Fabricación aditiva y nuevos procesos de producción
La fabricación aditiva ha experimentado un rápido crecimiento en los últimos años y el futuro parece prometedor: los expertos prevén un nuevo crecimiento de alrededor del 20% en los próximos cuatro años. Las industrias metalúrgicas también se beneficiarán de ello. Las acerías y fundiciones, los fabricantes de plantas metalúrgicas y los proveedores están utilizando la impresión 3D y los nuevos procesos de fabricación para una amplia variedad de modelos de negocio, como se verá en las ferias Metec, Gifa y Newcast en el ‘Bright World of Metals’ de Düsseldorf del 12 al 16 de junio de 2023.
La fabricación aditiva, con su variada oferta de procesos generativos, ofrece a las fundiciones y empresas siderúrgicas un amplio abanico de oportunidades. Mientras que para los fabricantes de acero la impresión 3D directa de metales es principalmente un complemento del negocio existente y un pilar cada vez más importante en la reparación y adquisición de piezas de repuesto, los procesos aditivos indirectos, en particular la impresión 3D de moldes, núcleos y modelos con arena, son opciones destacadas para las fundiciones.
“La fabricación aditiva se utiliza desde hace tiempo para algo más que la creación de prototipos”, afirma Markus Heering, director general del Grupo de Trabajo de Fabricación Aditiva (AG AM) de la VDMA, fundado el año pasado. En la industria de la ingeniería mecánica, la fabricación aditiva es un proceso de fabricación complementario que permite el desarrollo y la innovación, abriendo nuevas aplicaciones”. El experto en ingeniería mecánica subraya explícitamente el potencial de los procesos generativos para la industria.
Empresas siderúrgicas y fabricantes de instalaciones: negocio adicional con componentes y polvos metálicos
Las empresas siderúrgicas y los fabricantes de plantas pueden beneficiarse en muchos aspectos de los procesos de fabricación aditiva.
El grupo SMS, con sede en Düsseldorf, es una de las pocas empresas del mundo que abarca todo el proceso de fabricación aditiva. Ya en 2017, este fabricante de plantas metalúrgicas y sus socios comenzaron a desarrollar procesos relacionados a escala industrial para que la fabricación aditiva fuera competitiva también en la producción en serie. En el corazón de su Centro de Competencia de Fabricación Aditiva, controlado digitalmente, se encuentra un sistema de atomización de polvo metálico desarrollado por SMS con una capacidad de 4000 t al año, con clasificación y manipulación de polvo conectadas. El sistema de producción se completa con una gran impresora LPBF de 400 x 400 x 400 mm para la fabricación aditiva en metal, el postprocesado, el control de calidad y el envío de las piezas acabadas. Un joven equipo de investigación y desarrollo (I+D) diseña, fabrica y prueba piezas impresas en 3D, principalmente para los propios productos del grupo SMS.
Hans Ferkel, director de Tecnología del grupo SMS, aprecia las ventajas que ofrece la fabricación aditiva: poder fabricar componentes funcionalmente optimizados con la mayor libertad geométrica posible, lo que no sería factible con los procesos de fabricación clásicos. SMS utiliza la fabricación aditiva para fabricar, por ejemplo, componentes de planta producidos en serie. Un primer resultado fue un premiado cabezal de pulverización para prensas de forja, fabricado en plástico o metal. Este componente ligero y, por tanto, más rápido acorta significativamente el tiempo de producción durante la forja, aumentando así la eficiencia económica. El cabezal de pulverización impreso en 3D consta de una sola pieza en lugar de 16 y pesa sólo una décima parte que un cabezal de pulverización convencional, que pesa unos 80 kilos. Dispone de canales de flujo optimizado y enfría las matrices de forma selectiva y adaptada a cada caso. Al mismo tiempo, es más barato, más eficaz y puede fabricarse individualmente según las necesidades. El cabezal de pulverización impreso en 3D ya está siendo utilizado con éxito por clientes de la industria automovilística.
