las técnicas de 'point milling' y 'flank milling'. En el 'point milling' el contacto durante el arranque de viruta se realiza en un área cercana a un punto. En el 'flank milling' el arranque de material se realiza a lo largo de una arista del contorno de la herramienta.
El 'flank milling' es una estrategia enfocada a operaciones de semiacabado y acabado, en superficies de álabes generadas por la revolución de una línea alrededor de un eje (single-curved surface) o generadas por el barrido de una línea (isoparamétrica) a través de dos curvas guía (superficie reglada o ruled surface). Diversas referencias y datos experimentales muestran que la estrategia de 'flank milling' disminuye el tiempo de mecanizado y mejora la calidad superficial respecto al 'point milling'. Por otro lado, a mayor contacto entre pieza y herramienta, se requieren mayor potencia, estabilidad, evacuación de viruta y capacidad de movimiento de la máquina, por lo que la operación de 'flank milling' puede quedar limitada por estos aspectos.
Sin embargo el desarrollo de trayectorias óptimas para el uso del fresado con el flanco sigue siendo el objetivo de diferentes investigaciones. Se trata de un problema de alta complejidad, ya que no toda superficie reglada es posible mecanizarla de manera perfecta. Esto se debe a que se distinguen dos tipos de superficies regladas, las desarrollables, en las que el plano tangente a la superficie es el mismo en todos los puntos de una misma isoparamétrica, y las no desarrollables en caso contrario. En el caso de las superficies no desarrollables cuanto mayor es el ángulo entre el plano tangente en los dos extremos de la isoparamétrica y mayores son los diámetros de herramienta utilizados, mayor es el error de interferencia con la pieza cometido, siendo geométricamente imposible mecanizar de forma perfecta la superficie. Por lo tanto, aunque con el fresado en point milling se necesitan tiempos de mecanizado superiores para acabar un alabe, no tiene las limitaciones respecto a la geometría del álabe que tiene la operación de 'flank milling'. Además las fuerzas de corte generadas son inferiores, un aspecto importante a considerar con materiales de baja maquinabilidad.
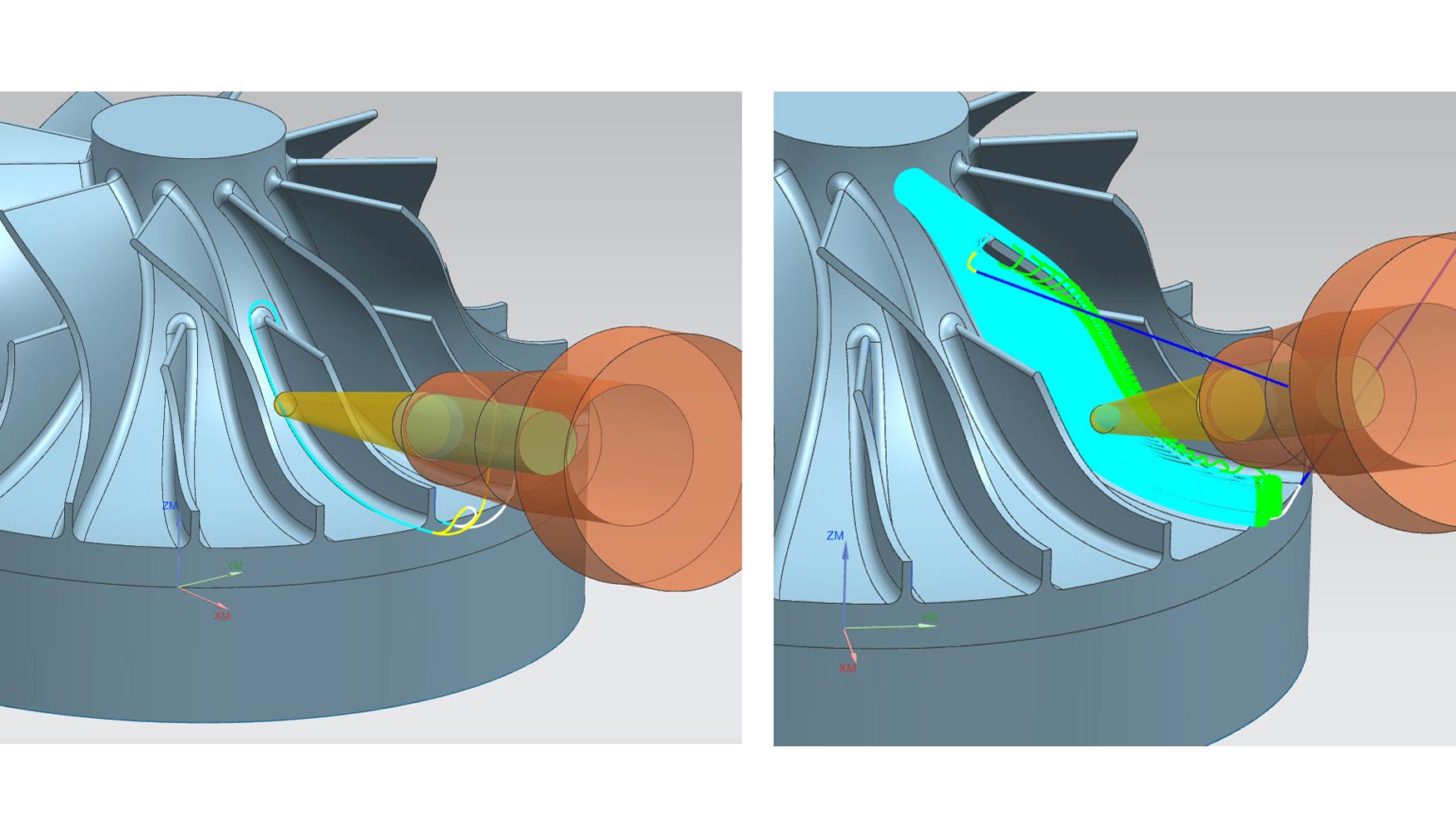
Simulación de trayectorias de mecanizado
Una vez generada la trayectoria se ha de simular el mecanizado antes de ejecutar las operaciones en máquina. Un primer paso de cara a detectar posibles modificaciones en la operación es la simulación de arranque de material. Esta función incorporada en los softwares CAM, permite visualizar en un entorno CAD 3D el movimiento de la herramienta a lo largo de la trayectoria y cual va siendo el material arrancado. Dentro de esta simulación, una opción muy útil de verificación es el análisis de demasías de material respecto del sólido objetivo final. Mediante esta opción tras simular el arranque de material, se pueden observar las zonas más conflictivas en las que queda sobrespesor o en las que se ha mecanizado más de lo deseado.
