Modelos de los procesos, cerca del usuario
Estamos inmersos en una época de cambios constantes en todos los ámbitos, acelerada por los desarrollos tecnológicos, en el que las empresas deben ser referentes en la vanguardia de la tecnología. Esta situación ha dado lugar al nacimiento de un nuevo concepto: la Fábrica del Futuro (FoF). Esto implica que hay que transformar las fábricas tradicionales en un modelo más inteligente de producción y fabricación, creando unos entornos sostenibles y totalmente conectados.
Durante la última década se han estado empleando una serie de términos relacionados con la fábrica del futuro e interconectados entre sí, como pueden ser Industria 4.0 o IIoT. El primero de ellos fue acuñado por los Ministerios de Educación, Investigación y Economía de Alemania en el año 2010, el cual se emplearía posteriormente en la Feria Hannover Messe de 2011. Desde entonces, el punto de mira del sector de fabricación ha estado focalizado en los desarrollos tecnológicos a nivel global, englobados en lo que se conoce como ‘la cuarta revolución industrial’. Ésta hace alusión a la integración de sistemas inteligentes en el mundo industrial; es decir, que todas las máquinas estén conectadas entre sí (M2M) y con la nube. El segundo de ellos proviene del inglés Industrial Internet of Things, mediante las cuales se quiere analizar y coordinar los esfuerzos para acelerar la incorporación del internet en todos los elementos de un proceso.
![Figura 1. Representación del concepto Industrial Internet of Things (IIoT) [1] Figura 1. Representación del concepto Industrial Internet of Things (IIoT) [1]](https://img.interempresas.net/fotos/1869366.jpeg)
La introducción de las nuevas tecnologías en las fábricas es esencial para el futuro, ya que se trata de una solución más inteligente hacia la eficiencia, la sostenibilidad y la competitividad [2]. No obstante, este cambio no se puede implementar de golpe en las empresas, es necesario ir introduciendo progresivamente las tecnologías, como son los modelos cerca del usuario, los cuales permiten hacer frente a la problemática común que se da en los procesos de mecanizado.
Hasta hace poco, los problemas que surgían en el mecanizado se afrontaban de manera única e independiente, obviando las posibles relaciones que pudieran tener entre sí. Hoy en día se están desarrollando sistemas de simulación física completa del entorno de proceso, denominados Process Twins o Twin-Control. Mediante estos sistemas se pretende abordar de forma conjunta dichos problemas para una amplia gama de procesos de corte, no sólo modelizando de manera virtual todo el proceso, sino, a su vez, implementando también en él modelos mecanísticos que han funcionado de manera individual hasta ahora.
Modelos de procesos físicos
La fabricación de piezas de alta calidad al precio más bajo posible y en el menor tiempo posible requiere de un análisis detallado en la fase de definición y desarrollo de las etapas del proceso. En el pasado, se ha demostrado la utilidad de las herramientas de simulación de proceso de cara a reducir el número de pruebas-error antes de llevar los parámetros a producción real [3].
Por ejemplo, las fuerzas de corte son responsables de deflexiones que dan lugar a errores de forma; en casos extremos, excesivas fuerzas generan sobrecargas que pueden dañar el husillo de alta velocidad o, como mínimo, el fallo prematuro de la herramienta. Por otro lado, las vibraciones tipo chatter deterioran la superficie, pueden dejar marcar imborrables sobre la pieza y dañar también partes de la máquina. Por tanto, es fundamental que el ingeniero de producción sea capaz de elegir unos parámetros de mecanizado adecuados. Tradicionalmente, ante la duda, la estrategia habitual ha sido la selección de parámetros de corte conservadores y, por tanto, la reducción de la productividad. Bajo el paradigma de la Industria 4.0, esto debe cambiar.
En los últimos tiempos, ha surgido entre la comunidad industrial y en la científica, el término de gemelos de proceso, Process Twins o Twin-Control. Esta técnica consiste en el desarrollo de una simulación física completa del entorno del proceso de corte o gemelo digital, para el acercamiento a su otro gemelo, el mecanizado real. Mediante ella, se pretende dotar de generalidad a todos los desarrollos de modelización y simulación realizados en el pasado.
