Las claves del recubrimiento. Nuevas fórmulas para su mejora
Pablo Fernández-Lucio, Felipe Marin, Gaizka Gómez Escudero y Haizea González Barrio, del Dpto de Ing. Mecánica. Universidad del País Vasco (UPV/EHU); y Ander del Olmo, Gonzalo Martínez de Pissón, Octavio Pereira, Asier Fernández-Valdivielso y Luis Norberto López de Lacalle, del Centro de Fabricación Avanzada de Aeronáutica (CFAA)
25/05/2022El aumento de la competitividad en los procesos de mecanizado, a través del aumento de la velocidad de corte hace que se deban desarrollar, sobre todo en taladrado, recubrimientos de herramienta que protejan el sustrato del aumento de esfuerzos de corte y el consiguiente aumento de temperatura y, así, poder cubrir las necesidades del mercado.
El recubrimiento de herramienta es una película aplicada tras la conformación de la misma, cuyo espesor está en un rango entre 2 y 15 micras [1]. Esta película se deposita de forma sólida y se adhiere al sustrato de la herramienta de corte con el fin de mejorar el rendimiento de la misma. Sus propiedades deben ser:
- Aumento de la dureza superficial, para soportar el rozamiento por abrasión.
- Tenacidad, para que se puedan deformar sin romperse de un impacto.
- Reducción del coeficiente de fricción que facilita el deslizamiento de la viruta en su evacuación, reduce fuerzas de corte, previene de la adhesión entre las superficies de contacto y reduce la generación de calor debido a la mayor facilidad de evacuación de viruta.
- Reducción, a su vez, de la parte de la energía térmica que se transmite a la herramienta por la capacidad para resistir altas temperaturas.
- Estabilidad química, para que no exista afinidad química con el material a mecanizar.
- Resistencia a la corrosión y a la oxidación.
- Mejora de la calidad superficial de las piezas acabadas.
- Precio competitivo, puede suponer el 5-10% del coste de la herramienta.
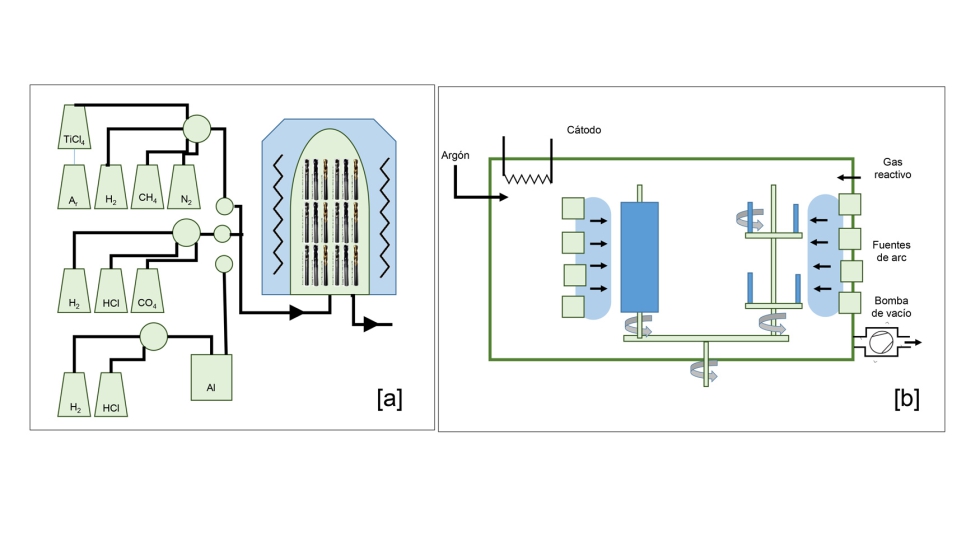
Las dos tecnologías más utilizadas actualmente en la industria para la aplicación de los recubrimientos sobre las herramientas de corte son las tecnologías ‘Chemical Vapor Deposition’ (CVD) y ‘Physical Vapor Deposition’ (PVD). Las principales diferencias entre ambas tecnologías radican en que con la tecnología PVD durante el proceso de recubrimiento los átomos de este son los que ‘se mueven’ desde el blanco y ‘depositan’ sobre el sustrato mediante un arco eléctrico, mientras que con la tecnología CVD son las moléculas gaseosas del recubrimiento las que reaccionan con el sustrato de la herramienta. Asimismo, en el caso del PVD la temperatura de trabajo es de alrededor de 250-450 °C, mientras que con el CVD alcanza hasta los 1.050 °C.