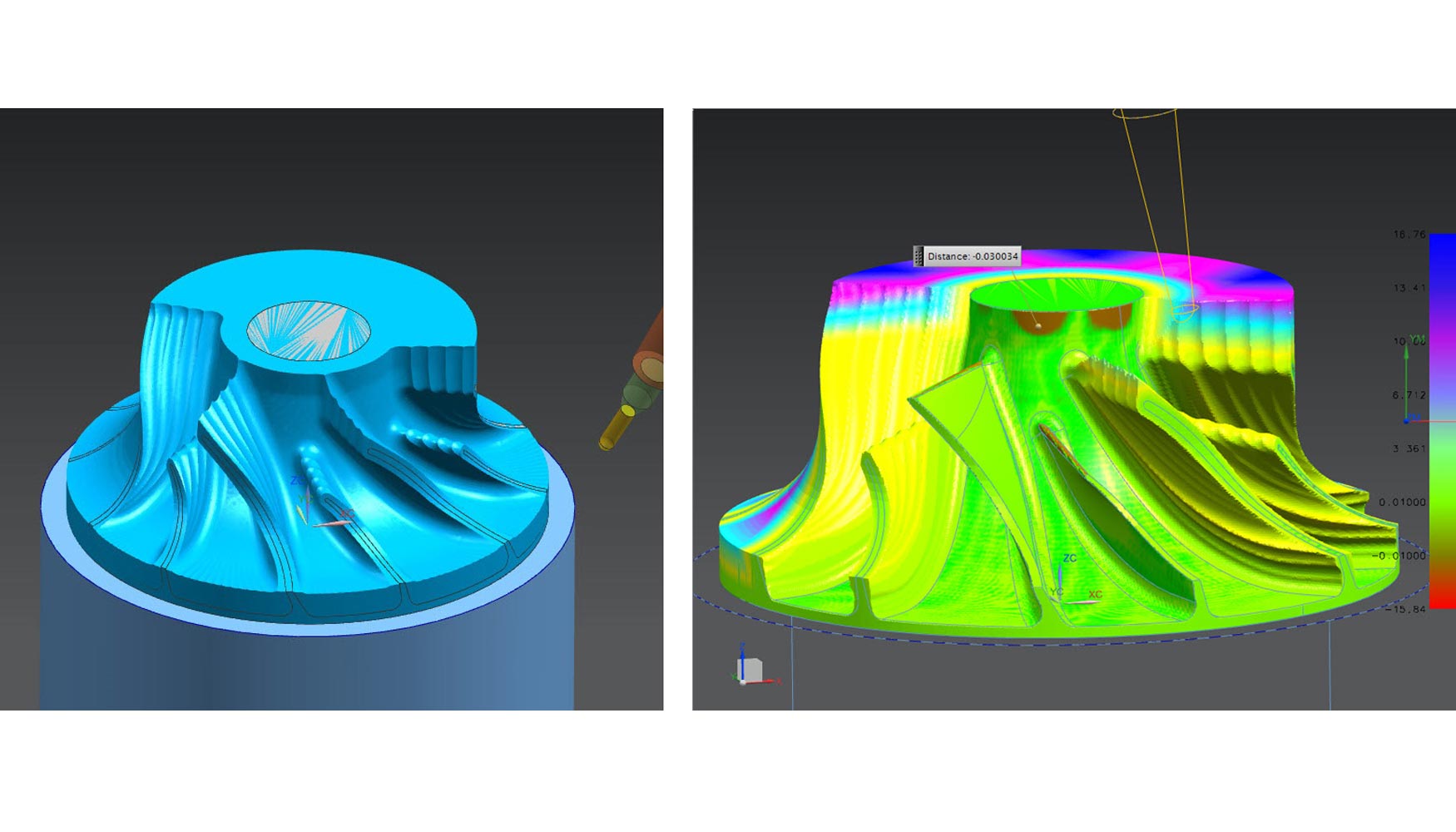
La siguiente etapa dentro de la simulación de la operación es detectar posibles colisiones con los diferentes elementos del centro de mecanizado. Para ello es necesario disponer del CAD 3D de los elementos la máquina y utillajes. Además se requiere configurar la cinemática del ensamblaje 3D de la máquina. De esta manera los grados de libertad y el movimiento simulados en una operación de mecanizado, se corresponden a los que se producirían en la máquina real. En el mercado se pueden encontrar software específico para realizar este análisis y algunos softwares de CAM también incluyen la simulación del mecanizado con el ensamblaje de la máquina.