Muchos algoritmos numéricos han servido en el pasado para la resolución de problemas de mecanizado. Así, los casos más sencillos de predicción y control de fuerzas de corte, rugosidad superficial, temperatura o estabilidad de proceso, se consideran superados en el estado del arte. Por citar algunos, la detección de estabilidad en fresado para un solo grado de libertad y con parámetros dinámicos invariables en el tiempo (un modo dominante en la herramienta) o la predicción de rugosidad en el fresado periférico de Aluminio, son casos ampliamente documentados. Los modelos (mecanísticos) clásicos resuelven el problema, pero se trata de un único problema. Para la aplicación real, la práctica industrial requiere de modelos holísticos y acercamientos globales y generalizables a la gran gama de operaciones de corte posibles.
Para ello, debe hacerse acopio de toda una gama de algoritmos de modelización y predicción de parámetros de mecanizado. Un buen comienzo es partir del cálculo de fuerzas de corte, potencias y par en los procesos de corte. A partir de ahí, la modelización puede ser extremadamente compleja. Efectos no lineales como process damping, que altera las fronteras de estabilidad, especialmente en materiales de baja maquinabilidad; modos variables de la pieza a lo largo del mecanizado como en el fresado de acabado de piezas complejas, etc. hacen que la puesta a punto de las simulaciones para el mayor parecido posible con su gemelo real sea una labor titánica. La figura 2 muestra el intento de acercamiento desde el gemelo de simulación hacia el lenguaje de la máquina, donde se describe la trayectoria de la herramienta en función de la localización XYZ en el espacio y de la orientación espacial de la herramienta (vectores unitarios i, j, k).
![Figura 2. Modelo de interacción pieza/herramienta desarrollado por método Z-map y simulación de la trayectoria (y orientación) de la herramienta [4]... Figura 2. Modelo de interacción pieza/herramienta desarrollado por método Z-map y simulación de la trayectoria (y orientación) de la herramienta [4]...](https://img.interempresas.net/fotos/1883697.jpeg)
Desde el punto de vista del mecanizado real, se necesita de una monitorización eficaz [5]. Poniendo el foco en la máquina-herramienta, uno de los últimos hot-topic a nivel internacional y europeo es el de la máquina monitorizada y conectada. La toma de datos de forma contínua para el reajuste rápido de los parámetros de corte, detección de fallos de forma prematura, diagnóstico y mantenimiento remoto, etc. es ya casi una realidad [6]. La figura 3 da una idea de la envergadura del proyecto europeo Twin Control, con las ubicaciones, casos de estudio y socios estratégicos: fabricantes (Goratu, Comau, Chiron, …), socios tecnológicos (Tekniker, Marposs, Artis, …) y Universidades (Aachen, AMRC Sheffield, País Vasco - Bilbao, …) involucrados.
![Figura 3. Ubicación de socios y empresas involucrados en el proyecto Twin Control [6] Figura 3. Ubicación de socios y empresas involucrados en el proyecto Twin Control [6]](https://img.interempresas.net/fotos/1869368.jpeg)
Para la toma de datos intensiva, debe aprovecharse la sensorización inherente a la máquina: posición, velocidad, aceleración y jerk de los ejes, velocidades de husillo, pares y potencias consumidas, etc. Esto, tradicionalmente ha sido un problema, ya que los CNC no estaban preparados para la extracción de datos.
Pueden utilizarse programas comerciales o también es posible la programación con sistemas más abiertos y personalizables como por ejemplo Labview e NI. Sin embargo, en este caso, las necesidades de programación son mucho mayores. La figura 4 representa un diseño típico de arquitectura de monitorización, donde la empresa Artis está bien posicionada. El módulo del sistema de adquisición (Artis Genior Modular, GEM) obtiene datos en tiempo real del CNC/PLC. Dependiendo de las necesidades y el control de la máquina, se elige el tipo de protocolo de comunicación (Artis Fagor CAN, Profibus, etc.) para recoger el número de señales y los tiempos de muestreos adecuados. Para necesidades de guardado importantes, el grabador del Artis (OPR) puede conectarse al GEM y almacenar cientos de GB.
