En prótesis de rodilla se busca reproducir la articulación original, para lo que se requiere materiales resistentes y biocompatibles
Nuevas ideas en mecanizado de prótesis
La rodilla es una de las articulaciones más complejas e imprescindibles del cuerpo humano. Su ubicación se halla en el extremo inferior del muslo (fémur), la parte superior de la pierna (tibia) y la rótula. Esta articulación trabaja todo el día y por eso tenemos la necesidad de tenerla en un buen estado. Si la rodilla no tiene un estado de salud bueno, esto puede causar molestias en nuestra vida cotidiana, al caminar o al correr entre otras actividades. Esta articulación trabaja gracias al movimiento relativo entre el fémur y la tibia, a través del contacto de sus superficies cartilaginosas recubiertas con un líquido sinovial que lubrica la zona. Sin embargo, con el paso del tiempo, el cartílago se va desgastando y los huesos rozan entre sí produciendo un dolor severo y pérdida de funcionalidad. Esta enfermedad se conoce como osteoartritis o artrosis de rodilla y, en su caso más extremo, es una de las principales razones que llevan a una persona a requerir una prótesis de rodilla.
Una prótesis total de rodilla consiste en una serie de elementos implantados, a través de un procedimiento quirúrgico entre el fémur y la tibia y que sustituyen la articulación dañada. Estos elementos son principalmente tres: componente femoral, tibial y meniscal. Este sector está en constante evolución, el diseño de estas prótesis busca reproducir la articulación original para lo que requieren de materiales resistentes y biocompatibles que prolonguen la calidad de vida del paciente. El titanio es un material recurrente en el campo médico gracias a su gran biocompatibilidad. Además, su módulo elástico cercano al óseo y su baja densidad relativa a otros materiales protésicos, lo convierten en un material clave para la fabricación de prótesis de rodilla. Sin embargo, el titanio presenta el inconveniente de ser un material de difícil maquinabilidad que, sumado a los requisitos de salubridad en aplicación protésica, plantea un problema no trivial a la hora de abordar su proceso de fabricación.
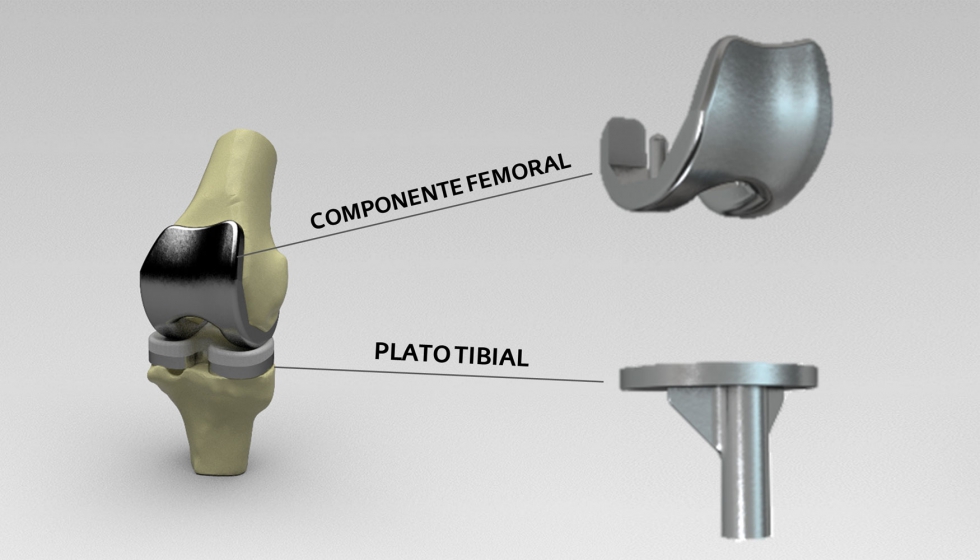
En esta línea, la Escuela de Ingeniería de Bilbao se ha propuesto adentrarse en el proceso de mecanizado de este tipo de componentes, ya que cada vez son más comunes en la vida cotidiana. En este trabajo se va a mostrar el todo el camino recorrido desde la conceptualización de la primera idea hasta el mecanizado de la misma, pasando por las etapas de selección de alternativas o el diseño de trayectorias de mecanizado; explicando brevemente cada uno de los campos más importantes.
