Afronte los retos de la automatización industrial con una nueva generación de controladores lógicos programables (PLC)
Rolf Horn, Applications Engineer at DigiKey
09/05/2024Aunque las tecnologías adecuadas basadas en estándares constituyen la espina dorsal de la fábrica conectada, el hardware y el software de muchos controladores lógicos programables (PLC) heredados o “caballos de batalla” tienen capacidades limitadas. Esto hace que sea difícil para los ingenieros implementar rápidamente las actualizaciones en toda la fábrica que se necesitan para aprovechar al máximo la IIoT. Para complicar aún más las cosas, los ingenieros corren el riesgo de basar las costosas actualizaciones de fábrica en una tecnología que podría quedar obsoleta o sin soporte a medida que se introduzcan nuevas tecnologías.
Se pueden aprender lecciones de otras partes del IoT, como el hogar inteligente, donde los sistemas abiertos, las plataformas colaborativas y el software accesible facilitan la implantación de soluciones inteligentes preparadas para el futuro. Los fabricantes de automatización industrial están aprovechando esta experiencia y conocimientos.
En este artículo se analiza brevemente el reto de implantar la tecnología IIoT y se explica cómo los avances en sistemas abiertos y hardware de automatización de fábricas ofrecen soluciones. El artículo presenta un ejemplo de implementación de hardware y software de controladores lógicos programables de última generación de Phoenix Contact y muestra cómo simplifica la recopilación de datos y su envío a la nube para el análisis y la toma de decisiones automatizada.
La importancia de los controladores lógicos programables (PLC)
El pilar de la fábrica es el PLC, un dispositivo digital inventado a finales de los años 60 para sustituir a los anteriores sistemas lógicos de relés. Los PLC están diseñados para trabajar en entornos difíciles sin fallos durante muchos años. La clave de esta fiabilidad es la simplicidad. En el raro caso de que algo falle, los PLC están diseñados para detectar y solucionar problemas, de modo que la producción en serie pueda reanudarse rápidamente.
Las unidades constan de un módulo de entrada (que recibe datos de dispositivos de entrada digitales y analógicos, como teclados, interruptores, relés y sensores), una fuente de alimentación, una CPU programable con memoria asociada y un módulo de salida para enviar información a los dispositivos conectados (Figura 1).
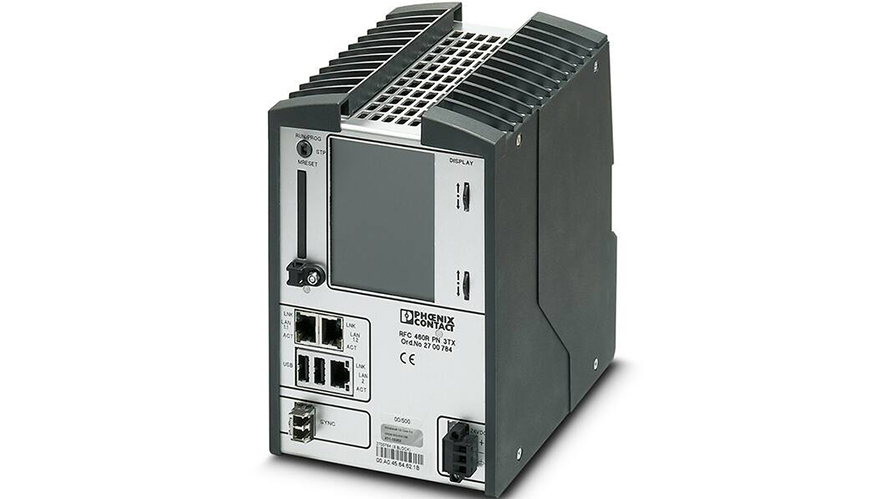
Figura 1: Los PLC resistentes y fiables son la columna vertebral de la automatización industrial. (Fuente de la imagen: Phoenix Contact).
