Pintado de plásticos en base acuosa
Antoni Porta Mateu
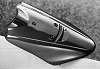
Antoni Porta Mateu es director de Cromaresme, S.L., firma suministradora de pinturas para plásticos.
1. Razones del pintado de plásticos
El pintado de plásticos se ha generalizado por diversas razones. Las más frecuentes son tres: protección, estética y motivos tecnológicos concretos.
1.1 Razones de protección:
Un porcentaje muy elevado de plásticos no resisten la radiación ultravioleta. La radiación ultravioleta afecta a la superficie del plástico, rompiendo las macromóleculas y formando microfisuras que, ayudadas por los cambios de temperatura y la humedad ambiente, acaban por degradar el plástico con la consiguiente pérdidas de propiedades mecánicas y otras. Se precisa, pues:
- Protección frente a las acciones mecánicas, aumentando la resistencia a la abrasión y al rayado.
- Protección ante medios agresivos como agentes químicos, disolventes, detergentes, grasas y otros.
- Protección contra la migración de ciertos plastificantes a la superficie.
1.2 Razones estéticas
A fin de ocultar defectos producidos por la transformación, tales como las líneas de flujo en piezas inyectadas, poros o desperfectos.
- Conferir a la superficie más lisura o distinto tacto
- Igualar tonos y brillo entre distintas piezas cuando no existe la posibilidad de conseguirlo directamente en la masa del plástico
- Conseguir aspectos especiales como metalizados, texturados, soft u otros
1.3 Razones tecnológicas
Conferir características antiestáticas, aumentar la conductividad eléctrica, aislar componentes electrónicos, aumentar las características mecánicas o la resistencia al caminamiento.
Descritas las razones por las que se pintan los plásticos, se presentan a continuación las motivaciones que han llevado a la industria de recubrimientos orgánicos a desarrollar las pinturas en base acuosa.
2. Problemas de los disolventes en el medio ambiente
La mayor parte de las pinturas empleadas en el pintado de plásticos son todavía en base disolvente. Si consideramos el extracto seco que presentan estas pinturas, veremos que su valor medio es de un 25-30% en peso. Esto significa que, por cada tonelada de pintura aplicada, se emiten a la atmósfera alrededor de 700-750 kg de disolventes.
![]() |
La parte hidrófoba forma un núcleo (core), y la parte hidrófila forma la envoltura (shell) de cada una de las gotas de emulsión
Los disolventes de las pinturas pertenecen al grupo más general de compuestos orgánicos volátiles y se conocen, generalmente, por las iniciales VOC (del inglés Volatile Organic Compounds).
Los efectos que producen los VOC en el medio ambiente son varios, y todos ellos perjudiciales. Los mecanismos perjudiciales básicos son cuatro:
- La destrucción de la capa estratosférica de ozono.
- El efecto invernadero, con el consiguiente aumento de la temperatura global.
- La lluvia ácida
- La formación de ozono en la troposfera.
Los disolventes participan plenamente en los puntos 1 y 4, e indirectamente en el 2 (tabla I). Para paliar estos efectos, los países mas adelantados en la protección medioambiental han legislado normativas restrictivas al uso de los disolventes, reduciendo las cantidades permitidas de emisión o las que intervienen en la pintura. La directiva europea sobre los VOC afectará a todos los integrantes de la Unión Europea.
3. Directiva europea sobre los VOC.
La directiva define al disolvente como cualquier compuesto orgánico que tiene una presión de vapor de 0.01 KPa o mayor a 293K, y separa a los disolventes del resto de VOC, tales como combustibles y otros compuestos, los cuales a su vez son objeto de otras acciones de la directiva.
