Utilización del proceso de electroescoria (ESW) para la realización de recargues
La soldadura mediante electroescoria tiene como característica principal su elevada tasa de deposición. Es por ello que se utiliza industrialmente para el recargue de depósitos de gran tamaño. En la figura 1 se muestra la velocidad de deposición de los diversos sistemas de soldadura. Cabe destacar la elevada cantidad de material depositado para el proceso de electroescoria (entre 22 y 52 kg/hora para banda de 60 y 120 mm, respectivamente), muy superior a la tradicional variante de recargue por arco sumergido (SAW) con banda (que da valores de deposición significativamente menores (entre 10 y 34 kg/hora para banda de 60 y 120 mm, respectivamente).
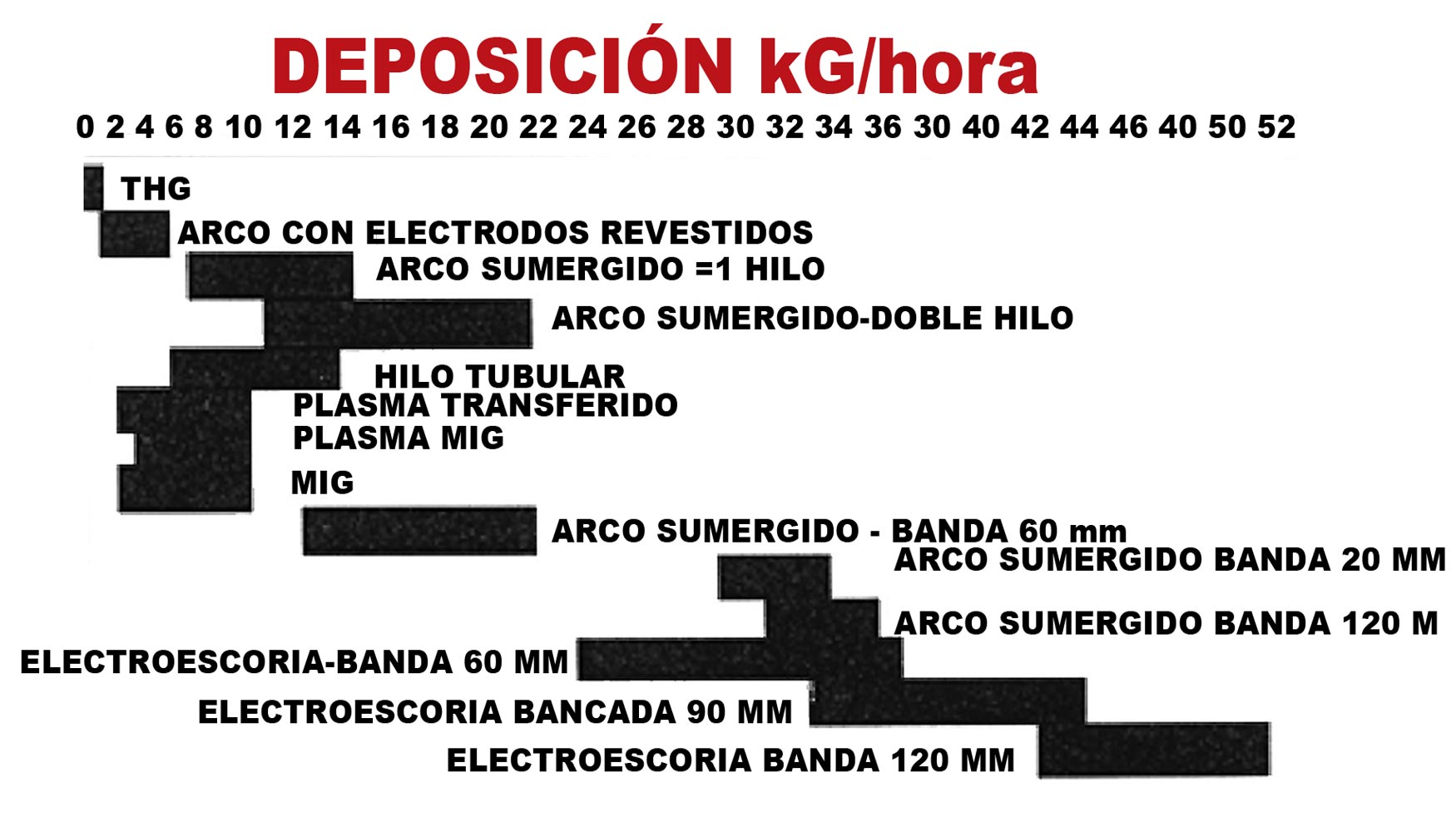
Características del proceso
Algunas de las principales características del proceso de recargue por electroescoria se mencionan a continuación:
- Baja dilución (8-15%).
- Baja penetración (<1 mm).
- No necesita gas protector.
- Utiliza elevadas intensidades de corriente.
- Es un proceso automatizado.
En el caso de la variante de soldadura por arco sumergido existe un arco eléctrico que ocasiona la fusión del consumible. Mediante electroescoria solo existe arco eléctrico durante el primer momento de ignición y posteriormente la banda se funde por efecto Joule (resistencia ofrecida por la escoria de tipo electroconductora en su estado fundido, H= I2R) por lo que solamente se alcanza una temperatura en el baño de fusión de alrededor de 1.800 °C (frente a los 3.400 °C del arco sumergido).
Los materiales que se depositan mediante este sistema son principalmente base níquel, cobre o hierro (habitualmente inoxidables, figura 2). La variedad de composiciones disponibles es amplia lo que permite realizar un gran abanico de aplicaciones donde se necesitan consumibles muy especiales.