1. Proceso de fabricación de una prótesis de rodilla
1.1. Selección de material
Uno de los primeros pasos del proceso fue decidir qué material se iba a emplear en la fabricación de una prótesis de rodilla. Después de realizar una revisión literaria al respecto, se confirmó que las aleaciones de titanio son un material cuyas propiedades de biocompatibilidad y alta resistencia específica lo convierten en un material de gran interés para el mundo aeronáutico y biomédico, dos campos de muy alto valor añadido.
Ahondando un poco más en el material, el titanio puede presentar dos tipos de cristalizaciones: la fase α y la fase β. En la fase α, el titanio presenta una estructura hexagonal compacta; mientras que en la fase β, se transforma en una cúbica centrada a una temperatura de 883°C. En función de la cristalización que presente, las aleaciones de titanio se clasifican en tres categorías:
- Fase ALFA o α. Las aleaciones α son fáciles de soldar y relativamente tenaces a bajas temperaturas. Su principal aleante es el aluminio.
- Fase BETA o β. Poseen una gran formabilidad y su principal aleante es el Vanadio.
- Fase ALFA más BETA o α+β.
De entre las aleaciones α+β, destaca la aleación de titanio Ti6Al4V de aplicación general. Esta aleación posee una excelente combinación de resistencia y dureza, además de ser muy resistente a ataques corrosivos por lo que su uso está muy extendido en el campo aeroespacial, médico y naval. A su vez, dentro de las aleaciones Ti6Al4V se pueden encontrar distintos grados en función de una composición más específica. Por ejemplo, el grado 5 es el que se suele emplear en aeronáutica, mientras Grado 23 ELI (Extra Low Intersticials) se emplea para la fabricación de implantes dentales y prótesis. La diferencia entre ambos es que el grado 23 tiene un menor contenido de impurezas intersticiales que mejoran la biocompatibilidad del material.
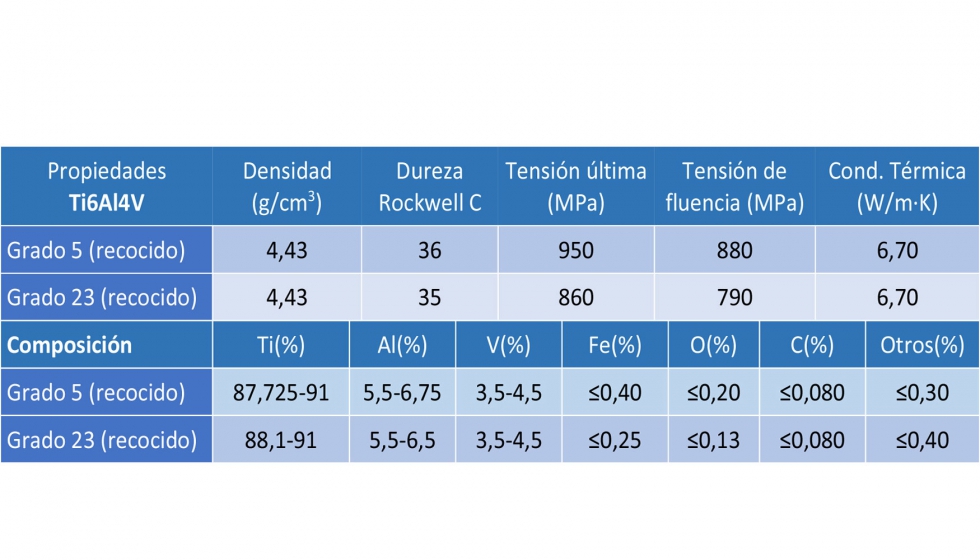
Además, hay que tener en consideración la difícil maquinabilidad de este tipo de material, que, a diferencia de otros, su baja maquinabilidad no se debe a las fuerzas de corte, sino debido principalmente a dos propiedades del propio material: su baja conductividad térmica y su alta reactividad. Para este trabajo el material seleccionado fue la aleación Ti6Al4V grado 5 debido a la diferencia de material entre ambos materiales, ya que en ningún caso iba a emplearse en ningún paciente dicha prótesis.
