Los plásticos marcan nuevas pautas en la ingeniería naval moderna
28 de abril de 2008
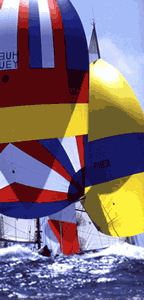
Mucha espuma bajo cubierta
"Miravella V", la encarnación de la visión de un alto directivo norteamericano del sector coches de alquiler, es un claro ejemplo de que algunos sueños sólo se pueden hacer realidad gracias al plástico: El casco de esta impresionante embarcación fue fabricado con plástico reforzado con fibra de vidrio en sándwich. La capa interna del casco de plástico reforzado es de espuma de PVC de la casa suiza Alcan Airex. Con el barco zarpan también unas 35 toneladas de este material configurado en gruesos paneles, que se ocupan de proporcionar un buen aislamiento contra el calor del trópico y el frío de los mares del norte. La envoltura interna de espuma hace que este velero de lujo sea prácticamente imposible de hundir, incluso aunque un huracán lo haga zozobrar en aguas caribeñas.
Por cierto, Vittoria también alquila el "Mirabella V", aunque por una ingente cantidad de dinero. Por un precio chárter de 250.000 dólares americanos por semana, los que lo deseen pueden participar de su sueño y, rodeados de un inmenso lujo, surcar los mares del sur. Muchas de las embarcaciones que acogió el recinto ferial de Düsseldorf, son también verdaderos sueños (o sueños hechos realidad).
Aire estival
La apariencia externa es el aspecto que más se valora en las embarcaciones de todos los tamaños. Se presta especial atención al diseño y a una cubierta atractiva. Lo que se esconde bajo ese envoltorio de aspecto tan perfecto no despierta tanto interés. El profesional sabe que se trata básicamente de material plástico: bajo el barniz brillante y aplicado generalmente en varias capas, se encuentra una resina de poliéster reforzada con vidrio o con carbono laminada.
Para la asociación alemana de empresas de deportes náuticos Bundesverband Wassersportwirtschaft e.V. (BWVS), el salón náutico boot de Düsseldorf es una ocasión idónea para presentar los números del sector y para abordar la situación del mundo náutico. En este sentido sólo hay buenas noticias. La temporada de deportes náuticos 2007 colmó las elevadas expectativas que se habían puesto en ella: la cifra de negocios de las empresas alemanas, a excepción de los proveedores de "superyates", ha aumentado un 6,8% y se ha situado en 1.877 millones de euros.
El sector también califica de positivas las perspectivas para este año, dado que se está consolidando la buena coyuntura por la que pasa el sector náutico.
También Bavaria Yachtbau, la empresa más importante del sector, cerró con un balance muy positivo el ejercicio 2006/2007, puesto que logró su objetivo de fabricar 4.000 embarcaciones (3.200 veleros y 800 embarcaciones a motor). Esto equivale a un incremento de más del 10% respecto del año anterior. De los astilleros de Bavaria, que cuentan con instalaciones de producción altamente automatizadas, salen cada año más de 3500 embarcaciones de distintos tamaños y diseños.
A finales del siglo pasado esta empresa de construcción de barcos bávara ya producía en serie cubiertas y cascos en la planta de laminación propia de los astilleros. Las capas de las esteras fabricadas con resina reforzada con fibra de vidrio se establecen para cada tipo de construcción mediante un plano de laminado utilizando la colocación manual, capa tras capa, que se sigue empleando hoy en día para proyectos singulares y de gran volumen. Se instaló un centro de mecanizado de control numérico (CNC) para el conformado integral de los tipos de cubiertas más habituales. Según unos datos predeterminados se pueden serrar los contornos exteriores de la cubierta de resina reforzada con fibra de vidrio y recortar las escotaduras correspondientes a las escaleras de bajada o a los cofres de las anclas. Para labrar las ventanas u otras aberturas, o el hueco para los asientos en la pieza preformada de resina reforzada, se utilizan unas fresas de punta de metal duro.