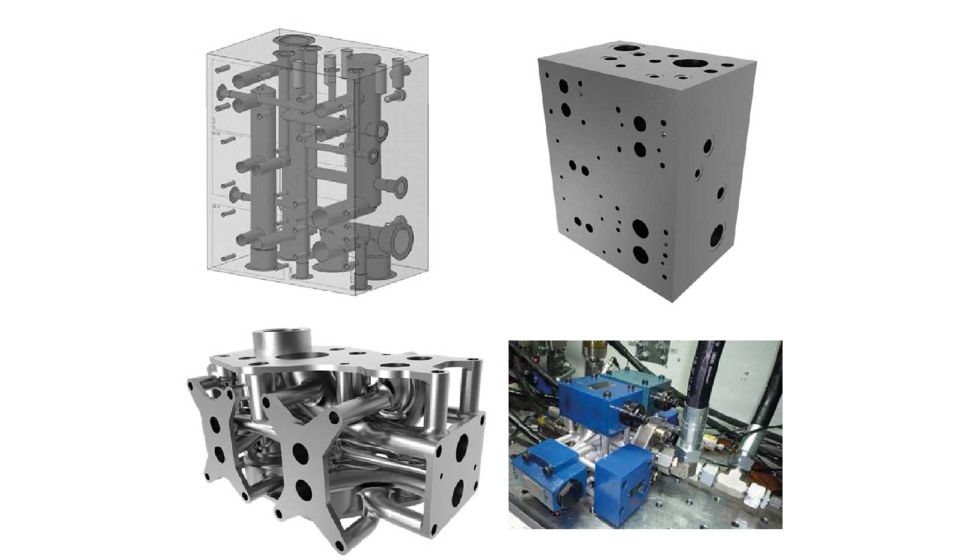
Como otro ejemplo de éxito, el jefe de investigación de SMS cita un diseño de flujo optimizado y un bloque hidráulico de fabricación aditiva para plantas metalúrgicas. Un bloque hidráulico convencional consiste en un bloque de acero con canales perforados a través de los cuales debe forzarse el aceite hidráulico utilizado para la transmisión de potencia. Los canales rectos perforados en el bloque siempre forman inevitablemente conexiones a tope. En términos de flujo, el curso angular es por tanto desfavorable. Un patrón de flujo calculado por ordenador se parece más a un tubo digestivo. Siguiendo el ejemplo de la naturaleza, se consiguió la menor pérdida de presión posible en el trayecto entre la entrada y la salida. Recién calculado y fabricado de forma aditiva, el bloque hidráulico consigue unas características de flujo óptimas. En comparación con su predecesor convencional, basta un compresor mucho más pequeño para generar la presión de funcionamiento necesaria en el sistema hidráulico, con lo que se consigue un importante ahorro de energía.
Empresas siderúrgicas
Cada vez son más las empresas siderúrgicas que utilizan toda la gama que ofrece la fabricación aditiva. En la austriaca Voestalpine, la actividad abarca desde el desarrollo de aleaciones y la producción de polvo metálico hasta el diseño, la fabricación y el acabado. Con la fabricación aditiva, la división de conformado de metales del grupo ofrece a sus clientes un complemento a su cartera tecnológica. Especialmente en el campo de la construcción ligera, esta deposición metálica por capas permite fabricar componentes con mayor libertad de diseño y mayor funcionalidad de forma rápida e, idealmente, rentable, como señala el grupo tecnológico.
El mayor grupo siderúrgico del mundo, ArcelorMittal, ya trabaja desde 2017 con Additive Industries, un fabricante especializado en la impresión de metales. Additive Industries se considera la empresa líder mundial en impresoras de metal escalables e integradas industrialmente. Mediante la impresión 3D de metales, ArcelorMittal produce bajo demanda piezas de repuesto listas para usar, incluidas piezas de repuesto de acero de gran tamaño para la siderurgia o la minería. “Empezamos imprimiendo unidades pequeñas y ahora hemos pasado a piezas grandes y complejas”, informa José López Fresno, responsable de fabricación aditiva de ArcelorMittal.
