El luthier, un operador de almas
6 de julio de 2010
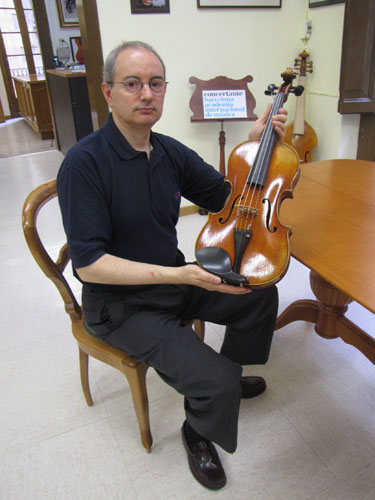
Es difícil encontrar un objeto cuyo proceso y materiales de construcción se hayan mantenido prácticamente idénticos a lo largo de los siglos. Cualquier intento de alteración en las medidas, las proporciones, las forma o los materiales de los instrumentos de cuerda ha concluido inevitablemente con el retorno a los cánones que se establecieron entre los siglos XVI y XVII. Las vitrinas de Casa Parramon, el taller de luthería más antiguo de España, fundado en 1897 y dedicado a la venta y restauración de violines, violas, violoncelos y contrabajos, albergan una colección de estos instrumentos de formas caprichosas, que jamás pasaron de eso, un simple capricho. “Puedes igualar o mejorarlo un poco en ciertos aspectos, pero la esencia ya está fijada. Todas las pruebas que se han hecho están en vitrinas; por alguna cosa será”, afirma Jordi Pinto, actual director de Casa Parramon.
Además, un instrumento de mediados del siglo XVI bien conservado, suena perfectamente en nuestros días. “La única cosa que ha variado desde el siglo XVI es el grado de exigencia sonoro, es decir, en los siglos XVII y XVIII se escuchaba música de cámara. La potencia exigida al instrumento no es la que se espera para llenar un auditorio”. Por ello, a finales del XVIII y durante el siglo XIX se introducen unos cambios “sutiles” que les permite tocar en espacios más grandes como los grandes auditorios.
Otra cosa sucede con los arcos, tanto o más importantes que el propio instrumento. Son obra de los arqueteros, oficio diferente pero complementario al del luthier, “el uno sin el otro no va a ninguna parte” comenta Jordi Pinto. La fabricación de arcos sí que ha evolucionado más que la de los instrumentos, sobre todo en el ámbito de los nuevos materiales. Tradicionalmente los arcos se realizaban en pernambuco, una madera tropical proveniente de la región homónima de Brasil dura y flexible. Últimamente se está probando la fibra de carbono, que permite obtener “arcos ‘de batalla’ de mucha calidad, pero que no se pueden comparar con la calidad de los de madera. Aunque el material puede evolucionar, la forma es inmejorable”.
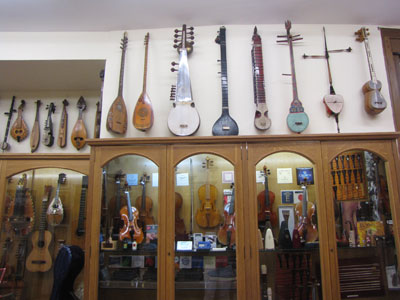
El taller centenario
113 años y tres generaciones de luthiers resumen la historia de Casa Parramon. Fundada por Ramon Parramon, que posteriormente se asoció a los hermanos Pinto, Jacint y Àngel, esta casa vivió su máximo esplendor constructor —más de 400 instrumentos— durante los años 20 y 30 del siglo pasado. Pero llegó la Guerra Civil e hizo estragos también en la actividad de Casa Parramon. La demanda de instrumentos cesó de golpe debido a la guerra y a la larga posguerra. Desde entonces, el negocio se reorientó hacia la restauración: los músicos no se podían comprar instrumentos nuevos, pero sí podían reparar y mantener los que ya tenían.