Los PLC convencionales se programan utilizando uno de los cinco lenguajes definidos por la norma IEC 61131-3. Se trata de la lista de instrucciones (IL), el diagrama de flujo simbólico (SFC), el diagrama de escalera (LD), el diagrama de bloques de funciones (FBD) y el texto estructurado (ST). El más popular es el LD, o lógica de escalera, que utiliza símbolos para representar funciones como relés, registros de desplazamiento, contadores, temporizadores y operaciones matemáticas. Los símbolos se disponen según la secuencia de acontecimientos deseada.
Los fabricantes de controladores lógicos programables (PLC) se están adaptando rápidamente a los avances en automatización de fábricas que ha supuesto la implantación de Ethernet Industrial. Ethernet Industrial es interoperable con IP, es la opción de cableado más utilizada y cuenta con un amplio respaldo de los proveedores. Ethernet Industrial se caracteriza por un hardware resistente y un software estándar industrial, y es una tecnología probada y madura para la automatización de fábricas (Figura 2). El hardware se complementa con protocolos de Ethernet Industrial, incluidos Ethernet/IP, Modbus TCP y PROFINET. Cada uno de ellos está diseñado para garantizar un alto nivel de determinismo en las aplicaciones de automatización industrial.
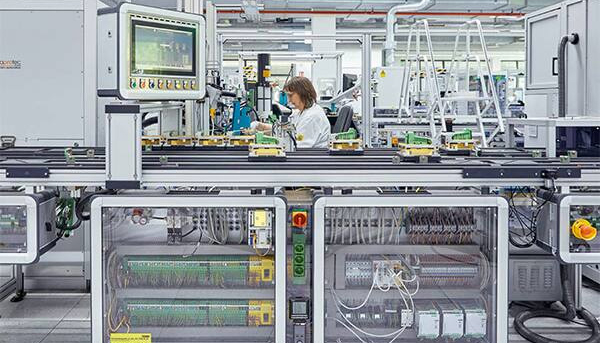
Muchos de los PLC actuales ofrecen conectividad Ethernet integrada. En el caso de los dispositivos heredados con interfaces no Ethernet, la división entre la infraestructura Ethernet y los controladores lógicos programables (PLC) se puentea mediante puertas de enlace.
La próxima generación de PLC
Una fábrica que utiliza una mezcla de sistemas modernos y heredados puede dificultar que los ingenieros aprovechen todas las ventajas que promete la Industria 4.0. Sin embargo, las lecciones aprendidas de otras partes del IoT, como los sectores del hogar inteligente y la logística, revelan que los sistemas abiertos, las plataformas colaborativas y el software accesible basado en estándares facilitan la implementación de soluciones inteligentes preparadas para el futuro.
Los conocimientos adquiridos en estos otros sectores animan a los fabricantes de PLC y sistemas asociados a introducir una nueva generación de productos que funcionan como los PLC tradicionales sin verse restringidos por las limitaciones del hardware y el software heredados. Un ejemplo de esta nueva generación es la tecnología PLCnext Control de Phoenix Contact.
Desde el punto de vista del software, un producto como el controlador PLCnext de Phoenix Contact representa un avance significativo hacia las soluciones abiertas que están empezando a dominar otras áreas del IoT. Por ejemplo, PLCnext es compatible con un amplio rango de software, por lo que las innovadoras aplicaciones de automatización de fábricas pueden descargarse fácilmente de Internet e instalarse en el PLC, como las aplicaciones de un smartphone.
PLCnext utiliza el sistema operativo (SO) Linux. Se puede seguir programando con los lenguajes definidos en la norma IEC 61131-3, pero Linux facilita a los ingenieros la programación de los controladores lógicos programables (PLC) con los lenguajes de alto nivel C++, C#, Java, Python y Simulink. Estos lenguajes de uso sencillo ponen la automatización moderna de fábricas al alcance de un grupo mucho más amplio de ingenieros. Además, PLCnext cuenta con un manejo de tareas que permite ejecutar rutinas de programación de distintas fuentes como código PLC heredado, con lo que los programas en lenguaje de alto nivel se convierten automáticamente en deterministas (Figura 3).