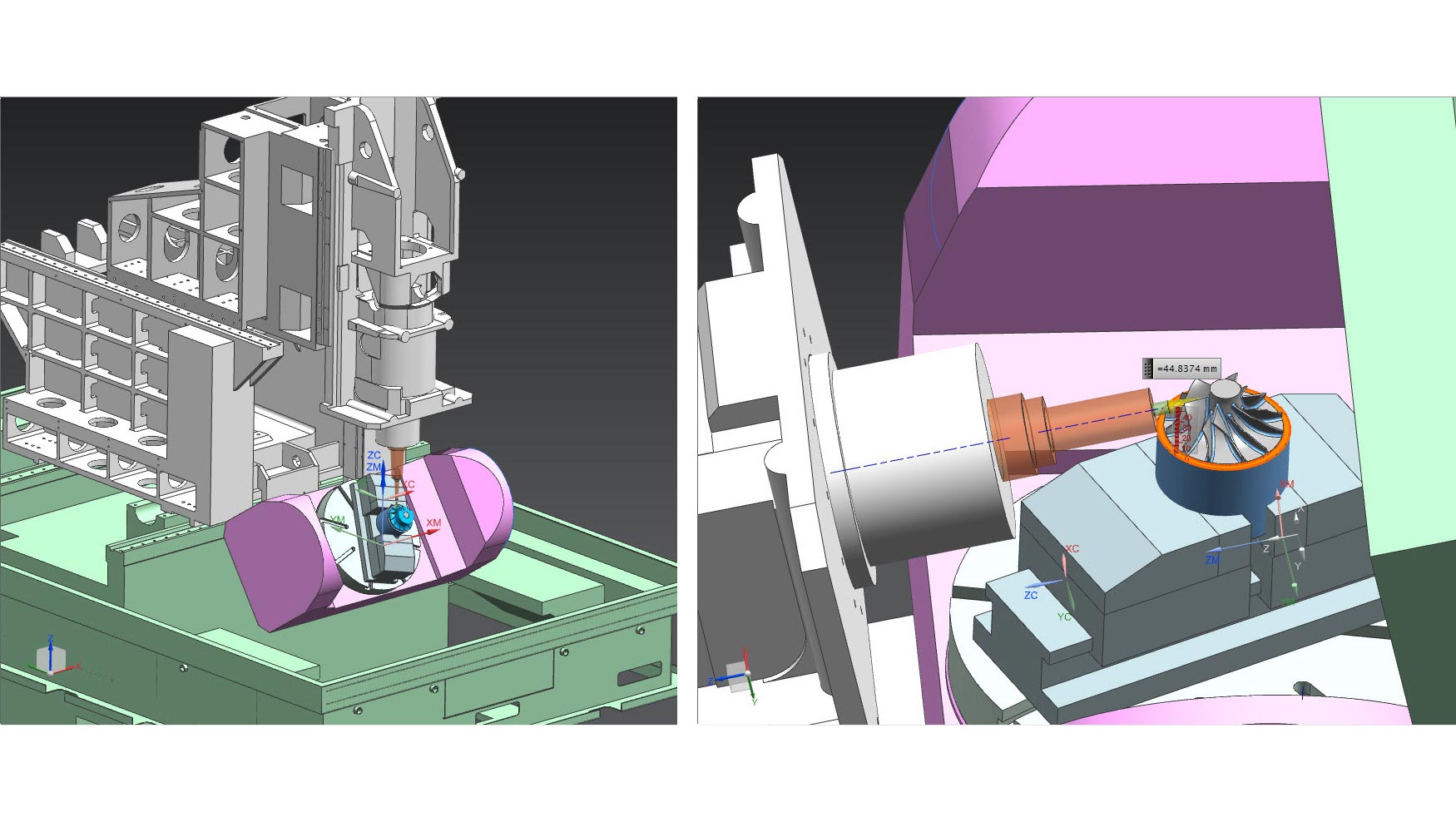
Sin embargo, a pesar de que estos análisis geométricos y volumétricos son de gran ayuda, los softwares CAM comerciales habituales no permiten apoyarse en análisis mecánicos. Al no tener en cuenta los esfuerzos mecánicos que se están produciendo en el proceso de mecanizado, pueden obtenerse trayectorias que siendo correctas desde un punto de vista geométrico, den lugar a altas fuerzas de corte y vibraciones, y por tanto mala calidad de acabado superficial, altos desgastes en la herramienta e incluso daños en la máquina. El estudio de las fuerzas de corte y el modelado de estas es una de las áreas más clásicas de la literatura científica asociada al mecanizado. Se han desarrollado diferentes modelos de fuerzas que permiten simular el mecanizado de piezas en cinco ejes como blisk e impellers, con el objetivo de completar mediante un análisis mecánico el diseño de operaciones de fresado. Estos modelos tienen como parámetros de entrada el material, la geometría de la herramienta y de la pieza y los parámetros de mecanizado, como por ejemplo la velocidad de avance y la velocidad de giro de la herramienta. Con estos datos el modelo de fuerzas calcula las fuerzas de corte durante el mecanizado, lo que permite conocer si estas se mantienen dentro del rango deseado.
En el grupo de Fabricación de Alto Rendimiento de la UPV/EHU se ha trabajado en el desarrollo de diferentes modelos de fuerzas con el objetivo de optimizar el diseño de trayectorias. El conocer de antemano las fuerzas que se van a producir durante el mecanizado, toma gran importancia en las operaciones de acabado, donde el margen de error es menor. Por este motivo se ha creado un modelo de fuerzas para herramientas cónicas en operaciones de 'flank milling'. Este modelo se ha integrado mediante programación interna en el CAM NX. De esta manera el usuario puede conocer los valores de las fuerzas de corte una vez generada la trayectoria de 'flank milling' sin necesidad de salir del software de CAM. Por otro lado, en un gran número de piezas se puede reducir notablemente el tiempo de mecanizado en operaciones de acabado en 'point milling' utilizando fresas de barril. Por este motivo se ha desarrollado un modelo de fuerzas para este tipo de herramientas con el objetivo de analizar trayectorias de mecanizado en 5 ejes de álabes de geometría compleja. Por otro lado se han desarrollado modelos para optimización de las trayectorias de mecanizado en operaciones de desbaste y semiacabado. La mejora de la productividad de estas dos etapas del mecanizado es crucial a la hora de reducir tiempos de fabricación y coste de producción. Los modelos desarrollados están orientados a la mejora de las estrategias de mecanizado, haciendo que el programa de mecanizado sea más eficiente en base a un compromiso entre conservación de la vida de la herramientas y reducción de tiempos de producción.