Durante la década de los 60 la segunda generación tomó el relevo en el taller de Casa Parramon con los hijos de Àngel Pinto: Ramon y Josep Maria. Mientras este último se puso al frente del taller, modernizándolo con técnicas actuales y herramientas más precisas, Ramon Pinto sustituyó a su padre y a Ramon Parramon en la dirección de la tienda. Ramon amplió horizontes y miró hacia Europa para ver cómo reorientar y modernizar la tienda. Él y su esposa Maria Rosa viajaron por todo el mundo y son los artífices de la colección de instrumentos clásicos, étnicos y folclóricos que se puede contemplar en las vitrinas y muros de Casa Parramon. Ramon Pinto también es autor de ‘Historia del violín’ (1973), embrión de ‘Los luthiers españoles’ (1987), primer y de momento único libro sobre la luthería española desde 1.700. Dos años más tarde publicó ‘Manual del luthier’, el único en su género escrito en castellano.
A finales de los 70 se incorpora a la Casa la tercera generación de profesionales: Àlex Canals, sobrino de Ramon, y Jordi Pinto, hijo de Josep Maria. El taller se reforzó con la incorporación de Jordi Térmens, en 1998, e Ignasi Flo, en 2003.

Calma aparente
En el taller de Casa Parramon, tan cercano al bullicio de las Ramblas de Barcelona, se respira calma. Pero es una calma aparente. Muchos músicos dependen de estos artesanos para poder ejercer su oficio, por lo que hay que ajustar mucho los plazos de entrega y trabajar rápido y con mucha precisión con instrumentos de 200 ó 300 años de antigüedad. Por ejemplo, durante nuestra visita tenían entre manos un violín de 1835 y otro de 1739, y otros muchos esperaban su turno colgados en las paredes y el techo de la estancia.
En el taller no hay mucha tecnología, que digamos. Gubias, cepillos, formones, herramientas típicas de cualquier labor relacionada con la madera, se alinean en el banco de trabajo del taller. Algunas de ellas son específicas para su trabajo, como un pequeño cepillo hecha a la medida de los violines, y el almero, un pincho con el que se coloca el pequeño cilindro en el interior del instrumento. Además, deben equiparse con herramientas de medición como el compás de gruesos, con el que se calcula con décimas de milímetro los gruesos de la madera con mucha precisión. Hay que tener en cuenta que la superficie de contacto del instrumento cuando se cierra tiene un grueso mínimo y debe ser uniforme para que encaje perfectamente.
También se usan plantillas y moldes, donde se trabaja con pasta dental. “Antiguamente se hacían de yeso, pero cuando se seca se contrae y siempre teníamos diferencias en las medidas”. La pasta dental se seca más rápido y con más precisión. “Es una de las muchas cosas que hemos aprendido de los profesionales del extranjero”, comenta Jordi Pinto. Y es que desde hace años, Casa Parramon invierte en investigación, desarrollo y en la formación continua de sus miembros. Regularmente organiza ‘stages’ intensivos trayendo colegas luthiers de otros países a sus instalaciones para aprender las últimas técnicas en restauración de instrumentos.
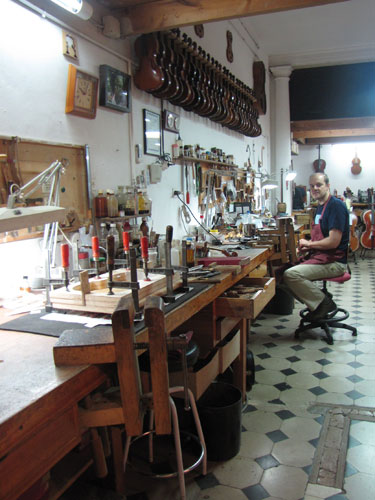
Los principales daños que suelen padecer estos instrumentos se deben al uso, a los fenómenos atmosféricos o a los transportes. “El violín es como una bóveda arquitectónica” —cuenta Pinto— una bóveda que soporta presión. Las cuatro cuerdas presionando, en el caso del violín, ejercen de 10 a 12 kilos de presión constante sobre la tapa, y la tensión de los extremos es de unos 25 kilos”. Si contamos que esta presión y esta tensión se dan sobre una superficie de 1,5-2 milímetros, a la mínima que hay un poco de humedad y calor, el violín puede desencolarse, la presión cede y puede llegar a deformar la madera.
