Caracterización del desgaste de herramientas rotativas de superabrasivo
Uno de los aspectos más importantes del rectificado es el diamantado, proceso usado para regenerar tanto la capacidad abrasiva de las muelas como su forma inicial. En general, los diamantadores se pueden clasificar en estáticos o rotativos. El comportamiento de los diamantadores estáticos ha sido analizado desde el punto de vista científico [2], y a nivel industrial, no conlleva problemas en la producción; sin embargo, los diamantadores rotativos son una fuente continua de errores y rechazos de piezas. Se caracterizan por su alta velocidad de giro y la posibilidad de generar geometrías complejas. Por ello, estos tipos de diamantadores son ampliamente usados en la industria con procesos de rectificado que requieren geometrías complejas, alta repetitividad y alta precisión. Asimismo, el desgaste de los diamantadores rotativos es uno de los hándicaps para los usuarios ya que el desgaste sufrido por los diamantadores se refleja en la superficie de la muela y, ésta a su vez, plasma el error en la pieza final, dando lugar a un gran número de piezas rechazadas. Es por ello que, a nivel industrial, existe un gran interés por caracterizar el desgaste sufrido por los diamantadores rotativos. En la figura 1 se puede observar una muestra de la gran variedad de configuraciones de diamantadores rotativos que se encuentran en el mercado.
![Figura 1. Diferentes configuraciones de diamantadores rotativos [1] Figura 1. Diferentes configuraciones de diamantadores rotativos [1]](https://img.interempresas.net/fotos/2182090.jpeg)
Por otro lado, durante los últimos años, el uso de muelas de superabrasivo, especialmente de CBN, se ha extendido en la industria gracias a su estabilidad térmica y a la ausencia de afinidad química con materiales férricos. Asimismo, gracias a su dureza, es apropiado para aplicaciones de gran arranque de viruta como el Creep Feed Grinding, High Speed Grinding o Superabrasive Machining (SAM). Además, en función de la aplicación los aglomerantes que se usan en este tipo de muelas puedes ser vítreos, resinosos o metálicos. La gran ventaja de las muelas con aglomerante vítreo es la refrigeración del proceso, así como su capacidad de ser diamantado mediante el uso de diamantadores rotativos. Sin embargo, para determinadas aplicaciones, por ejemplo, para geometrías complejas en las que se requieren estrechas tolerancias geométricas, las muelas electrodepositadas, con aglomerante metálico, son necesarias, ya que éstas no pierden su forma inicial. Una de estas aplicaciones son las muelas de pequeños diámetros utilizadas en procesos de SAM.
El mecanizado superabrasivo (SAM) es un proceso que presenta las ventajas del fresado convencional y a su vez del proceso de rectificado; este proceso se podría definir como ‘rectificado en condiciones de mecanizado’. Además, debido al tamaño que presentan las herramientas puede ser utilizado en una máquina multitasking que combine procesos de fresado y de SAM. Cabe destacar que la principal limitación que presenta dicho proceso está relacionada con las características de la máquina, puesto que para operar en condiciones óptimas puede llegar a requerir una velocidad de rotación del husillo de entre 60.000 y 80.000 rpm. En la figura 2 se muestra una muela de desbaste de SAM empleada para el mecanizado de álabes de Inconel®718 de un motor de avión, estas herramientas pueden presentar diferentes geometrías adaptativas a la superficie a mecanizar, como es el caso de las herramientas de SAM para la fabricación de fir-threes [4]. Estas muelas no se diamantan durante su vida útil, es decir, ni su forma ni su capacidad abrasivas se pueden recuperar una vez desgastadas. Al igual que ocurre con el desgaste de los diamantadores, el desgaste de las muelas de SAM afecta a las tolerancias geométricas, dimensionales, e incluso a la calidad superficial de la pieza rectificada. Por ello, caracterizar el desgaste de este tipo de muelas es imprescindible para evitar que las piezas sean rechazadas.
