Estrategias para abordar la limpieza en los procesos de fabricación: defectivo cero
En algunas ocasiones el objetivo es modificar la superficie para aportar una propiedad que antes no tenía el material y/o superficie. En estos casos lo habitual es definir previamente qué propiedad se busca (brillo, protección contra la corrosión, mayor dureza, aportar color, etc.) y se suele tener muy claro cómo se cuantifica y, por tanto, cómo se controla dicha propiedad (brillómetro, cámara de corrosión, durómetro, colorímetro, etc.). Esta información se graba a fuego y pasa a formar parte de las especificaciones del producto.
Pero ¿qué sucede en otros casos, cuando el motivo para realizar una preparación superficial es sencillamente limpiar, es decir, eliminar ‘algo’ (restos de grasa, aceites, óxidos y/o partículas) que se han generado en cualquier etapa anterior del proceso y que dificultan o impiden etapas posteriores? Aquí es donde empieza el problema, ya que en pocas ocasiones se define de manera clara cómo de limpia debe estar la superficie y qué método de medida se va a utilizar para su cuantificación y control.
Esta indefinición suele hacer que aparezcan problemas en producción que acaban alejando cada vez más a la empresa de la tan ansiada fabricación ‘cero-defectos’.
Probablemente parte del problema esté en la dificultad para definir y medir la suciedad y en el modo de establecer cuándo se ha limpiado una superficie. Una manera de resolverlo es centrar la atención en un solo tipo de suciedad y tratar de parametrizarla, tal y como ha establecido la Norma 16232. En este caso la Norma ha definido una metodología para evaluar únicamente las partículas, dejando de lado el resto de posibles contaminantes como aceites, grasas, óxidos, etc., ya que sólo tiene en cuenta aquellos ‘contaminantes sólidos, que presenten una cohesión mecánica y sean extraíbles en alguna condición determinada’ (véase 16232-1, punto 1 Alcance y las definiciones de contaminante (3.27) y partícula (3.56)).
No obstante, esta simplificación del problema no puede aplicarse en todos los casos ya que en la mayoría de los procesos la suciedad tiene varios orígenes. En ocasiones pueden ser manchas de aceite o grasas, que dificultan operaciones de soldadura posteriores. Otras veces son óxidos generados durante el proceso de fabricación que manifiestan propiedades distintas que el resto de la superficie (color, rugosidad, volumen) y acaban afectando a la funcionalidad de esa superficie. Ninguno de estos supuestos podría ser abordado por la norma mencionada con anterioridad y debe tener un trato especial, distinto y particular.
En este contexto, el trabajo que realiza Cidetec Surface Engineering es multidisciplinar: abarca desde la caracterización de las piezas en diferentes estadios del proceso de su fabricación y la evaluación de cada una de las operaciones y procesos que pueden estar afectando al estado de las piezas, hasta las acciones, controles o equipos que habría que considerar para solucionar o minimizar el problema.
