Nuevo artículo sobre Conceptos que hacen más fácil la vida en la planta de inyección
Las responsabilidades del inyectador
José Ramón Lerma, dpto. técnico de Biesterfeld Ibérica
08/04/2019Cuando pregunto en alguno de mis seminarios de Scientific Injection Molding a los asistentes, ingenieros de proceso, tecnólogos, preparadores de máquina e ingenieros de simulación, cuáles creen que son sus mayores responsabilidades en la fabricación de piezas por inyección, frecuentemente me contestan que estas responsabilidades son: la calidad del producto inyectado, el ciclo y la productividad, el rendimiento de la máquina, el aprovechamiento del personal o de la MOD o el correcto trato del molde y de la máquina. Entre todas las respuestas destacan con más frecuencia las responsabilidades que tienen que ver con la productividad y la calidad del producto.
Pero casi nunca aparecen respuestas que tengan que ver con el material o con el proceso mismo. Por ejemplo:
Mantener la máxima cristalinidad del material durante el proceso
La cristalización tiene lugar en los materiales semicristalinos en el intervalo de temperaturas entre la temperatura de fusión Tm y la temperatura de transición vítrea Tg, por debajo de la cual la cristalización no es posible. Si este cambio de temperatura durante el enfriamiento se produce muy rápido, las moléculas quedarán congeladas en una inestable estructura.
Si es usted quien define las condiciones de inyección, tiene bajo su responsabilidad definir esta velocidad de enfriamiento. Usted tiene el control de este aspecto tan importante y crucial par la vida del producto final inyectado. Indiferentemente del nivel de cristalinidad del polímero inyectado, la definición del proceso es la que va a determinar el nivel de cristalinidad del producto fabricado.
Es esta estructura de lamelas agrupadas en cristales la que nos va a dar la resistencia mecánica, la resistencia al creep, la resistencia al stress craking ESC, etc. Si no la obtenemos correctamente nuestras piezas no soportarán el uso esperado en su aplicación.
Yo pongo el ejemplo real en mis cursos de piezas inyectadas con POM o con PPS, materiales semicristalinos, a las cuales se les aplica una temperatura de molde baja para poder desmoldear rápido. Esto hace que el ciclo se reduzca y alguien consiga una mejora productiva, momentánea, porque si la pieza en cuestión está sometida a esfuerzos y altos requerimientos, la pieza fallará y las reclamaciones superarán con creces los beneficios obtenidos con la reducción de ciclo. Habremos obtenido un nivel bajo de cristalinidad. Siempre hay queso gratis en las trampas para ratones.
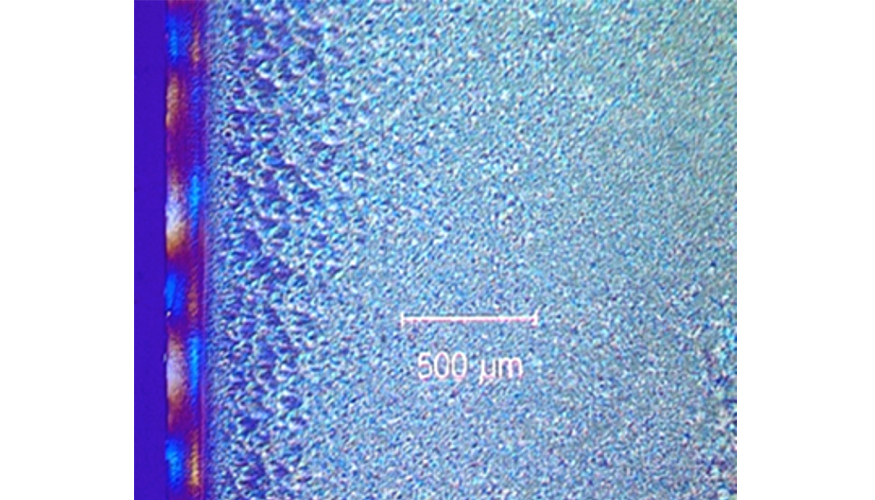
Mantener al máximo el peso molecular del material virgen original
Si nuestro proceso es muy “agresivo” con el polímero, puede producirse una pérdida de peso molecular. Esto va asociado a la longitud de la cadena molecular.
La reducción en el peso molecular determinará propiedades de requerimientos de corta duración, como el impacto y también de larga duración como el creep o plasto deformación. También la resistencia al stress cracking o ESC también se verán afectadas.
Pero ¿qué causas son las que agreden a la cadena molecular de los polímeros?
Condiciones tales como temperaturas de masa elevadas, tiempos de permanencia excesivos, cizalla en las entradas, cantos vivos, en algunos materiales el efecto de un mal o insuficiente secado, es precisamente una pérdida de peso molecular producido por la temida hidrólisis.
Estas pérdidas de peso molecular, hasta determinado nivel, pueden pasar inadvertidas para el inyectador ya que las piezas pueden no presentar un aspecto diferente, medidas etc. Pero sus propiedades estarán notablemente reducidas. Con frecuencia esto es detectado por el cliente final en el uso o utilización de las piezas.
Mantener al máximo el pack de aditivos que el material contenga
Otros casos son aquellos en los que por degradación térmica perjudicamos el pack de aditivos, por ejemplo de protección UV, acumulándose restos de este paquete de protección UV en las salidas de gases, colapsándolas y manchando frecuentemente los texturizados o acabados superficiales de las piezas. Además de estrangular el venting o salida de gases del molde, siendo necesario su limpieza a intervalos muy reducidos.
Esta es siempre la prueba evidente de que el aditivo no está pasando a la pieza inyectada sino que lo estamos evacuando a través de las salidas de gases.