1.2. Selección del bruto de partida
La elección del bruto o material de partida es de suma importancia, pues ésta repercute, entre otros factores, en el peso del mecanizado sobre el proceso global de producción de la prótesis. Esto es, dependiendo del proceso del que provenga el bruto de partida y de su geometría, el tiempo y coste del mecanizado influirá en mayor o menor medida sobre el coste y tiempo total de producción. Por ello, se plantearon distintas alternativas para ambos componentes:
- Bruto laminado. Consistía en un tocho prismático que contuviera la pieza que se desea mecanizar. Este tocho provendría de una barra laminada de sección cuadrada normalizada. Su producción es elevada y no requería un proceso específico para este trabajo, por lo que su valor se reduce prácticamente al precio de coste.
- Pieza forjada. Se trataría de una pieza con una geometría cercana a la final. Las propiedades mecánicas de la pieza mejorarían gracias a la orientación del fibrado en el proceso de forja. Sin embargo, cuanto más se aproxime a la pieza final, mayor será el coste de la pieza forjada y menor la influencia del mecanizado. Este proceso solo se hubiera justificado con una tirada media/alta.
- Pieza de fundición. El mecanizado partiría de una pieza cercana a la pieza final por lo que solo hubiera requerido de operaciones de semiacabado y acabado, por lo que el mecanizado perdería peso en el proceso de fabricación. El coste por pieza aumentaría cuanto más se aproxima a la pieza final. La porosidad del proceso la convierten en la peor de las tres alternativas en cuanto a integridad metalúrgica. Esta alternativa solo se justificaría con una producción elevada.
La alternativa escogida fue el bruto laminado. Los componentes se fabricaron a partir de un tocho prismático en el que se realizaron operaciones de desbaste, semiacabado y acabado. En donde se les dieron mayor peso a las operaciones de mecanizado.
1.3. Estrategias de amarre
Desde el punto de vista de las estrategias de mecanizado, el componente femoral puede considerarse una pieza de geometría compleja. Teniendo en cuenta que se parte de un tocho prismático, en el caso de que se quisiera realizar en una máquina de 3 ejes, se tendría que llevar a cabo en varias atadas. Además del tiempo adicional que requiere, un cambio de atada induce imprecisiones en la geometría final de la pieza, llegando a ser mayor cuanto mayor sea el número de atadas. No obstante, estas imprecisiones se pueden llegar a controlar y minimizar con una buena estrategia de operaciones. La premisa de este trabajo de emplear un centro de mecanizado de 5 ejes permite aumentar la precisión del proceso, ya que mejora potencialmente la accesibilidad de la herramienta de manera que puede llegar a realizarse en una única atada. Sin embargo, existen otros factores que afectan a la precisión del proceso, como es la rigidez del sistema pieza-máquina. Y es que las fuerzas de corte pueden llegar a deformar la pieza si el sistema no es lo suficientemente rígido, de manera que la geometría de la pieza final no es la esperada. Por ello, fue necesario seleccionar el sistema de amarre de la pieza y la disposición de la misma en la máquina que asegurasen la mayor precisión del proceso de mecanizado. Las alternativas planteadas fueron.
Alternativa 1. Esta alternativa no era viable para este proyecto porque la configuración está diseñada para una cinemática distinta a la del centro de mecanizado disponible, pero sirve de base para la siguiente alternativa. La pieza está contenida en una barra cilíndrica dispuesta de manera horizontal. Esta configuración permite realizar todas las operaciones en una misma atada, ya que, a través del eje A (correspondiente al giro alrededor del eje X), se puede orientar la pieza de modo que la herramienta sea accesible a todas las zonas. El contrapunto proporciona rigidez al sistema.
Alternativa 2. Esta alternativa es una adaptación a la configuración del centro de mecanizado disponible. Esta disposición permite realizar todas las operaciones en una misma atada. Sin embargo, no existe posibilidad de poner contrapunto, por lo que el sistema pierde rigidez. La pieza queda en voladizo y la posición de la cuna necesaria para que la pieza quede orientada como se muestra en la figura, no es la más estable para la máquina. Ello lo convierten en susceptible a deformaciones durante las operaciones de mayor solicitación mecánica, como son las de desbaste.