Industria de la fundición
Los procesos aditivos ofrecen a las fundiciones una amplia gama de oportunidades. Aquí son posibles tanto la impresión directa de metales como proceso complementario a la fundición como, sobre todo, los procesos indirectos, como la impresión de moldes de arena, machos y patrones.
La fundición FrankenGuss, por ejemplo, se dedica al proceso directo. “La fabricación aditiva es un excelente complemento a los procesos de fundición convencionales”, afirma la fundición de hierro y aluminio de Kitzingen, en la región de Main-Franconia. Con la fundición por láser de metales en lecho de polvo, FrankenGuss también fomenta los lotes pequeños e incluso las piezas únicas. El espectro de aplicaciones abarca desde prototipos hasta componentes ligeros para la aviación y la movilidad eléctrica, o incluso componentes especiales sometidos a grandes esfuerzos sin un amplio mercado de ventas, por ejemplo para deportes de motor. La impresión bajo demanda también puede utilizarse para producir piezas de recambio individuales, por ejemplo para el mercado de coches antiguos. Escaneando piezas existentes, éstas pueden reproducirse mediante ingeniería inversa, aunque no se disponga de datos de diseño.
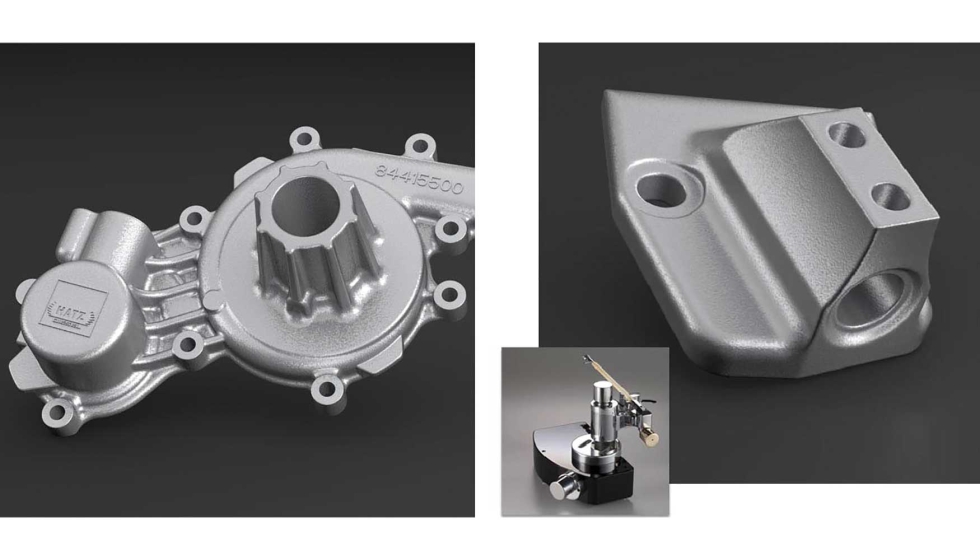
A la izq., prototipo de carcasa de bomba de agua de fabricación aditiva de aleación de aluminio AlSi10Mg para un cortacésped con conductor. A la dcha., Componente para un giradiscos de gama alta, fabricado por adición
de aleación de aluminio AlSi10Mg. Foto: FrankenGuss.
Avanza la industrialización de los procesos aditivos
Un estudio actual realizado en colaboración con el Instituto Fraunhofer de Tecnología de Fundición, Composites y Procesado IGCV prevé un crecimiento de alrededor del 20% en el campo de la fabricación aditiva en los próximos cuatro años. Los procesos aditivos ya se han impuesto con éxito, especialmente para cantidades comparativamente pequeñas, por ejemplo cuando se requiere una geometría compleja y un alto grado de personalización. Hasta ahora, este ha sido principalmente el caso de la fabricación de herramientas, la industria aeroespacial o los productos médicos.