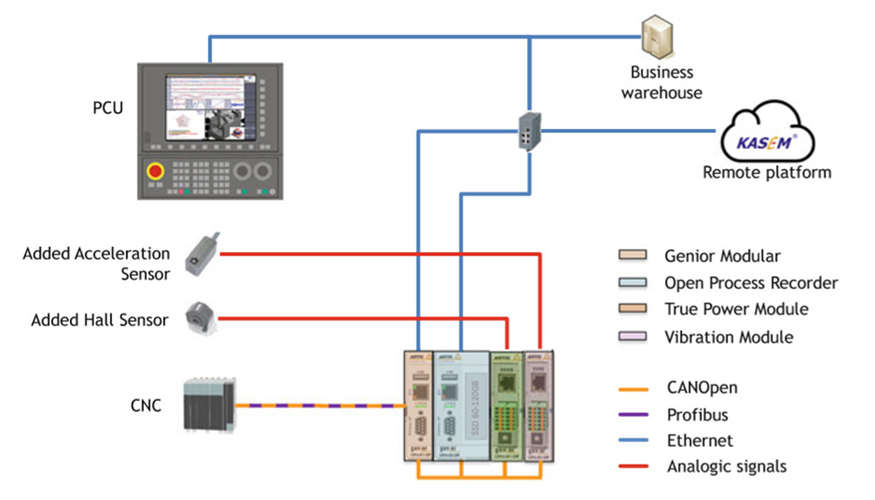
El Control por gemelo requiere una representación virtual de la máquina y de la forma de la pieza. Un buen ejemplo es el software ModuleWorks (Aachen) que utiliza las aplicaciones MachSim para crear la geometría 3D y cinemática de la máquina y CutSim para generar el status actual de la pieza durante el mecanizado, para su posterior implementación en la interfaz CNC. La idea del doble gemelo es generalizar y optimizar este enfoque.
Como se muestra en la figura 5, parte de los datos de monitorización (Genior Modular de Artis) correspondientes a la posición de la herramienta son bifurcados para su reutilización por el CAM. Por otro lado, el lazo se cierra desde la obtención del par del husillo. De esta manera se cierran ambos lazos, simulación virtual y monitorización real, para estrechar el vínculo entre los dos gemelos.
![Figura 5. Flujo de trabajo entre monitorización de ejes máquina y datos de proceso [7] Figura 5. Flujo de trabajo entre monitorización de ejes máquina y datos de proceso [7]](https://img.interempresas.net/fotos/1883701.jpeg)
Así, la integración de la monitorización del proceso sobre la simulación CAM es ya hoy una realidad posible. El CAM puede hacerse más inteligente y optimizar los parámetros de mecanizado en aquellas zonas donde se detecten grandes desviaciones entre la geometría deseada y la medida. Para ello, pueden correlacionarse los datos obtenidos vía monitorización con los resultados de la pieza medida. Además de esto, las simulaciones de fuerzas de corte para otras condiciones, ayudarán a reorientar y replanificar las estrategias y operaciones sobre la pieza.
Modelos de procesos basados en correlaciones
Otra forma de abordar los problemas del mecanizado más cercana a las nuevas tecnologías es el uso de la inteligencia artificial en el sector de fabricación industrial, con el fin de reducir al mínimo la aparición de problemas durante la producción.
La inteligencia artificial es una alternativa que permite tener un mayor número de incógnitas y presentar una solución a sistemas más complejos de manera flexible; así, mediante el análisis de históricos de información del proceso, crea correlaciones y tendencias que prevén el comportamiento de las distintas variables envueltas en dicho proceso [8]. La figura 6 muestra diferentes estrategias para analizar el histórico de datos englobadas en la inteligencia artificial: lógica difusa, redes neuronales y estrategias combinadas.
![Figura 6. Descripción de las diferentes técnicas de estrategia inteligente [8] Figura 6. Descripción de las diferentes técnicas de estrategia inteligente [8]](https://img.interempresas.net/fotos/1869372.jpeg)
Entre las estrategias citadas anteriormente, las redes neuronales tienen gran aplicación en la industria de la fabricación. Estas estrategias ofrecen la posibilidad de que la propia máquina sea capaz de identificar patrones en el mecanizado y correlacionarlos con sus correspondientes causas y efectos. Esta alternativa permite tener un mayor número de incógnitas que los modelos mecanísticos.
