Rectificado inteligente: garantía de calidad para engranajes de transmisión electrónica
Martin Witzsch, físico diplomado, periodista independiente para Kapp Niles
04/01/2023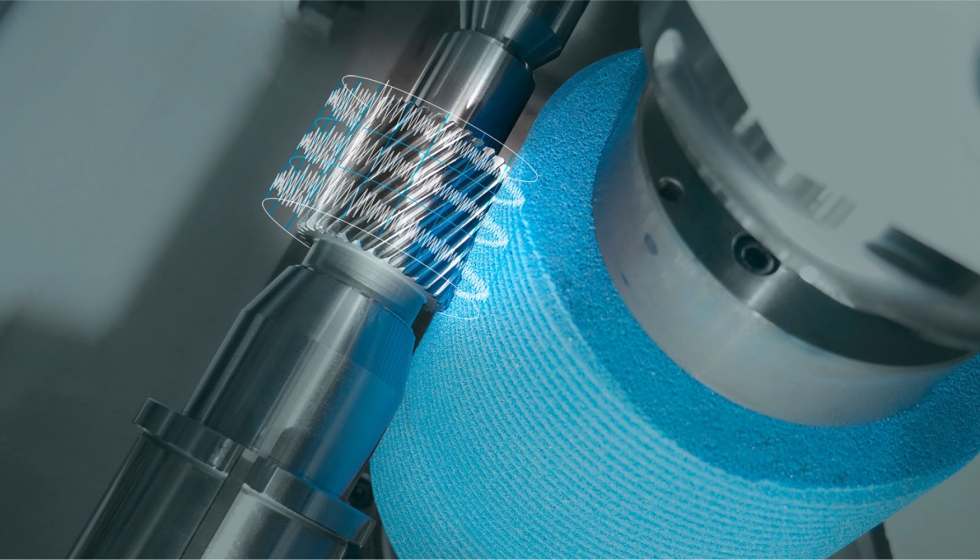
Las transmisiones de vehículos totalmente eléctricos se suelen conformar con transmisiones de dos etapas no conmutables. Se podría pensar que esto simplificaría mucho la producción. Al fin y al cabo, este tipo de transmisión sólo tiene cuatro engranajes, distribuidos entre el eje de transmisión, la segunda etapa con engranaje fijo y eje intermedio, y el engranaje de transmisión del eje. Pero en realidad no es tan sencillo: en primer lugar, las revoluciones del motor son mucho más altas en el e-drive que, en los motores de combustión, de hasta 16.000 rpm. Esto significa que los motores eléctricos ofrecen un par casi constante en una amplia gama de revoluciones. A diferencia de los motores de combustión, se aplica a la transmisión desde el régimen cero.
Además, existe una limitación adicional que hace que la producción sea mucho más exigente que con la transmisión convencional, como describe Friedrich Wölfel, jefe de ventas de maquinaria de Kapp Niles: “El ruido de un motor de combustión enmascara el ruido de la transmisión, por lo que pasa desapercibido en primer lugar. En cambio, un motor eléctrico es casi silencioso. Por encima de unos 80 km/h, el ruido de rodadura y el del viento son los sonidos predominantes, independientemente de la transmisión. Pero por debajo de esa velocidad, el ruido de la transmisión puede ser irritante en los vehículos eléctricos. También hay que tenerlo en cuenta al fabricar las marchas”.
Por supuesto, la capacidad de carga de los flancos de los engranajes y las buenas propiedades de marcha también son de vital importancia en las transmisiones eléctricas. Sin embargo, el nivel de par casi constante y las altas velocidades requieren un diseño de engranaje diferente, que a su vez puede afectar a la dinámica del ruido. Aquí, en particular, las exigencias son mayores que con los motores de combustión.
Sin embargo, cuando se trata de la presión para generar la máxima eficiencia, no hay diferencia alguna entre los engranajes para vehículos eléctricos y los engranajes convencionales. En consecuencia, el proceso de rectificado generador de alta productividad también se utiliza generalmente como proceso de mecanizado fino en la producción en serie de engranajes para e-transmisión.