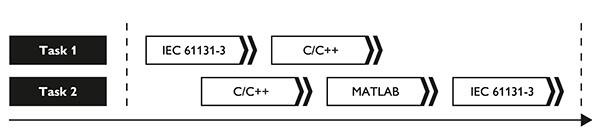
La conectividad se realiza a través de hardware Ethernet industrial; el sistema de control se ejecuta bajo el protocolo PROFINET interoperable por IP y utiliza la plataforma IoT PROFICLOUD como soporte de computación en la nube. El PLC también admite otros protocolos de estándar abierto como http, https, FTP, SNTP, SNMP, SMTP, SQL, MySQL y DCP.
El hardware se basa en un microprocesador Intel Atom que funciona a 1.3 gigahercios (GHz). Los controladores lógicos programables (PLC) disponen de 1 gigabyte (Gbyte) de memoria Flash y 2048 megabytes (Mbytes) de RAM. El sistema de tiempo de ejecución IEC 61131 tiene 12 Mbytes de memoria de programa y 32 Mbytes de almacenamiento de datos de programa. La unidad admite hasta 63 dispositivos de bus local y requiere una alimentación de 24 voltios con un consumo máximo de corriente de 504 miliamperios (mA) (Figura 4).
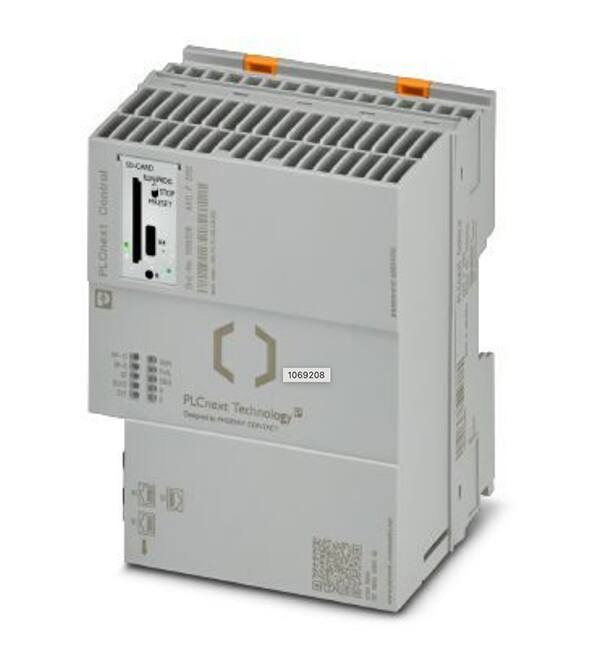
La gama PLCnext de Phoenix Contact incluye PLC y otros elementos críticos de un sistema de automatización industrial, como módulos de comunicaciones e interruptores gestionados. Algunos ejemplos concretos son el módulo de comunicaciones y el interruptor de traducción de direcciones de red (NAT) gestionado. El módulo de comunicaciones añade al PLC una interfaz Ethernet industrial adicional con capacidad para gigabits. El módulo tiene una dirección MAC independiente, ofrece compatibilidad con PROFINET e incluye aislamiento eléctrico entre la interfaz Ethernet y la lógica.
El interruptor gestionado se utiliza para almacenar y reenviar información transportada por Ethernet y cuenta con cuatro puertos Ethernet RJ45, dos puertos de factor de forma pequeño enchufable (SFP) y dos puertos combinados (RJ45/SFP). El interruptor es un producto PROFINET Conformance Class B.
Mejorar la toma de decisiones en la fábrica
La optimización de la producción en fábrica es esencial porque la fabricación exige precisión y repetibilidad. La clave para garantizar altos niveles de precisión y repetibilidad es el control del proceso. En la fábrica moderna, los sensores y cámaras IIoT pueden supervisar las máquinas y medir los componentes acabados para captar cualquier pequeña desviación en el producto y corregir el proceso en consecuencia. Otros sensores realizan un seguimiento del estado de las máquinas para predecir las necesidades de mantenimiento antes de que una máquina desgastada empiece a fallar. Hay aún más sensores que controlan la temperatura, la humedad y la calidad del aire de la fábrica.