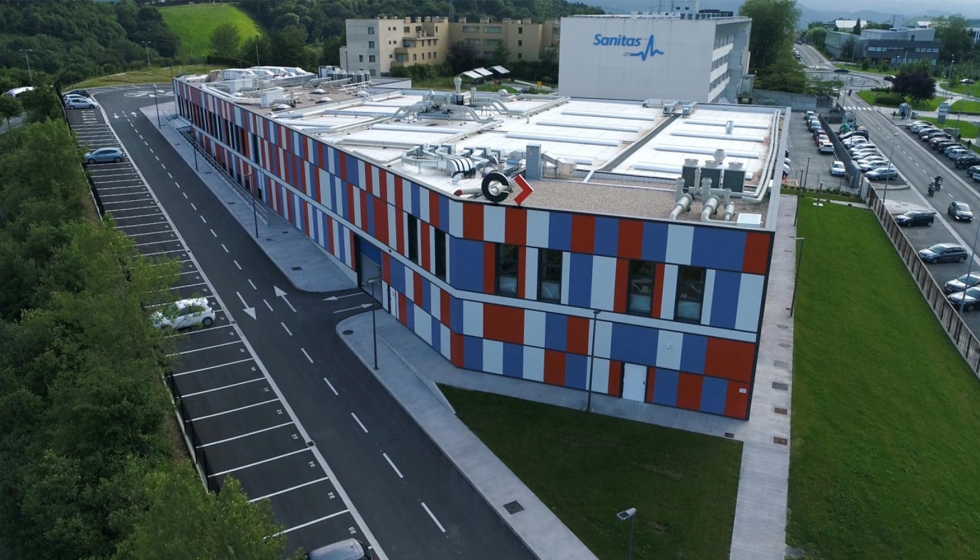
Caso práctico
A continuación, se muestra, de manera resumida, el trabajo realizado por Cidetec Surface Engineering en un subproceso industrial donde se detectaron manchas y suciedad en las piezas tras su proceso de lavado. La presencia de suciedad en la superficie de estas piezas dificultaba, y en algunos casos impedía, una operación de soldadura sin aporte que se realizaba posteriormente, dando lugar a un aumento del defectivo en este puesto. Además, la existencia de partículas afectaba de manera crítica a las funciones de uso del componente terminado.
Inicialmente se realizaron varias reuniones para conocer las instalaciones, el proceso, el tipo de máquina de limpieza utilizado y otros aspectos técnicos relevantes (composición de los detergentes, tipo de agua de lavados, depuraciones y filtraciones, mantenimientos realizados por la empresa, etc.). Además, se realizó una revisión del estado previo de las piezas para conocer qué tipo de suciedad estaba siendo tratada en el proceso de limpieza. En base a la información obtenida en este primer contacto con el problema se planteó hacer un seguimiento del estado de las cubas de limpieza y aclarado, en paralelo con una caracterización superficial de las piezas que estaban siendo limpiadas en ellas. Así, Cidetec evaluó periódicamente diversos parámetros de las cubas del proceso de limpieza, tal y como se recoge en el siguiente cuadro:
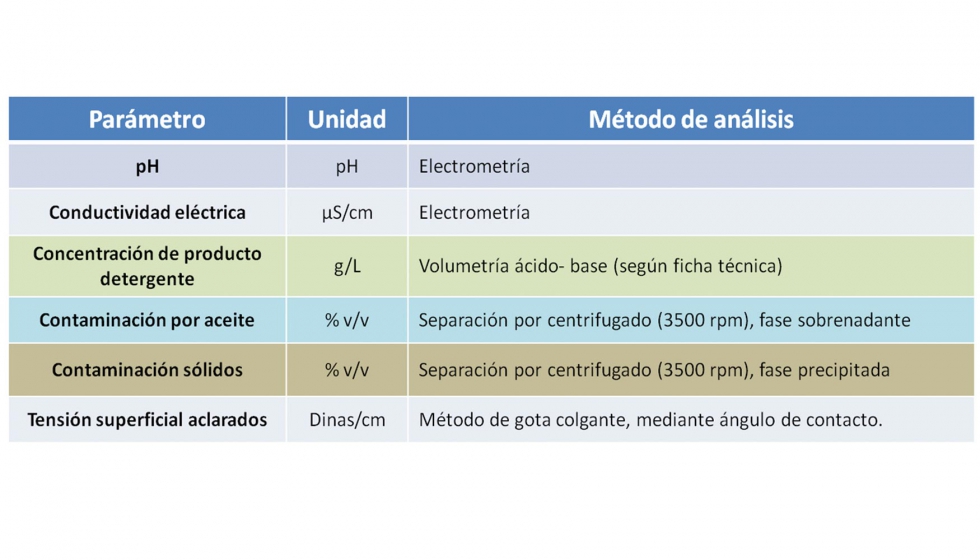
Simultáneamente a este estudio se tomaron muestras de las piezas en diferentes estadios del proceso y se caracterizó la suciedad que contenían.