Además de las desencoladuras, los instrumentos pueden sufrir desajustes en el sonido, el montaje y el reglaje. “La cuerda vibra; del puente, el sonido pasa a la tapa y el alma lo transmite al fondo”. De esta forma, con el alma del violín, la tapa y el fondo del instrumento vibran igual, en fase. Sin alma, vibra en contrafase y el sonido sale descontroladamente. “La colocación del alma es muy importante, y a menudo, de tanto tocar el instrumento o de moverlo en viajes, se desajusta”.
También, el desgaste por uso se debe enmendar regularmente. La clavija de madera tiene un roce constante con el cabezal y con el tiempo se desajusta y hay que readaptarlo. Asimismo se producen a menudo incidencias en el instrumento por golpes o caídas, que provocan grietas. Para repararlas, se debe aflojar la tensión de las cuerdas y abrir el instrumento, desmontarlo y enmendar la grieta a nivel, reforzándola con unos pequeños tacos en el interior y el barniz por el exterior.
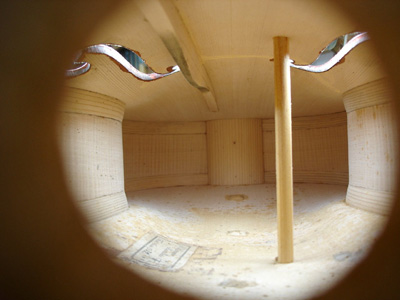
Los instrumentos olvidados en algún desván también pueden sufrir el ataques de la carcoma, cuyos daños son muy difíciles de remediar. “Lo malo no son los daños exteriores del instrumento, que son solo al punta del iceberg, sino cuando lo abres y ves todo lo afectada que está la madera por dentro”. Entonces hay que plantearse si la recuperación merece la pena. “Hay que calcular si el instrumento merece el esfuerzo y el dinero que se invierte en su restauración”.
La incontestable competencia oriental
Como en cualquier sector industrial, en el mercado se pueden encontrar instrumentos musicales con un amplio abanico de calidades. Jordi Pinto nos contó que se pueden distinguir a groso modo tres tipos diferentes de instrumentos. Por un lado, el instrumento más industrializado, sencillo, hecho en grandes series, con cierta calidad —“cada día mejor”— y a un precio razonable. Son instrumentos pensados para estudiantes. Después, hay un tipo de instrumento artesanal hecho de manera seriada por varias manos. “No deja de ser un trabajo hecho en cadena ni deja de ser hecho a mano, con lo que se obtiene un instrumento a un precio no muy elevado y de alta calidad”. Por último, se encuentra el instrumento totalmente artesanal. El constructor escoge la madera, la corta, la rebaja, realiza todo el proceso hasta el barnizado. Todo el instrumento está hecho por un solo artesano, por lo que la calidad es excepcional. Suelen ser trabajos muy personales, construidos a medida del músico. “No olvidemos que el instrumento es la herramienta de trabajo del músico, y cada músico le exige cosas diferentes a su instrumento”. El luthier debe estar a la altura de estas sutilezas, que no solo son características objetivas del instrumento, “como si el sonido es limpio o si se oye un ruidito, o hay descompensación entre agudos, medios y graves”, sino también hay mucho componente psicológico: “Independientemente de lo que estés oyendo, hay que adaptarse lo que quiere el músico”.