Convencionalmente, los recubrimientos utilizados por gran parte de los herramentistas son los conocidos como ‘recubrimientos monocapa’. Estos recubrimientos, a pesar de recibir este nombre, generalmente presentan dos capas: una de adhesión al sustrato y otra capa que es el propio recubrimiento en sí. Las capas de adhesión generalmente son de titanio o cromo dando lugar los recubrimientos TiN, TiAlN, TiCN o CrN y AlCrN. Tradicionalmente este tipo de recubrimientos han aportado una mayor dureza (20-40 GPa hasta los 400-1.000 °C de temperatura de corte) y resistencia al desgate a las herramientas y en la actualidad siguen utilizándose tanto en herramientas de metal duro (WC) como de acero rápido (HSS). Sin embargo, tienen una baja resistencia a la propagación de grietas que hacen que en materiales de difícil maquinabilidad no lleguen a aportar una mejora sustancial a las herramientas de HSS para hacer frente a los altos esfuerzos de corte a los que son sometidas durante el mecanizado.
Para solventar esta problemática, se han desarrollado los recubrimientos multicapa que, frente a los monocapa, mejora la resistencia a la propagación de grietas y a la vez conducen a minimizar la delaminación y fractura frágil [2]. Sin embargo, para aumentar su dureza frente a los recubrimientos monocapa deben aplicarse según la variante denominada nanocapa. Con esta variante, se logran durezas que alcanzar los 55 GPa mediante la combinación óptima de los espesores de cada una de las capas [3]. No obstante, debido a la dificultad de reproducir en el espesor óptimo, nacen los recubrimientos nanocomposite. Gracias a ellos se consigue la mayoría de las características de los recubrimientos multicapa/nanocapa, es decir, se obtiene un aumento significativo de la dureza (hasta 50 GPa) y una estabilidad de sus propiedades a altas temperaturas (hasta 1.200 °C) a la vez que se evita la propagación de grietas, pero se generan de manera espontánea bajo determinados parámetros en la deposición. Entre estos recubrimientos se encuentran AlTiSiN o el AlCrSiN [4].
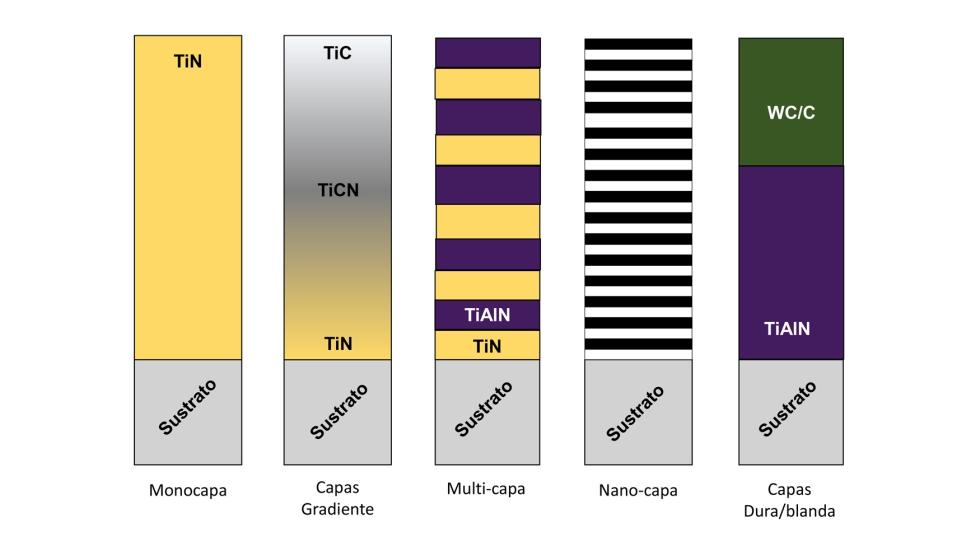
En el Centro de Fabricación Avanzada Aeronáutica (CFAA), estos últimos años ha estado analizado el impacto producido por los recubrimientos avanzados multicapa en brocas de acero rápido. Concretamente se ha analizado la influencia en el desgaste y en los esfuerzos de corte de incluir distintos recubrimientos en brocas convencionales para el mecanizado de acero DIN 1.2738.