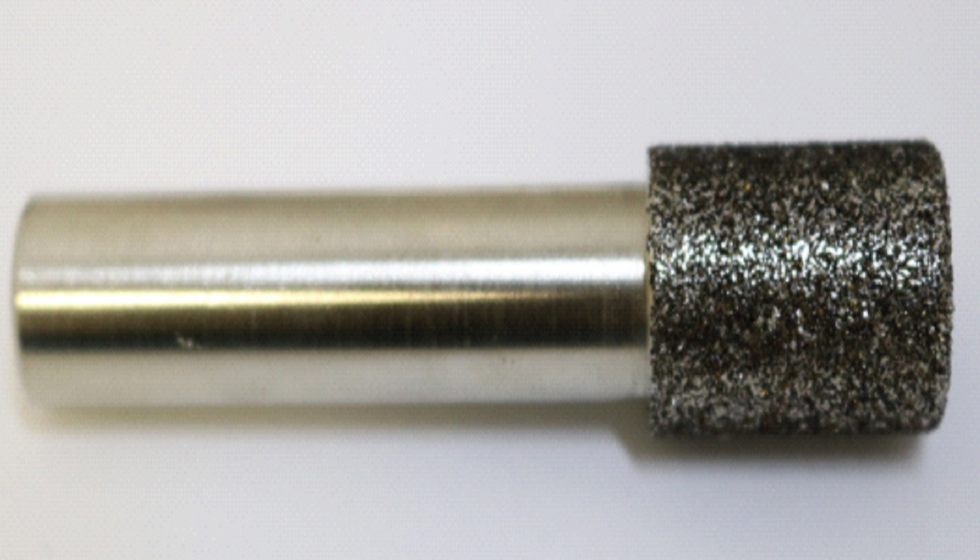
Debido a la similitud en cuanto a la problemática de las dos herramientas de superabrasivo, así como al gran interés industrial, en este trabajo se diseña una metodología para la caracterización de cada tipo de herramienta abrasiva. En ambos casos se trata de materiales superabrasivos, sin embargo, la disposición de los mismos en la matriz metálica es diferente. Esto lleva a realizar dos metodologías de caracterización del desgaste diferentes, una para abrasivos embebidos y otra para abrasivos electrodepositados. Además, para cada una de las tipologías de herramienta superabrasiva se muestra un caso de aplicación industrial real.
Metodología para la caracterización de diamantadores rotativos con diamantes embebidos
Existe una gran variedad de diamantadores rotativos a nivel industrial en función de su geometría, material superabrasivo y la disposición del mismo en el cuerpo metálico. Incluso el fabricante del mismo tiene influencia en la configuración de los diamantes y combinación abrasivo-aglomerante utilizada. Es por ello, que diseñar una metodología de caracterización de los diamantadores rotativos es de gran interés, tanto para la industria como para los investigadores. En este trabajo se plantea una metodología de caracterización del desgaste de diamantadores rotativos mediante ensayos de diamantado acumulativo.
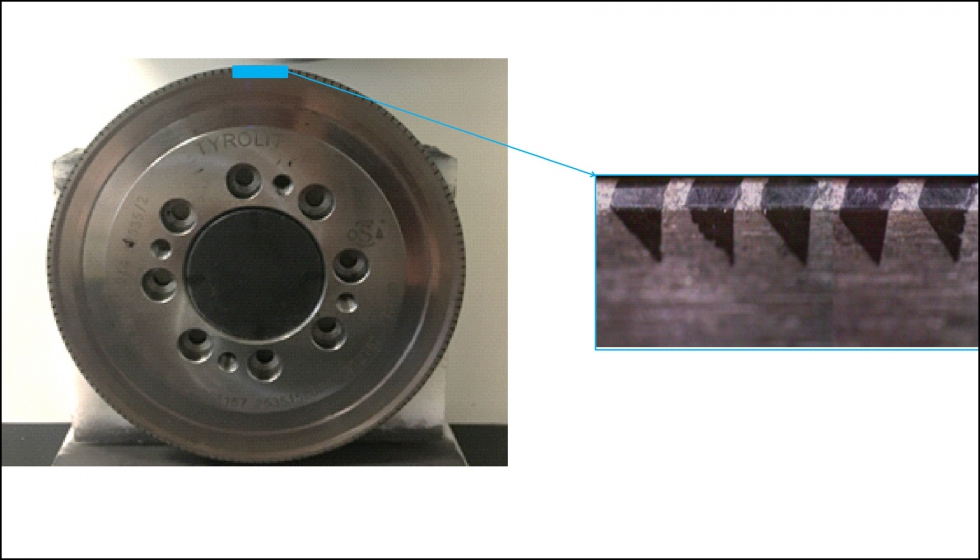
Se ha seleccionado un diamantador rotativo con diamantes CVD insertados de forma radial en un cuerpo metálico, tal y como se detalla en la figura 3. La nomenclatura del diamantador rotativo es RIG 52034 fabricado por Tyrolit. En la tabla 1 se detallan las características geométricas del diamantador y se muestra el patrón de los diamantes insertados. Además, la muela a diamantar es de CBN con aglomerante vítreo, con la siguiente nomenclatura CBN170N100V, de diámetro exterior 450mm y ancho 10,3mm. Los ensayos se realizan en una rectificadora cilíndrica DANOBAT FG600S con refrigerante a alta presión, 13bar.