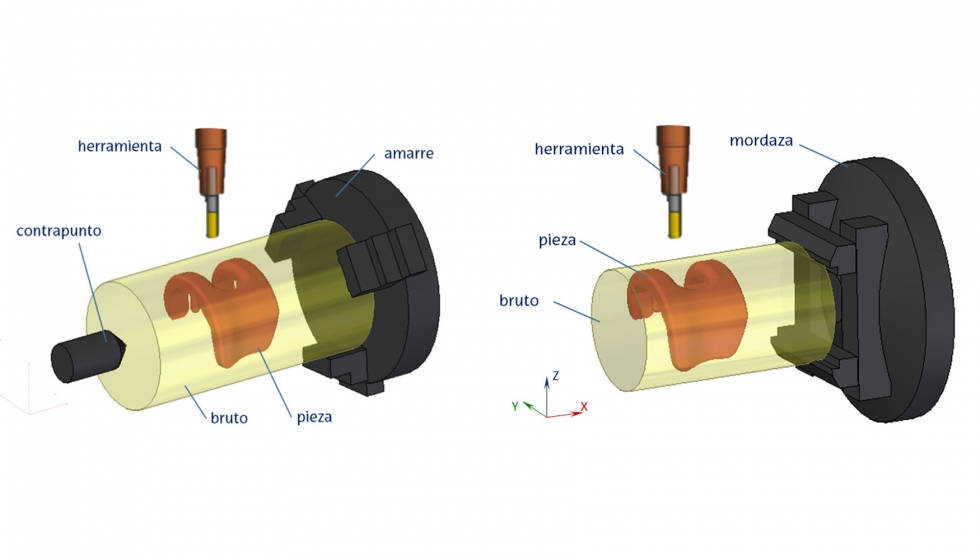
Alternativa 3. El bruto es un cubo circunscrito a la pieza y es amarrado por una mordaza. Esta configuración implica emplear dos atadas. En la primera, se realiza la zona interior (o cavidad) del componente femoral y en la segunda, las superficies exteriores de los cóndilos y pared rotuliana (o zona convexa). Para la segunda atada es necesario un utillaje para sujetar la pieza. A pesar de ello, esta alternativa mejora la estabilidad de la máquina.
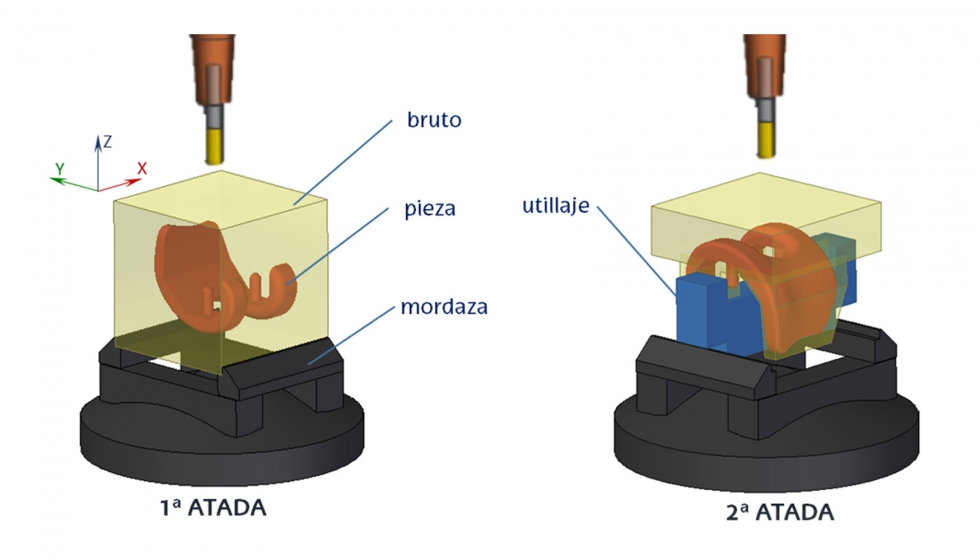
La solución escogida fue la alternativa 3. A pesar de requerir dos atadas, es la que proporciona mayor rigidez a la pieza y estabilidad a la máquina para el proceso de corte. La primera alternativa no era viable debido a que la configuración cinemática de la máquina requerida es diferente a la disponible. La adaptación de al centro de mecanizado disponible obliga a prescindir del contrapunto, lo que implica una menor rigidez en la pieza.