Una característica clave de PLCnext Control es que, a diferencia de los PLC tradicionales, puede acceder a estos datos de fábrica. Según Phoenix Contact, basta con conectar el autómata programable a tan solo entre el 3% y el 5% de las entradas y salidas (E/S) analógicas y digitales del sistema para que éste sea capaz de cartografiar los procesos de fabricación de forma exhaustiva y sin intervenciones significativas.
A continuación, PLCnext Control puede conectarse a cualquier servicio en la nube, incluidos Proficloud.io de Phoenix Contact, AWS de Amazon o Azure de Microsoft. Como resultado, el sistema de la fábrica gana acceso a potentes recursos informáticos para garantizar que los procesos de gestión de operaciones y mantenimiento se desarrollen con la mayor eficacia posible. El resultado es mayor productividad, mejor calidad del producto y menores costos.
Introducción a PLCnext
Trabajar con controladores PLCnext y unidades relacionadas es relativamente sencillo. Para ayudar a iniciar un proyecto de programación de controladores lógicos programables (PLC), Phoenix Contact ha presentado el kit inicial PLCnext Technology. El kit incluye un módulo de controladores lógicos programables (PLC), un portamódulos y módulos analógicos o digitales a elegir.
Para utilizar el kit de arranque, primero hay que conectar los controladores lógicos programables (PLC) y las unidades de módulos analógicos/digitales a la alimentación de 24 voltios CC (VCC). A continuación, se conecta un cable Ethernet entre el PLC y el PC y se configura la dirección IP del PC. A continuación, se ingresa la dirección IP de los controladores lógicos programables (PLC) en una ventana del navegador del PC. Los controladores lógicos programables (PLC) entran en funcionamiento después de que los usuarios inicien sesión con su nombre de usuario y contraseña. El sistema de gestión por Internet proporciona más instrucciones. La programación de los controladores lógicos programables (PLC) se realiza mediante el software PLCnext Engineer. El software permite a un ingeniero configurar, diagnosticar y visualizar una solución de automatización completa.
PLCnext Engineer permite la programación y configuración utilizando los lenguajes heredados definidos en la norma IEC 61131-3. También es sencillo programar en lenguajes de alto nivel como C++ y C#. Además de PLCnext Engineer, el código se puede crear en otros entornos completos de desarrollo integrado (IDE) conocidos, como Eclipse o Microsoft Visual Studio. A continuación, el software puede importarse a PLCnext Engineer como biblioteca para su uso con cualquier controlador lógico programable (PLC) compatible (Figura 5).
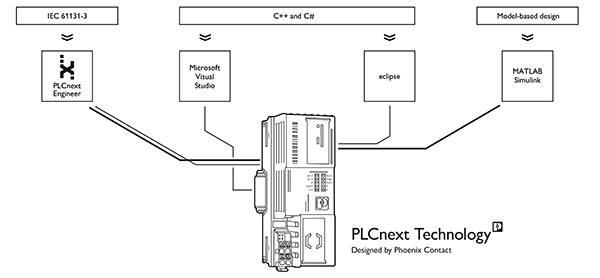
Una ventaja clave de la tecnología PLCnext es que permite que varios desarrolladores trabajen de forma independiente y en paralelo en un mismo programa de controladores lógicos programables (PLC), aunque utilicen lenguajes de programación distintos. Esto permite un desarrollo rápido de aplicaciones complejas y que los desarrolladores con conocimientos de lenguajes heredados y aquellos con conocimientos de lenguajes de alto nivel combinen sus talentos.