Características geométricas |
|
Diámetro exterior | 120 mm |
Diámetro interior | 40 mm |
Ancho | 3,88 mm |
Radio de punta | 0,25 mm |
Tabla 1. Características geométricas del diamantador rotativo.
La metodología diseñada integra ensayos de diamanto y rectificado, mediciones del diamante rotativo off-line y el desarrollo de un programa en Python para cuantificar el desgaste del diamantador. Para la medición del desgaste se usa microscopía confocal, específicamente se ha usado el microscopio confocal Leica DCM 3D. Antes de realizar los ensayos, se mide la topografía del diamantador, la cual se tomará como referencia para posteriormente poder cuantificar el desgaste sufrido. Tras la primera medición se realizan los ensayos de desgaste acumulativo del diamantador, en la tabla 2 se recogen los parámetros de diamantado utilizado. Finalmente, se mide la topografía del diamantador con el microscopio confocal anteriormente citado. Esta secuencia de pasos se repite 4 veces, eliminando en cada uno de los pasos 12.354 mm3 de volumen de muela, hasta un total de 49.415 mm3.
Parámetros de diamantado |
|
Velocidad de corte de la muela vs | 50 m/s |
Velocidad de giro del diamante nd | 3.453 rpm |
Profundidad de pasada del diamantador ad | 10 µm |
Ratio de velocidades muela-diamantador | 0,434 |
Velocidad de avance del diamantador vfd | 100 mm/min |
Tabla 2. Parámetros de diamantado.
Una vez llevados a cabo los ensayos, es necesario procesar y analizar las topografías para cuantificar el desgaste del diamantador. Para ello, en primer lugar, se muestran en detalle los parámetros utilizados para la medición de las topografías, así como el procedimiento a seguir para poder cuantificar el desgaste. En la figura 4 se detalla el procedimiento desde la adquisición de la topografía hasta la obtención del perfil del diamantador rotativo. El primer paso es medir la topografía de la muela en 4 sectores diferentes, el área de medición es de 2.546 x8.477 mm2 y la altura escaneada es de 2.808mm. Posteriormente, de cada topografía 3D se extraen 5 perfiles 2D, haciéndolos coincidir con los diamantes insertados. De cada estado de desgaste obtenemos un total de 20 perfiles.
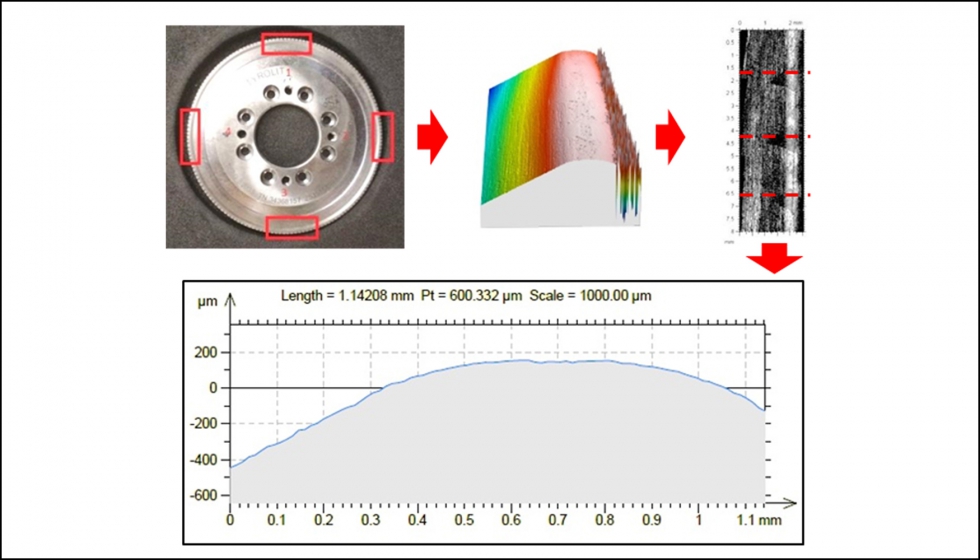
Para realizar un correcto tratamiento de los perfiles y con el fin de comparar los diferentes estados de desgaste, se desarrolla un programa en Python que permite realizar esta comparación y obtener valores cuantitativos del desgaste. Este programa consiste en la superposición de perfiles en sus diferentes fases del desgaste. En primer lugar, se elimina el ruido de las señales filtrando las señales con una frecuencia de corte de 1,5Hz. Posteriormente, para obtener los valores de desgaste del diamantador, se superponen los perfiles y se aplica la técnica Best-Fitting. Para la aplicación de esta técnica, es necesario fijar dos puntos de referencia, los cuales no van a sufrir desgaste, es decir, se van a mantener durante todo el proceso para poder usarlos como puntos de referencia. En la figura 5 se muestra el proceso de filtrado y superposición de perfiles que permiten cuantificar el desgaste. En la primera imagen se observan las zonas de referencia que no sufren desgaste, en la siguiente se observan los puntos 1 y 2 correspondientes a la referencia de dos perfiles diferentes, uno sin desgaste y otro desgastado, y en el tercer paso se puede observar la diferencia entre perfiles.