El reto para Kapp Niles, como especialista en el mecanizado fino en duro de engranajes, es implementar un proceso de rectificado generador que sea productivo y, sobre todo, optimizado en términos de dinámica del ruido. Achim Stegner, responsable de predesarrollo en Kapp Niles, describe los fundamentos de este proceso: “Dependiendo de las modificaciones del engranaje definidas en la fase de diseño, como las correcciones de línea, la convexidad de anchura, la retracción de la cabeza, así como los enclavamientos de perfil y línea típicos del proceso, se producen ruidos característicos en la transmisión durante el engrane, que pueden asignarse a frecuencias de engrane de dientes específicas. A su vez, toda la transmisión presenta también propiedades características en lo que respecta al ruido estructural y a la radiación, en función del diseño constructivo. Esto se estimula en la frecuencia de engrane del diente y sus múltiplos. Los fabricantes intentan minimizar este efecto en la medida de lo posible adaptando el diseño de la transmisión y los engranajes”. De momento, estas consideraciones sólo se aplican a los engranajes ‘perfectos’. Pero, por supuesto, como cualquier otro componente mecánico, los engranajes también generan desviaciones respecto a la geometría objetivo ideal en la producción en serie. Éstas tienen diferentes causas y efectos, como explica Achim Stegner: “Además de la estimulación causada por el engrane del diente, hay otras variables de perturbación que pueden dar lugar a ruidos en el engrane del diente. Se manifiestan como ‘frecuencias fantasma’. “Se trata de frecuencias que no coinciden con las frecuencias de engrane del diente y sus múltiplos, y que pueden introducirse sin más en el componente durante el rectificado”, añade.
Las ‘frecuencias fantasma’ están causadas por irregularidades mínimas que son casi imposibles de evitar por completo en la producción en serie. La situación es especialmente crítica cuando estas desviaciones coinciden casi exactamente con la circunferencia de un engranaje, ya que se produce una estimulación armónica.
Se necesita mucha pericia y experiencia en el proceso para reconocer las razones de tales irregularidades y, si es posible, evitarlas desde el principio. La causa de estas averías puede encontrarse, por ejemplo, en los accionamientos de los ejes de la máquina herramienta utilizada. Los motores eléctricos tienen ciertos momentos pendulares. Los sistemas de medición trabajan con recuentos de líneas discretos y errores de excentricidad finitos de montaje. Por último, pero no por ello menos importante, el estado de equilibrado y los rodamientos de los husillos pueden contribuir a posibles irregularidades. Unas ondulaciones tan pequeñas como 0,1 μm pueden provocar ruidos en los engranajes.
Achim Stegner explica algunas causas más: “Toda máquina tiene vibraciones naturales. Por ejemplo, la frecuencia natural típica de un husillo portapiezas es de unos 250 Hz. Esto también puede reproducirse exactamente en la pieza si la constelación de velocidades en el proceso de rectificado generador es desfavorable. Podemos eliminar tales efectos mediante la elección inteligente de una ventana de velocidad adecuada durante el mecanizado”.
Una vez agotado el potencial de optimización en el lado de la máquina, también hay una serie de opciones tecnológicas para mejorar la calidad de los componentes en términos de dinámica del ruido. Entre ellas se encuentran, por ejemplo, la selección del número de marchas del tornillo sinfín de rectificado, la relación de velocidad durante el reavivado y el rectificado, la velocidad de acabado y el avance.
No todos los errores son iguales
A grandes rasgos, existen dos tipos típicos de patrones de error en el rectificado de engranajes en serie: por un lado, surgen tendencias que muestran un cambio continuo de las características. Por otro lado, hay componentes individualmente conspicuos. Las tendencias suelen ser más fáciles de controlar. Pueden deberse, por ejemplo, al desgaste gradual de un tornillo sinfín de rectificado. Si en este caso se superan las tolerancias de fabricación permitidas, suele bastar con acortar el ciclo entre dos procesos de rectificado. También pueden reconocerse fácilmente durante las pruebas de los componentes por una aproximación gradual de los valores medidos al límite de tolerancia.
En cambio, los defectos específicos de los componentes son imprevisibles.
Se manifiestan por desviaciones repentinas de uno o varios criterios de calidad. Esto puede deberse al astillado del tornillo sinfín, a errores en la pieza en bruto o a errores de ajuste. Dado que el mecanizado propiamente dicho de un engranaje requiere mucho menos tiempo que la medición de control en procesos de fabricación altamente eficaces, como el rectificado por generación, tampoco es posible inspeccionar cada uno de los componentes. Además, como se ha descrito al principio, las exigencias de calidad de los engranajes para transmisiones electrónicas son extremadamente altas. “Las tolerancias requeridas de ángulo de perfil, ángulo de línea de flanco, concentricidad, dimensión de dos bolas son en algunos casos menores que en la transmisión convencional por un factor de 3. Para el error de ángulo de línea de flanco fHß, un requisito típico es ± 4 μm; con transmisiones de motor de combustión, esto era a veces ± 13 μm”, dice Friedrich Wölfel, describiendo los requisitos de sus clientes.