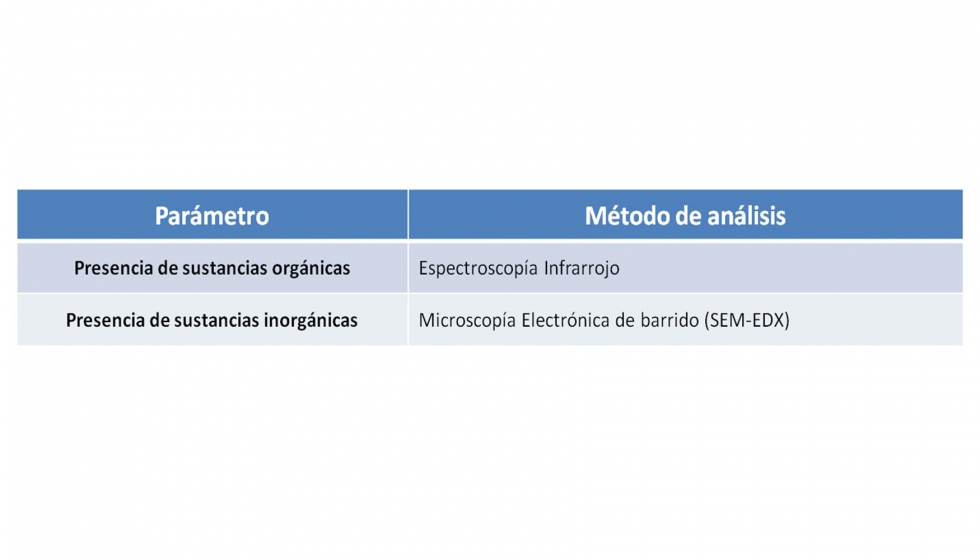
Durante varios periodos de trabajo distintos se hizo un seguimiento de los parámetros indicados anteriormente y se observaron las variaciones que se producían durante el transcurso de la producción.
A continuación, se muestran varias gráficas que ilustran parte del trabajo realizado:
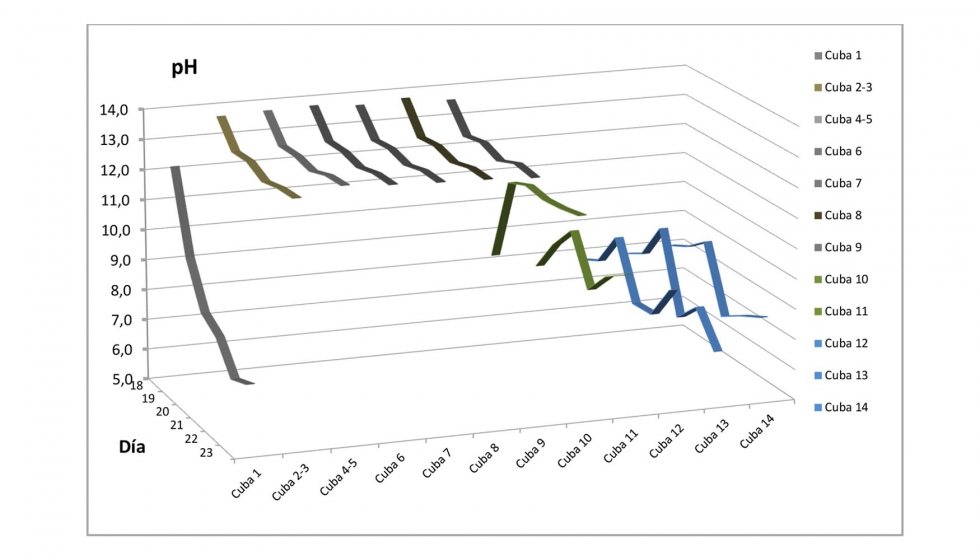
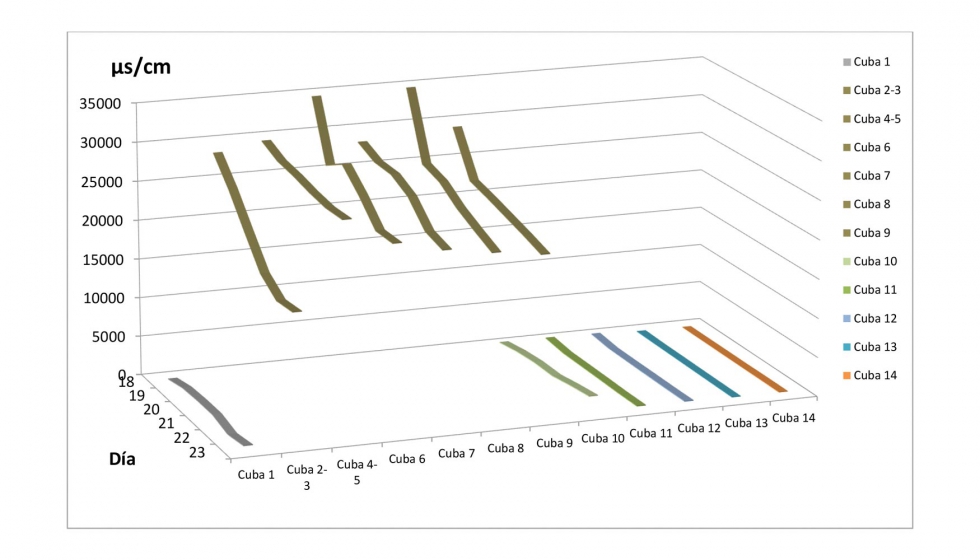