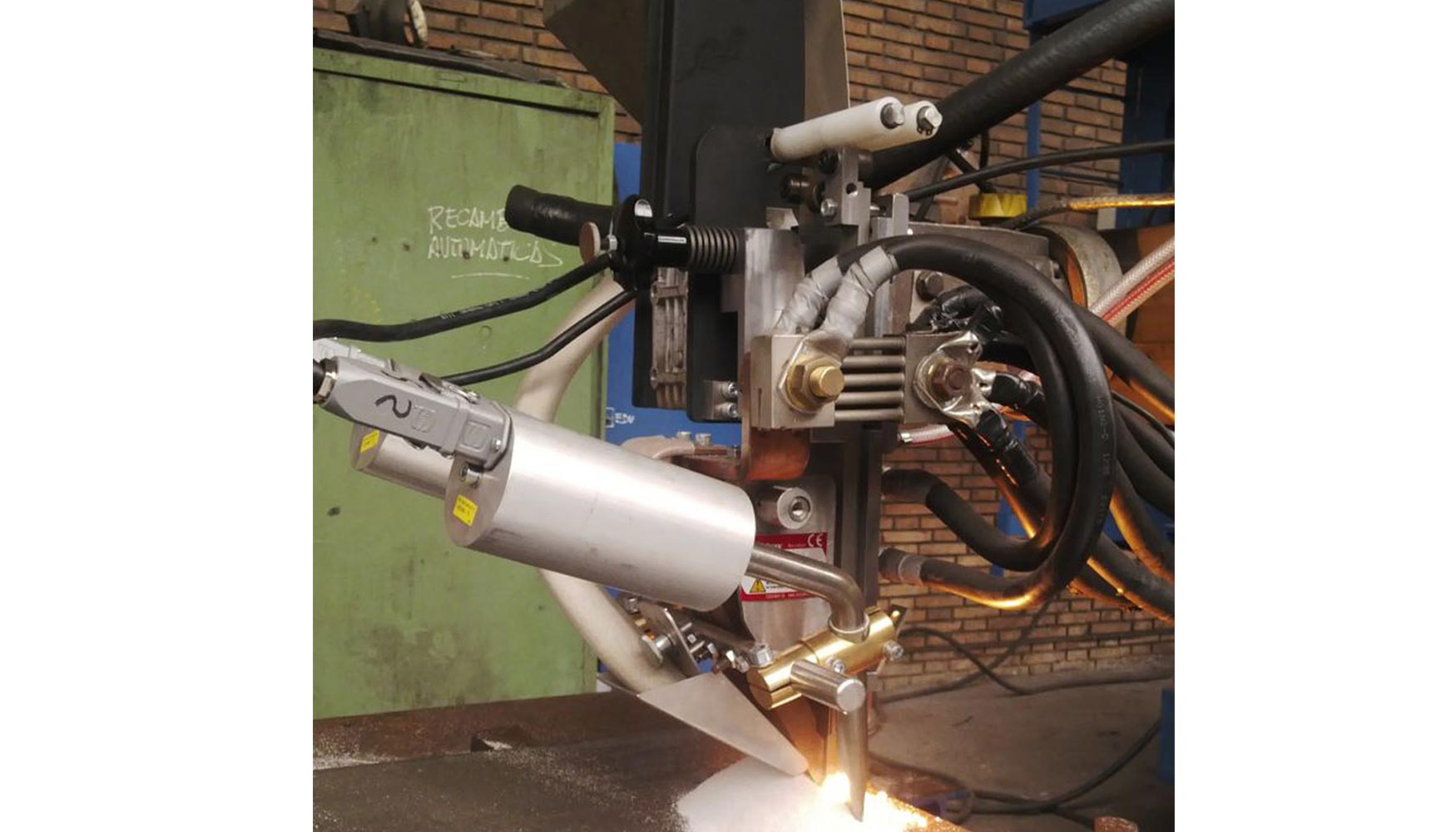
Debido a la baja dilución de este proceso es posible realizar depósitos con un contenido en elementos químicos adecuados en la primera pasada de material soldado, lo que a su vez repercute en un ahorro económico. En algunos casos el propio cliente pide una segunda pasada para revenir el material base, que podría haber sufrido un proceso de temple al depositar la primera capa, o también para asegurar una cierta composición química en la parte superior del depósito.
Los consumibles empleados para realizar los depósitos son bandas de dimensiones variables, pero en general tienen un grosor de 30, 60 y 90 mm (u ocasionalmente 120 mm) y un espesor de 0,5 mm. Para la soldadura mediante esta técnica se necesita también la utilización de un fundente especial.
Los fundentes aglomerados son los más atractivos para la utilización en el proceso de electroescoria. Este tipo de fundente se realiza mediante mezcla y aglomerado de las materias primas seguido de un proceso de cocción, molienda, cribado y envasado. Es posible adicionar elementos de aleación que durante la soldadura se incorporarán al depósito, por lo que se denominan fundentes o fluxes ‘compensados químicamente’. Pueden ser higroscópicos y llegar a captar humedad por lo que es aconsejable mantenerlos en lugar seco y libre de humedad.
El fundente tiene varias funciones. Entre ellas destacan:
- Es el responsable de transmitir la energía calorífica a la banda.
- Protege al material fundido del contacto con la atmósfera para originar un enfriamiento lento y una protección ante la oxidación.
- Proporciona elementos de aleación (o también denominado, compensación química) al depósito para obtener así la composición adecuada.
- Ofrece estabilidad operacional.
- Mejora la vistosidad del cordón.
Una de las características especiales del fundente es que debe poseer una buena fluidez y ser electroconductor en su estado fundido. Para cumplir con estos requisitos el fundente contiene una gran cantidad de fluoruro de calcio (CaF2). El fundente se ha de almacenar en un lugar seco pues absorbe humedad y podría originar recargues con porosidad.
El parámetro de voltaje modifica la distancia desde el final de la banda al material base (‘stick out’). El voltaje se ha de mantener entre 24 y 25 voltios para que la banda a fundir esté a una distancia adecuada, sin formarse un arco por encima del fundente ni aglomeraciones con el material base.
La medida del voltaje, aunque está indicada en la placa de control, se debería tomar entre la zapata y el metal base, para así conocer exactamente su valor real. Normalmente, la gran intensidad del circuito junto a la existencia de conexiones que no son totalmente perfectas produce una caída de tensión, por lo que la medida en la placa de control y la real es ligeramente diferente (variación 2-3 voltios).