Junto con las capacidades requeridas de la máquina y el proceso, estos requisitos de calidad ponen a prueba los límites de lo que es técnica y económicamente viable. Y la estabilidad estática y dinámica de la máquina y el proceso de transformación no puede aumentarse a voluntad. La única salida es empezar por los métodos de análisis y control. Porque de lo contrario: cuanto más estrechos sean los límites de tolerancia con la misma capacidad de máquina/proceso, mayor deberá ser el número de componentes medidos. Sin embargo, esto supone un gran esfuerzo. Y, en última instancia, las pruebas de componentes posteriores tampoco aportan valor añadido.
En lo que respecta al enfoque de las desviaciones de la geometría objetivo relacionadas con las tendencias, en particular, el ‘bucle cerrado’ ya se ha establecido como una herramienta importante. Esto acelera y mejora la retroalimentación entre la medición de engranajes posterior y la propia máquina de procesamiento. Aquí, los resultados de la inspección en la máquina de medición ya no se imprimen y se ponen a disposición del operario de la máquina en papel para su evaluación, sino que se transmiten directamente a la máquina de procesamiento como un archivo normalizado. A continuación, la rectificadora utiliza los pasillos de tolerancia preseleccionables para decidir de forma independiente si debe intervenir en el proceso, por ejemplo, con valores de corrección escalables. Si se producen desviaciones inesperadamente elevadas de la geometría objetivo, la decisión sobre cómo proceder recae en el propio operario (Figura 1).
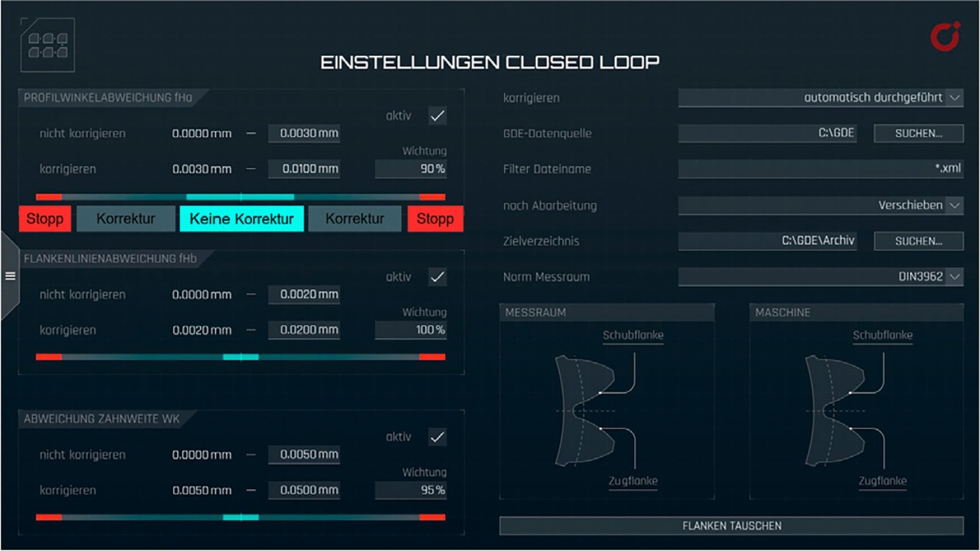
El árbitro al final del proceso de fabricación
Al final del proceso de fabricación de una transmisión completa se encuentra lo que se conoce como ‘banco de pruebas de final de línea’. Aquí ya no sólo se comprueba la calidad de los engranajes individuales, sino que se evalúan transmisiones totalmente montadas. Se someten a varios ciclos de prueba que simulan las condiciones de funcionamiento en un vehículo real. También se registra el ruido de funcionamiento. Los acústicos pueden analizar estos datos para extraer relaciones de intervención, frecuencias típicas y posibles ruidos parásitos. “Por desgracia, esto también significa que los defectos de los engranajes sólo se detectan al final del proceso de fabricación”, se queja Friedrich Wölfel. “Entonces hay que desmontar la transmisión completa, comprobar los componentes individuales y, a partir de ahí, analizarlos para determinar qué componente es el responsable de la anomalía en el banco de pruebas. También puede ocurrir que un lote completo de componentes cause problemas. Pero eso sólo se pone de manifiesto cuando ya se ha completado toda la cadena de valor”.
