Conectividad de alta velocidad para la obtención de información en plantas hiperconectadas
En las plantas hiperconectadas, la eficiencia y calidad dependen en gran medida de la adquisición de datos y la implementación de modelos predictivos, lo que hace que estas tecnologías sean esenciales.
Sin embargo, a pesar de su enorme potencial, aún existen obstáculos que obstaculizan su adopción generalizada en numerosas empresas, como indica el informe de la Comisión Europea sobre la Estrategia Europea de Datos [1]. Una de las principales razones de esta situación es la complejidad asociada con la extracción de datos de producción, especialmente en entornos de fabricación avanzados donde se buscan análisis en tiempo real. La complejidad de este desafío surge de la diversidad de fuentes y protocolos de comunicación industrial disponibles, la falta de estandarización, la carencia de interoperabilidad entre sistemas y equipos, así como la variabilidad en los formatos y la calidad de los datos.
En la figura 1 se presentan las diversas fases que componen el ciclo de vida de los datos. La primera fase se centra en la obtención de datos relevantes, requiriendo la determinación de la manera de acceder a ellos. Una vez recopilados los datos, es necesario procesarlos y transformarlos para su posterior análisis y entrenamiento de modelos. Seguidamente, se lleva a cabo la etapa de publicación de datos, que puede involucrar el uso de modelos para realizar predicciones o con fines de visualización. Finalmente, el almacenamiento de datos garantiza su disponibilidad para usos futuros.
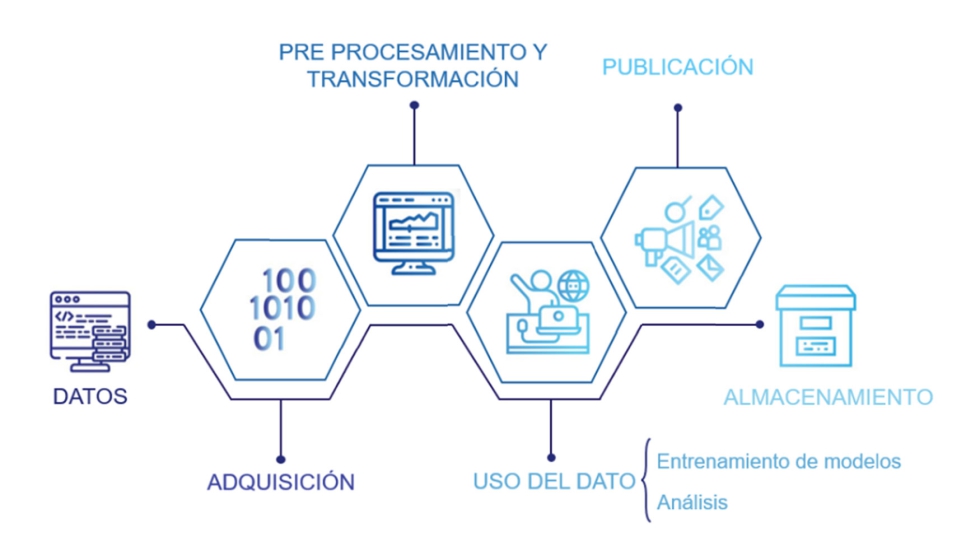
En entornos de fabricación avanzados, las máquinas suelen incorporar PLC para gestionar la automatización y el manejo de datos. La creciente necesidad de conectividad de estos PLC, cumpliendo con los estándares de la industria mediante protocolos disponibles, facilita la interconexión de máquinas, equipos y sistemas en una red industrial. Esto garantiza una supervisión completa y control sobre las actividades en el área de producción. Para aprovechar los datos y explorar las aplicaciones de la Industria 4.0, resulta crucial adquirir datos con la latencia adecuada según los objetivos de la aplicación.
Protocolos de comunicación industrial
En esta sección se explorarán los fundamentos de la comunicación industrial a través de protocolos clave como Modbus, Profibus, Profinet, Ethernet/IP y OPC UA, seleccionados por su amplio uso en la industria [2]. A lo largo de las décadas, estos protocolos han evolucionado para mejorar la velocidad, interoperabilidad, seguridad y capacidad de manejar grandes volúmenes de datos, facilitando una comunicación más eficiente en entornos industriales y la implementación de tecnologías avanzadas como la Industria 4.0.