En la directiva se definen 10 anexos (tabla II) en los que se trata de manera individual cada sector. El que afecta al pintado de plásticos (pintura industrial en general) es el anexo VII. En los parámetros propuestos, se establecen dos niveles en función del consumo de disolvente anual, y se limita la emisión por chimenea a un valor máximo, expresado en miligramos de carbono por metro cúbico de aire, al tiempo que obliga a llevar un Plan de Gestión de Disolventes (tabla III). En este plan se cuantifican las entradas de disolventes comprados o recuperados, y las salidas como disolventes emitidos. La diferencia entre ambos valores es considerada emisión fugitiva (disolventes perdidos en emisiones al aire no capturadas).
![]() |
A la vista de todo lo anterior está claro que se impone un cambio de tecnología. Al aplicador de pinturas se le presentan dos alternativas: invertir en una instalación que elimine las emisiones de disolventes evaporados en el proceso de secado, mediante varias técnicas como la condensación, absorción y posterior incineración; o bien cambiar el actual sistema de pinturas en base disolvente a un sistema en el que se cumpla la normativa. Los sistemas alternativos actuales son tres:
- Sistemas de alto contenido en solidos.
- Sistemas de curado por ultravioleta
- Sistemas en base acuosa.
El aplicador de pinturas deberá escoger la opción que mejor se adapte a su proceso.
4. Tecnología de las pinturas en base acuosa para plásticos
Los tipos de polímeros utilizados usados en las pinturas en base agua, atendiendo a su naturaleza química, son prácticamente los mismos que se utilizan en base disolvente:
- Acrílicas.
- Acrílicas modificadas o en combinación con otros polímeros.
- Poliuretanos en dispersión.
- Ésteres de epoxi.
- Acrílicas hidroxiladas con isocianatos emulsionables.
- Poliésteres hidroxilados con isocianatos emulsionables.
- Alquídicas modificadas.
La presentación física de estos polímeros es en forma de dispersiones-emulsiones y dispersiones coloidales (existe un grupo de polímeros que se presenta en forma de soluciones, pero prácticamente no se utilizan en el pintado de plásticos).
4.1 Dispersiones o emulsiones:
Se obtienen polimerizando monómeros hidrófobos, en medio acuoso, en presencia de un agente emulsionante, que mantiene en equilibrio a los agregados moleculares hidratados resultantes. La polimerización se activa mediante catalizadores solubles en agua. El tamaño de las partículas de la dispersión oscila alrededor de 0.5-1 m. La viscosidad es independiente del peso molecular, lo que tiene gran importancia puesto que permite obtener pesos moleculares altos sin problemas de viscosidad. Contienen pequeñas cantidades de disolventes como coalescentes.
La última aportación técnica a este tipo de resinas son las llamadas autoemulsionantes core-shell (figura 1), que se componen de una parte de resina hidrófoba y segmentos de polímeros hidrófilos injertados. En el proceso de emulsión, la parte hidrófoba forma un núcleo (core), y la parte hidrófila forma la envoltura (shell) de cada una de las gotitas de la emulsión.
![]() |
Las ventajas de este tipo de resinas respecto a las convencionales reside en la ausencia de emulsionantes externos, lo que mejora la resistencia a las fuerzas de cizalladuras en la fabricación de la pintura, la reducción de la cantidad de coalescentes y la resistencia al agua de la película de pintura seca.
4.2 Dispersiones coloidales
Se forman por copolimerización de monómeros funcionales que contienen grupos carboxilo, que solubilizan mediante una neutralización con aminas o amoníaco, dentro de un campo de pH alcalino (8-9). Este proceso da nombre a este tipo de polímeros como álcali-solubles. La viscosidad depende del peso molecular y del contenido en sólidos. El tamaño de las partículas es menor que 0.1 m. Contienen también una pequeña cantidad de disolventes como coalescentes.
4.3 Proceso álcali-soluble
Se trata (figura 2) de un sistema reactivo de poliuretano de dos componentes. Es la tecnología en base agua más reciente de todas, y su origen está en los trabajos de investigación sobre los poliisocianatos emulsionables realizados por la firma Bayer.