Hoy es posible identificar los componentes que podrían causar ruido antes de instalarlos en la transmisión. Un procedimiento muy habitual en las transmisiones electrónicas es el análisis de ondulación en las superficies de los engranajes. Para ello, se realizan mediciones del perfil, la línea y el paso de todos los dientes en la máquina de medición de engranajes y se alinean de tal forma que el engranaje quede cartografiado en toda su circunferencia. La ondulación de la rueda dentada puede medirse matemáticamente.
Sin embargo, al partir de la medición completa de los engranajes, este procedimiento requiere mucho tiempo y, por tanto, no es adecuado para comprobar cada pieza en la producción en serie. Así lo explica Friedrich Wölfel: “El tiempo de rectificado de los componentes típicos de una transmisión electrónica es inferior a un minuto, mientras que el tiempo de medición es de cuatro a seis minutos; de hecho, en el caso de una medición de todos los dientes como base de un análisis de ondulación, puede ser bastante más. Y, en última instancia, las pruebas posteriores de los componentes tampoco aportan valor añadido. Lo que se necesita aquí es un mayor desarrollo del análisis durante el proceso, que permita sacar conclusiones sobre la calidad del componente producida durante el propio mecanizado”.
Detectar posibles problemas de ruido en la fase de mecanizado
Un enfoque prometedor es, de hecho, detectar posibles defectos ya en el proceso de rectificado. La monitorización del proceso es la palabra de moda. Achim Stegner explica el enfoque: “Ya disponemos de numerosos sensores y sistemas de medición en la máquina que pueden proporcionarnos muchas indicaciones, valores medidos e información. De momento, sólo los utilizamos para controlar las funciones de la máquina. En el futuro, sin embargo, también queremos utilizarlo para evaluar el proceso de mecanizado directamente en la máquina”. Sin embargo, no se trata de integrar una función de medición táctil adicional en la rectificadora para conseguir un bucle cerrado más rápido. Tampoco se trata aquí de inspeccionar un componente rectificado directamente en la máquina, evaluarlo y corregir cualquier discrepancia durante la producción de otros componentes. Se trata más bien de analizar el proceso de mecanizado en tiempo real (¡!) para detectar las desviaciones con respecto a un proceso de referencia previamente definido. Sin embargo, para ello no basta con definir envolventes para las señales procedentes de la máquina. Esto puede explicarse utilizando como ejemplo la señal ‘consumo de potencia del husillo de rectificado’ de la figura 2.
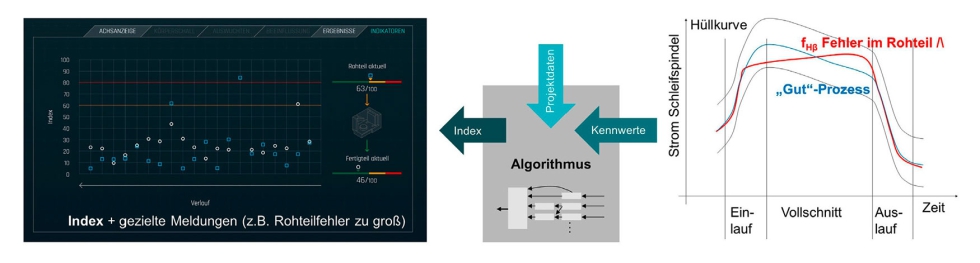
Esta señal puede utilizarse para detectar un posible error en el ángulo de la línea de flanco (fHß) en una fase temprana. Stegner explica: “Sin embargo, el procedimiento mediante detección envolvente alcanza aquí sus límites, ya que el error es difícil de identificar. Mientras la señal permanezca dentro de la envolvente, no se dispara ninguna alarma. Así que se necesita una forma de evaluación más inteligente. Una inteligencia artificial que intente emular las estructuras humanas de toma de decisiones. Se trata de tomar decisiones basadas en una multitud de informaciones diferentes -a las que se superponen las propias experiencias- sobre las que se actúa.