Estos protocolos, desarrollados para satisfacer las crecientes demandas de conectividad y eficiencia en la industria, desempeñan un papel vital en la automatización y control de procesos. Desde la transmisión de datos en tiempo real hasta la interoperabilidad entre sistemas, cada uno contribuye a la eficacia operativa. La sección también presenta una comparación detallada para ofrecer una visión integral de sus fortalezas y aplicaciones específicas.
Modbus
Modbus es un protocolo de comunicación industrial empleado en la transferencia de datos entre dispositivos en sistemas de automatización y control de procesos [3]. Adopta un modelo cliente/servidor que facilita la comunicación entre dispositivos conectados mediante varios tipos de buses o redes.
Para iniciar una conexión Modbus, se configura un dispositivo como servidor y otro como cliente. Al iniciar una conexión TCP/IP, el cliente envía una solicitud al servidor, que responde transmitiendo la información solicitada a través de un canal. Modbus utiliza varios tipos de mensajes de datos para leer o escribir información en dispositivos compatibles, siendo Modbus RTU uno de los métodos más comunes de comunicación serial.
Modbus destaca por su capacidad para conectarse con una amplia gama de dispositivos y su confiabilidad en la transmisión de datos. Además, al ser un protocolo de código abierto, cuenta con numerosas bibliotecas de alto nivel para diversos lenguajes de programación.
Por otro lado, Modbus TCP presenta limitadas funciones de seguridad integradas. La falta de cifrado y autenticación por defecto lo deja vulnerable a accesos no autorizados y manipulación de datos. Para fortalecer la seguridad, implementar medidas adicionales como Redes Privadas Virtuales (VPNs) y métodos de cifrado de capa de aplicación, como Transport Layer Security (TLS) o Secure Sockets Layer (SSL), puede proteger de manera efectiva las comunicaciones Modbus TCP contra posibles amenazas.
Profibus y Profinet
Profibus es un estándar de red digital para bus de campo abierto utilizado en entornos industriales para interconectar componentes de automatización de procesos, como sensores de campo, actuadores y PLCs [4]. La arquitectura de Profibus sigue un modelo cliente/servidor, permitiendo al servidor, como controlador de procesos, supervisar la comunicación con clientes que pueden ser controladores, motores, dispositivos de entrada/salida y robots. Para establecer conexión con un dispositivo Profibus, es esencial contar con una red operativa y configurada, asignar una dirección al dispositivo y establecer un canal de comunicación con un servidor Profibus, como un PLC u otro dispositivo similar.
Con los cambiantes requisitos de las redes industriales, Profibus ha quedado obsoleto en comparación con protocolos de campo más modernos como Modbus TCP, Ethernet/IP y Profinet.
Profinet, un bus de campo basado en Ethernet con una arquitectura abierta y estandarizada, ofrece ventajas significativas sobre su predecesor, incluyendo tasas de transmisión de datos más rápidas, mayor flexibilidad y mejor escalabilidad [5]. La migración de Profibus a Profinet ha permitido a los sistemas industriales aprovechar los beneficios de la comunicación basada en Ethernet, lo que resulta en mayor eficiencia, mejor interoperabilidad e integración del sistema simplificada.
Profibus, al ser un protocolo más antiguo, carece de mecanismos integrados de cifrado y autenticación por defecto, lo que lo expone a posibles vulnerabilidades de seguridad. En contraste, Profinet ofrece avanzadas funciones de seguridad, como autenticación mediante certificados X.509 y nombre de usuario/contraseña, así como cifrado mediante TLS o Secure Real-Time Transport Protocol (SRTP). Estas medidas garantizan la confidencialidad e integridad de los datos en Profinet, ofreciendo una sólida protección contra el acceso no autorizado y la manipulación de datos.
Ethernet/IP
Ethernet/IP es un protocolo de comunicación industrial basado en la tecnología Ethernet que permite la transferencia de datos en tiempo real entre dispositivos de diversos fabricantes y tecnologías [6]. Se basa en una arquitectura cliente/servidor y se utiliza extensamente en aplicaciones de control en entornos de producción que demandan la transmisión eficiente de datos a velocidades y volúmenes elevados.