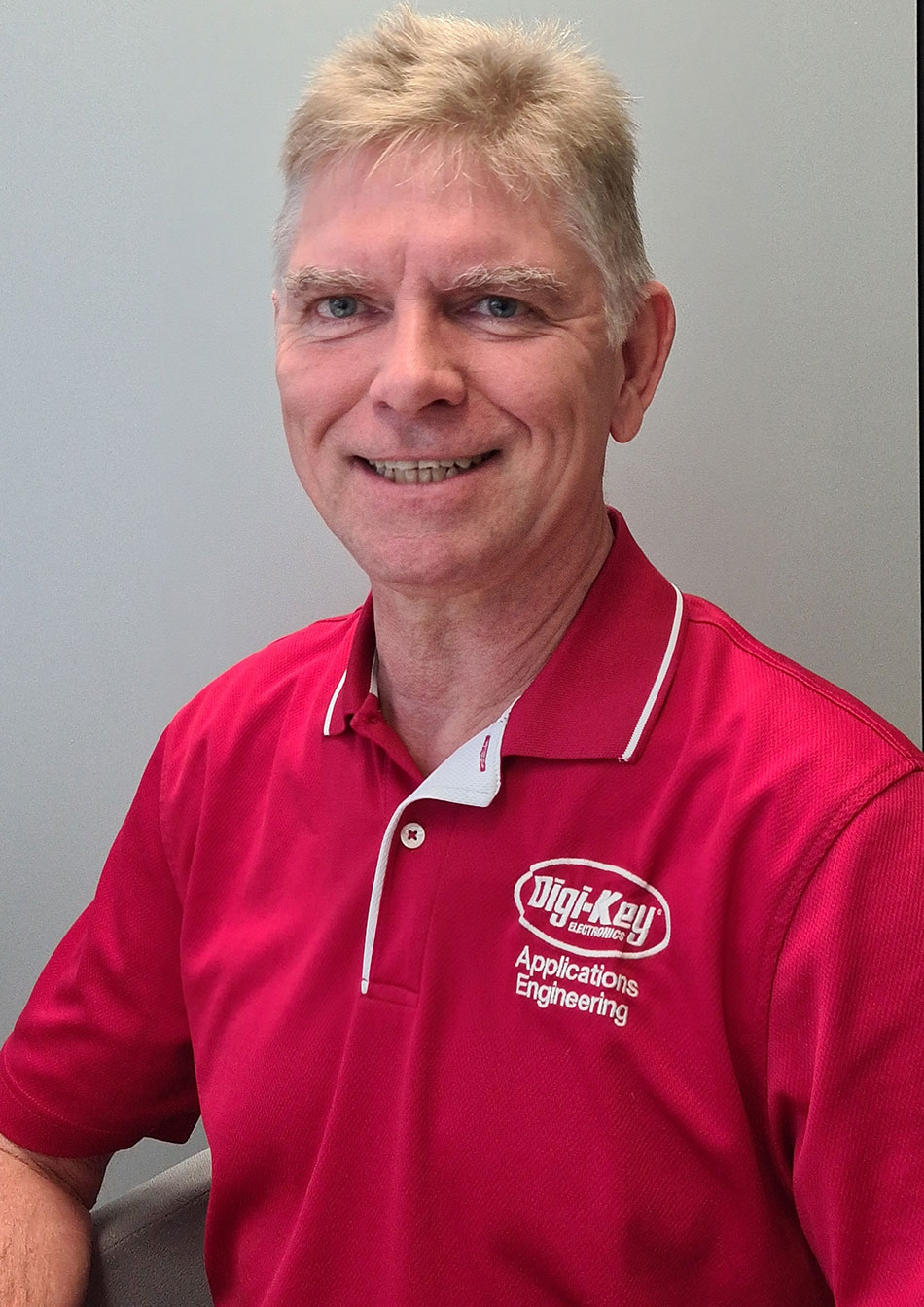
Rolf Horn, Applications Engineer at DigiKey.
Conclusión
La IIoT promete transformar la fábrica. Sin embargo, mientras los ingenieros instalan Ethernet industrial, el pleno potencial de la automatización de las fábricas se ve frenado por los PLC tradicionales, que ofrecen una conectividad limitada y un software anticuado. La tecnología PLCnext de Phoenix Contact se basa en sistemas abiertos, plataformas de colaboración y software accesible. Puede combinar rutinas codificadas en lenguajes heredados con otras escritas en lenguajes de alto nivel para abrir la automatización industrial a soluciones preparadas para el futuro con mayor productividad, mayor rendimiento, mejor calidad del producto y menores costos.