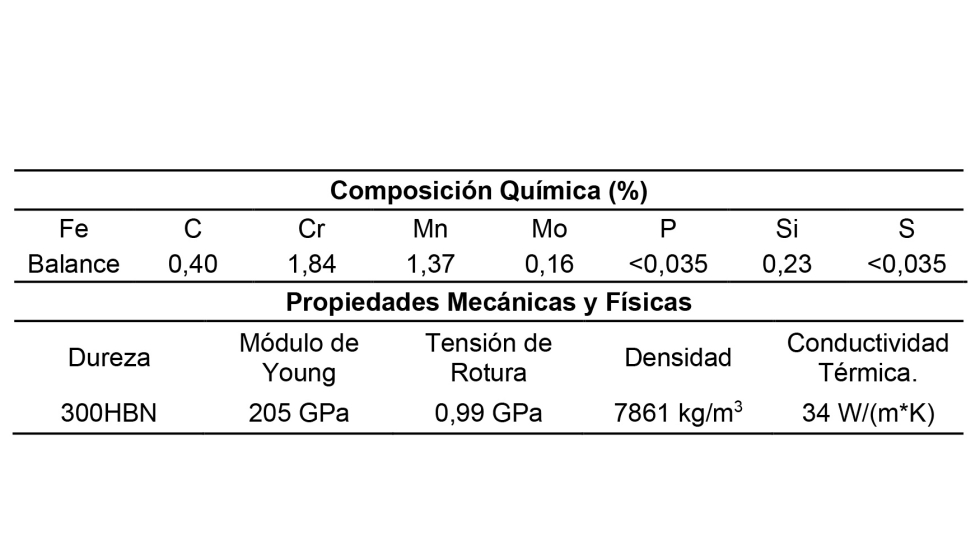
El Din 1.2738 es un acero bonificado para trabajar en frío y de moldes para plástico, teniendo, además, una buena capacidad de pulido y aptitud para el ataque químico. Es un material altamente templable y con un revenido posterior adquiere una resistencia uniforme en las piezas. Puede alcanzar una dureza de trabajo aproximada de 32 HRC pudiendo alcanzar hasta 50 HRC bajo tratamiento térmico. Este material posee una microestructura martensítica con carburos finamente dispersos. La composición química se detalla en la siguiente tabla, así como las propiedades del mismo.
Diseño de los ensayos
Las herramientas utilizadas han sido tres. La primera de ellas, usada a modo de referencia, es una broca comercial sin recubrir. Las otras dos brocas presentan la misma geometría, pero distintos recubrimientos, una con un recubrimiento de AlTiN y la otra con un recubrimiento TiN. Todas las brocas eran de diámetro 8 mm.
En la figura 3 se pueden ver las tres brocas con sus respectivos recubrimientos y en la tabla 2 se presentan las principales propiedades de los distintos recubrimientos usados.
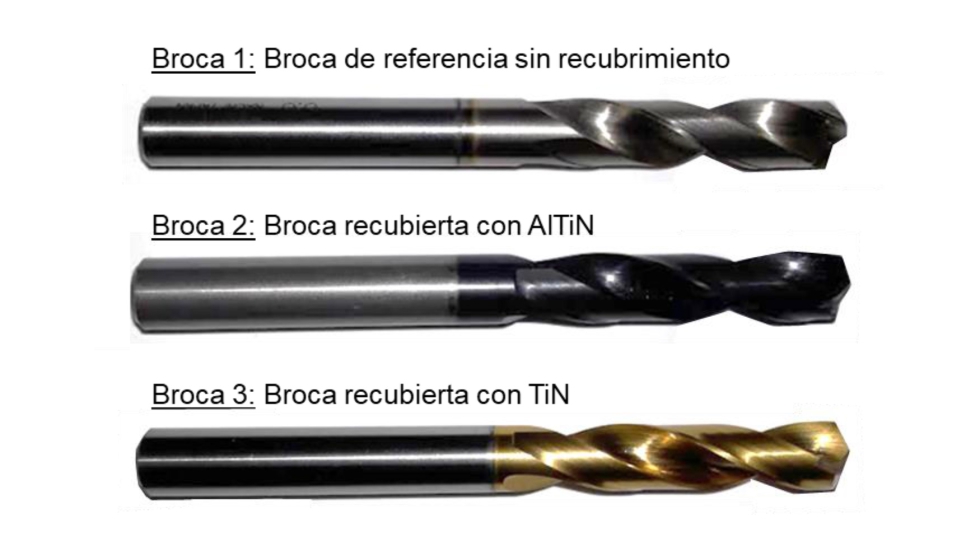
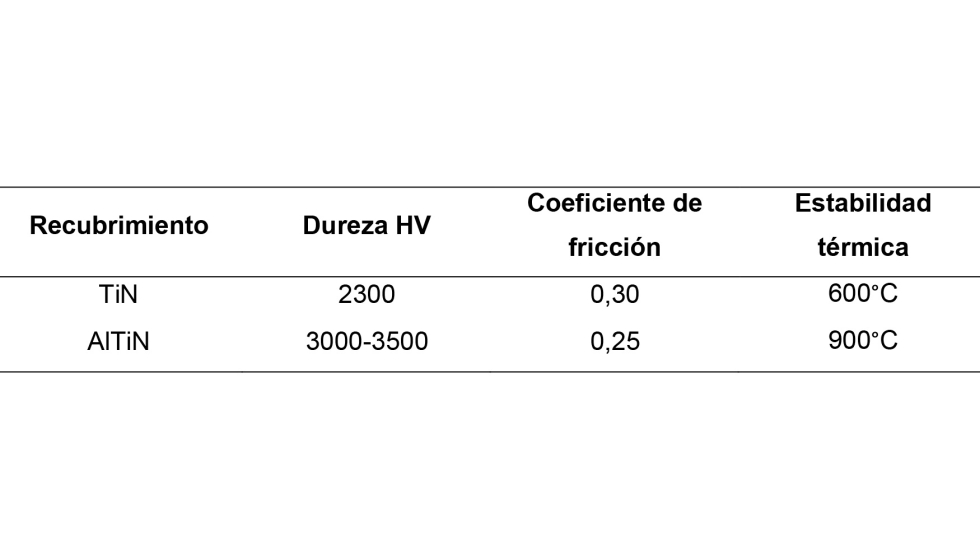