Para desplegar Ethernet/IP, es necesario conectar varios dispositivos, como sensores, actuadores y controladores, a una red compartida y permitirles comunicarse entre sí para coordinar las operaciones de producción. Esto implica conocer las direcciones IP y los nombres asignados a estos dispositivos, así como configurarlos para la comunicación en intervalos de tiempo específicos. Posteriormente, se inicia una conexión TCP/IP con cada dispositivo para facilitar el intercambio de mensajes de entrada/salida.
Ethernet/IP ofrece varios beneficios, como transmisión de datos a alta velocidad, escalabilidad para integrar una amplia gama de dispositivos, y facilidad de configuración y resolución de problemas. Además, al ser un protocolo estandarizado, es más fácil de mantener.
En comparación con Modbus TCP, Ethernet/IP ofrece características de seguridad más robustas. Admite mecanismos de autenticación, incluida la autenticación basada en nombre de usuario y contraseña, para verificar la identidad de dispositivos y usuarios. Además, Ethernet/IP admite IPSec (Internet Protocol Security), que proporciona confidencialidad, integridad y autenticación para comunicaciones basadas en IPs. Al implementar IPSec, los datos intercambiados entre dispositivos pueden cifrarse, protegiéndolos contra el acceso no autorizado.
OPC UA
OPC-UA es un protocolo de comunicación multiplataforma diseñado para el intercambio seguro y confiable de datos en el ámbito de la automatización industrial [7]. La arquitectura OPC está compuesta por uno o más servidores OPC y clientes OPC.
OPC-UA facilita un flujo constante de datos entre múltiples dispositivos y aplicaciones de control con restricciones limitadas, sirviendo como medio de comunicación tanto entre aplicaciones de Supervisión, Control y Adquisición de Datos (SCADA) como entre sensores. Para mantener una comunicación activa y continua entre clientes y servidores, son esenciales las conexiones bidireccionales y las sesiones persistentes. En términos de frecuencia de captura, OPC-UA se emplea típicamente para monitorear un conjunto reducido de variables, generalmente de 1 a 10.
Además se ha establecido como el protocolo de comunicación predeterminado para la Industria 4.0 [8]. Proporciona ventajas notables, incluyendo altos niveles de seguridad, transmisión en tiempo real de grandes volúmenes de datos y una gran escalabilidad. Su independencia tecnológica garantiza la compatibilidad con dispositivos y plataformas de distintos fabricantes y sistemas operativos. No obstante, la implementación de OPC-UA en entornos con numerosos dispositivos puede ser tanto compleja como costosa.
OPC-UA fue diseñado con la seguridad como un aspecto fundamental. Soporta protocolos de seguridad de capa de transporte, como TLS/SSL, permitiendo la encriptación y autenticación para una transmisión segura de datos. Además, OPC-UA incluye mecanismos de control de acceso que posibilitan a los administradores establecer políticas detalladas de acceso para usuarios y dispositivos.
Comparativa entre protocolos
La tabla 1 presenta una comparativa de los cinco protocolos mencionados anteriormente, abordando aspectos como el alcance de transmisión, frecuencia, tasa de datos y seguridad. En el análisis, se destaca que Modbus, Profibus y Profinet son idóneos para redes locales, mientras que Ethernet/IP y OPC-UA son más apropiados para redes de área extensa, siendo OPC-UA el que ofrece un rango de transmisión ilimitado. Asimismo, Ethernet/IP y Profinet exhiben la frecuencia más elevada, oscilando entre 1 y 100 MHz, y la tasa de datos más alta, con la capacidad de alcanzar velocidades de hasta 1 Gbps.
Estas características, en conjunto, son esenciales a la hora de seleccionar un protocolo industrial adecuado para una aplicación específica, considerando el tamaño y la complejidad de la red, el número de dispositivos a emplear y la cantidad de datos a transmitir.
