Aiju encabeza la participación española en el proyecto europeo Custom-Fit que investigará sobre "rapid manufacturing"
Custom-Fit es un nuevo proyecto que engloba a 32 socios de 16 países europeos. Además de AIJU, el Instituto de Biomecánica de Valencia (IBV), la juguetera Feber, y los fabricantes y distribuidores de material deportivo de montaña Artiach y Barrabés completan la participación española en el mismo. Esta nueva iniciativa, que será el principal proyecto de investigación europeo sobre la materia, pretende crear un sistema totalmente integrado que permita realizar el diseño, producción y distribución de artículos individualizados tales como cascos, prótesis e implantes directamente de un fichero 3D. Basándose en el fundamento de las tecnologías de prototipado rápido, la revolución vendrá al producirse la deseada transición hacia la “fabricación rápida” de piezas finales sin tener que recurrir a la construcción de un molde.
“El objetivo de este proyecto es crear productos adaptados a las necesidades individuales de cada cliente o usuario” comenta Rafael Valero, Gestor de Proyectos en AIJU y Director de Explotación y Diseminación del proyecto. “Pretendemos crear un proceso completo e integrado que abarcará desde las fases iniciales de captura de datos y creación del diseño, la realización de las piezas con distribuciones multimateria plástico-metal en un solo componente y la verificación final y distribución. Esta filosofía reducirá costes, aumentará la flexibilidad de fabricación de series micro cortas e individualizadas y permitirá implantar políticas de fabricación ‘Just in Time’”.
El proyecto une, dentro del consejo de administración formado por 7 entidades y el resto de participantes hasta formar un consorcio de 32 socios, a los principales y más respetados centros de investigación, universidades y empresas que trabajan en procesos de “fabricación rápida”, prototipado rápido, CAD/CAE, ergonomía, materiales y fabricantes finales de productos susceptibles de ser mejorados a través de una individualización. Centros de investigación como el TNO holandés, Fraunhofer IFAM de Alemania, SINTEF de Noruega y AIJU de España; universidades como las de Loughbourough y De Montfort en Gran Bretaña y empresas usuarias como la italiana DUCATI y la juguetera española FEBER International forman un grupo que ha recibido el reconocimiento de la Comisión Europeo.
Cuatro procesos como base de producción
- La Universidad de Loughborough, por ejemplo, está actualmente investigando con una tecnología, High-Viscosity-Jetting, que permite desplazar una pequeña gota de material a través de una máscara a la localización deseada. Un sistema multi-tobera controla el pulso por medio de la presión, la distancia del sustrato y la duración del proceso de extrusión de material. Este sistema tiene el potencial de trabajar con polímeros, cerámicas y metales con la misma filosofía.
- Sintef desde Noruega, investiga un sistema que permite producir objetos metálicos tridimensionales con un metal en polvo. Las capas de material que forman la pieza son creadas atrayendo el metal a un fotorreceptor cargado bajo la influencia de un campo eléctrico. La capa atraída, se deposita sobre un área de trabajo y se vuelve a producir el ciclo hasta que el objeto 3D se forma por completo.
- El TNO holandés se encuentra, actualmente, investigando sobre un novedoso sistema de extrusión de fluidos de hasta una viscosidad de 300 mPa/s. Una corriente de pequeñas gotas de material se cargan a través de un campo eléctrico y unos deflectores eléctricos dirigen las gotas de material hasta la zona deseada. Al ser una técnica de deposición selectiva, la posibilidad de usar multitud de materiales es una gran ventaja.
- La cuarta técnica, proveniente de la Universidad británica de De Montfort, consiste en la precolocación por un campo eléctrico de capas de multimaterial cargadas y su posterior fusión entre ellas.
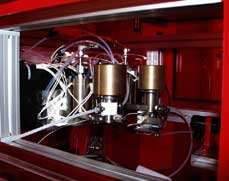
Santiago Gisbert, Director de AIJU, cree que aunque el proyecto Custom-Fit se concentrará inicialmente en cuatro productos específicos –prótesis, implantes, cascos y mangos deportivos- las aplicaciones de este novedoso sistema pueden revolucionar los productos que se ofrecen al consumidor consiguiendo una individualización máxima. “Tras este proyecto, cada cliente estará presente en el corazón del proceso de diseño y ello repercutirá directamente en la fase de fabricación rápida. Niños con discapacidades, personal de seguridad y bomberos, gente aficionada al deporte podrán tener productos con uno de los mayores valores añadidos: ser únicos y adaptados a cada uno”.
“Estoy convencido que conseguiremos lo que pretendemos” comenta Rafael Valero, “Existe una voluntad e ilusión fantástica por parte de los socios de colaborar e interactuar. Es un proyecto excitante, que puede traer beneficios reales y es un placer estar involucrado en una iniciativa cuyos objetivos principales son mejorar la calidad de vida de las personas y la competitividad de la industria europea”.