Las condiciones de corte utilizadas durante los ensayos son 45 m/min de velocidad de corte y 0,14 mm/rev de avance. Para recolectar los datos de fuerza de avance y par desarrollados por las brocas se ha utilizado un sistema Artis, un adquisidor de datos que cuenta con sensores externos (un rotor acoplado en el portaherramientas y un estator fuera de la herramienta). Los desgastes de las herramientas se han medido con un microscopio PCE-200. El criterio utilizado para dar el ensayo por concluido fue establecido según la norma ISO 3685, es decir, la obtención de un desgaste de 0,35 mm o la rotura de la herramienta.
Resultados obtenidos
A la hora de analizar el rendimiento de los recubrimientos frente a la broca sin recubrir, se tuvo en cuenta la vida útil alcanzada por cada broca, la fuerza axial generada durante el mecanizado y el par de corte que realizan las brocas al realizar el agujero. En la figura 4 se pueden ver los desgastes obtenidos durante los ensayos.
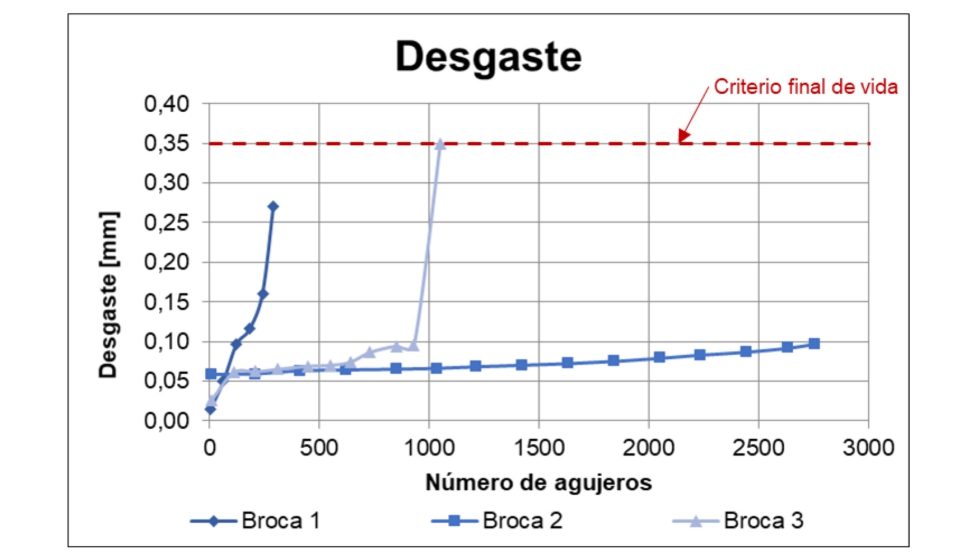
La broca 1, tomada como referencia y que por tanto carece de recubrimiento, realizó 292 agujeros completos, partiendo en el siguiente agujero. Esta broca, al no estar recubierta no presentó la típica curva de desgaste donde se genera una zona estable de desgaste, sino que tuvo una tendencia creciente a lo largo de toda su vida útil.