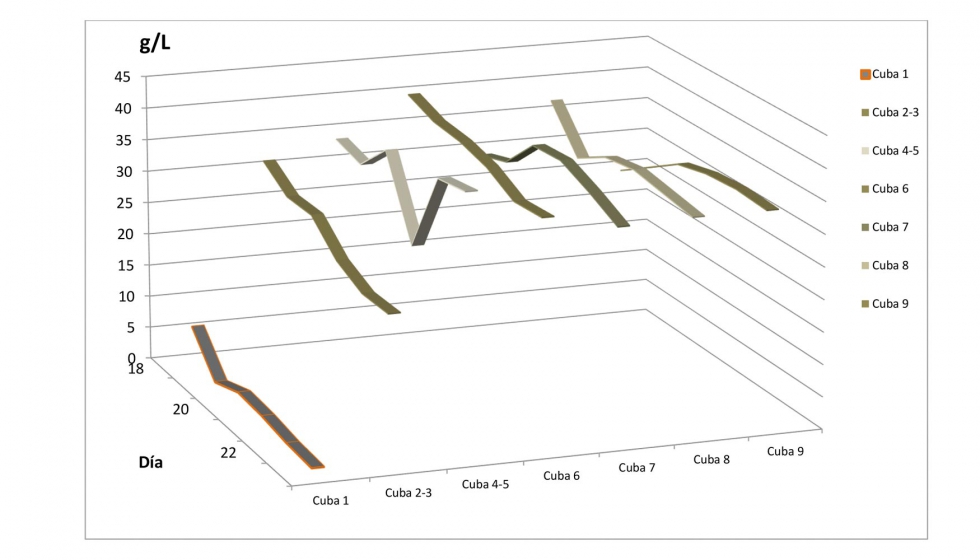
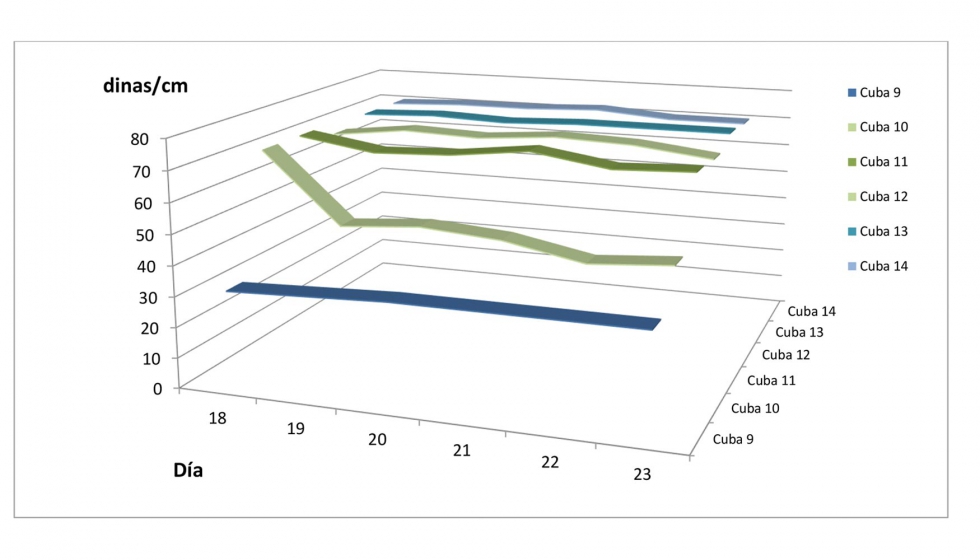
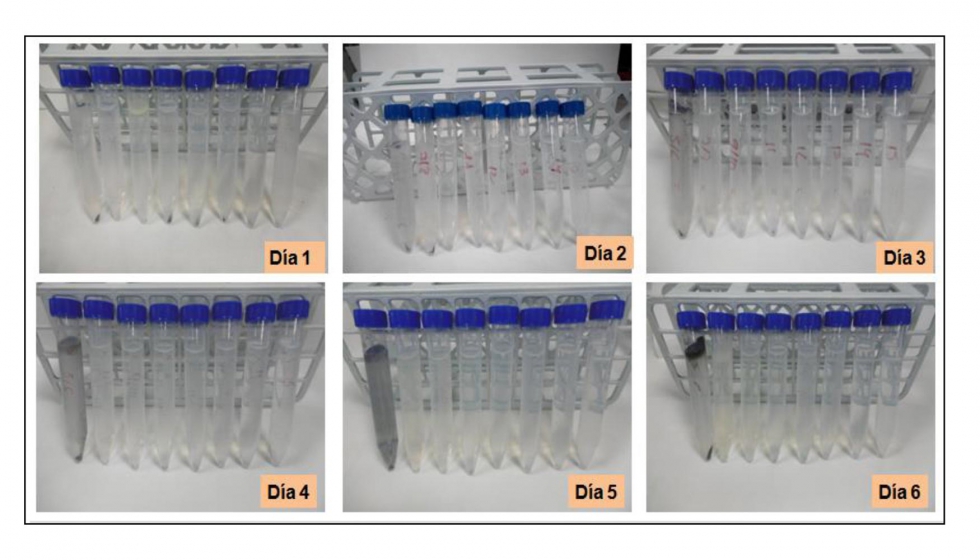
Esta información, junto con otra que se iba obteniendo sobre el proceso de limpieza, era analizada por todo el personal involucrado en el estudio. Además, la caracterización superficial que se realizaba sobre las piezas que estaban siendo tratadas aportaba datos adicionales que permitían completar la foto real del problema. Para el estudio de la suciedad presente en las piezas se utilizaron varios métodos, tanto directos como indirectos.
A continuación, se describe un sistema de cada método:
1. Directos:
Empleando un microscopio electrónico de barrido se analizó la superficie con la ayuda de un módulo de análisis EDX (Energy Dispersive X-ray spectroscopy), pudiendo determinar los elementos que estaban presentes en la suciedad.