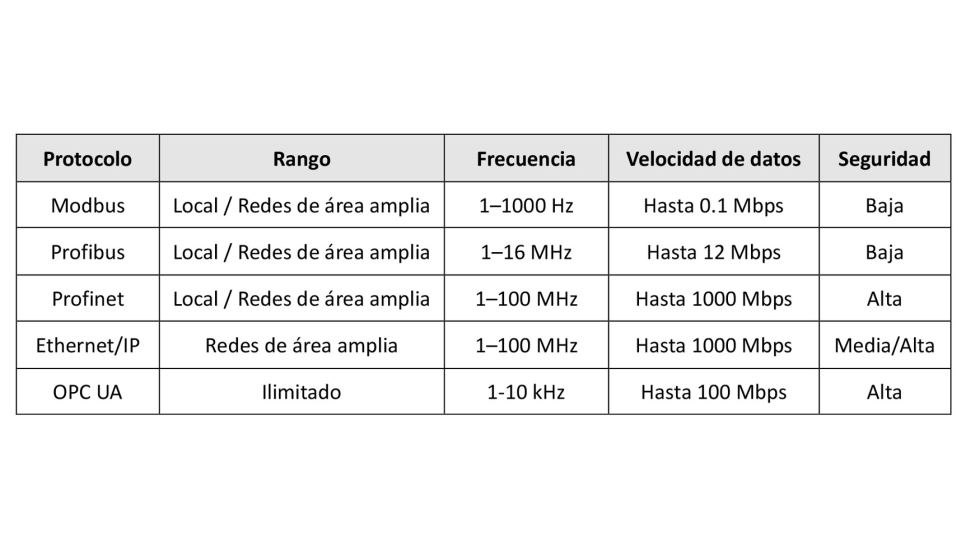
La figura 2 presenta la distribución porcentual del uso de protocolos industriales, basada en un estudio realizado por HMS Networks en 2019 [9]. En ese año, el 59% de los nodos recién instalados correspondieron al Ethernet industrial, mientras que los buses de campo representaron el 35% de la utilización industrial. Ethernet/IP se destacó como la red predominante, abarcando el 15% de las instalaciones totales, mientras que Modbus TCP se empleó en un 4% de los casos. En la categoría de buses de campo, Profibus DP lideró con un 10% de cuota de uso. Adicionalmente, se observó un incremento del 30% en la incorporación de tecnologías inalámbricas, atribuido al rápido progreso del Internet de las cosas (IoT) y al aumento de dispositivos móviles en los entornos periféricos.
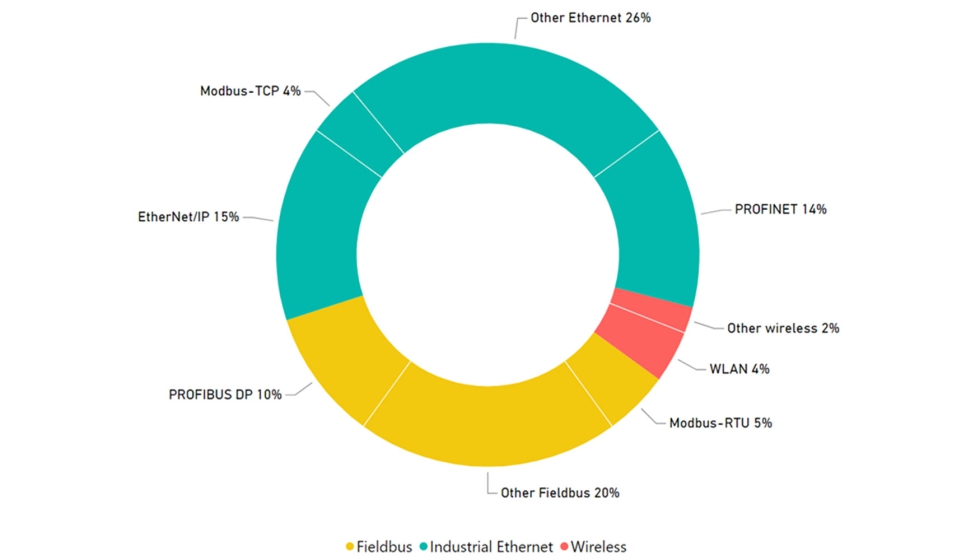
Caso de uso: infraestructura con tecnologías open source para gestión de datos industriales
En el ámbito de la detección de anomalías y la construcción de plataformas de monitoreo, las herramientas de código abierto desempeñan un papel fundamental. Estas herramientas no solo proporcionan flexibilidad y personalización, sino que también fomentan la colaboración y la transparencia en el desarrollo de soluciones tecnológicas.