Pero también, como en cualquier sector industrial, la construcción de instrumentos está sufriendo una delocalización galopante. Cada vez más, empresas europeas, sobre todo alemanas están haciendo grandes inversiones e instalan sus factorías en países como China. “Los constructores alemanes forman a los trabajadores chinos a su manera, controlan el producto con un precio muy razonable, con lo que el 80% de la producción china se va para Alemania”. A pesar de tener especies de madera autóctonas con calidades similares, desde China se compra madera europea de alta calidad y manufacturan allá, con una mano de obra muy barata pero muy calificada. “El sueldo de un chino construyendo instrumentos es el 5% del de un alemán. Creo que la mayoría de productos europeos ya no son competitivos ni por precio ni por calidad. Los fabricantes europeos, conscientes de ello, han corrido a deslocalizar, de manera que de las 12 calidades básicas con las que nosotros trabajamos, hemos pasados de tener 12 europeas a 2 europeas y 10 chinas. Y eso teniendo en cuenta que hay capital europeo y norteamericano detrás”.
Pero antes de la globalización de las últimas décadas, durante los 60-70 del pasado siglo, quien irrumpió en el mercado fue Japón, y lo hizo por dos frentes. Por un lado, la empresa Suzuki empezó a producir instrumentos de calidad equiparable a lo que se podía encontrar en Alemania y con un precio similar. Pero el segundo frente fue el método Suzuki de aprendizaje, con el que enseñaban a los niños ‘jugando’ y además proporcionaban el instrumento. Tras Japón, aparecieron los coreanos, con productos cualitativamente más bajos y a mitad de precio que los japoneses. Corea subió su nivel de vida y sus precios y ya no eran tan competitivos. “Entonces irrumpió China, de manera que los propios coreanos te dicen ‘¿quieres instrumentos coreanos hechos en Corea o hechos en China?’, porque el producto coreano hecho en China es un 20% más barato que el fabricado en Corea”.
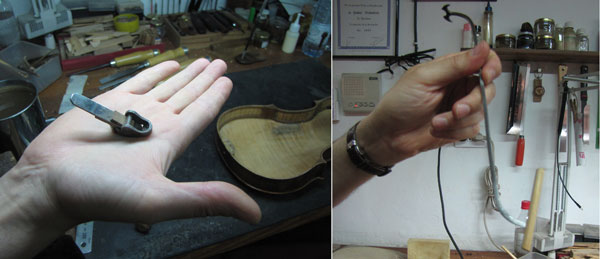
Unión contra el intrusismo
Ramon Pinto, perteneciente a la segunda generación en Casa Parramon, siguiendo su firme intención de conocer cómo trabajaban los luthiers extranjeros, contactó con los mejores talleres de Europa, donde se dió a conocer. Gracias a su labor, se convirtió en el primer español en formar parte de la Entente Internationale des Maitres Luthiers et Archetuers d’Art, la asociación internacional de luthería. “Los franceses llevaban 50 años asociados y los alemanes han celebrado ya el centenario de su asociación... nos llevan mucha ventaja”, afirma Jordi Pinto, sobrino de Ramon. A su imagen fundó en 1987 la Asociación Española de Luthiers y Arqueteros Profesionales, cuya sede estaba situada en el propio taller Parramon, en la calle Carme, 8, en pleno casco antiguo de la Ciudad Condal. Después, “por razones de diferencias en las maneras de hacer y por incompatibilidad de caracteres”, la asociación se subdividió en 2. Actualmente, Jordi sigue en AELAP, escisión nacida en febrero del 2003, tras la disolución de la antigua AEML/ALAE. “Algunos de los miembros de esta antigua asociación seguían teniendo la inquietud de formar un grupo o colectivo que pudiera dar una imagen de unidad y coherencia en el trabajo y en la ética profesional delante de los músicos y público interesado en general”. Entre los objetivos de AELAP están los de fomentar la luthería contemporánea y moderna clásica, dando a los músicos la mayor información acerca de sus miembros, de la seriedad y honestidad que ofrecen en su trabajo cada uno de ellos. Además se pretende fomentar el diálogo e intercambio con otros luthiers y asociaciones de otros países, para así enriquecer nuestro trabajo y conocimiento, tanto en la restauración y reparación como en la construcción de instrumentos y arcos.