1.4. Resumen de la solución
De entre todas las alternativas que se plantearon durante la realización del trabajo, se optó por las siguientes soluciones:
Componente Femoral. Se decidió fabricar en una aleación de titanio Ti6Al4V (grado 5) en el centro de mecanizado Kondia HS1000 disponible en la Escuela de Ingeniería de Bilbao. Su proceso se dividiría en dos atadas partiendo de un tocho de sección cuadrada circunscrita a la pieza. En la primera atada se realizarían las operaciones necesarias para la referencia de las siguiente atada y el acabado de la zona de unión con el fémur. En la segunda atada, con la ayuda de un utillaje se finalizaría el resto de la pieza.
Componente tibial. Se decidió fabricar en una aleación de titanio Ti64AlV (grado 5) en el centro de mecanizado Kondia HS1000 disponible en la Escuela de Ingeniería de Bilbao. Su proceso de mecanizado se dividiría en dos atadas partiendo de un tocho de sección cuadrada circunscrita a la pieza. En la primera atada, se realizían las operaciones necesarias para la referencia en la siguiente atada y el acabado de la meseta tibial que sirvirían de unión con el inserto meniscal. En la segunda atada, se finaliza el resto de la pieza.
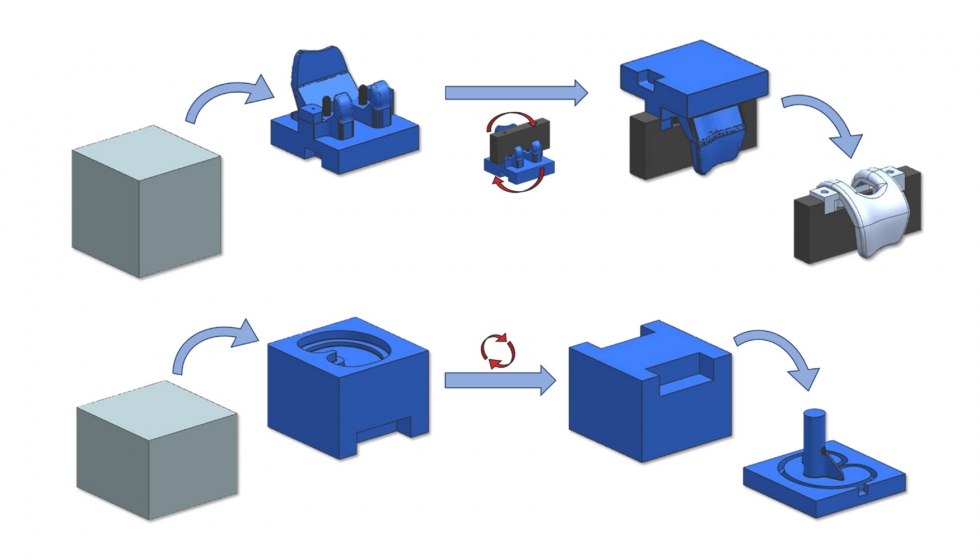
Componente meniscal. Se decidió fabricar usando ABS (Acrilonitrilo Butadieno Estireno) en una máquina de prototipado de plástico. Aunque no cumpla los requisitos reales del inserto meniscal, sirve como complemento para la exposición de la prótesis completa.
1.5. Diseño CAD de las geometrías
El modelo completo se realizó con el módulo CAD del software Siemens NX12 y el diseño de los componentes protésicos se basaron en unos modelos de endoprótesis de rodilla Columbus, de la empresa B. Braun. El sistema Columbus proporciona el material quirúrgico necesario para la artroplastia de rodilla, desde una amplia gama de modelos de prótesis hasta las herramientas necesarias para su implementación. A continuación, se muestran una serie de planos con las cotas más representativas de los componentes femoral y tibial.
El componente femoral está compuesto principalmente de dos cóndilos simétricos que mejoran la estabilidad de la rodilla en todo movimiento de flexo-extensión, una superficie curva sobre la que desliza la rótula y dos espigas interiores que mejoran la unión al hueso. Desde el punto de vista del mecanizado, son de especial interés la superficie rotuliana y la de los cóndilos, ya que son las zonas de contacto y deslizamiento con la rótula y el componente meniscal respectivamente. Por ello, estas zonas deben tener un buen acabado superficial para disminuir la fricción entre componentes y evitar así el desgaste de las piezas y las molestias en el paciente.