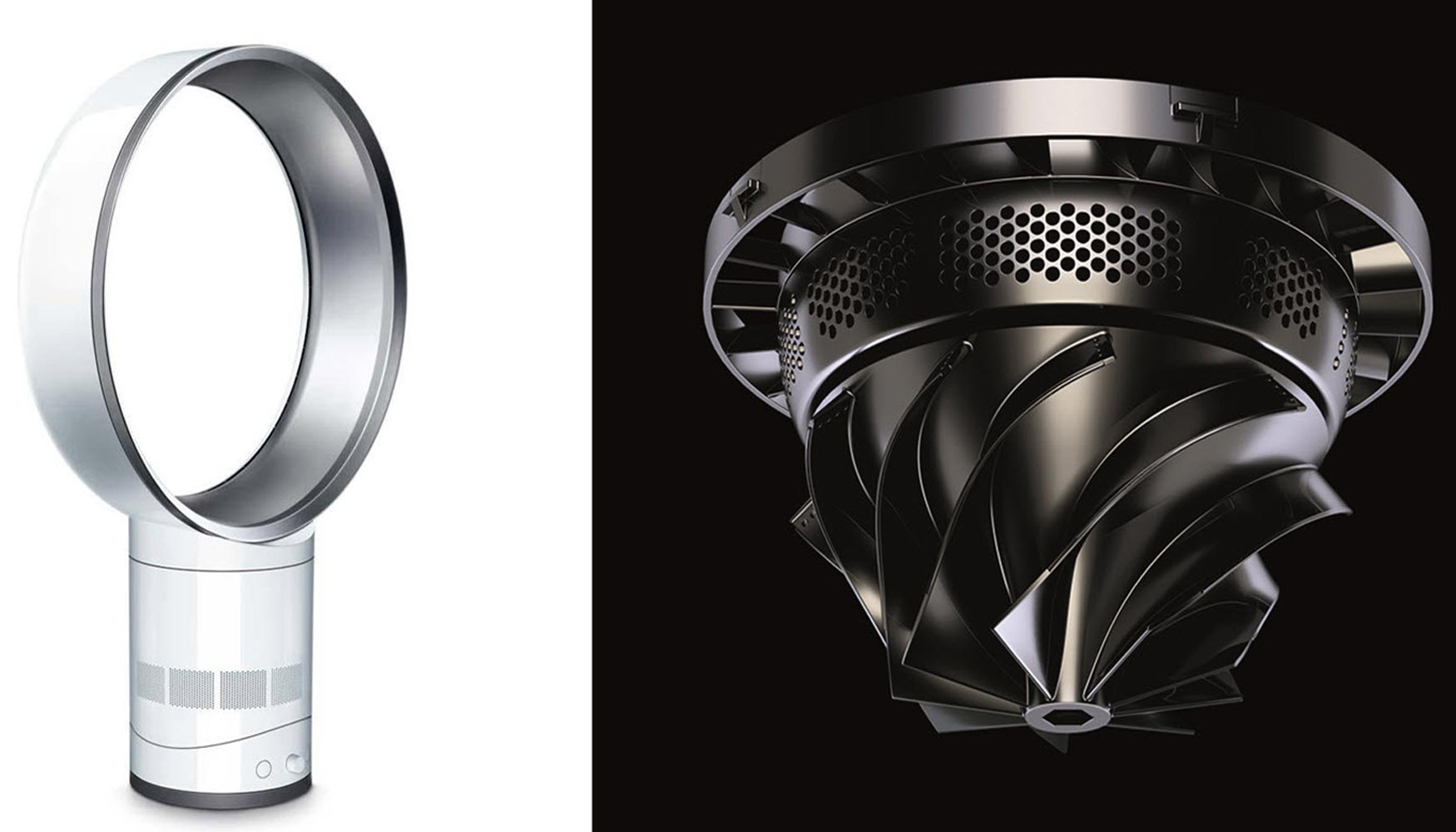
Mecanizado en 5 ejes de discos rotativos integrales
Una vez verificadas las operaciones de mecanizado se postprocesan las operaciones generada en el CAM. Obtenidos los programas de control numérico se ejecuta el mecanizado de la pieza. Durante el mecanizado y posteriormente se analizan diferentes parámetros que permiten optimizar el proceso. El objetivo de estas verificaciones es obtener un proceso de mecanizado robusto con dentro de unos tiempos y costes competitivos. Un aspecto importante es el uso de herramientas adecuadas para cada operación. Entre los parámetros asociados a la elección de fresas de mecanizado podemos destacar el material, la geometría, el recubrimiento o el tipo de refrigeración. El ratio de volumen de material mecanizado por herramienta y la medición de los desgates producidos en los filos de las herramientas permite valorar la idoneidad de las diferentes trayectorias y comparar diferentes geometrías de herramientas y recubrimientos.