Los sistemas de poliuretano dos componentes, tanto los acrílico/isocianato como los poliéster/isocianato en base disolvente, son los más utilizados en el pintado de plásticos cuando se desea un acabado de la máxima calidad y resistencia al exterior. La capacidad de reacción de los poliisocianatos en el agua parecía limitar este sistema sólo a los productos en base disolvente pero, a pesar de esta aparente limitación, se ha conseguido un sistema similar soluble en agua.
El sistema poliuretano en base acuosa se basa en un componente polihidroxilado en dispersión, con el tamaño de partícula lo más pequeño posible y con propiedades emulsionantes del poliisocianato. El poliisocianato es alifático de baja viscosidad al 100% de sólidos, para facilitar su emulsión en el componente polihidroxilado y no incorporar disolventes a la mezcla. Las moléculas de polímero se sitúan rodeando las gotitas de poliisocianato tal como lo harían las moléculas de un emulsionante. Al empezar la reacción, los grupos NCO del isocianato reaccionan a la vez con los grupos OH del poliol y con el agua, por lo que se obtienen, además de la estructura del poliuretano, compuestos de poliurea.
Su aplicación se realiza mediante pistola convencional, y la mezcla de los dos componentes debe realizarse con un agitador, a fin de lograr la máxima emulsión de la misma. Las propiedades del sistema son similares a los basados en disolvente y el tipo de pinturas el mismo.
Los tipos de secado de las pinturas hidrosolubles, son los mismos que las pinturas en base disolvente:
- Físico, por evaporación del agua y sin modificación química del ligante
- Oxidación: se realiza una reacción del ligante con el oxígeno del aire, produciéndose una modificación química del mismo
- Polimerización, se realiza una reacción química entre dos compuestos, que se presentan mezclados en la misma pintura (los de secado al horno) o en envases separados que se mezclan antes de su aplicación.
5. Características de las pinturas en dispersión para plásticos
Al compararlas con las clásicas en disolvente, las resinas en dispersión tienen unas características diferentes a las pinturas convencionales que conviene explicar, y que son dependientes de la temperatura de formación de película MFT y del fenómeno de la coalescencia.
Para que una pintura en dispersión forme una película uniforme y sin defectos es necesario que las partículas se unan sin dejar espacios entre si: a este efecto se le denomina coalescencia. Para que ésta tenga lugar se requiere un equilibrio entre diversos factores opuestos entre si:
- Factores favorables: temperatura elevada, elevada energía superficial de contacto, adición de plastificantes, adición de disolventes coalescentes y pequeño tamaño de la partícula.
- Factores desfavorables: elevado módulo elástico del polímero y Tg del polímero elevada.
La Tg (temperatura de transición vítrea) del polímero es la que determina la temperatura de formación de la película (MFT), y a la vez determinará las características finales del recubrimiento en cuanto a dureza, resistencia al rayado, etc.
En la practica, la adición de coalescentes reduce la MFT. El coalescente reduce la Tg del polímero para que éste forme correctamente el film. Después de la evaporación del agua, el coalescente también se evapora, el Tg vuelve a su valor original y mejoran las características físicas de la pintura. Si se efectúa un secado forzado a temperatura (60-90C ) no es necesaria la adición de coalescentes.
Debido a la adición de coalescentes se produce un retraso en el alcance de las condiciones óptimas de la pintura pues, en muchos casos, el coalescente es retenido en el interior de la pintura y tarda un tiempo en evaporarse totalmente. Este retraso se puede paliar en parte, según el tipo de coalescentes escogidos o efectuando un secado forzado.
Otra característica diferente en comparación con las pinturas al disolvente es su viscosidad estructural (figura 3). Las pinturas al disolvente para el pintado de plásticos tienen una viscosidad de tipo newtoniano o seudoplástico. El sistema habitual de controlar la viscosidad es mediante copa Ford o DIN. En las pinturas hidrosolubles, debido a su viscosidad estructural, este tipo de viscosímetros no son adecuados para la mayoría de formulaciones, por lo que es necesario emplear viscosímetros dinámicos. También debe controlarse el pH de la pintura debido a su influencia sobre la viscosidad.