La implementación de plataformas que ejecuten la detección en tiempo real de anomalías se facilita mediante el empleo de herramientas de código abierto, tal como se ejemplifica en la figura 3. La arquitectura de esta plataforma se ha desarrollado utilizando herramientas ‘open source’ del ecosistema Apache. Cabe destacar que se está abordando específicamente un flujo de datos que se origina en el centro de mecanizado monitorizado y culmina en una representación visual.
Los componentes de software se implementan en distintas máquinas virtuales, conformando una arquitectura de sistema distribuido. Estas máquinas constituyen un clúster Kafka que opera de manera distribuida, encargándose del almacenamiento, recepción y envío de mensajes entre sus diversos brokers. La gestión y coordinación de los brokers recae en Zookeeper, que también asigna un broker para desempeñar el rol de líder.
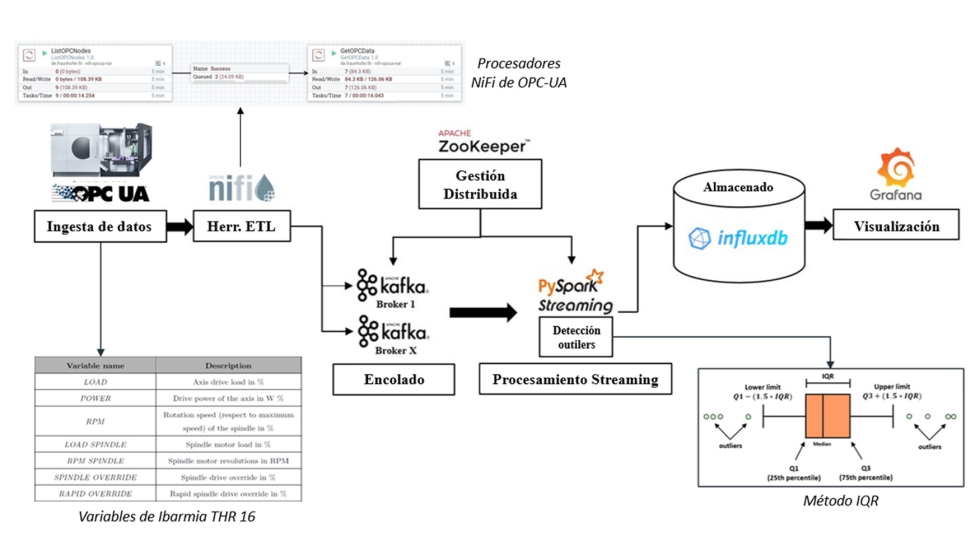
Como se observa en la figura 3, en el inicio del proceso, se adquiere un conjunto de variables de un centro de mecanizado a través de OPC-UA, utilizando el software de la plataforma como cliente OPC y el PLC del centro como servidor OPC. La frecuencia de captura de OPC-UA se ajusta para monitorizar un conjunto específico de variables críticas de la máquina. Seguidamente, NiFi lleva a cabo la extracción y transformación de estas variables, configurando dos procesadores personalizados para establecer un flujo de datos entre el Servidor OPC y NiFi, obteniendo los valores del PLC de la máquina de mecanizado.
Posteriormente, los datos se envían a un sistema de colas, como Kafka, que retiene los datos hasta que PySpark los consume, asegurando la secuencia de entrega mediante el método FIFO. PySpark, en su modalidad Streaming, procesa y analiza el conjunto de datos utilizando DataFrames, comparándolos con lecturas históricas para supervisar el estado actual de cada variable y detectar posibles anomalías.
En cuanto al almacenamiento y persistencia de datos, se opta por InfluxDB como base de datos no relacional, donde los datos de series temporales se almacenan y ordenan según las marcas de tiempo. La visualización de estos datos se realiza a través de Grafana, que efectúa consultas a InfluxDB y presenta los resultados en un cuadro de mandos mediante paneles, facilitando la interpretación intuitiva de los valores para los trabajadores de la fábrica.