A diferencia de los procesos que se describen en este artículo, el material de elección clásico para la construcción de buques es el acero. En este tipo de barcos el aluminio y el plástico siguen siendo dos grandes excepciones. Existen algunos ejemplares de la armada, lanchas, barcos buscaminas o submarinos cuyos cascos cuentan con un armazón de plástico reforzado con fibra de vidrio. Se sabe, y ha dejado de ser secreto militar, que en Gran Bretaña se está utilizando para un portaaviones un casco de resina reforzada con fibra de vidrio indetectable para los radares. También son conocidos los frustrados intentos de Alemania de construir pequeños pesqueros de plástico y los intentos de construir barcos de paseo fluviales para excursiones y el transporte de personas, en este caso algo más exitosos y duraderos.
Hasta el momento, no obstante, los avances registrados no han conseguido aumentar el consumo de plásticos por parte de los astilleros internacionales. Los datos de que se dispone para determinar la cantidad precisa de plástico que se utiliza en la construcción naval no son exactos o bien son producto de estimaciones aproximativas. Según los cálculos de la empresa parisina JEC S.A., organizadora de la feria JEC Composites, que se celebra cada año en la capital francesa, aproximadamente el 6 por ciento del consumo de materiales de composite se produce por parte del sector de la construcción naval. No se trata de una cifra astronómica, pero con toda seguridad tampoco recoge la totalidad de materiales plásticos utilizados en la industria naval de todo el mundo.
Moldeo por soplado en la construcción de barcos
En Altenkirchen las embarcaciones se fabrican más rápidamente, si bien sus dimensiones son mucho más modestas: se trata de kayaks de dos colores fabricados en polietileno de alto peso molecular (PE). En dicha localidad, situada en las montañas de Westerwald, la empresa Rikutec fabrica cada cinco o seis minutos la estructura básica de una de estas embarcaciones deportivas. Como sucede con un cuerpo hueco convencional de plástico, como una botella, un bidón de gasolina o un cuerpo geométrico habitual del mismo tipo, estas embarcaciones se fabrican con PE fundido y se conforman en una máquina de moldeo por soplado de enormes dimensiones, en la que también se pueden fabricar tanques u otras piezas de gran volumen en caso necesario.
Tal y como describe un reportaje de la revista especializada alemana "Plastverarbeiter", el casco en bruto del kayak se conforma a partir de una manga de PE de unos cuatro metros de largo marcada longitudinalmente con dos colores. A continuación, se dota al casco de los asientos y de los reposapiés. Su sofisticado diseño ha permitido reducir el número de tornillos que se venían utilizando, de alrededor de 40, a sólo seis. En estos momentos la empresa fabrica 13 modelos distintos de embarcaciones. La previsión de la producción para el año pasado fue de 3.000 kayaks. El tiempo de ciclo del casco de la embarcación depende en buena parte del tiempo de enfriamiento. En función del modelo, se moldean entre diez y doce piezas por hora.
Para Rikutec, fundada en el año 1986 por su actual gerente, Günter Richter, la fabricación de los cascos, al igual que la de los tanques y los contenedores, al principio sólo suponía un negocio complementario. Se trataba de utilizar de forma racional las máquinas de demostración. La actividad comercial de la empresa se centraba y se sigue centrando en la fabricación de máquinas especiales de moldeo por soplado de coextrusión. Sin embargo, el negocio que en principio era eventual, ha resultado ser una actividad muy rentable. La fabricación de kayaks, por su parte, se puso en macha en 2004 con éxito y, según el gerente de la empresa Günter Richter, el proceso ofrece algunas ventajas más que los moldes rotativos habituales. Permite, por ejemplo, transformar materiales de más calidad y fabricar embarcaciones con diferentes colores de cubierta y de quilla.