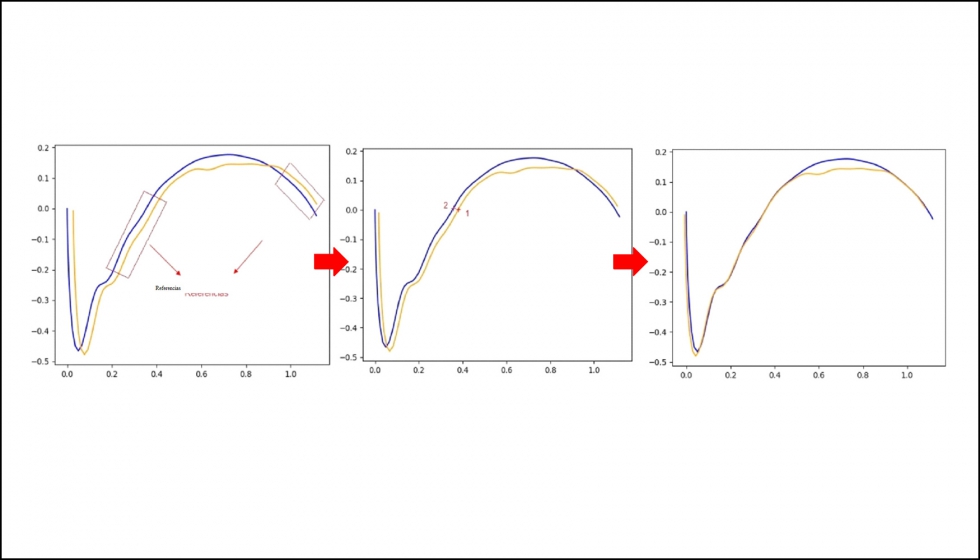
Una vez superpuestos los perfiles, en la figura 6 se observa el área desgastada del diamantador, la altura del desgaste (hd) y la longitud de contacto entre el diamantador rotativo y la muela abrasiva. Este proceso se aplica a cada etapa del desgaste y para la obtención de los resultados del desgaste se hace la media entre los 20 perfiles en cada estado del desgaste. En la parte inferior de la figura 6 Se muestra la evolución del volumen desgastado de diamantador en función del volumen de muela eliminado y la evolución de la altura de diamante desgastada. Estos dos parámetros cuantifican el desgaste de las moletas rotativas. Por un lado, cuantificar la altura de desgaste permite corregir la trayectoria de los diamantadores para asegurar un correcto reperfilado de las muelas en caso de presentar geometrías complejas. Por otro lado, conocer el volumen de desgaste es primordial para determinar la vida útil de los diamantadores rotativos [3]. Además, cabe destacar que la metodología aplicada es de utilidad para la caracterización de diferentes tipos de moletas rotativas que se encuentran en el mercado.