Supervisión de procesos: intervenir antes de que sea demasiado tarde
La supervisión del proceso puede definirse como el seguimiento y la evaluación del proceso de trituración por componentes específicos. Tal y como se ha descrito, no es trivial generar una instrucción de actuación a partir de las señales de los sensores. Pero es posible. A partir de las señales de tiempo se pueden formar diversos valores característicos. En el caso más sencillo, pueden ser valores máximos o RMS (Root Mean Square) de las señales. A continuación, los valores característicos se combinan con los datos conocidos del proyecto mediante algoritmos y se procesan en índices, por ejemplo, un índice de ruido o de rotura de tornillos. Achim Stegner explica específicamente los ruidos de transmisión: “Puede crearse un análisis de orden similar al espectro de orden en un banco de pruebas de final de línea para los componentes críticos de ruido mediante una FFT (Transformación rápida de Fourier). Esto facilita la clasificación de las señales registradas y su relación con los resultados en el banco de pruebas de transmisión (véase la figura. 3). Los datos de medición que no se procesan no sirven de nada”.
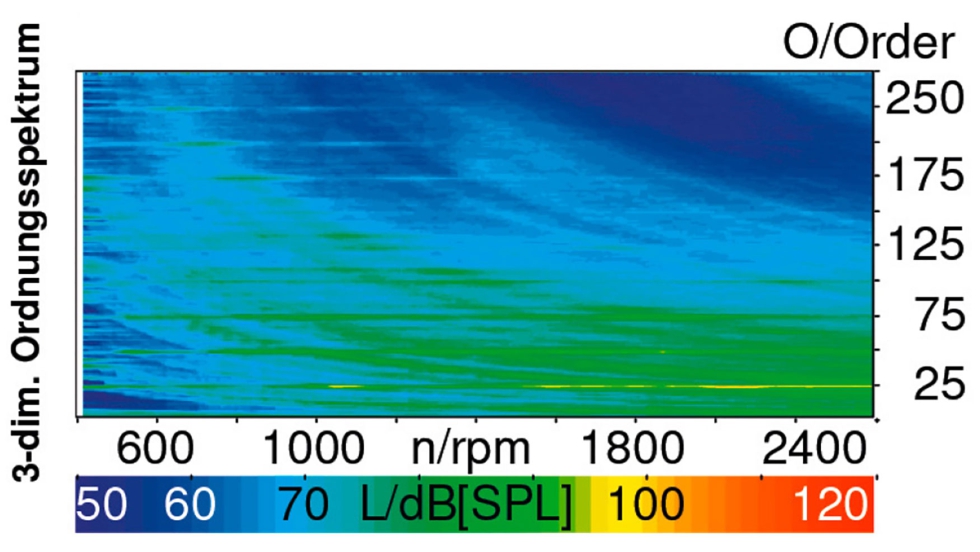
Al final, especialmente en el entorno de fabricación, sólo unos índices adecuados ayudan a identificar los errores de forma muy específica. Por tanto, las ventajas de la supervisión de procesos pueden apreciarse en los siguientes puntos:
- Comprobación del 100 % de todos los componentes
- Identificación de anomalías cuando aún se está en el proceso de rectificado
- Detección de fallos específicos de los componentes
- Notificación selectiva de las irregularidades
- Intervención adaptativa en el proceso
- Rastreo de piezas
Siguiente paso: normalización
La supervisión de procesos aún no es una aplicación que pueda descargarse y utilizarse sin más. Se trata más bien de un desarrollo específico para el cliente y la aplicación que define y supervisa los índices en relación con el componente respectivo. Pero incluso este primer paso es mucho más de lo que se consideraba factible hasta hace poco. Achim Stegner al respecto: “Varios clientes piloto ya utilizan hoy esta funcionalidad. Ya podemos detectar distintos errores e intervenir en el proceso.
Además, ya estamos trabajando para que la rectificadora aprenda por sí misma los valores característicos de los nuevos componentes. Sin embargo, esto requiere, por supuesto, un amplio conocimiento empírico a partir de patrones de error, la calidad geométrica de los componentes y la correspondiente retroalimentación del banco de pruebas de transmisión”. Friedrich Wölfel añade: “El siguiente objetivo es que el usuario también pueda utilizar esta funcionalidad sin nuestro soporte específico de componentes. También es importante comprender que la supervisión de procesos y el bucle cerrado no son contradictorios, sino complementarios”.
Ambos enfoques del aseguramiento de la calidad integrado en el proceso ya están disponibles para las máquinas de Kapp Niles en la actualidad y, gracias a la experiencia adquirida en la producción en serie, se les están dando continuamente nuevos alcances funcionales y opciones de utilización.