El incremento de la intensidad produce un aumento de la velocidad de deposición de la banda. Sin embargo, este aumento puede conllevar también un aumento de la dilución y una modificación del perfil del depósito, por lo que se aconseja mantener la intensidad entre los límites aconsejados por el fabricante
En la figura 3 se muestra un esquema del sistema de electroescoria. Se aprecia como existe una sola tolva situada en la parte delantera del equipo. Esta tolva proporciona el fundente adecuado para llevar a cabo la soldadura. La cantidad de fundente aportado es superior a la necesaria, por lo que el exceso se recicla para usos posteriores.
Dos rodillos se encargan de la correcta alimentación de la banda. Existe una fusión correcta del fundente situado entre el sistema que proporciona la corriente y el metal base. Este fundente en estado líquido proporciona mediante transferencia la energía calorífica necesaria a la banda para que funda y se deposite sobre la superficie del metal base. Los grosores más habituales de la escoria solidificada y del metal depositado son en ambos casos de 4mm a 5 mm. La figura 3 muestra también la zona afectada térmicamente muy pequeña en este proceso, de alrededor 0.3-0.5 mm. Los cabezales que se utilizan son idénticos a los de arco sumergido (figura 4) y sus dimensiones varían con relación al ancho de banda. Sin embargo, una de las diferencias más importantes de este sistema con respecto a la soldadura con arco sumergido es la existencia de 2 magnetos que proporcionan un control magnético del baño fundido (no necesarios al utilizar banda de 30mm). Su utilización correcta es totalmente necesaria para obtener depósitos adecuados. Al igual que una gota de agua o de mercurio sobre una superficie plana, el material fundido tiende a contraerse dando lugar a un depósito estrecho e irregular. La función de los magnetos es la de proporcionar una fuerza mecánica (Fuerza de Lorentz) inducida por el campo eléctrico originado por la bobina, que ensanche el baño de fusión para obtener las anchuras deseadas (figura 5-a, 