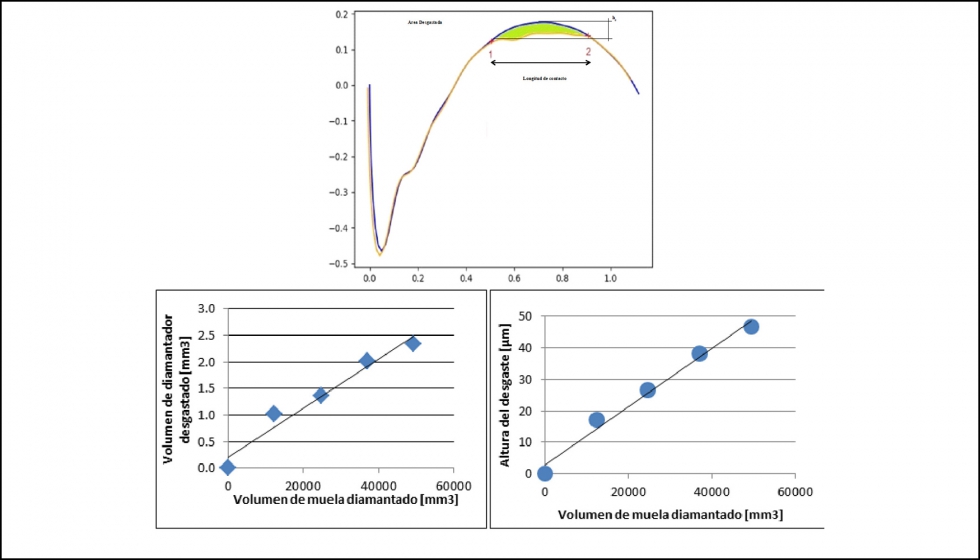
Caracterización de los tipos de desgaste presentes en herramientas de SAM
En comparación con los procesos de rectificado convencionales, el SAM se considera un proceso nuevo y emergente en la industria, siendo además un proceso más agresivo que los procesos de mecanizado como el fresado o el torneado. En este sentido, el proceso de SAM es comparable al proceso de Creep Feed Grinding, en el que se utilizan profundidades de pasada grandes, incluso del orden de 1 ó 2 mm. De este modo, el proceso de SAM genera elevadas temperaturas en la zona de corte que se han de controlar con diferentes técnicas de refrigeración-lubricación para evitar daños térmicos.
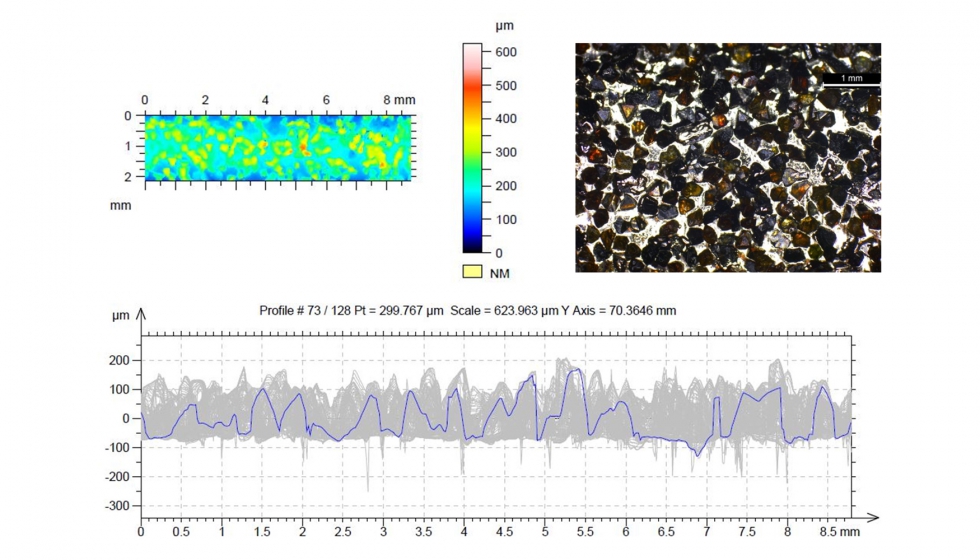
Las muelas utilizadas para el proceso de SAM son muelas de pequeño diámetro comparadas con las muelas de rectificado, su geometría podría equipararse a la de algunos diamantadores rotativos. Además, las muelas de SAM se fabrican con materiales superabrasivos, normalmente de CBN debido a su estabilidad térmica y son muelas electrodepositadas. No sólo por su geometría, sino también por el material abrasivo, la metodología de análisis para diamantadores rotativos y para muelas de SAM es similar.
Al igual que se ha mencionado anteriormente, uno de los hándicaps de estos procesos es el desgaste sufrido por las muelas o moletas. Por ello, es de gran importancia caracterizar el desgaste sufrido por las herramientas de SAM durante el proceso. Para caracterizar los tipos de desgaste presentes en un proceso de SAM se ha diseñado una metodología de ensayo, y se ha aplicado al siguiente caso concreto. Se ha realizado una serie de ensayos aplicados en un material aeronáutico Inconel718. La herramienta seleccionada es monocapa electrodepositada de CBN (Diprotex EB300 CBN109677 912134521-03) con una geometría cilíndrica de 16 mm de diámetro, una longitud efectiva de corte de 20 mm y un tamaño de grano de 300 µm. La figura 7 representa el perfil y la distribución de granos de la herramienta seleccionada.