Por otro lado, la medición de las fuerzas generadas durante el mecanizado permite en primer lugar, analizar si las operaciones de mecanizado ejecutadas, generan un rango de fuerzas aceptable y conocer su vinculación a defectos superficiales que hayan podido ocasionar. Además comparar las fuerzas reales generadas con las que predice un modelo permite optimizar el proceso de fabricación.
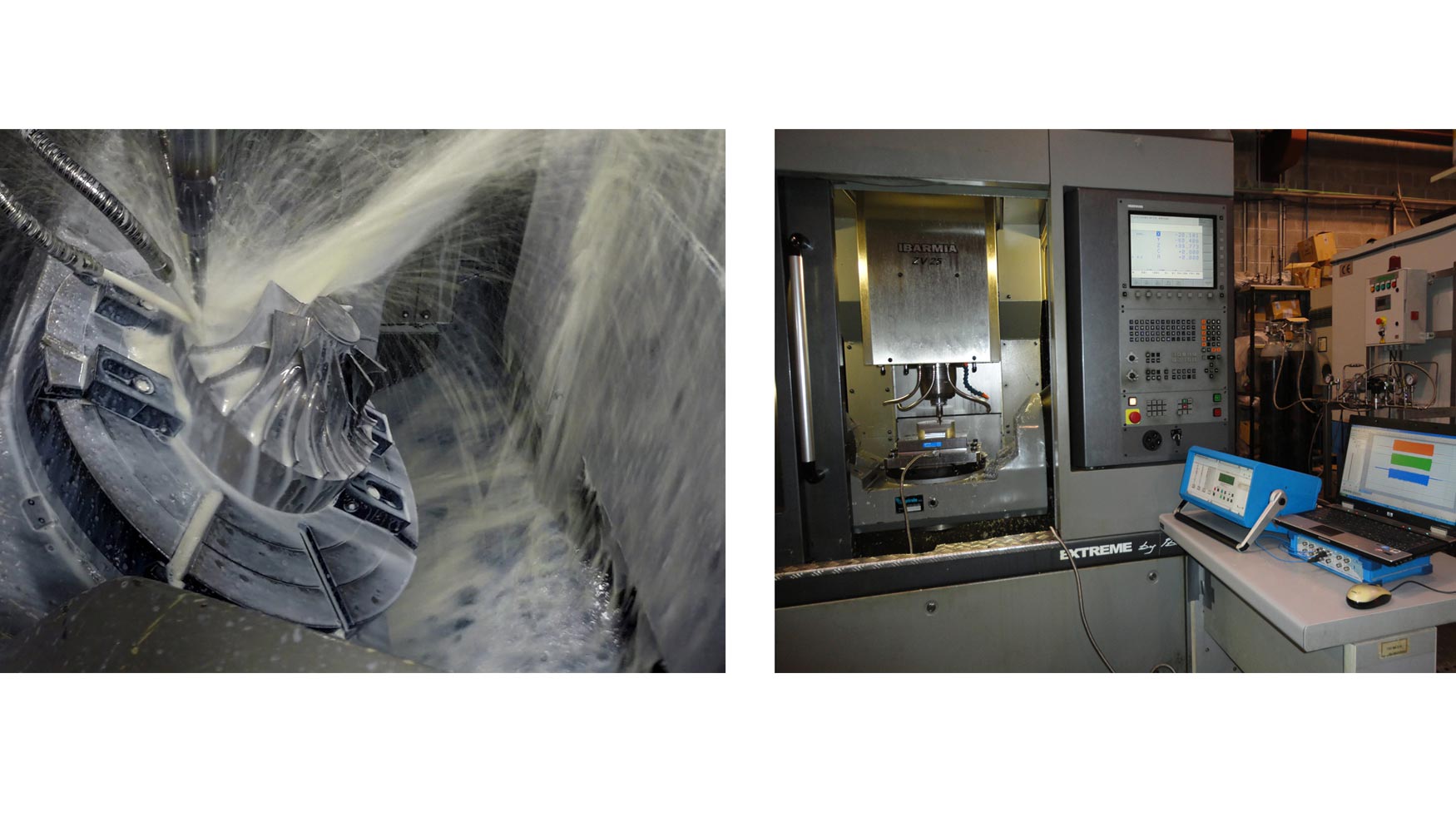
Por último, una vez finalizado el mecanizado de la pieza, la principal verificación del proceso es comprobar si la geometría final entra dentro de las tolerancias especificadas.
Esta medición es de gran utilidad para conocer en qué zonas de la pieza existe exceso de material y en cuales se han mecanizado en exceso. Cabe resaltar que cuanto mayores sean las fuerzas de corte y vibraciones en el proceso más se alejará la superficie real obtenida, de la virtual generada por un análisis simplemente geométrico y volumétrico.
La medición de discos rotativos de motores aeronáuticos es de gran complejidad debido a su geometría y altos requerimientos. Son necesarias máquinas de metrología de gran precisión, poca incertidumbre y reducidos tiempos de medición. También es de gran interés, tener la posibilidad de preprogramar la medición completa de la pieza concreta a medir. Hoy en día podemos destacar principalmente dos tecnologías utilizadas en la medición de estas piezas, las máquinas de medir por coordenadas y los escáneres 3d. De las máquinas de medir por coordenadas podemos destacar su alta precisión, mientras que de los escáneres de luz la rapidez con la que se pueden medir una gran cantidad de puntos de la superficie de una pieza. Hoy en día también se utilizan palpadores de no contacto para las máquinas de medir por coordenadas.