5-b). Los magnetos han de estar situados unos 3 mm por delante del fleje. La anchura del depósito originado por una banda de 60 mm es de alrededor de 65-70 mm y el espesor de 4-5 mm. El ángulo comprendido entre el borde del depósito y el material base debe ser menor a 70º, sino quedarán ancladas partículas de escoria (figura 5-c).
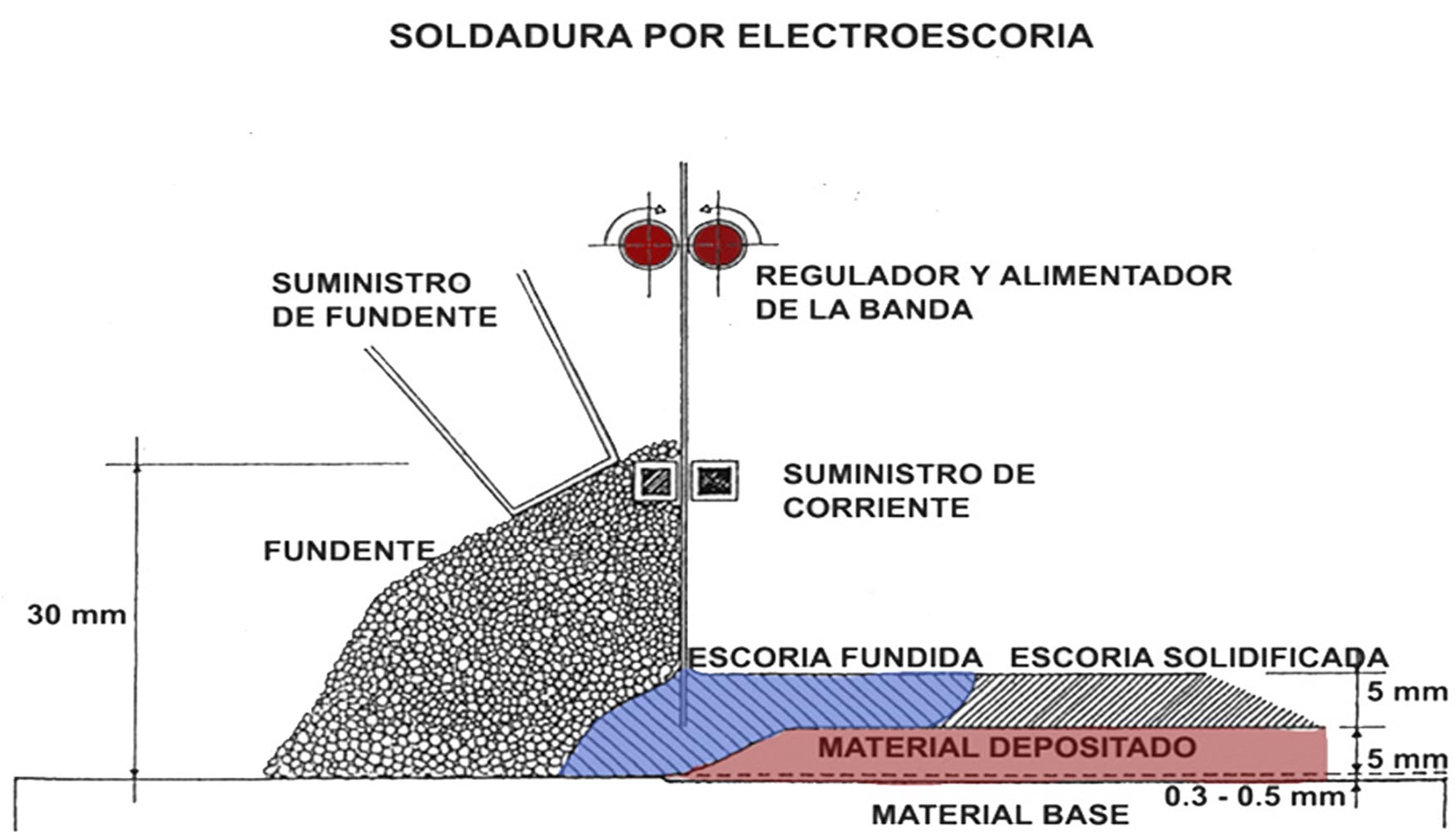
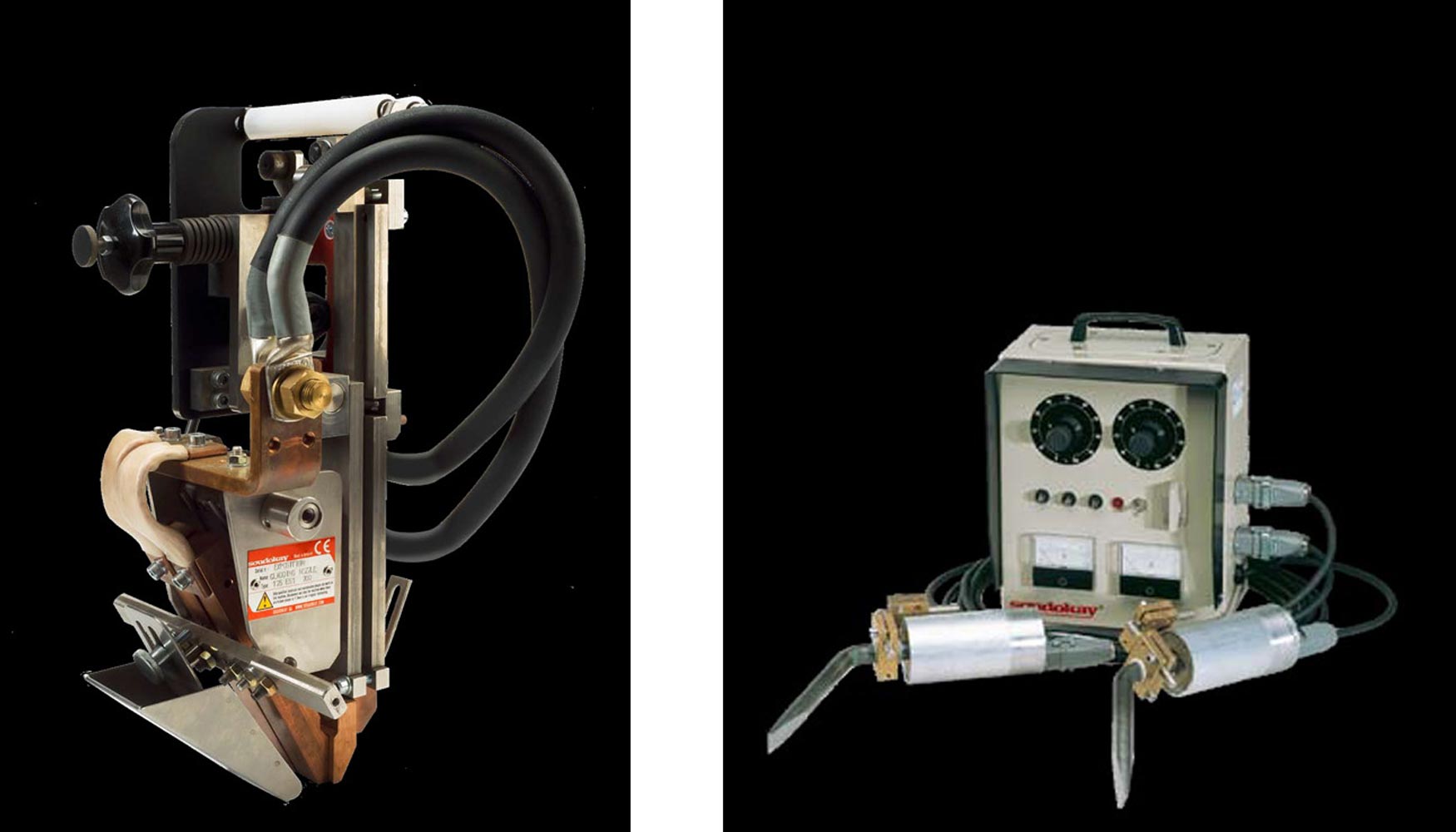
Unas condiciones típicas de trabajo para una banda de 60 mm de anchura, obtenidas mediante una combinación de banda –flux de Soudokay, podrían ser las siguientes:
Corriente (A) |
1250 |
Voltaje (V) |
24 |
Vel. (cm/min) |
18 |
Espesor de cordón (mm) |
5.0 |
Densidad de corriente |
42 A/mm2 |
Dilución (%) |
10% |
Velocidad de deposición |
22Kg/ h 0.6 m2/h |
Esta baja dilución puede dar lugar a un contenido en carbono del depósito menor a 0.030% al recubrir un acero al 0.18% en carbono. La velocidad de deposición en este caso alcanzaría los 0.6 m2/h. La variación de los parámetros de soldadura altera la anchura y el grosor del cordón y modifica la dilución. De esta manera, se destaca aquí de nuevo la ventaja de la electroescoria en relación al número de pasadas, ya que puede obtenerse mediante la solución de una sola pasada una composición química (en el punto en que se haga en análisis químico deseado, a veces a una cierta distancia de la línea de fusión o de la superficie) adecuada según código o clasificación del material. A modo de ejemplo, la utilización de una banda Soudotape 347 (EQ347) + Flux Record EST 347-1 (fabricación Soudokay) da lugar a un depósito de aleación 347 (composición media obtenida 0.025%C, 1.25%Mn, 0.39%Si, 18.40%Cr, 9.70%Ni, 0.45%Nb, resto Fe, ferrita según Fischer 6FN)
Existen otras variantes del proceso, por ejemplo la denominada electroescoria de alta velocidad, donde la velocidad de soldadura es superior, necesitándose también mayores amperajes. En este caso, el flux contiene una mayor cantidad de CaF2 (substancia que decrece la viscosidad del flux fundido, lo que facilita la fluidez del baño de fusión).