En la tabla 3 se detallan los parámetros de corte utilizados para obtener los distintos tipos de desgaste presentes en este proceso, al tratarse de un proceso relativamente cercano al fresado y utilizando una máquina multitasking, los parámetros vienen representados de similar manera que en el fresado convencional. Para ello, se han realizado una serie de ranurados puesto que se dan bajo condiciones extremas de mecanizado, dificultad de evacuación de calor y viruta. Los ensayos se han llevado a cabo en un centro de mecanizado Ibarmia ZV-25/U600, consta de 5 ejes de mecanizado simultáneo, 3 lineales y 2 rotativos, con una configuración plato-cuna para una futura aplicación de fabricación de geometrías complejas en 5 ejes simultáneos.
Tras la realización de los diferentes ensayos, se ha obtenido una topografía 3D utilizando el microscopio confocal Leica DCM 3D a lo largo de diferentes secciones de la herramienta, considerando más crítica la sección más próxima a la punta de herramienta puesto que es la zona en donde se producen mayores valores de temperatura y dispone del menor espacio de evacuación de viruta. Además, cabe destacar la dificultad presentada por el material a mecanizar en este caso, Inconel718. En la herramienta de SAM se han reconocido, en mayor medida, tres tipos de desgastes mostrados en la figura 8: adhesión de material o embotamiento, desgaste de grano plano y desprendimiento de grano. La adhesión de material se presenta como una acumulación del material objeto de mecanizado sobre la herramienta, se deben principalmente a la insuficiencia de refrigeración-lubricación del proceso en cuestión. El desgaste de grano plano y el desprendimiento de grano son más comunes en estos procesos y se caracterizan por la desaparición o desprendimiento de los granos abrasivos. Estos desgastes son comunes debido a que se trata de un proceso de altas temperaturas en la zona de corte y las presiones presentes entre la herramienta y la pieza durante el proceso abrasivo.
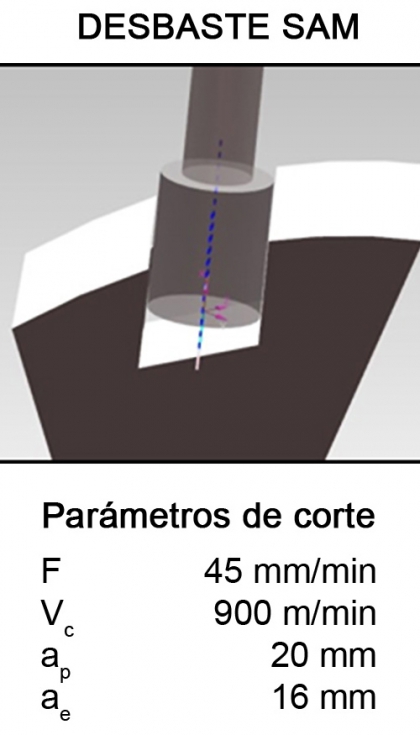
Conclusiones
El proceso de rectificado es un proceso de gran valor añadido el cual ha sido y es objeto de estudio durante muchos años y hoy día lo sigue siendo. Dentro del proceso de rectificado, el diamantado es uno de los procesos más críticos para conseguir las condiciones de rectificado óptimas. Por ello, el control del proceso de diamantado es esencial para conseguir buenas tolerancias dimensionales y geométricas, así como buenos acabados superficiales. Por otro lado, el proceso de rectificado se ha ido continuamente adaptando a las necesidades industriales, en primer lugar, con la evolución de las muelas de superabrasivo, con los procesos de Creep Feed Grinding o High Speed Efficiency Grinding y en los últimos años es el proceso de SAM el último en incorporarse a estos nuevos procesos. Como se ha comentado, el proceso de SAM ha surgido para dar respuesta a necesidades industriales en las que ni el mecanizado ni el rectificado encontraban cavidad. Es por ello, que el proceso SAM utilizando una herramienta superabrasiva con parámetros más cercanos a los parámetros de mecanizado de alta velocidad dan lugar a un mecanizado con altas velocidades de corte y grandes ratios de arranque de material, mayores que los del proceso de rectificado. Cabe destacar que su uso cobra especial interés en aquellos materiales de baja maquinabilidad, como es el caso de superaleaciones termorresistentes base Níquel o Titanio.