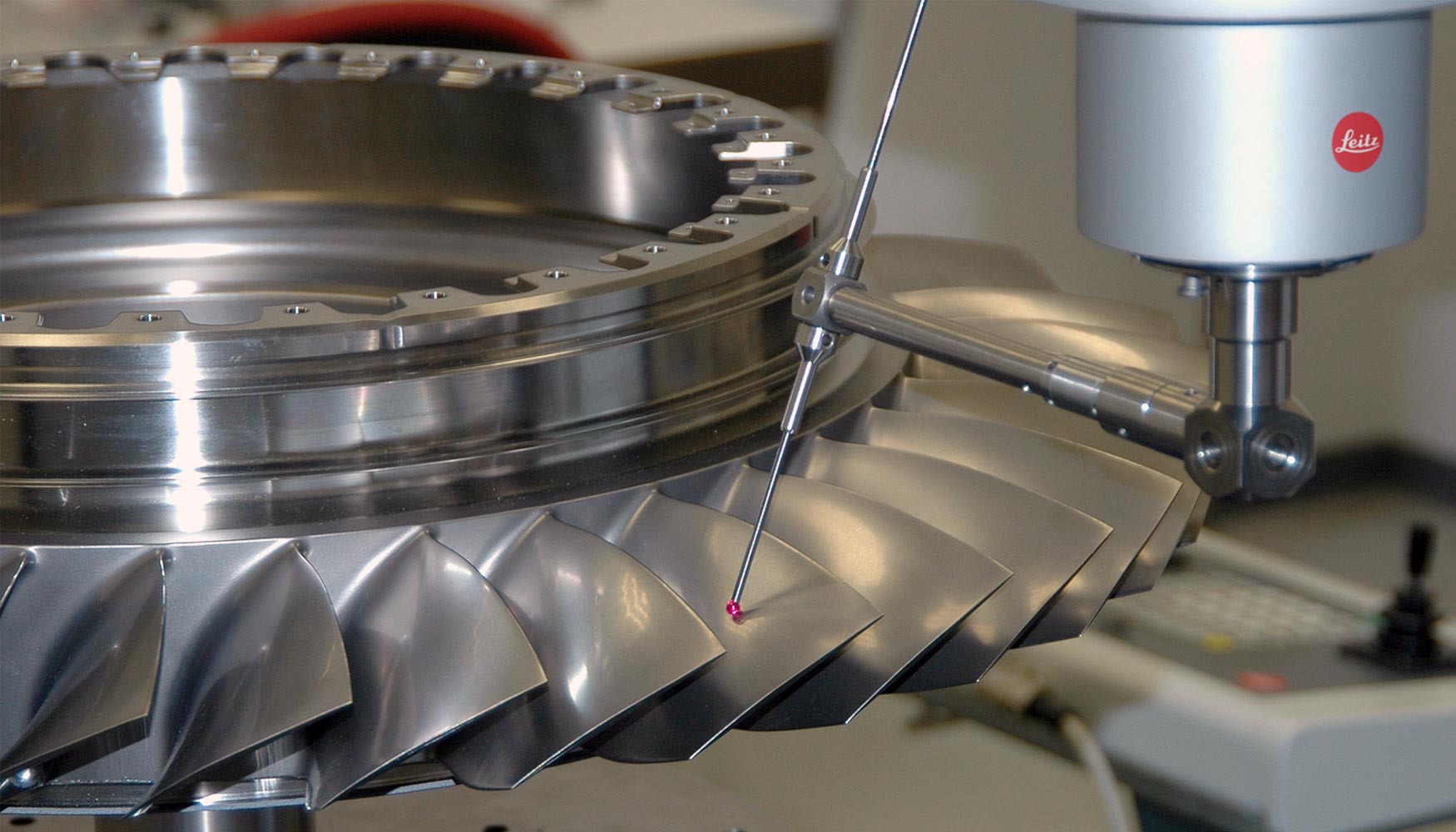
Rotores de álabes integrados, no sólo de aeronáutica vive la empresa
Los rotores de álabes integrados son discos rotativos fabricados en una sola pieza. Habitualmente estos componentes son mecanizados completamente o para obtener la superficie final. La principal ventaja respecto a discos ensamblados, es la reducción del número de componentes y la eliminación de elementos de unión. Este aspecto es de gran importancia en la fiabilidad de la pieza, ya que las uniones entre elementos son una de las principales fuentes de iniciación de fractura por fatiga. La disminución del rozamiento y la reducción de flujos de fuga conllevan un aumento de la eficiencia de compresión. Por otro lado es posible obtener una reducción del peso hasta el 30%.