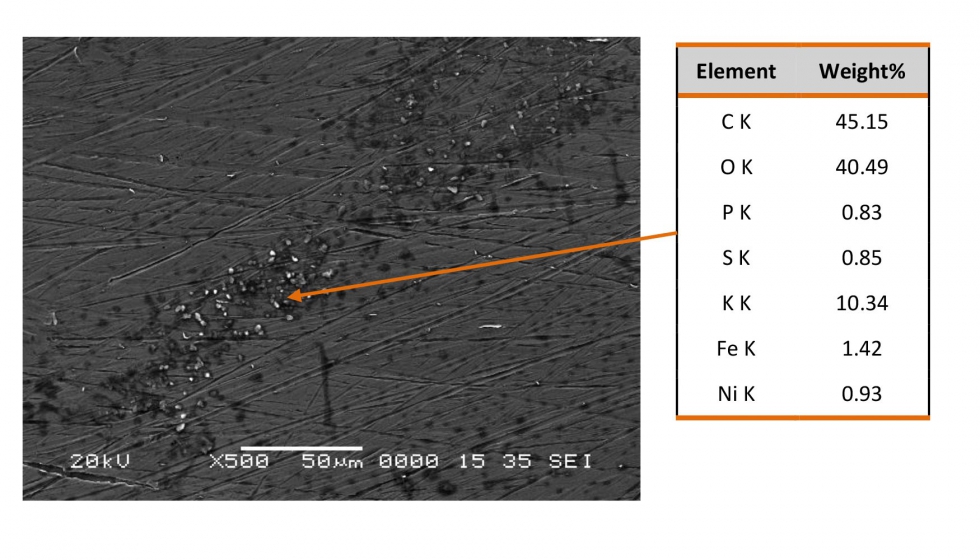
La información obtenida en la caracterización superficial se contrastó con los análisis realizados sobre los diferentes productos químicos utilizados en el proceso de limpieza y en las operaciones previas que sufren las piezas durante su fabricación. Así se pudieron relacionar los elementos encontrados en las piezas con una o varias operaciones del proceso de fabricación.
2. Método indirecto:
Consiste en poner en contacto las piezas sucias con un disolvente apropiado, normalmente con la ayuda de ultrasonidos, para que los contaminantes pasen al líquido y puedan ser analizado mediante diversas técnicas. En esta ocasión se utilizó heptano para limpiar las piezas y extraer unos restos que estaban manchando la superficie de las piezas, de manera que se separaron dos fracciones distintas: partículas sólidas y resto orgánico.
- Las partículas sólidas fueron caracterizadas por microscopía óptica y electrónica, lo que permitió conocer su morfología y composición y relacionar dichas partículas con una operación concreta del proceso de fabricación. A continuación, se muestran dos micrografías SEM obtenidas sobre la fracción sólida.