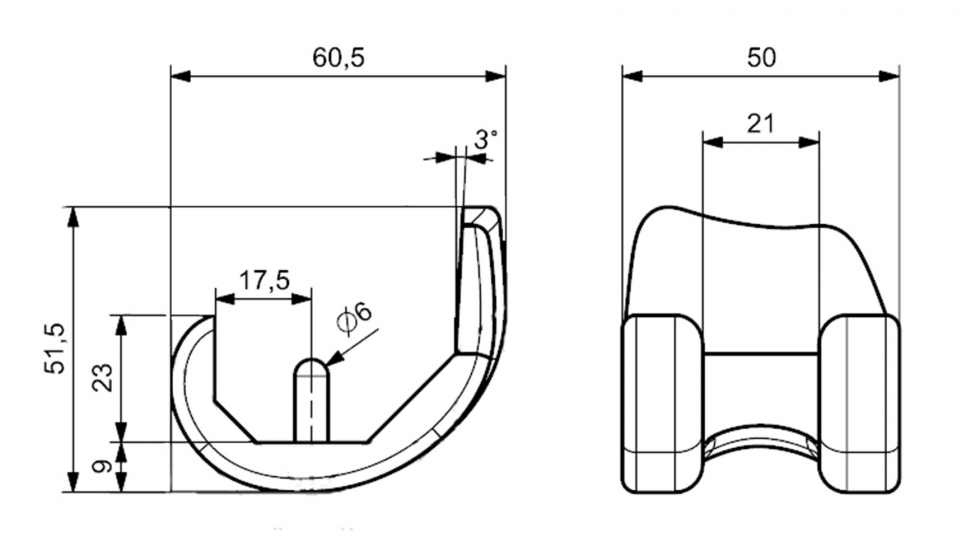
El componente tibial es el enlace entre el inserto meniscal y el hueso de la tibia. Su principal función es soportar las cargas generadas en la articulación y proporcionar un mejor reparto de los esfuerzos en la tibia. Al igual que el componente femoral, la fabricación del componente tibial parte de un cubo laminado que contiene a la pieza y debido a su geometría, junto a la configuración cinemática de la máquina, el proceso de mecanizado planteado también radica en dos atadas.
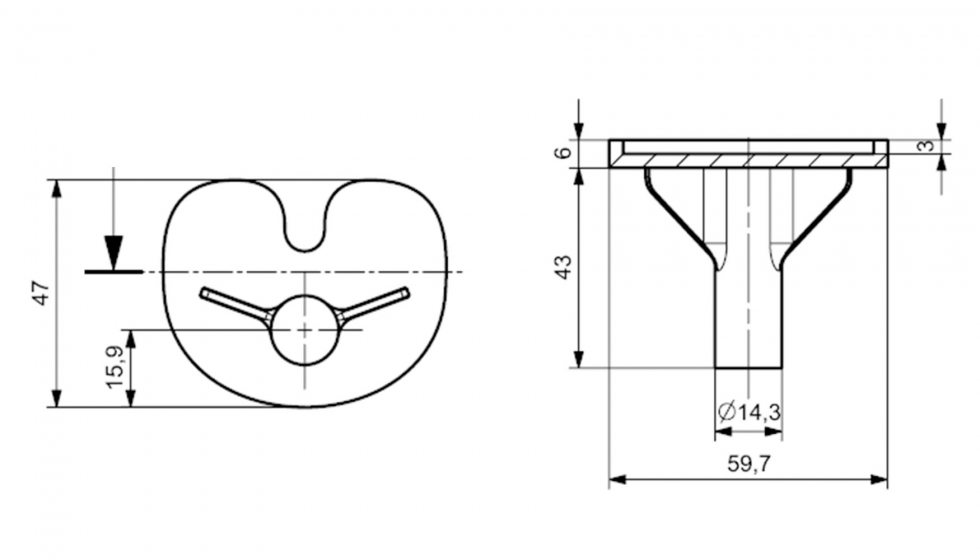
1.6. Diseño CAM de las trayectorias
El programa diseñado partía de un cubo de 80x80x80 mm de material Ti6Al4V en el caso del componente femoral. El mecanizado se realizó en dos atadas y requirió de un utillaje en forma de U para poder amarrar la pieza en la segunda atada.