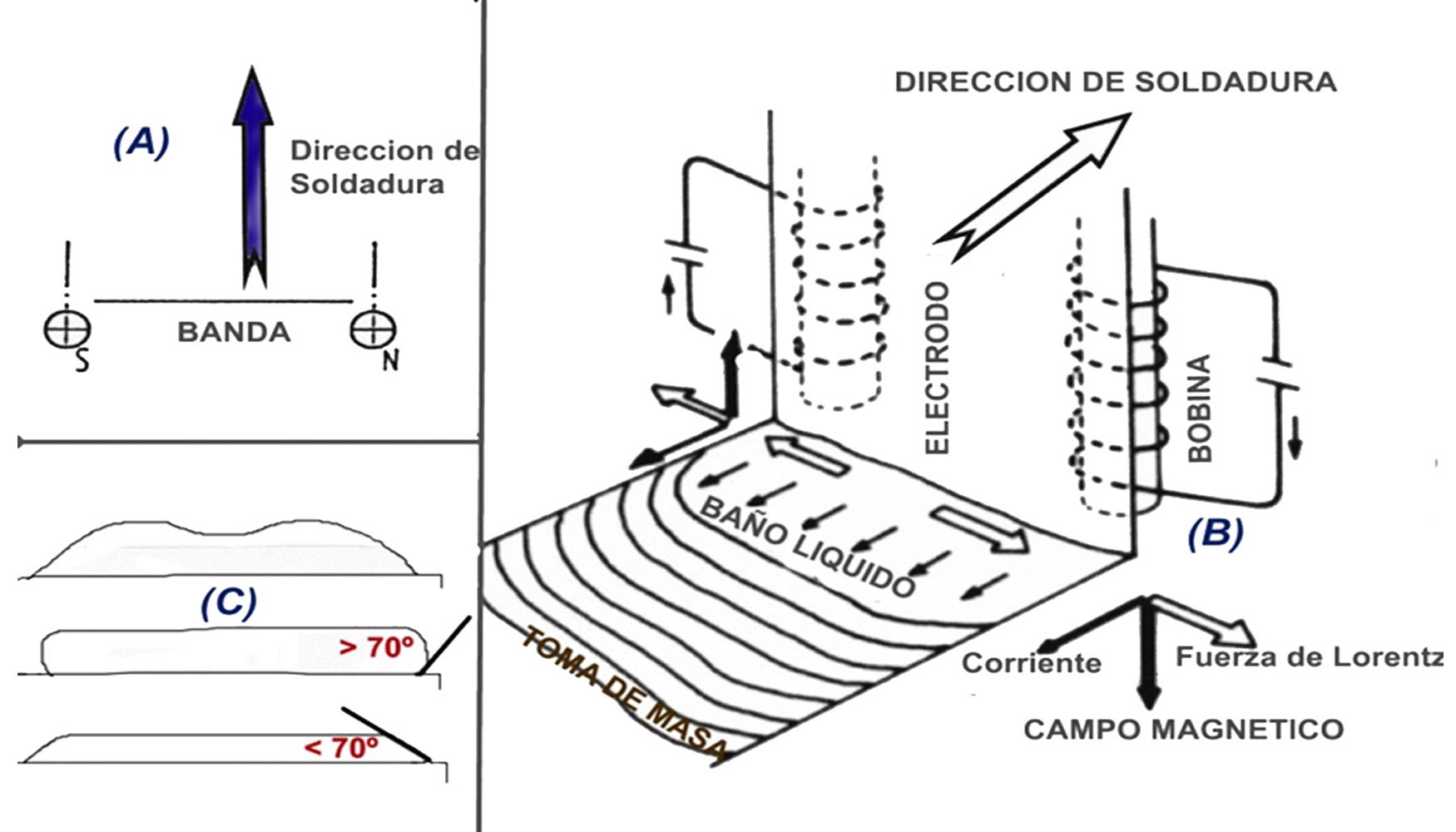
Las fuentes de potencia necesarias deben aportar una gran corriente ya que como se ha dicho anteriormente, los parámetros de intensidad que utiliza la soldadura por electroescoria son bastante elevados. En el caso de utilizar banda de 120 mm la corriente necesaria puede superar los 2400 A.
Ajustes necesarios y fallos a evitar
Soudokay recomienda realizar una serie de ajustes antes de comenzar el proceso de recargue:
- Los rodillos de alimentación han de sujetar la banda con la suficiente fuerza como para que exista una alimentación constante.
- Las zapatas han de presionar la banda de forma adecuada como para que exista una buena transmisión de corriente, pero suficientemente suave como para que se produzca una correcta alimentación de la banda.
- Las distancias entre los diferentes componentes del equipo han de mantenerse de forma correcta (distancia entre zapatas y material base ‘stick out’, distancia entre magnetos y material base, etc.) (figura 6).
- La tobera debe estar 10-20 mm por encima del ‘stick out’. Distancias demasiado altas podrían dar lugar a porosidad y demasiado bajas a proyecciones y cortocircuitos.
- El solape entre cordones ha de ser correcto. Para ello posicionaremos el extremo de la banda solapado 4-7 mm sobre la pasada anterior, lo que originara un solape final entre cordones de unos 7-10 mm. Si solape es mayor puede quedar ocluida escoria. Si es menor no habrá un buen solape.
- Es necesario que el magneto norte esté situado a la derecha de la dirección de soldadura (figura 5-a).
- La masa ha de quedar atrás del avance de la soldadura y de forma que se aleje (figura 5-b).
- La posición de los magnetos ha de disponerse correctamente.
- Se sugiere comenzar por 2,0 A en el magneto norte y 1,5 A el sur, aunque esto depende mucho de la geometría de la pieza y de la situación del recargue en la superficie de la pieza. Debe comenzarse con valores 0.5 A mayor el norte que el sur y buscar a partir de ese momento el valor óptimo para cada magneto. Si parámetros son demasiado altos se obtendrá un cordón demasiado ancho y estrecho en el centro. Si los parámetros son demasiado bajos se obtendrá un cordón estrecho y ancho en el centro.