La broca 3, que fue recubierta con TiN, logró mecanizar 1050 agujeros, es decir, la vida de herramienta incrementa un ≈360% frente a la referencia. En este caso, la evolución del desgaste presentó un patrón típico de este fenómeno en el cual se presenta una zona prolongada de estabilidad antes de alcanzar la zona de desgaste exponencial donde generalmente el corte se vuelve inestable.
La broca 2, la cual fue recubierta con AlTiN, mecanizó un total de 2753 agujeros, es decir, casi un 950% más que la broca sin recubrir de referencia y un 38% más que la broca recubierta con TiN. En este ensayo, cabe destacar que a pesar de que el desgaste apenas alcanza un valor de 0,1 mm cuando alcanzó los 2753 taladros, en el taladro 2754 ésta quedó inservible debido a que el filo transversal de la broca sufrió un aplastamiento quedando por tanto la broca inutilizada la broca inutilizada.
En lo que se refiere a la fuerza de empuje/axial que estuvieron sometidas las brocas, la figura 5 presenta la fuerza generada durante el corte del primer agujero. El motivo de analizar la fuerza en esta etapa es debido que es en la que al no existir prácticamente desgaste se puede observar de forma clara la influencia de los recubrimientos sin otros parámetros que influyan de forma significativa en este.
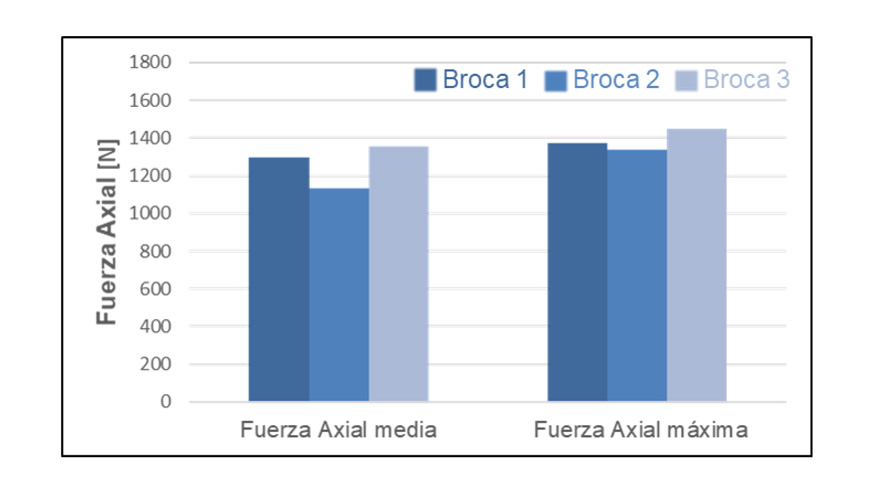
La broca 2, tal y como se puede ver en la figura, es la que menores fuerzas axiales generó durante el mecanizado. Esto se debe a que el recubrimiento AlTiN presenta un menor coeficiente de rozamiento, una mayor dureza combinada con una mayor temperatura de oxidación, que hace que no pierda sus propiedades hasta superar unos rangos de temperaturas superiores a los soportados por las otras dos herramientas. No obstante, hay que destacar que la diferencia de fuerzas entre las tres tipologías de brocas es mínima, no llegando a superar en ningún caso el 10%.
Por último, en la figura 6 se presenta el par de corte durante el mecanizado del primer agujero. Al igual que en la anterior figura, se ha representado el par de corte del primer taladro con el fin de analizar la influencia de los recubrimientos sin que otros factores, como el desgaste, tengan influencia significativa en dichos valores.