El cero-pieza o MCS correspondiente a la atada 1 se situó en uno de los vértices de la cara superior del cubo, mientras que para la atada 2, el cero-pieza se encontraba en una cajera de referencia realizada en la atada 1. En la siguiente imagen se puede apreciar la evolución de dicho componente.
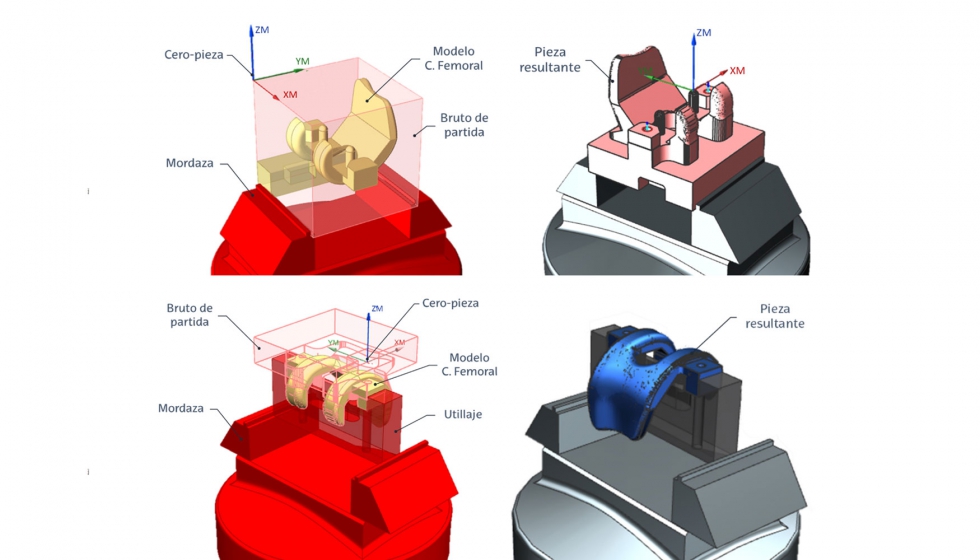
El componente femoral requiere de numerosas operaciones para ser correctamente mecanizada. La primera atada comenzó con un desbaste general en el que se buscaba arrancar la mayor cantidad posible de viruta en el menor tiempo posible. Para aproximar la pieza a su geometría final, se realizó un redesbaste disminuyendo la profundidad de pasada. También se realizó una operación de desbaste concentrada en la superficie de contacto con la rótula. Finalmente se desbastó la cajera que sirviría de referencia para la segunda atada. Después se realizaron las operaciones de semiacabado a lo largo de las distintas zonas del componente para dejar una demasía de 0,2 mm homogénea a lo largo de toda la superficie. Las operaciones de acabado se centraron en dejar acabada la parte interior de la pieza, ya que no era accesible en la atada 2.
Al igual que en la primera atada, se realizó una primera operación de desbaste general que fue mecanizando por capas, y seguido un redesbaste con una pasada axial menor para aproximarse a la geometría final. Al igual que en la primera atada, se realizaron las operaciones de semiacabado para homogeneizar la superficie a una demasía de 0,2 mm. Finalmente se realizó las operaciones de acabado.
Como se adelantaba en el diseño CAD, las superficies correspondientes a los cóndilos y a la cara rotuliana requieren un muy buen acabado superficial (rugosidad baja). Para ello, las operaciones correspondientes a estas zonas se programaron en 5 ejes para mantener fija la orientación del eje de la herramienta con respecto a la superficie. Esta orientación asegura que la herramienta no corte con la punta de la bola, ya que en dicho punto la velocidad de corte es nula. Además, las trayectorias están programadas en zig, de modo que el corte siempre sea en concordancia.