Son diversos los ejemplos de aplicación de las redes neuronales en procesos de mecanizado; entre otros, una estimación en el proceso de torneado que relaciona las vibraciones autorregenerativas con el desgaste de una herramienta [9] o la predicción de errores en el espesor obtenido en la fabricación mediante la técnica de electroerosión por hilo (WEDM) [10].
Sin embargo, la cantidad de datos necesarios es tan grande que muchas empresas no disponen de tal cantidad de datos para poder implantar estos sistemas a día de hoy. Es por ello por lo que la sensorización de las máquinas se está volviendo tan importante, ya que no se sabe con total seguridad qué parámetro puede ser clave en la identificación y posterior corrección de un problema.
Formación avanzada de simulación de procesos mediante aulas virtuales y equipamientos de realidad virtual
Hasta ahora se han mencionado posibles métodos para afrontar problemas que se dan en los procesos de mecanizado, pero como las exigencias son máximas debidas a la complejidad de los productos, también hay que tener en cuenta el posible error humano del operario. Por ello, cada vez es más importante la formación para la correcta utilización del equipamiento. Hay operaciones que son muy críticas como es el caso de la soldadura, y la única manera de formación es la práctica. En la actualidad, con la emergencia en el mercado de equipamientos cada vez más complejos desde el punto de vista del usuario, los procesos de formación para la correcta utilización y mantenimiento del equipamiento son cada vez más importantes. En este sentido, dado el elevado coste de los equipamientos, la posibilidad de realizar formaciones en entornos de realidad virtual es una opción muy valorada tanto por las empresas como por los centros de formación de diferentes niveles educativos sobre todo en estudios de la rama tecnológica.
Son muchas las empresas que incorporan opciones de formación avanzadas de simulación de proceso a sus productos. En concreto, en el campo de la fabricación y la máquina herramienta destacan simuladores virtuales para la programación por control numérico, equipos de realidad virtual para el manejo de equipos de soldadura, etc.
Simulación del proceso de programación mediante control numérico:
La fabricación de un componente mediante mecanizado con control numérico requiere de una formación específica y depende en gran medida de la experiencia del programador. Sin embrago, la demanda de profesionales crece año a año y son muchas las personas que se forman en el sector metal-mecánico para cumplir con las demandas de las empresas. En este campo, los fabricantes de controles numéricos, en vista del gran volumen de gente en formación para familiarizarse con la fabricación mediante control numérico, han desarrollado simuladores virtuales para poder practicar una y otra vez sin ocasionar ningún error en máquina que conlleve a una posible rotura de herramientas, de pieza o componentes de la máquina y en consecuencia su correspondiente coste.
Los fabricantes de controles con mayor volumen de controles numéricos instalados en el mercado, como Heidenhain, disponen de controles independientes o estaciones de programación que pueden instalarse en un PC. De la misma forma, Fanuc, también dispone de estaciones de programación que permiten la simulación previa de los programas de mecanizado. También los fabricantes de controles Fagor incorporan esta opción que cuenta con las mismas opciones que el control real instalado en los centros de mecanizado y la misma disposición de todos los elementos.
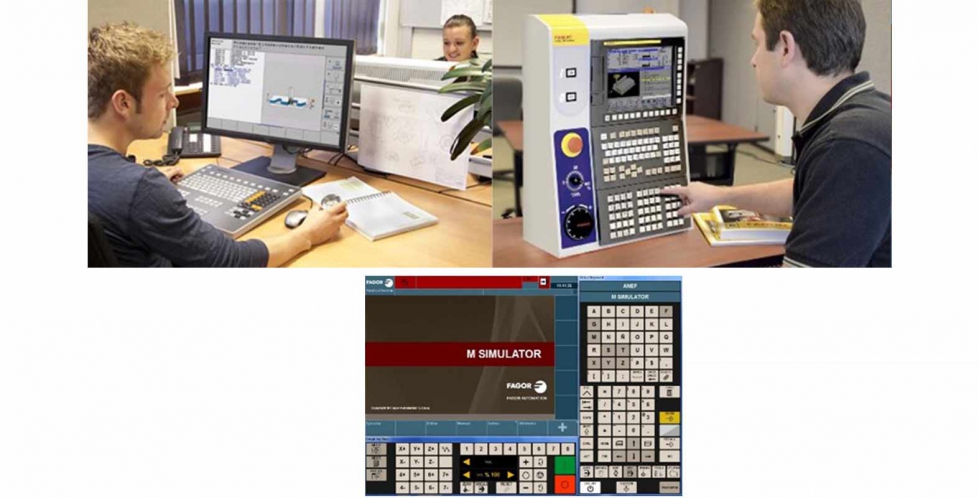
Figura 7. Izquierda: Simulador Heidenhain; Derecha: Simulador Fanuc; Abajo: Simulador Fagor.