La pieza fabricada en estas condiciones no soportará en el exterior la misma cantidad de radiación o tiempo en la intemperie durante su utilización debido a que dentro de la matriz del polímero no habrá suficiente pack del aditivo protector UV debido a las condiciones del proceso.
Otros pack de aditivos que podemos perjudicar en exceso son los retardantes de llama, los protectores a la hidrólisis, y por supuesto el pack de resistencia térmica que todo polímero lleva incorporado para resistir su paso por la unidad de inyección sin degradarse inmediatamente.
De este último pack de estabilización térmica, siempre se produce una pérdida al pasar por la inyectora. Por ello, no es recomendable la utilización de altos porcerntajes de recuperado ya que este se degradará más fácilmente durante su paso por la unidad de inyección.
Mantener al máximo la longitud y características de la carga de refuerzo (fibras, microesferas, nano cargas, etc.) que el material pueda contener
Hay casos frecuentes, en los que la velocidad de rotación de husillo, las entradas restringidas o una velocidad excesiva de inyección perjudica a la carga de refuerzo, por ejemplo fibras de vidrio. Esto provoca que la resistencia mecánica de la pieza obtenida no sea la deseada además de perjudicar de manera seria al desgaste prematuro del conjunto husillo – cámara de la unidad de inyección.
En definitiva, en el desarrollo del producto se define un material reforzado para poder aplicar o solicitar unos esfuerzos requeridos a las piezas y pagamos un material reforzado con unas propiedades excelentes y lo deterioramos durante el proceso, perdiendo parte de la ventaja del refuerzo.
Mantener el color original del material
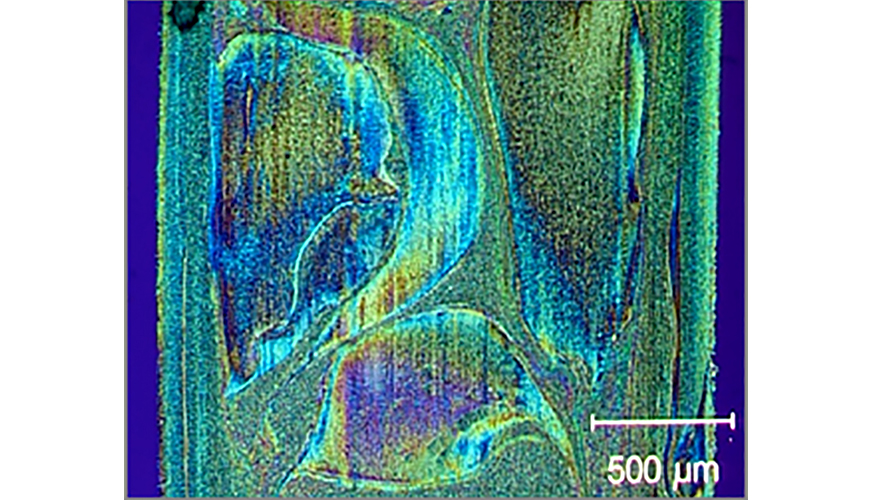
No perjudicar a los aditivos de color si los hay (masterbach) que puedan variar el color original deseado. Para ello las condiciones térmicas suelen ser críticas, temperatura de la unidad de inyección, revoluciones de husillo, contrapresión a la carga, tiempo de permanencia, etcétera.
Mantener la pieza inyectada sin stress aplicado por el proceso
Las condiciones de inyección pueden provocar que la pieza obtenida tenga un nivel de stress interno muy alto. Esto puede provocar roturas o deformaciones en el uso final de las piezas y una durabilidad menor de la esperada en las condiciones de utilización.
Son los parámetros definidos los que van a influir en el nivel de stress de las piezas.
No hay excusas
Como pueden ver, todas estas “responsabilidades" tienen que ver con mantener y cuidar propiedades y características que nos vienen dadas en el material plástico original y que con frecuencia no tenemos en cuenta.
Hay aspectos que son normalmente responsabilidad de otras funciones diferentes a la del ingeniero de proceso o inyectador, entre otras, las propiedades mecánicas intrínsecas del material seleccionado, la correcta selección del material empleado, el correcto diseño del molde y de la pieza o la correcta selección de la máquina de inyección y su capacidad o precisión, pero hay otras muchas que son responsabilidad exclusiva del inyectador como son las comentadas anteriormente.
Si tenemos en cuenta que todos estos factores comentados van a influir en la calidad y el rendimiento de la pieza en su aplicación nos damos cuenta de que no tenemos suficientemente claro cuál es nuestro rol en la calidad final del producto.
Podemos focalizarnos tan solo sobre la productividad por ejemplo (por supuesto no hay que perderla de vista) pero no podemos retirar el foco de los costes de la no calidad del producto. Esto pude provocar que los resultados finales no sean los deseados cuando se contabilicen el coste total soportado por el producto teniendo en cuenta la posible no calidad, reclamaciones, selecciones, muros de calidad, etcétera.
El inyectador, ingeniero de proceso, tecnólogo, o quien quiera que defina el proceso de inyección en una planta tiene la responsabilidad de mantener al máximo las propiedades que originalmente recibe en el material. No hay excusas, es nuestra responsabilidad.
José Ramón Lerma es autor del Libro Manual Avanzado de Inyección de Termoplástico, que tiene como objetivo ser, por un lado, una herramienta para la formación y, por otro, un manual de ayuda para todo el personal de una empresa de inyección de plásticos. El libro, comercializado por Plásticos Universales / Interempresas (libros@interempresas.net), consta de detallados casos prácticos, amplia información de moldeo científico y un ‘pendrive’ con 20 hojas de cálculo y herramientas de SC Molding o Scientific Injection Molding, además de optimización y definición de proceso, lo que lo hacen único en el mercado. Página web sobre Scientific Injection Molding: www.asimm.es