Sin embargo, y como denominador común entre el diamantado rotativo y el proceso de SAM, nos encontramos con el problema de desgaste de las herramientas rotativas. Se ha visto la necesidad de caracterizar estos desgastes y es por ello, que en este artículo se han presentado 2 metodologías de ensayo en las que se detalla cómo caracterizar y cuantificar el desgaste en ambos casos. Por un lado, en el caso de los diamantadores rotativos se ha cuantificado la pérdida de forma del diamantador mediante los parámetros altura del desgaste (hd) y volumen de desgaste del diamantador (vd). Es importante destacar que cualquier pérdida geométrica del diamantador se verá reflejada en la muela y por ende en la pieza, no cumpliendo los requisitos geométricos y dimensionales. Por otro lado, en el caso de las muelas de SAM se han detectado 3 tipos de desgaste frecuente: la adhesión de material, el desgaste de grano plano y el desprendimiento de grano, siendo el más perjudicial para el proceso el desgaste de grano plano, debido a las altas temperaturas que genera en el contacto.
En definitiva, este trabajo boga por el conocimiento del proceso y la reducción de sus limitaciones pretendiendo dar un paso más en el conocimiento del comportamiento de estos procesos mostrando la caracterización de los desgastes de las herramientas rotativas superabrasivas. Cabe destacar, que la problemática que aquí se aborda es de gran interés para empresas rectificadoras, quienes presentan gastos del orden del 25% únicamente debido al consumo de diamantadores y muelas abrasivas.
La UPV/EHU forma parte del Digital Grinding Innovation Hub
Este próximo mayo hará 2 años de la puesta en marcha del Digital Grinding Innovation Hub (DGIH), un nodo tecnológico ubicado en las instalaciones de Ideko con el fin de desarrollar soluciones de gran exigencia tecnológica e innovadora para problemas de digitalización y rectificado industriales. Es decir, es un centro que está trabajando en niveles de madurez tecnológica altos (más conocidos por sus siglas en inglés TRL), englobando los TRLs 7-8-9. El DGIH es un espacio capaz de atraer y traccionar iniciativas de diferentes ámbitos, como son la investigación y el desarrollo, la experimentación, la divulgación, e incluso la capacitación y la formación. Además, el DGIH es una herramienta estratégica para el País Vasco en cuanto a la atracción de talento, lo que es relevante en los últimos años. Este nodo presenta un posicionamiento internacional de primer nivel en cuanto a infraestructuras y capacidades en el ámbito del rectificado, siendo una de las premisas priorizar la colaboración local sin perder de vista la proyección internacional tanto de empresas como de centros tecnológicos.
Como se observa en esta imagen, en el DGIH forman parte diferentes agentes tecnológicos, fabricantes de equipamiento y de componentes y centros de formación, de entre los cuales se encuentra la universidad del País Vasco, concretamente, dentro del departamento de Ingeniería Mecánica, el Grupo de Investigación de Procesos de Rectificado. A día de hoy existe una colaboración potente, realizando proyectos en común en los que forman parte alumnos de grado, de máster y del programa de doctorado de ingeniería mecánica. En este proyecto también participa personal investigador y profesorado de la universidad y personal de IDEKO. Uno de los principales objetivos de acercar el DGIH a la universidad es formar expertos en rectificado y digitalización para su incorporación al mundo laboral de una forma más competitiva. Además, desde el punto de vista industrial, supone un beneficio para las empresas, ya que disponen en el mercado de ingenieros con una mayor cualificación en estas áreas.