Simulación del proceso de soldadura:
Otro proceso crítico y muy dependiente de la experiencia y habilidad del trabajador es la soldadura. Este proceso tan demandado en la industria requiere el conocimiento de diferentes técnicas. Además, se trata de un trabajo con alta tasa de accidentalidad teniendo en cuenta las localizaciones de ejecución de algunas soldaduras, el equipamiento que debe manejarse (gases, intensidades, voltajes...etc.) y el entorno de trabajo. Por todo ello, algunas empresas del sector han incorporado a sus productos equipos de soldadura virtual para la formación. Este es el caso de Fronius, que dispone de un simulador con diferentes módulos que permite a las personas en formación avanzar y trabajar con las diferentes técnicas de soldadura, así como diferentes niveles. El equipo cuenta con una réplica del equipamiento (soplete, EPI`s, etc.) que permite la práctica segura, así como el consecuente ahorro en material y recursos.
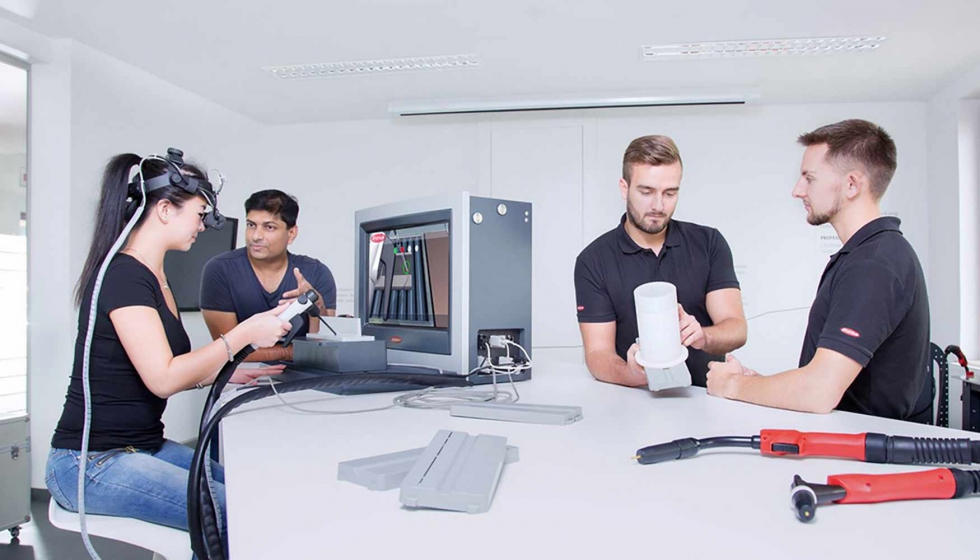
Utilización de herramientas de simulación para la mejora de precisión de los medios de producción
En 2019 el uso intensivo de modelos, tanto basados en principios físicos como en correlaciones de datos, es una realidad incuestionable en campos como el diseño mecánico (FEM), dinámica de fluidos (CFD), y muchos campos de la ingeniería. Las plantas de producción por otra parte han sido objeto de múltiples trabajos, tanto las de evento continuo (Scadas), como las de evento discreto. Si bien en la década de los 80-90 se hizo un gran avance bajo el paraguas del CIM, es en 2019 cuando se puede llegar a desarrollar sistemas de simulación, con unión directa a los sistemas de gestión de plantas (MES) o de proyectos. Es la captación de datos en planta uno de los puntos clave. En cada lugar geográfico se tiende a utilizar un nombre (4.0, IoT, IoE), pero lo que realmente supone es poder tener datos en tiempo real para adaptarse de forma rápida a los cambios.