- Existen pequeños dispositivos magnéticos para ver de forma externa que polaridad tiene cada uno de los magnetos.
- En el caso de soldar el interior de superficies curvadas (reactores) la posición de la banda debe estar unos 50 mm desplazada hacia delante del eje central del recipiente, pero esto depende mucho del diámetro de la virola y se debe analizar en cada caso.
Así pues, en el recargue de interiores de bridas de unos 80cm de diámetro sería solamente necesario desplazarse 20mm. Otra manera de realizar este cálculo es desplazar el cabezal 2 o 3 grados por delante del eje cenit de la virola. Si el desplazamiento es insuficientes se obtendrá cordones demasiado gruesos en el centro y, por el contrario, si es demasiado se obtendrá cordones demasiado estrechos en el centro.
- Soldar sobre superficie plana (máximo 2º de inclinación entre los extremos de la banda).
- Recargar solapando de manera que el norte del segundo cordón corresponda con el sur del primero.
- Para empezar a trabajar, el fundente debe inundar la zona de comienzo del recargue. Posteriormente debe encenderse la corriente y 3 segundos después comenzar el desplazamiento.
- Se recomienda cortar banda a 45º para facilitar el comienzo.
- Normalmente es mejor parar el desplazamiento y posteriormente cortar la corriente de soldadura.
- En algunos casos puede ser necesario secar el fundente, sobretodo en el caso de reutilizarlo.
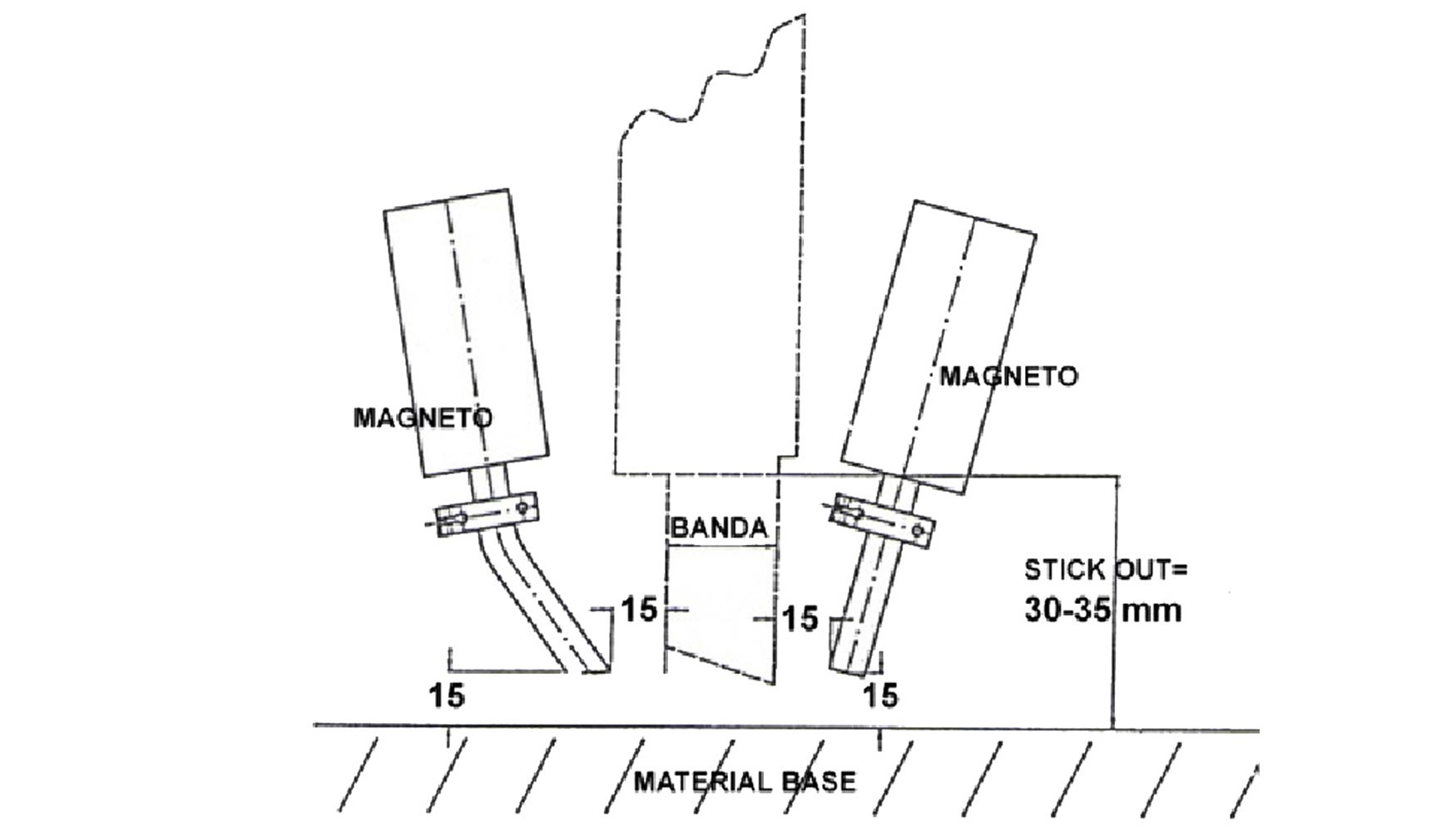
El proceso de electroescoria se utiliza cuando es necesario recubrir grandes superficies (figura 7). Las ventajas principales son su alta velocidad de deposición y su relativo bajo coste. Sus aplicaciones principales son:
- Reactores químicos (figura 8).
- Depósitos de Gas Líquido Licuado.
- Rodillos de laminación y colada continua.
- Industria nuclear.
- Plantas de desalinización.
- Industria off-shore.
- Industria papelera.
- Industria de desulfuración.
- Plantas de urea.
- Industria petroquímica (reactores de cracking).