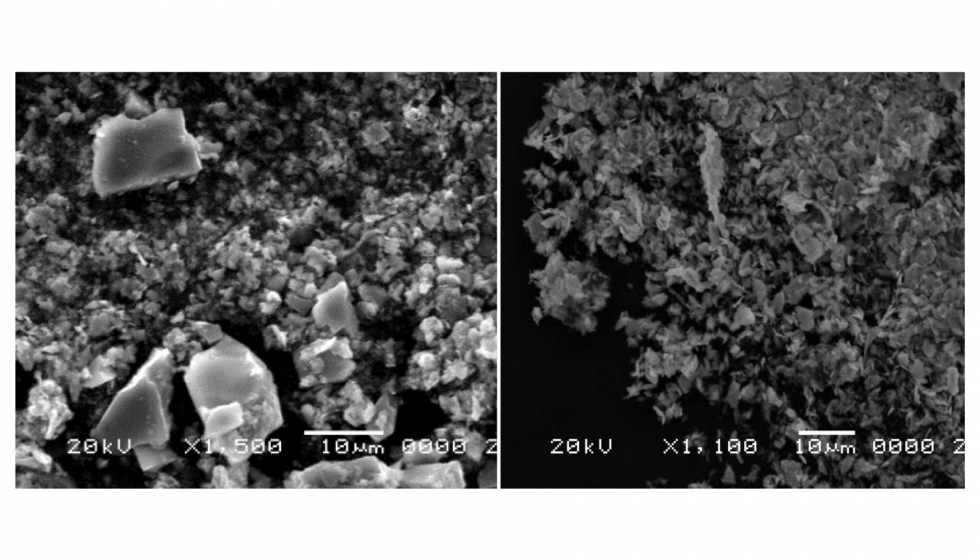
- El resto orgánico que se obtuvo tras la evaporación del heptano se analizó mediante espectrofotometría infrarroja. El espectro obtenido permitió identificar varios grupos funcionales que condujeron a un compuesto utilizado en una de las etapas de la limpieza.
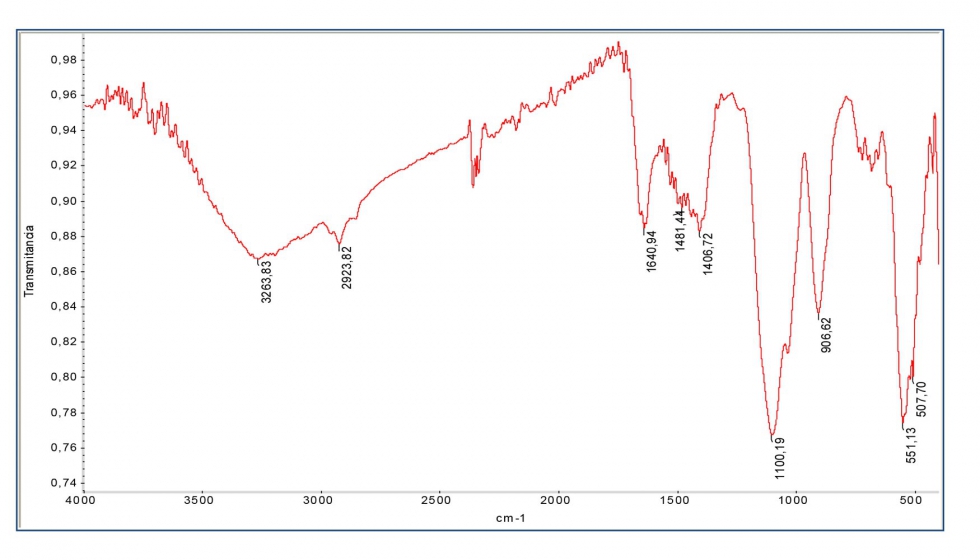
De esta forma, abordando el problema desde diferentes perspectivas, se dispuso en pocas semanas de información suficiente para identificar las etapas críticas que estaban afectando al estado superficial de las piezas y se pudieron realizar acciones concretas encaminadas a reducir el problema. Yo indicaría el valor aportado a la empresa: se redujo el defectivo, se ahorraron costes de mantenimiento, etc.
Siempre hay que tener presente que quien mejor conoce el producto, y por tanto la suciedad que puede aparecer en las distintas etapas de la fabricación, es el propio fabricante y debe ser éste el que dirija y lidere todas las acciones necesarias para la identificación, detección y control de la suciedad. Sin embargo, cuando se detecta un problema de suciedad que no se ha podido solventar con los medios que el cliente tiene a su alcance es cuando comienza la labor de Cdetec Surface Engineering. Tras ese primer contacto personal técnico de Cidetec se desplaza a las instalaciones del cliente y observa a pie de máquina, conjuntamente con el personal involucrado, las diferentes etapas que componen el proceso global. De esta forma, haciendo equipo con el cliente, Cidetec pone en juego su experiencia y su infraestructura (laboratorios, planta industrial, equipos de caracterización, etc.) para averiguar qué está generando el problema, cuál es su procedencia y qué acciones hay que realizar para solucionarlo.