La Jimtoff de 2018 además ha supuesto una afirmación por la vía de la gestión a los conceptos. Mazak, Okuma, DMGMori, Toyoda (Toyota) ya han establecido un campo de desarrollo en tres niveles:
- Conectividad, vía dispositivos de planta con posibilidad de conexión a los CNCs, buses de campo (MTconnect, profibus, Fieldconnect) o sensores más o menos inteligentes. Los dispositivos CPS empiezan a ser bastante habituales en los subórganos de las máquinas, con capacidad de edge computing.
- Filtrado y conexión a sistemas de almacenamiento de datos, bien en la nube, en el denominado ‘data lake’ o en sistemas propios. El acondicionamiento de los datos es clave, pues formatos, bases de datos, etc. deben ser el buffer de información colectiva a diferentes sistemas de la planta.
- Uso de los datos por los sistemas de gestión, planificación de la producción, supply chain. Y es en este nivel donde modelos predictivos de sistemas aislados pueden intervenir de forma decisiva, pues es la predicción la clave de poder establecer formas óptimas de producción.
La conexión al sistema de simulación es la vía de poder realizar el control de las plantas con información veraz de los medios disponibles, conectando con las formas de simulación predominantes.
La siguiente es una lista de técnicas de simulación populares: [11]
- Simulación física de los procesos, atendiendo a sus principios naturales.
- Simulación de eventos discretos (DES)
- Dinámica del sistema (SD)
- Modelado basado en agentes (ABM)
- Simulación inteligente: basada en una integración de técnicas de simulación e inteligencia artificial (AI)
- Red de Petri
- Simulación de Monte Carlo (MCS)
- Simulación virtual: permite al usuario modelar el sistema en un entorno inmersivo en 3D.
- Técnicas híbridas: combinación de diferentes técnicas de simulación.
Cada sistema permite una simulación determinada, que se resumen en la siguiente tabla.

Por lo tanto, las fábricas inteligentes serán el motor del cambio en un entorno conectado, que no para de evolucionar, donde las personas y su conocimiento seguirán siendo, aún con mayor fuerza, las piezas tractoras de su actividad.
Referencias
[1] http://www.autracen.com/internet-de-la-cosas-industrial/
[2] https://www.tecnalia.com/images/stories/Catalogos/informe-fabrica-del-futuro.pdf
[3] Altintas, Y.: Manufacturing Automation. Cambridge University Press, Cambridge (2012).
[4] Budak E. (2018) Machining Process Improvement Through Process Twins. In: Ni J., Majstorovic V., Djurdjanovic D. (eds) Proceedings of 3rd International Conference on the Industry 4.0 Model for Advanced Manufacturing. AMP 2018. Lecture Notes in Mechanical Engineering. Springer, Cham.
[5] Stavropoulos, P., Chantzis, D., Doukas, C., Papacharalampopoulos, A., Chryssolouris, G.: Monitoring and control of manufacturing processes: a review. In: 14th CIRP Conference on Modeling of Machining Operations (CIRP CMMO), vol. 8, pp. 421–425 (2013).
[6] http://twincontrol.eu
[7] Twin-Control: A digital approach to improve machine tools lifecycle, ISBN 978-3-030-02203-7, 2019.
[8] Ramírez, J.A., Sarmiento, H.O., López-Lezama, J.M. Diagnóstico de fallas en procesos industriales mediante inteligencia artificial. Revista espacios, Vol. 39(nº24), 12, ISSN 0798 1015, 2018.
[9] Sepúlveda, Alex & Illanes, Alfredo. (2013). Hacia la detección automática del desgaste de una herramienta de corte en un proceso de torneado CNC.
[10] Sanchez, J.A., Conde, A., Arriandaga, A., Wang, J., Plaza, S. Unexpected Event Prediction in Wire Electrical Discharge Machining Using Deep Learning Techniques. Materials 11(7): 1100, 2018
[11] Jahangirian, Mohsen; Eldabi, Tillal; Naseer, Aisha; Stergioulas, Lampros K.; Young, Terry (2010-05-16). Simulation in manufacturing and business: A review. European Journal of Operational Research. 203 (1): 1–13.
[12] Best Simulation Software | 2016 Reviews of the Most Popular Systems. www.capterra.com. Retrieved 2016-05-13.