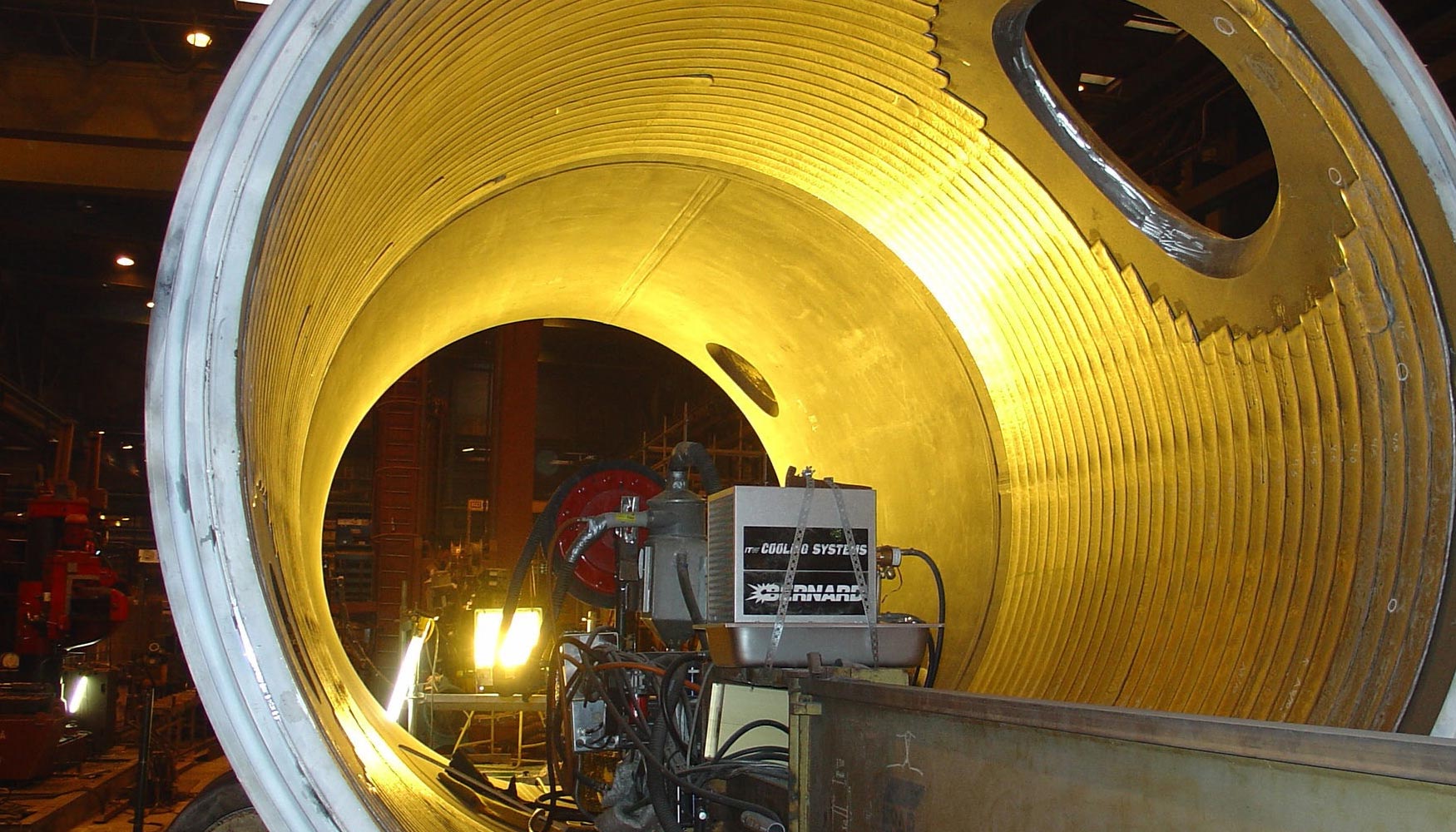
Algunos de los consumibles para electroescoria que tienen Soudokay (voestalpine Böhler Welding) son los siguientes:
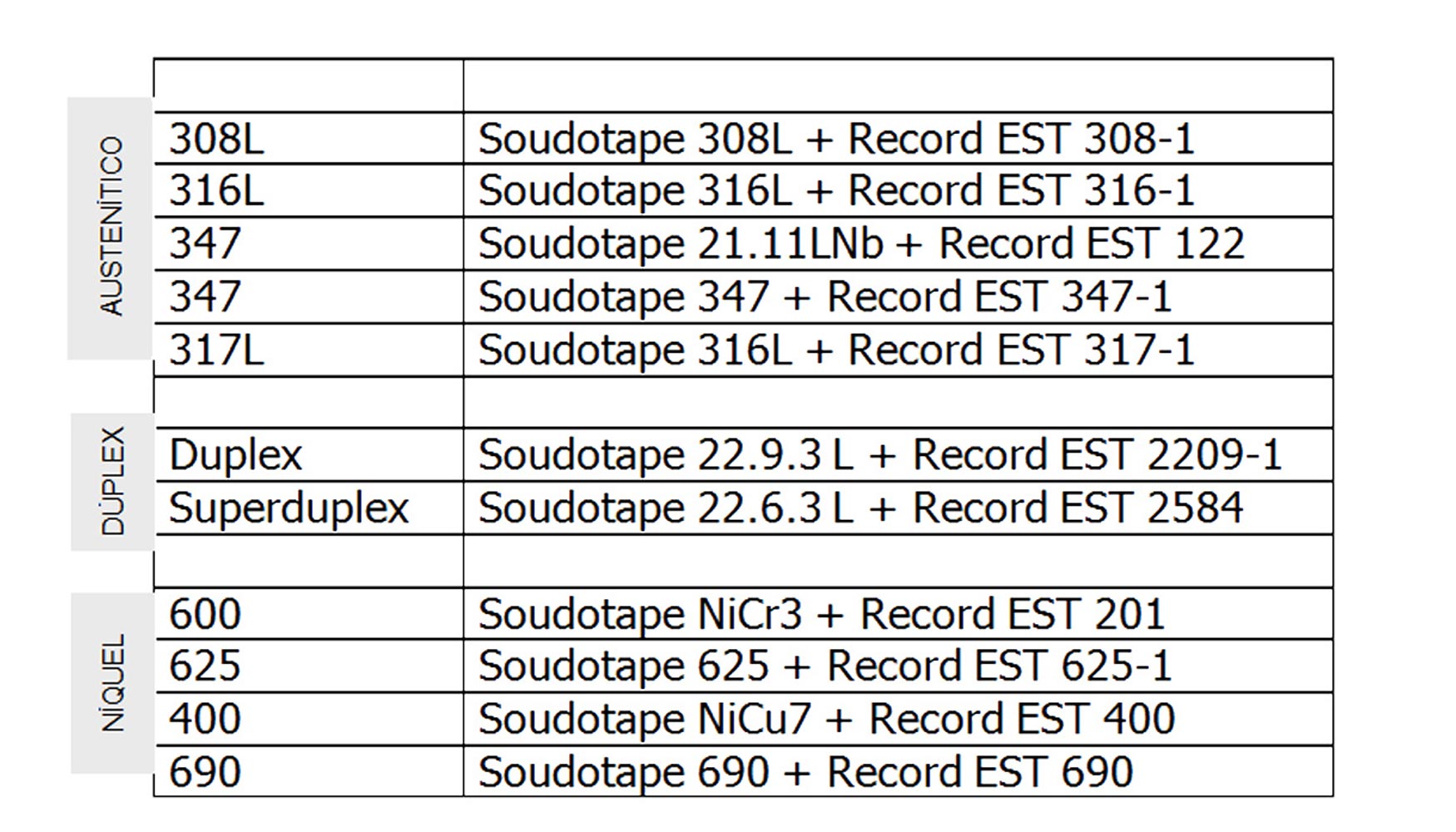
También se pueden hacer recargues de 307, 310, 310Mo 318, 430 (L), 410 (L), Aleación 