![]() |
Una tercera característica distinta respecto a las de base disolvente es la gran influencia, en su aplicación y secado, de la temperatura y la humedad relativa del aire. Al utilizar agua como disolvente, no se dispone del recurso a la modificación de las características de evaporación mediante mezclas de disolventes, por lo que la saturación de vapor de agua existente en el ambiente influirá en la velocidad de evaporación del agua de la pintura. Las condiciones normales de aplicación de las pinturas al agua se encuentran entre el 50 al 70% de humedad relativa y una temperatura de 18 a 28C. En el pintado industrial de plásticos se recomienda el secado forzado a 50-90C, según el tipo de plástico.
Una característica muy apreciada es la no agresión a los plásticos debido a la baja cantidad de disolventes (los coalescentes pueden representar como máximo un 5% sobre el total de la pintura). Un problema que se presenta en las pinturas hidrosolubles es su dificultad para humectar bien los sustratos.
La tensión superficial del agua es muy alta, del orden de 70 mN/m, lo que dificulta la mojabilidad de los soportes. El problema se soluciona mediante aditivos que rebajen la tensión superficial de la pintura, y cuidando la limpieza de las superficies de plástico. Otro problema característico de las pinturas en base agua es su facilidad para producir espuma, lo que obliga a la utilización de antiespumantes en su formulación.
6. Tipos de pinturas en base acuosa para el pintado de plásticos
6.1 Sistemas monocapa
Son sistemas de adherencia directa sobre el plástico, sin necesidad de imprimación de anclaje. Pueden ser monocomponentes o bicomponentes. Colores opacos o metalizados con distintos brillos según el tipo de resina escogido. En los monocomponentes los brillos no son muy elevados (máximo 80% a 60C). Para conseguir brillos altos similares a los de base disolvente se deben utilizar los poliuretanos bicomponentes.
6.2 Sistemas bicapa
El sistema se compone de un fondo opaco o metalizado y un barniz de acabado transparente aplicado encima del fondo. En el pintado actual de estos sistemas se dan dos casos:
- Fondo opaco o metalizado en base acuosa + barniz poliuretano 2 componentes en base disolvente, o
- Fondo opaco o metalizado en base agua + barniz poliuretano 2 componentes en base agua.
Este último sistema es el más reciente, y su resistencia al exterior aún está en observación (Florida), si bien tanto por su naturaleza química, como por los resultados obtenidos en los ensayos de envejecimiento acelerado, cabe pensar que no deben tener ningún problema. En la aplicación de los sistemas bicapa es necesario que al aplicar el barniz de acabado (tanto si es al agua como si es al disolvente) el agua del fondo se haya evaporado completamente. Ello obliga a estufar previamente el fondo a 80C durante 3 a 5 minutos. El sistema bicapa puede ser de adherencia directa sobre el plástico o requerir una imprimación de anclaje según el tipo de plástico de que se trate.
6.3 Imprimaciones
- Selladoras: Se utilizan normalmente para sellar o tapar defectos superficiales de los plásticos.
- Conductoras: Su función es convertir en conductora la pieza de plástico para su pintado posterior por sistema electrostático.
Pueden ser mononcomponentes y bicomponentes.
6.4 Barnices
Los barnices hidrosolubles monocomponentes se utilizan para la protección de ciertos plásticos o para proporcionar aspectos estéticos concretos; en general, su brillo no es tan elevado como los barnices en base disolvente. En el caso de los bicomponentes, el brillo es similar a los que se consiguen con los barnices en base disolvente.
6.5 Acabados hidrosolubles con efectos especiales:
- Acabados con efectos textiles, soft, texturados y otros.
- Monocomponentes y bicomponentes.