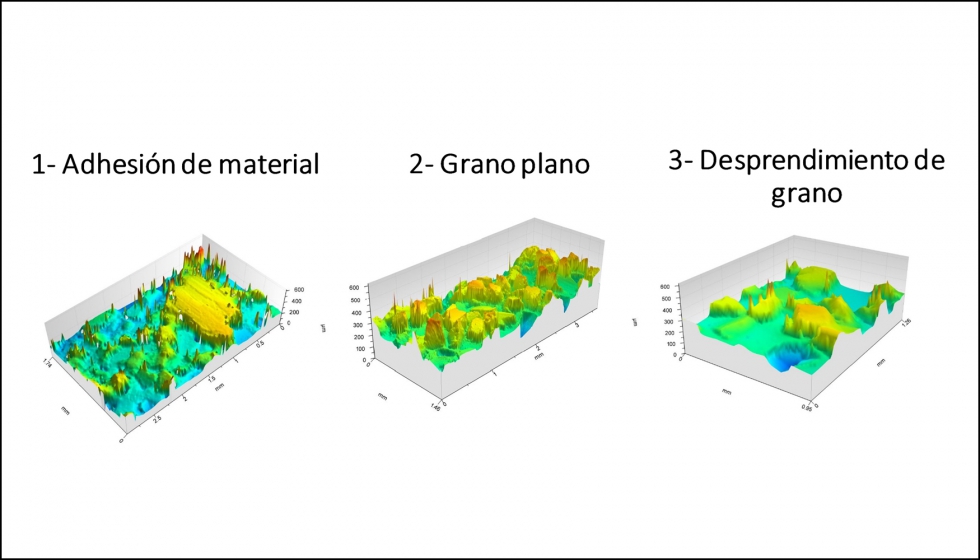
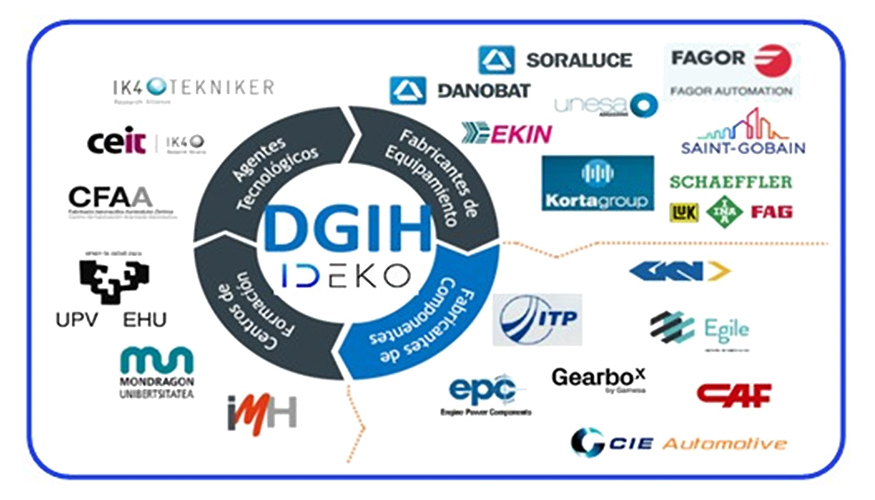
Referencias
[1] ‘Dr. Kaiser’. [Online]. Available: https://www.drkaiser.com/products/dressing-tools/profile-rollers.html.
[2] L. Godino, I. Pombo, J. A. Sanchez, I. Mendez, and X. Cearsolo, ‘Analysis of the dressing process using stationary dressing tools, ’ Procedia Manuf., vol. 13, pp. 146–152, 2017.
[3] L. Godino, J. Alvarez, A. Muñoz, and I. Pombo, ‘On the influence of rotary dresser geometry on wear evolution and grinding process, ’ Materials (Basel)., vol. 12, no. 23, 2019.
[4] González, H.; Pereira, O.; Fernández-Valdivielso, A.; López de Lacalle, L.N.; Calleja, A. ‘Comparison of Flank Super Abrasive Machining vs. Flank Milling on Inconel718 Surfaces’. Materials 2018, 11, 1638.
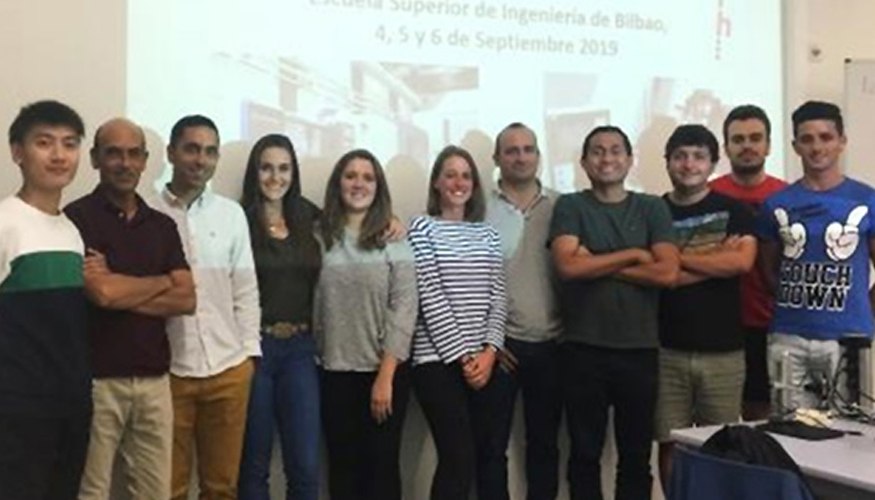