También, AELAP desea luchar contra el intrusismo en la luthería, el abuso y prácticas poco honestas y también ofrece asesoramiento a quién lo solicite para defenderse de estos actos. “El principal problema —cuenta Jordi— es que no existe un colegio oficial de luthería, con lo que cualquiera puede montar un ‘chiringuito’, sea legal o no”. Un tipo de intrusismo es los que revientan el mercado trabajando en negro. “También hay el típico listo de orquesta que hace chapuzas que pueden dañar irreversiblemente instrumentos de 200 ó 300 años, y que luego, a los verdaderos restauradores, nos da el triple de trabajo arreglar su pifia”. Los músicos a menudo no son conscientes de lo delicado que es trabajar con instrumentos y opta “por pagar menos, sin tener en cuenta la garantía y el servicio posventa que le ofrece un buen restaurador”. Del mismo modo, existe el mismo tipo de “trapicheo” con la compra-venta de instrumentos. A menudo, y también por razones económicas, se compran instrumentos a otros músicos sin ninguna garantía. “Los luthiers ofrecemos asesoramiento en compras de este tipo, pero no todo el mundo quiere oír la verdad sobre el instrumento que se ha comprado”, bromea Jordi.
Paneveggio, el Bosque de los Violines
Según de qué parte del instrumento estamos hablando, está hecho de una madera u otra: arce de los Balcanes para la parte de la cabeza y el puente; ébano para el batidor; palosanto, ébano o boj para el montaje (clavijas, cordal y mentonera). Para la tapa y todos los refuerzos interiores, se suele usar abeto. “La mejor madera de abeto es la del bosque de Paneveggio, en los Dolomitas”, nos cuenta Jordi Pinto. Situado al norte de Venecia, la Foresta dei Violini, el Bosque de los Violines, es un vasto bosque de abeto rojo (Picea abies excelsa), con ejemplares centenarios que superan los 40 metros de altura. En Paneveggio son verdaderos especialistas en madera para instrumentos de cuerda. Controlan su calidad ya desde el árbol, vigilando escrupulosamente épocas de tala según las lunas. Una vez cortada, se mide la densidad, la capacidad de vibración y de transmisión del sonido, identificando así la calidad de la madera.
En gran parte, el Bosque de los Violines le debe su fama a Antonio Stradivari (1644-1737), el más célebre constructor de instrumentos de cuerda —Stradivarius— destacados por su sonido inigualable. Stradivari procedía de Cremona, ciudad cercana a Paneveggio donde todavía pervive una de las más importantes escuelas de luthería del mundo. Mucho se ha dicho de las extraordinarias cualidades de los Stradivarius —el secado, el envejecimiento de la madera, el barniz con fórmulas secretas...— aunque recientes estudios científicos han demostrado que la época en que vivió Stradivari coincidió con el ‘mínimo de Maunder’, el periodo entre 1645 a 1745, que fue, al parecer, extraordinariamente frío. Los veranos frescos y los inviernos rigurosos hicieron que los abetos crecieran con más lentitud y dieran una madera más densa y rígida, que es la que usó el célebre constructor para sus instrumentos.
Sobre esta última teoría, Jordi Pinto tiene una clara opinión: “No hay una causa-efecto clara ni directa. Es más, si fuera así, todos los instrumentos de la misma época, fueran de quien fueran, serían igual de buenos que los de Stradivari, cosa que evidentemente no es así. Si tenemos en cuenta solo el factor Maunder y ningún otro, estamos subestimando el factor más decisivo: la maestría”. Sobre este tema, Pinto aclara muchas dudas en un interesante post de su blog: http://einafustalletrainota.blogspot.com/2008/07/el-secreto-de-stradivari-2-parte-versin.html
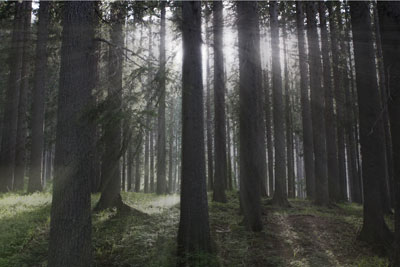