Pruebas y resultados
En esta sección, abordamos pruebas que examinan el rendimiento de 3 de los protocolos industriales mencionados anteriormente, centrándonos en la tasa de muestreo y el uso de CPU y RAM como aspectos clave. Al evaluar la tasa de muestreo, buscamos determinar la eficiencia de los protocolos en la transmisión y recepción de datos. Asimismo, la evaluación del uso de CPU y RAM proporciona perspectivas sobre el impacto de estos protocolos en los recursos computacionales del sistema.
La extracción de variables del PLC se realiza, como se muestra en la figura 4, mediante una conexión directa con la máquina utilizando un cable Ethernet. Este proceso requiere conectar el cable a un equipo con un entorno Python y las librerías necesarias para extraer datos, o a un entorno NiFi.
Durante las pruebas, se evaluaron tres protocolos en tres máquinas distintas. Específicamente, se empleó Modbus TCP para obtener variables de la máquina de brochado EKIN A218, Ethernet/IP para la máquina de torneado Danobat TV-1500 y, finalmente, OPC-UA para extraer variables de la fresadora de 5 ejes IBARMIA THR 16.
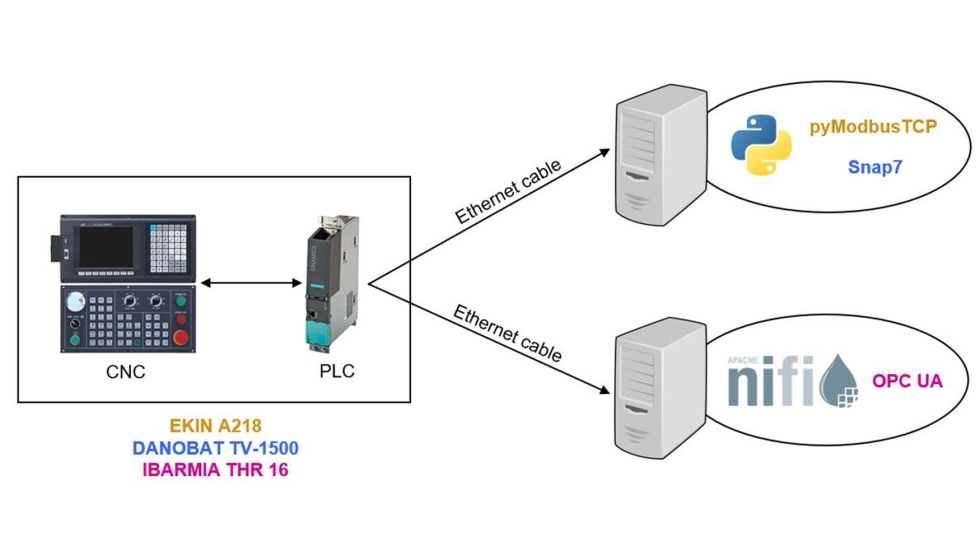
Frecuencias de muestreo
En entornos IIoT, lograr una conectividad de alto rendimiento es crucial debido a la importancia de los requisitos de baja latencia en la toma de decisiones en tiempo real para aplicaciones de extracción de datos. En esta sección, nos enfocamos en evaluar la tasa de muestreo de los protocolos industriales.
En la primera prueba, se midió el tiempo que emplea cada protocolo en recuperar lotes de diferentes tamaños, donde cada lote corresponde a un conjunto distinto de variables de la máquina. Además, se recopilaron métricas de rendimiento para lotes más grandes para evaluar la escalabilidad de la plataforma.
En la figura 5 se presentan las tasas de muestreo obtenidas al extraer diversas cantidades de variables mediante cada protocolo. En este análisis, todas las variables adquiridas eran de tipo Float y ocupaban 4 bytes cada una. Los resultados se derivaron de cinco mediciones separadas, donde un equipo estaba conectado directamente al centro de mecanizado correspondiente, como se ilustra en la figura 4.
