Mecanizado virtual de piezas de geometría compleja: ahorro de tiempo y dinero en todas las fases del proyecto
Ideko01/06/2006
Con estos clientes en mente y con la idea clara de ofrecer soluciones completas atractivas y a la vez productivamente eficientes, sin olvidar la mejora en la eficiencia interna de la empresa, el Grupo Danobat viene trabajando en el último periodo en la implantación del mecanizado virtual como herramienta para el desarrollo de sus procesos llave en mano, desde la fase de oferta hasta la puesta a punto del proceso en casa del cliente.
El concepto de mecanizado virtual viene siendo utilizado desde hace muchos años, bien es cierto que con diferentes perspectivas y alcances, y en el caso de la utilización de sistemas de visualización y verificación de procesos no es un concepto novedoso, sin embargo el enfoque que se le está dando a nivel de las empresas del Grupo Danobat con el apoyo del Centro Tecnológico Ideko, pretende hacer una utilización global e integrada de la tecnología en toda la cadena de desarrollo del producto llave en mano, incluyendo además de las fases típicas de programación y puesta a punto del proceso, otras no tan habituales como la oferta y el diseño de los utillajes de amarre de las piezas, elemento complejo y diferenciador en muchos casos. Y, como elemento adicional más avanzado, la implementación en el sistema diseño 3D-programación CAM-verificación, de modelos de corte que permitan definir las condiciones de trabajo más idóneas y seleccionar las características de máquina más adecuadas.
Descripción de la metodología
• La disposición de modelos 3D de las máquinas. No siendo necesario disponer del diseño 3D detallado de la máquina, sino sólo de las formas exteriores de las piezas que puedan entrar en colisión, es ya habitual entre las empresas del sector el diseñar sus máquinas en 3D, por lo que este punto no supone un trabajo añadido.
• La utilización de un CAM para la programación del proceso. Tampoco absolutamente necesario, en función de la complejidad del proceso a programar, pero sí recomendable y, como en el caso anterior, habitual.
• La utilización de un software de verificación y visualización del mecanizado, como es el caso de Vericut (el más utilizado y avanzado). Este software permite:
• Ejecutar y visualizar los programas de CNC (bien a partir del CAM o manualmente programados).
• Verificar la interacción entre máquina, herramienta, pieza y utillaje, detectando interferencias y colisiones.
• Detectar errores en la programación.
• Optimizar los ciclos programados.
• El último punto, que queda fuera de la utilización de paquetes comercialmente disponibles, y proporciona un valor añadido muy importante de cara a la consecución de un proceso optimizado, es la disponibilidad de modelos de simulación del proceso de corte. Estos modelos, en nuestro caso desarrollados por Ideko en colaboración con Tekniker y las empresas del Grupo Danobat, permiten conocer y determinar para un sistema máquina-herramienta-pieza-utillaje las condiciones óptimas de trabajo, esto es, de máxima tasa de arranque de material, en ausencia de vibraciones, permitiendo con ello seleccionar, además de las condiciones de trabajo, la herramienta más idónea, y proporcionando información sobre fuerzas de corte, pares y potencias derivadas del proceso.
La metodología completa es básicamente la misma para las distintas fases posibles de aplicación (oferta, diseño, puesta a punto), con ligeras variantes en cada caso. El esquema siguiente refleja los pasos a seguir en un caso genérico:
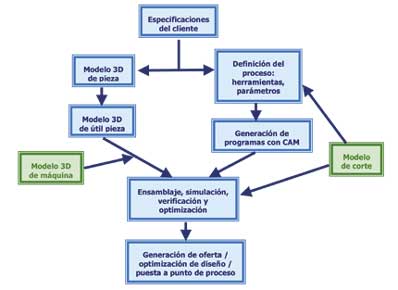
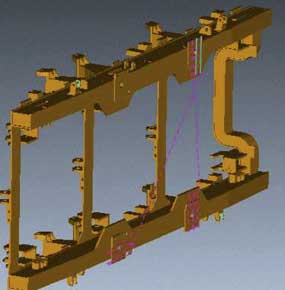
2. Modelo ensamblado de pieza, utillaje y máquina. El modelo de máquina únicamente requiere de las superficies externas, mientras que el de pieza y utillaje se incluyen al detalle, para analizar el proceso y optimizarlo.
3. Verificación del programa (Vericut): detección de errores de programación y visualización de colisiones
4. Selección de condiciones óptimas a través de la simulación en el modelo de corte (modelo de corte propio de Ideko)
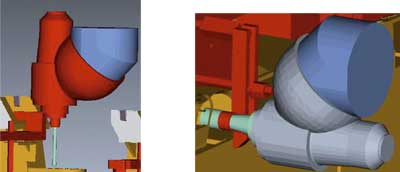
• En fase de oferta, permite disponer de una oferta, tanto a nivel de equipamiento (máquina seleccionada, utillaje básico) como de condiciones de proceso, y con ello tiempos y costes del mecanizado, mucho más ajustada y verificada, evitando posibles problemas o sorpresas posteriores.
La garantía que una oferta así desarrollada presenta al cliente (que puede visualizar su proceso de mecanizado en el simulador) es muy superior a la que se consigue con una oferta convencional, realizada “manualmente”.
• En la fase de desarrollo del proyecto, permite afinar al máximo la máquina y utillajes, así como la selección de herramientas y condiciones del proceso. Un aspecto muy importante en este tipo de piezas de geotermias y procesos complejos, es el diseño de un utillaje adecuado, que garantice la calidad de mecanizado (posicionado, repetibilidad, estabilidad del amarre) siendo lo más simple y ergonómico posible.
• En la fase de puesta a punto, permite disminuir drásticamente el número de pruebas a realizar, y depurar los programas de mecanizado antes de introducirlos en máquina. De esta manera, los ensayos a realizar para verificar la validez de la solución propuesta se minimizan.
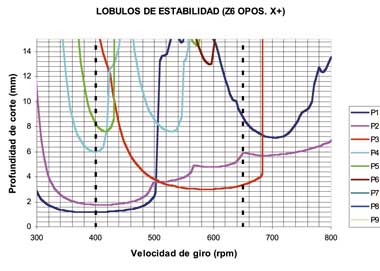
Conclusiones
• La oferta imprime un nivel técnico mayor, ya que muestra al cliente que el fabricante domina el proceso desde la fase de concepción hasta la consecución del mismo, controlándose todas las variables que toman parte en él.
• Los recursos empleados en fase de oferta pueden ser ligeramente superiores, pero a su vez repercuten directamente sobre la calidad de oferta. Estos recursos destinados en fase de oferta se emplean al 100% en la fase de desarrollo del pedido, disminuyendo los medios y dedicación necesarios en esta fase.
• La fase de puesta a punto del proceso en máquina se reduce drásticamente. Los programas de mecanizado tiene un elevado valor de fiabilidad antes de realizar cualquier prueba a pie de máquina.
• Se reducen los costes de no calidad al verificar todo el proceso en fase de diseño y previamente a fabricar cualquier elemento. Antes de llevar la solución adoptada a la puesta a punto en máquina, esta ha sido verificada, disminuyendo el riesgo de interferencias.
• La aplicación de los modelos de corte permite seleccionar y optimizar tanto las herramientas utilizadas como las condiciones de proceso, buscando la máxima tasa de arranque de material.