20.25.5 LCu, Aleación 276, Aleación C4 y Aleaciones base Cobalto.
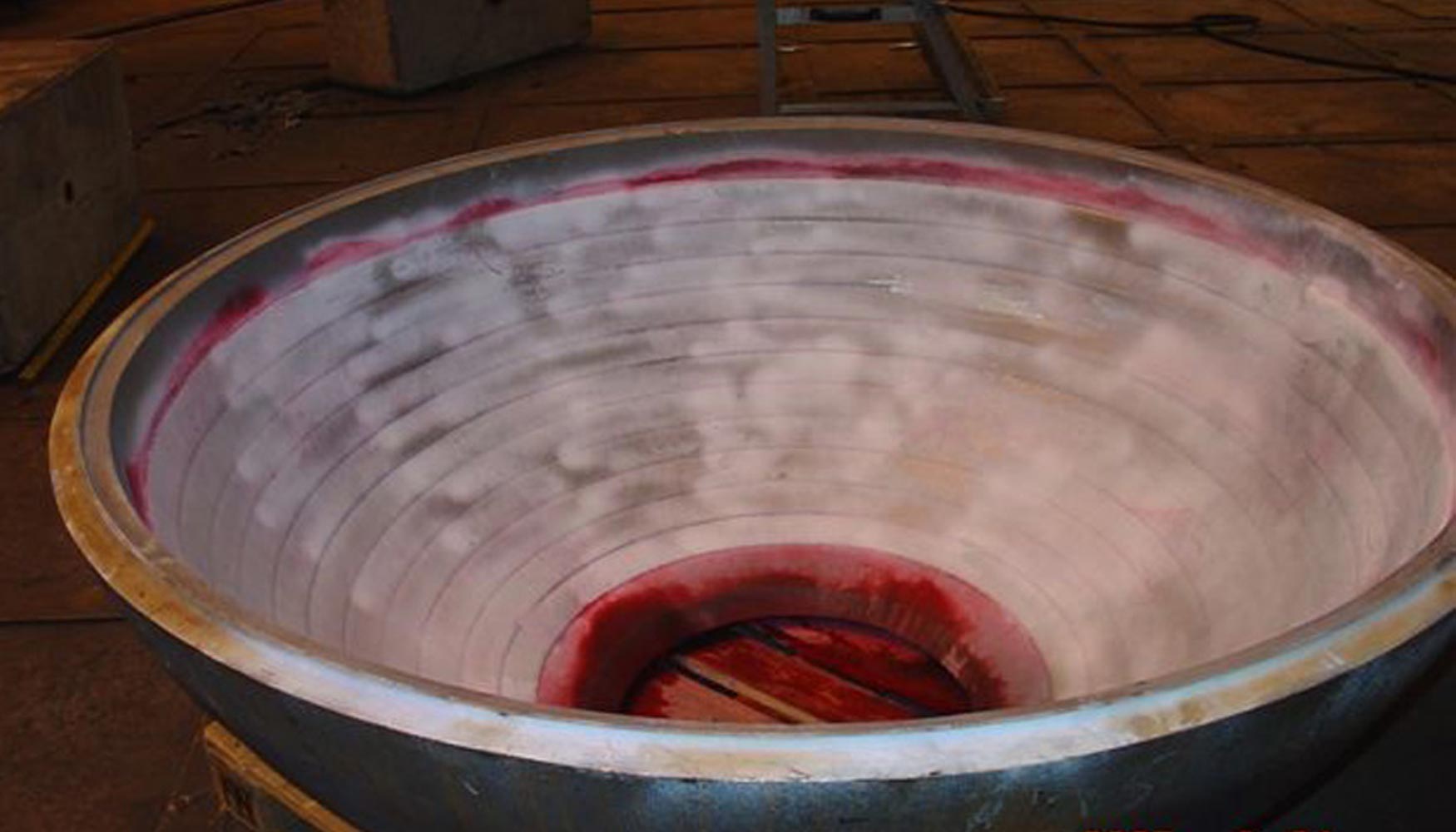
Agradecimientos
Agradecer a Pedro Miranda (Lointek) y Jean Pierre Van Nieuwenhoven (voestalpine Böhler Welding Belgium) su colaboración en la redacción y corrección de dicho artículo.