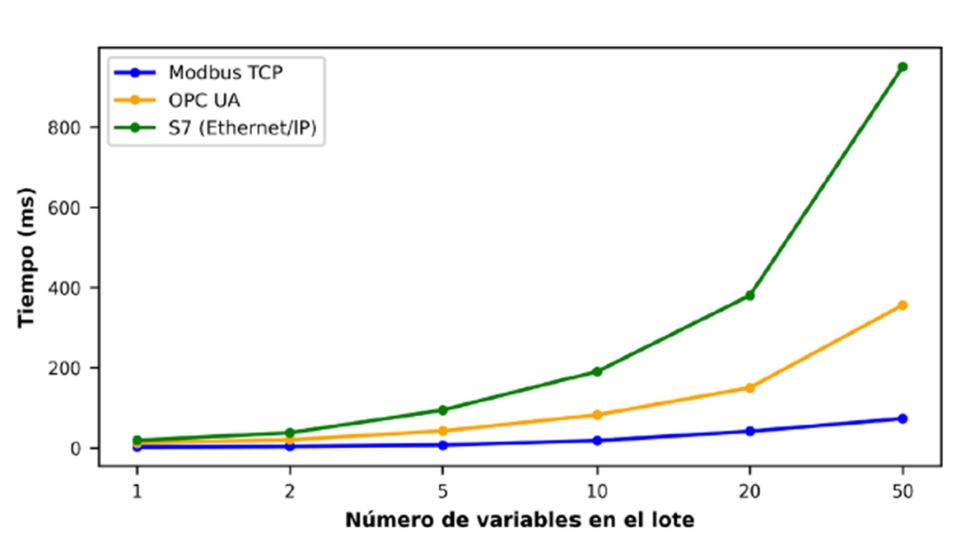
Modbus presentó la tasa de muestreo más alta entre los tres protocolos, seguido por OPC-UA, mientras que Ethernet/IP exhibió el tiempo de procesamiento más prolongado. Es esencial destacar que las pruebas no involucraron un mayor número de variables para evitar sobrecargar el PLC de cada máquina. Para asegurar un rendimiento óptimo del PLC de la máquina, se recomienda ajustar la frecuencia de adquisición o el número de variables por lote.
Consumo de CPU y RAM
La evaluación del impacto de los protocolos de comunicación en los recursos del sistema, especialmente en los retrasos en la adquisición de datos, se llevó a cabo mediante un análisis del consumo de CPU y RAM en el equipo encargado de la captura de datos. La prueba consistió en recuperar lotes de 50 variables, utilizando el comando top de Linux durante 2 minutos con todos los recursos activos. Durante las pruebas, se observó una variación mínima en el consumo de CPU y RAM al solicitar de 1 a 50 variables.
Los resultados, presentados en la tabla 2, indican niveles relativamente bajos de consumo de CPU y RAM, sugiriendo que el entorno ETL o de programación no se convierte en un cuello de botella. Entre los protocolos evaluados, Ethernet/IP mostró el mayor consumo de CPU con un 45%, mientras que OPC-UA consumió la mayor cantidad de memoria RAM con un 37%, atribuible a la inclusión de procesadores NiFi. Estos hallazgos sugieren que el rendimiento general de la extracción de variables no se ve significativamente afectado, ya que el consumo de CPU y RAM se mantiene por debajo del 50% en todos los casos.