La industrialización de los procesos aditivos avanza y, con la fusión de metales por láser, los procesos de fabricación generativa también ganan terreno como tecnologías de fabricación de pleno derecho. “Hemos alcanzado el ámbito de la producción en serie”, confirma Wolfram Volk, catedrático de la Universidad Técnica de Múnich y director gerente del Instituto Fraunhofer de Tecnología de Fundición, Composites y Procesado IGCV. Sin embargo, un proceso como la fusión selectiva por láser (SLM) de metal es más económico para componentes más pequeños. El profesor Volk señala el ejemplo de la industria del automóvil, donde la fabricación aditiva ya se utiliza para producir cantidades del orden de 1.000 a 2.000 componentes.
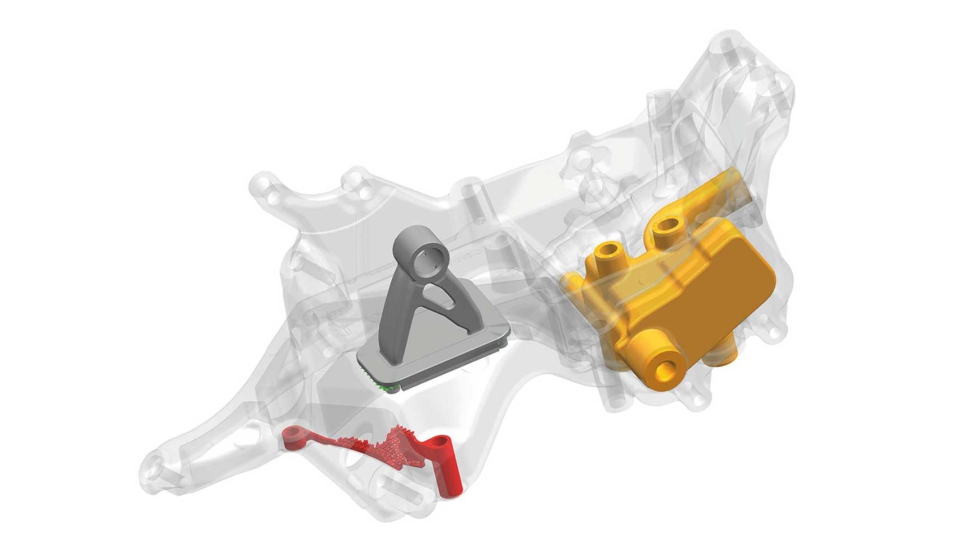
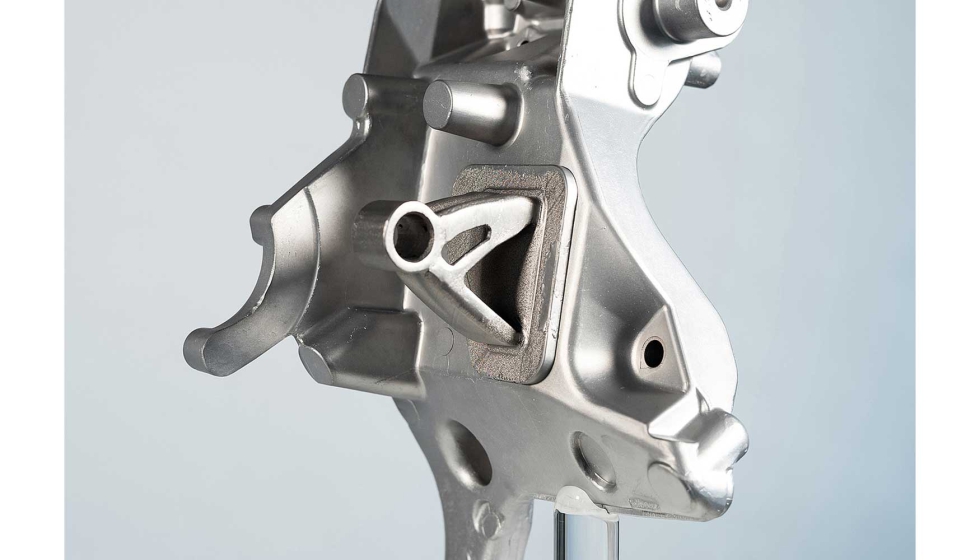
Prometedora tecnología de impresión 3D para fundiciones: inyección de aglutinante de arena
“La fabricación aditiva puede cambiar significativamente lo que ofrece una fundición”, afirma el profesor Volk. En el sector de la fundición, el experto ve un gran potencial para la impresión 3D, especialmente en procesos indirectos como la impresión de moldes de arena, machos y patrones mediante inyección de aglutinante. En la inyección de arena y aglutinante, los machos y moldes se construyen capa a capa a partir de arena que se mantiene unida con un aglutinante endurecedor. El aglutinante adecuado desempeña un papel clave en este proceso. Por ello, los fabricantes de productos químicos para la industria de la fundición, como Hüttenes-Albertus, Reinsicht o ASK, han desarrollado sistemas de aglutinantes especiales que se adaptan con precisión a los requisitos de los moldes y machos de fabricación aditiva.
El proceso de fundición propiamente dicho permanece inalterado con el chorro de arena aglutinante. Esta perfecta integración en los procesos de producción de fundición convencionales representa una ventaja clave frente a la fabricación aditiva directa en metal, incluso en la construcción de prototipos. Las propiedades de los componentes fabricados aditivamente son significativamente diferentes de las de