7. Tipos de plásticos que se pueden pintar en base acuosa
Los principales tipos de plásticos que se pintan en base disolvente pueden ser pintados en base acuosa: ABS, PS, PC, PMMA, PVCr, PVCf, PURr, PURf, PA, PP/EPDM, SMC.
![]() |
El PP es un de los plásticos de uso corriente en la industria que presenta más dificultades para ser pintado con pinturas acuosas. Si se trata su superficie hay sistemas con buena adherencia, y se está trabajando para conseguir promotores de adherencia emulsionados en agua.
8. Instalaciones para la aplicación de las pinturas en base acuosa
Las características principales a tener en cuenta en las instalaciones de aplicación de pinturas al agua son:
- Adecuar la cabina de aplicación al intervalo de temperatura y humedad relativa óptimo
- Un secado forzado para evaporar el agua
- Los conductos y calderines deben ser de acero inoxidable o plástico
- Las bombas no deben ser de discos o engranajes o cualquier otro sistema que produzca fuerzas de cizallamiento elevadas
9. Conclusión
La tecnología del pintado en base acuosa es una de las que se está desarrollando más rápidamente debido a sus características de respeto por el medio ambiente. Los problemas que presenta se están solucionando paulatinamente.
Emisiones de VOC en Europa, 1985
Procedencia | Cantidad
(MT/año) |
% |
Emisiones de disolventes | 3,4 | 34% |
Emisiones del transporte | 5,3 | 53% |
Emisiones de refinerías | 0,2 | 2% |
Emisiones de procesos industriales | 0,5 | 5% |
Otras fuentes de emisión | 0,6 | 6% |
Total VOC | 10 | 100 |
Tabla I.- Emisión de compuestos orgánicos volátiles en Europa, por procedencia. Fuente: Corinair
Parámetros de la directiva europea sobre VOC (1)
Anexo VII
Aplicación de pinturas |
Primer nivel |
Segundo nivel |
Consumo anual | > 2 T/año; < 25 T/año | > 25 T/año |
Capacidad nominal | > 2 kg/hora; < 25 kg/hora | > 25 kg/hora |
Plan de gestión | Tipo A | Tipo A (5 años);
después Tipo B |
Límites de emisión | 150 mg C/m3 | Secado: 50 mg C/m3
Aplicación: 100 mg C/m3 |
Emisiones fugitivas | < 25% | < 25% |
Derogación instalaciones existentes | 7 años | 5 años |
Condiciones de exención | Plan de reducción
de emisiones |
Plan de reducción
de emisiones |
Tabla II.- Parámetros de la directiva europea sobre VOC.
Parámetros de la directiva europea sobre VOC (y 2)
Tiempo (años) desde que la directiva entre en vigor | Tiempo (años) desde que la directiva entre en vigor | % tolerado sobre las emisiones controladas y fugitivas que se permitirán como máximo para las industrias que no presenten plan de reducción. El % se calculará en las T/año de la tabla II. |
Medianas/grandes | Medianas/grandes | |
3 (5*) / 2 (4*)
10 (12*) / 8 (10*) 14 (16*) / 12 (14*) |
8 (12)* / 7 (9*)
12 (14*) / 10 (12*) 14 (16*) / 12 (14*) |
150%
100% 75% |
Tabla III.- Tiempo de adaptación según la directiva europea sobre VOC. (*): Para procesos que usen recubrimientos que deben que cumplir con las condiciones de contacto con alimentos.
SUMINISTRADORES DE QUIPOS E INSTALACIONES PARA PINTURAS AL AGUA
FIRMA | Equipos | Instalaciones |
Air Industrie Systèmes | X | |
Aire y Construcción | X | |
Böllhof | X | |
DeVilbiss Ransburg | X | |
Geinsa | X | |
Graco | X | |
Haden Drysys | X | |
Nordson | X | |
Rexson | X | |
Sames | X | |
SKM Kremlin | X | |
Spray | X | |
System Car | X | |
TSA | X | |
Vizdür/Behr | X |