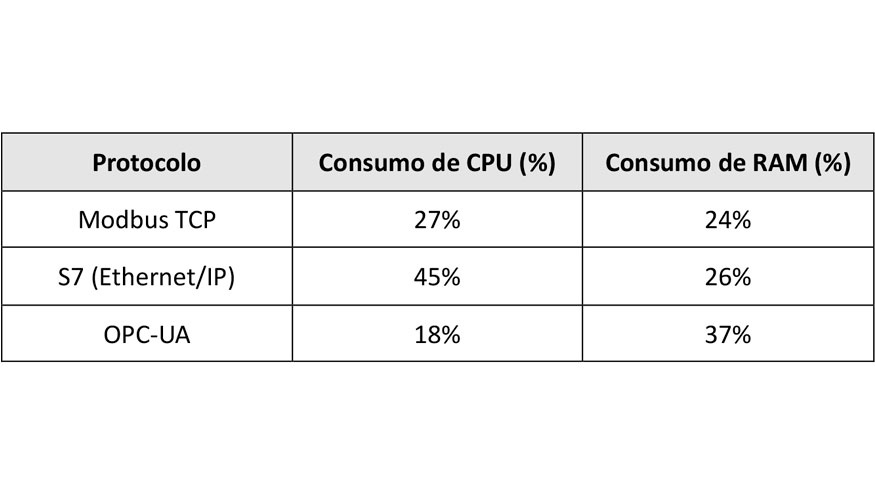
En resumen, la tabla 3 ofrece una visión general de las características proporcionadas por los protocolos utilizados en nuestros experimentos, incluyendo la frecuencia, complejidad del código y la infraestructura requerida. Esta información tiene como objetivo ayudar a otros expertos en la selección de un protocolo de comunicación adecuado para su aplicación específica de IIoT.
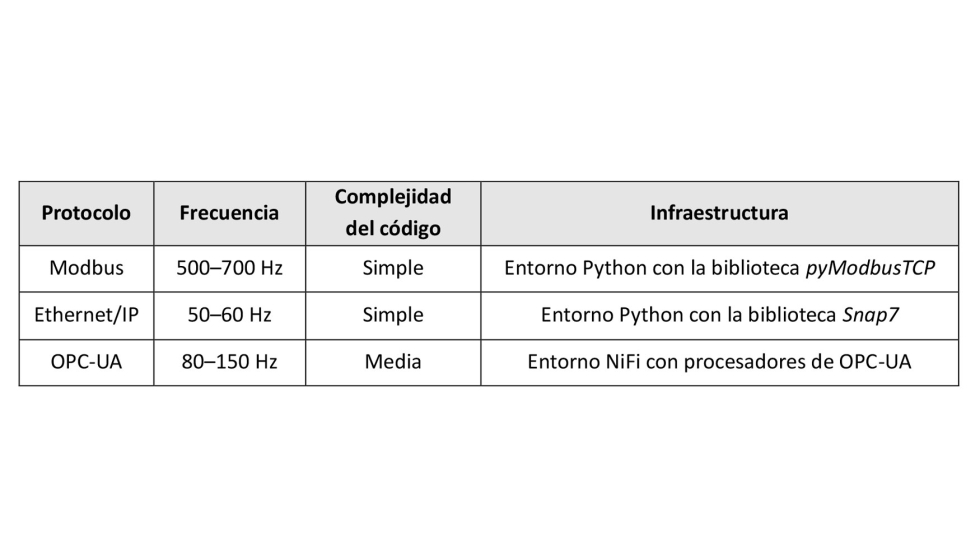
Referencias
[1] Estado actual de la digitalización en España. https://www.lainformacion.com/opinion/jorge-diaz-cardiel/estado-actual-de-la-digitalizacion-empresarial-en-espana/2853666/.
[2] Pereira, C.E.; Neumann, P. Industrial Communication Protocols. In Handbook of Automation; Springer: Berlin/Heidelberg, Germamy, 2009.
[3] Documentación de Modbus. https://www.modbus.org/specs.php
[4] Documentación de Profibus. https://www.profibus.com/technology/profibus/overview
[5] Documentación de Profinet. https://www.profibus.com/technology/profinet/overview
[6] Brooks, P. Ethernet/IP-Industrial Protocol. In Proceedings of the ETFA 2001 8th International Conference on Emerging Technologies and Factory Automation. Proceedings (Cat. No. 01TH8597), Antibes-Juan les Pins, France, 15–18 October 2001; Volume 2, pp. 505–514.
[7] Cavalieri, S.; Chiacchio, F. Analysis of OPC UA performances. Comput. Stand. Interfaces 2013, 36, 165–177.
[8] There Is No Industrie 4.0 without OPC UA-OPC Connect. https://opcconnect.opcfoundation.org/2017/06/there-is-no-industrie-4-0-without-opc-ua/
[9] HMS Report on Protocol Use in 2019. https://www.designworldonline.com/industrial-ethernet-takes-thelead-over-fieldbuses-says-study/