En el caso del componente tibial, también se programaron 2 atadas. En la primera de ellas se buscó 2 objetivos, preparar el bruto para el amarre referenciado de la atada 2 y dejar finalizada la meseta tibial. Primero se realizó un planeado de la cara superior y un recanteado perimetral de esa misma cara con el fin de que asegurar que el bruto estuviese escuadrado y alineado con la pieza. La mordaza en la atada 2 agarró por dos de las caras escuadradas. Después se practicaron dos cajeras en la parte inferior que sirvieron para tomar el cero en la atada 2. El mecanizado de la meseta tibial se realizó con una operación de desbaste y otra de acabado, con entrada en hélice y con una trayectoria de seguimiento del perímetro.
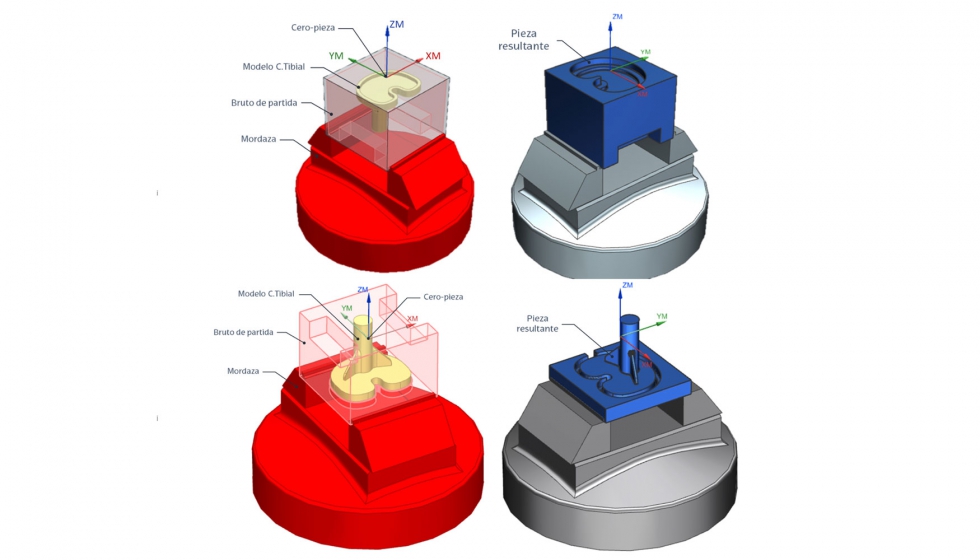
El resultado obtenido de los procesos de mecanizado de los componentes femoral y tibial se puede ver en la siguiente imagen.
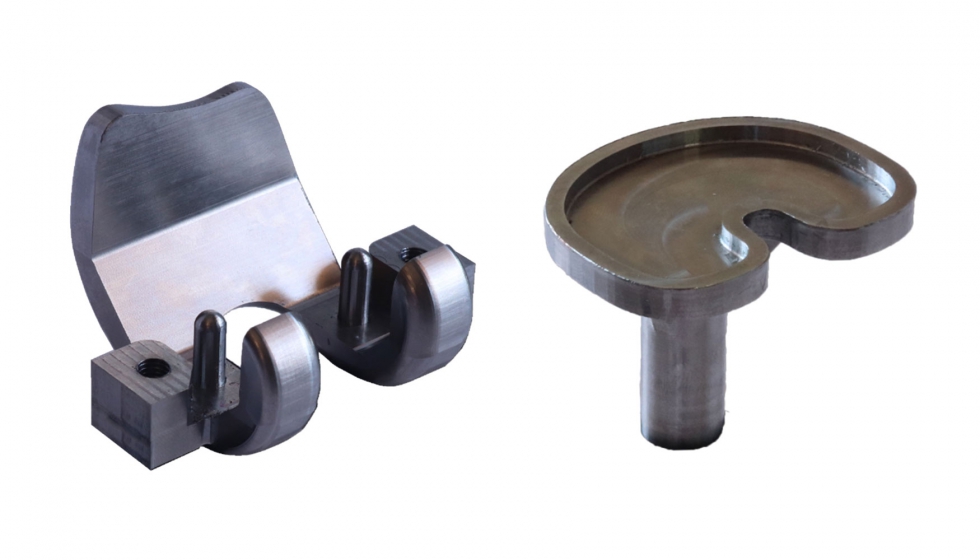