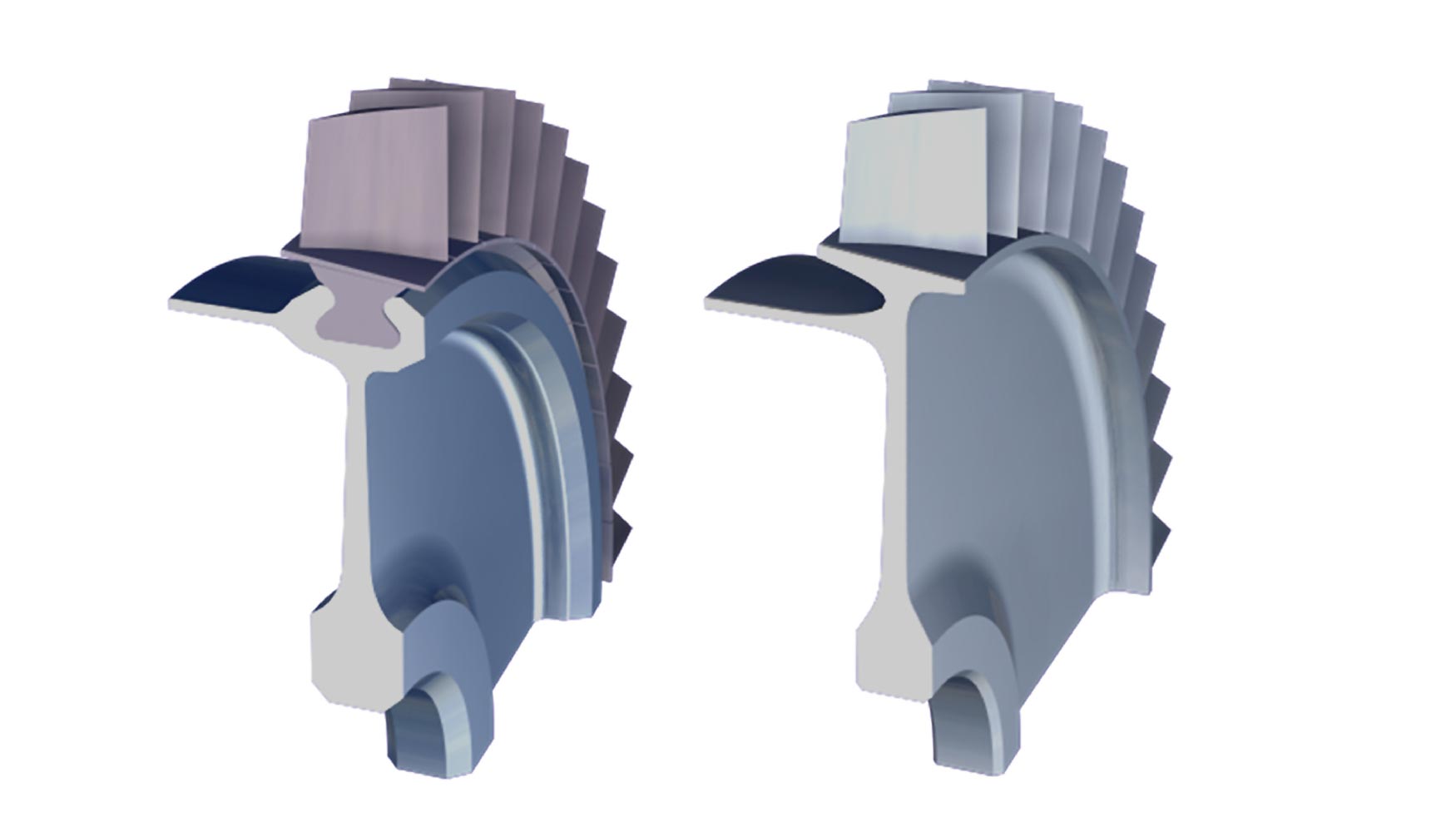
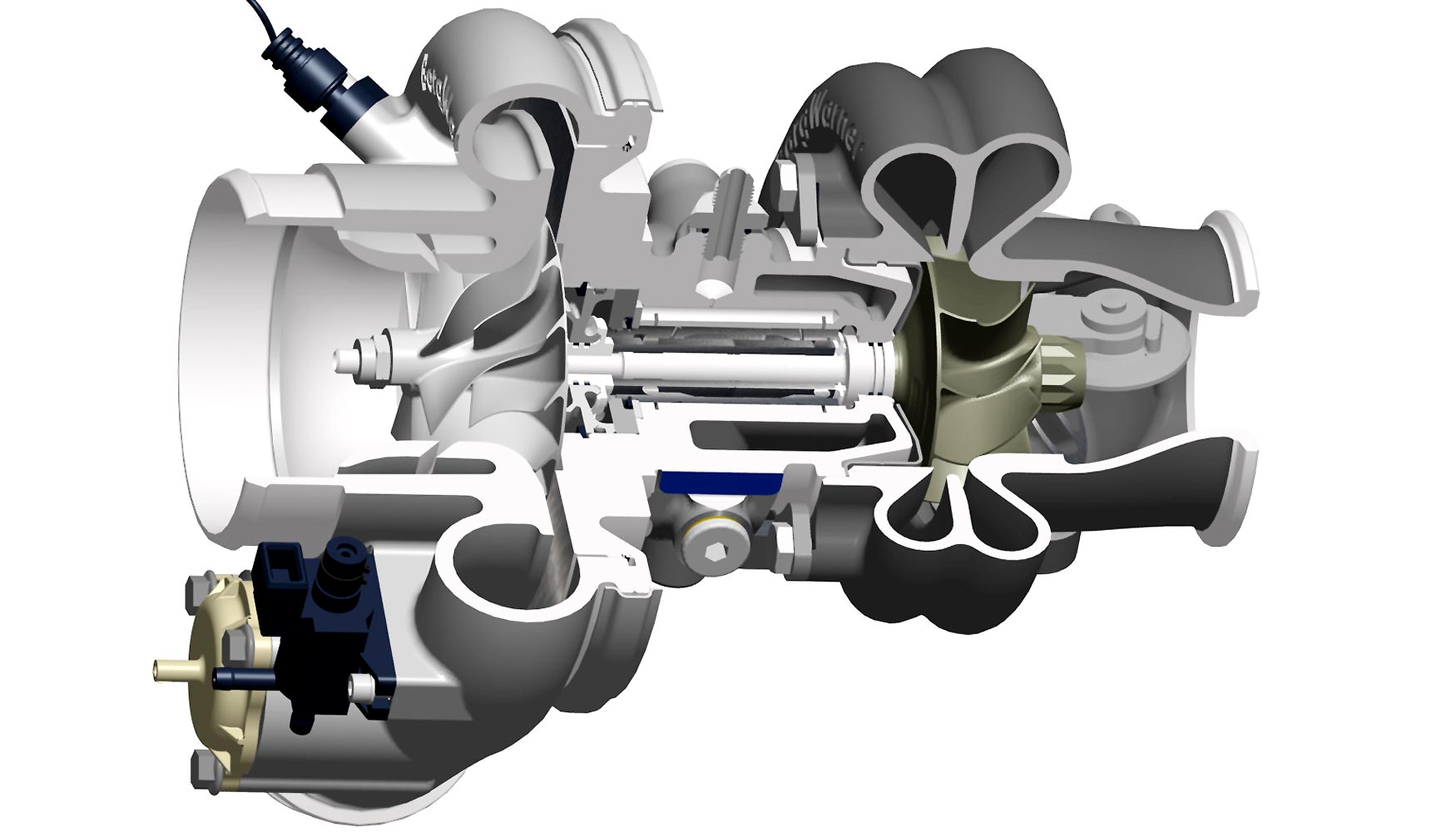
También podemos destacar los compresores centrífugos de aire, en los cuales los impellers son una de las partes más importantes. Su función es aumentar la presión y velocidad del flujo de aire, siendo de gran importancia ofrecer un funcionamiento robusto y eficiente, ya que suponen un gran porcentaje del consumo de la instalación. Los compresores de aire son ampliamente utilizados en la industria de aire acondicionado, la refrigeración y separación de aire, la industria médica, farmacéutica y química, procesos de generación de energía eléctrica, el sector alimentario o el tratamiento de aguas residuales.