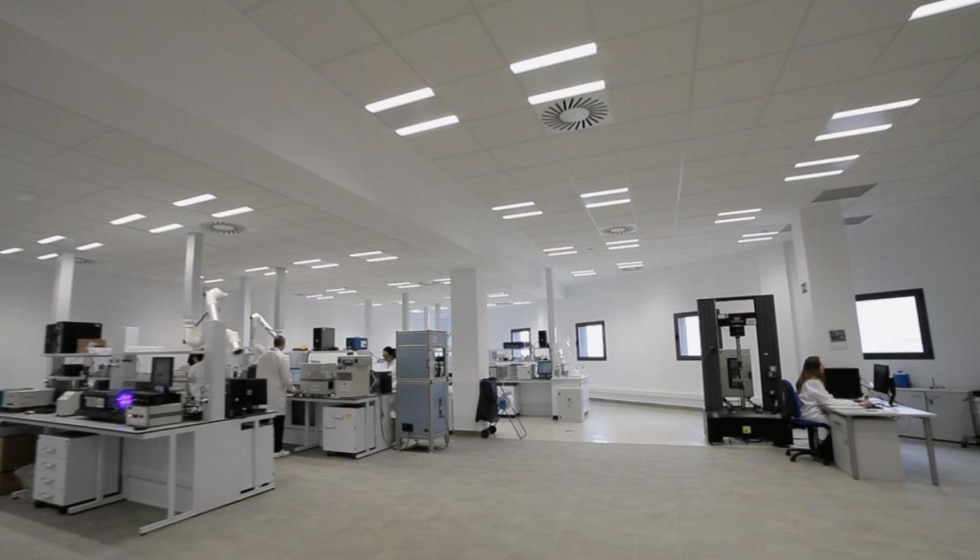
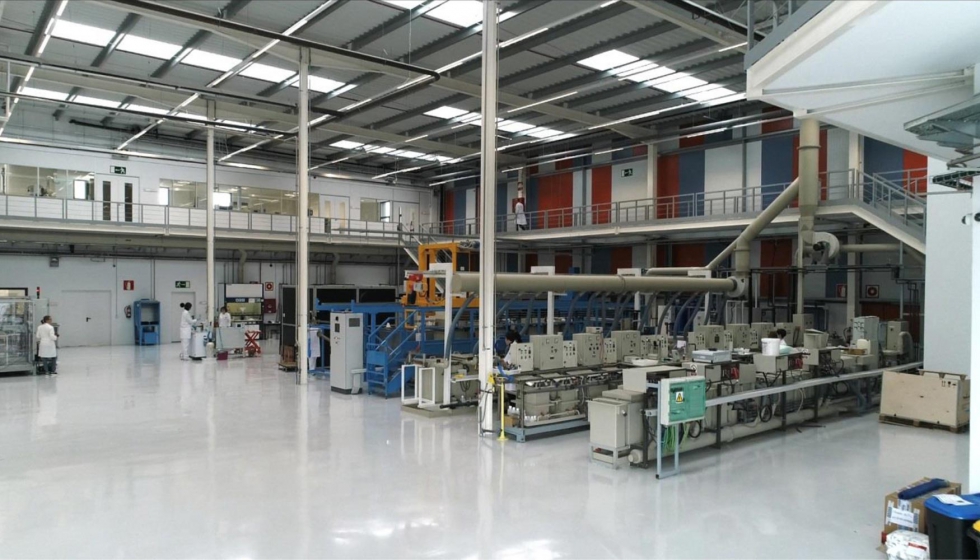
Interior de las instalaciones de Cdetec Surface Engineering.