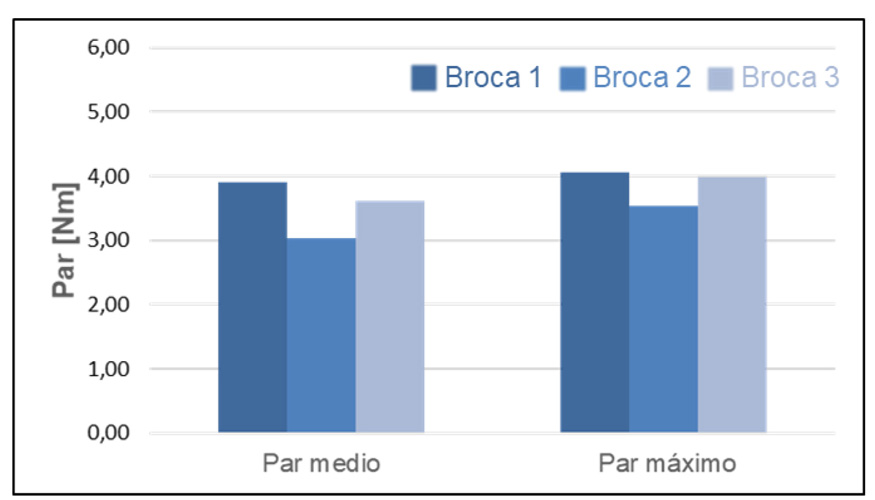
Análogamente a lo ocurrido en el caso de la fuerza axial, la broca recubierta con AlTiN es la que menor par de corte genera durante el mecanizado. En este caso, la diferencia entre la broca 2 (recubierta de AlTiN) y la broca 1 de referencia es mayor del 20%. Sin embargo, hay que destacar que la broca 3 (recubierta de TiN), a diferencia del caso anterior, el par al que está sometida la broca es menor, aunque si bien es cierto, que esta diferencia no es tan significativa como en el caso de la broca recubierta de AlTiN.
Por todo ello, a la vista de los resultados obtenidos el uso de los distintos recubrimientos implica que se provoque sobre las herramientas una reducción de los esfuerzos de corte sobre todo debido a sus bajos coeficientes de rozamiento que hace que la vida útil de las herramientas sea mayor.
Conclusiones
A continuación, se presentan las principales conclusiones obtenidas durante la realización de este estudio en el que se analiza el uso de diferentes recubrimientos en brocas de acero rápido para mecanizar acero DIN 1.2738:
- El uso de recubrimientos en el mecanizado actual con herramientas de acero rápido es crítico a la hora de retrasar el fallo de la herramienta o la aparición de un desgate acusado.
- La reducción de la fricción que trae consigo el recubrimiento de AlTiN junto con la mayor temperatura de oxidación y la mayor dureza ha disminuido en más de un 20% el par de corte generado durante el mecanizado en comparación con la broca sin recubrir. En el caso del recubrimiento de TiN la reducción no ha sido tan grande como en el caso del AlTiN, pero sí que presenta una diferencia notable en comparación con la broca sin recubrir.
- La broca con el recubrimiento de TiN ha superado los 1.000 agujeros mecanizados mientras que la broca sin recubrir únicamente ha realzado 292 agujeros. El uso del recubrimiento de AlTiN ha aumentado el número de agujeros realizados hasta alcanzar un total de 2.753 agujeros, es decir, un 950% más de vida de herramienta que la broca sin recubrir y un 38% en caso de comparar con la vida de herramienta de la broca recubierta con TiN.
Referencias
[1] L.Norberto López de Lacalle, A. Lamikiz, J Fernández de Larrinoa, I. Azkona, «Cutting Tools for hard machining»
[2] D. Li, F. Liu, M. Wang, J. Zhang, Q. Liu, ‘Structural and mechanical properties of multilayered gradient CrN/ZrN coatings’, Thin Solid Films, (2006) 506-507, 202-2
[3] www.platit.com visitado el 11/02/2020 a las 15:00
[4] W. Wu, W. Chen, S. Yang, Y. Lin, S. Zhang, T. Cho, G.H. Lee, S. Kwon. Design of AlCrSiN multilayers and nanocomposite coating for HSS cutting tools. Applied Surface Science, Vol. 351, pp. 803-810, 2015