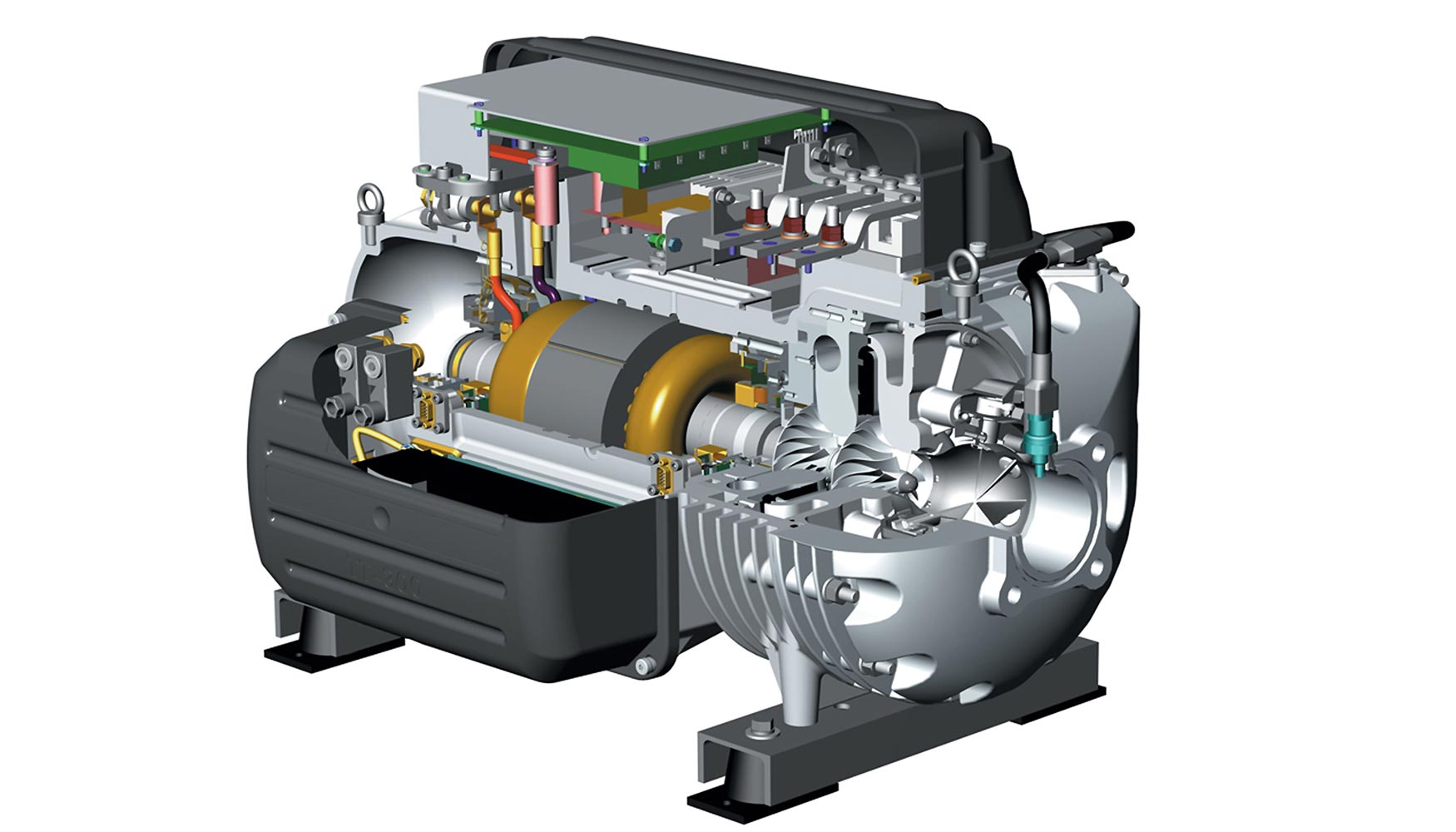
El sector de generación de energía mediante turbinas de gas y vapor es uno de los sectores de mayor aplicación de discos de álabes. Cada vez es más habitual fabricar rotores en un solo elemento para reducir el mantenimiento y reparación de álabes durante la vida de la turbina.
Por último podemos destacar la fabricación de rodetes para bombas en un gran número de industrias. Las bombas centrífugas mueven un volumen de líquido entre dos niveles transformando trabajo mecánico en hidráulico. La energía se comunica al líquido por medio de álabes rotativos.