los componentes fundidos. Por tanto, el uso de la fundición por láser de metal para la producción de piezas prototipo es muy limitado. “El proceso directo puede utilizarse para producir un componente de demostración, pero esto también suele conseguirse utilizando componentes fabricados indirectamente de forma aditiva”, señala Volk.
El grado de complejidad y complejidad de la inyección de aglutinante no puede alcanzarse con los métodos de fundición convencionales. Al eliminar la necesidad de construir modelos, el uso de una impresora de arena acorta considerablemente los plazos de fabricación de los componentes de fundición. Los moldes y machos de arena o los modelos de fundición de precisión pueden fabricarse en tan sólo unas horas. Dependiendo del grado de complejidad, esto puede suponer un ahorro de tiempo de varias semanas.
En el Centro Tecnológico de Fundición del Fraunhofer IGCV, Volk y su equipo colaboran con diversos fabricantes de instalaciones. Junto con los expertos del IGCV, el fabricante de impresoras Voxeljet ha desarrollado en un proyecto una impresora de arena que puede producir moldes para componentes de hasta 80 t de peso, por ejemplo para aerogeneradores. “El escalado de la tecnología ha sido un éxito, pero aún hay que demostrar su viabilidad económica”, informa Volk. La ventaja de los moldes sin soldadura frente a los ensamblados se compensa con la desventaja del esfuerzo tecnológico necesario para ampliar el sistema.
Una alternativa a la impresión de un molde grande es el proceso de fundición modular, llamado voxel, que también se está investigando en el IGCV. En este caso, en lugar de imprimir un molde grande, se imprimen segmentos individuales que luego se vuelven a montar como un rompecabezas 3D. “Con la fundición en voxel se obtienen superficies muy lisas que pueden ensamblarse de forma automatizada”, explica Volk, que ve en este proceso una gran oportunidad. “Aquí, con el montaje automatizado de los paquetes de núcleos, la fundición y el desbarbado automatizado con robots, podemos conseguir un proceso muy económico que nos permite realizar componentes muy grandes”.
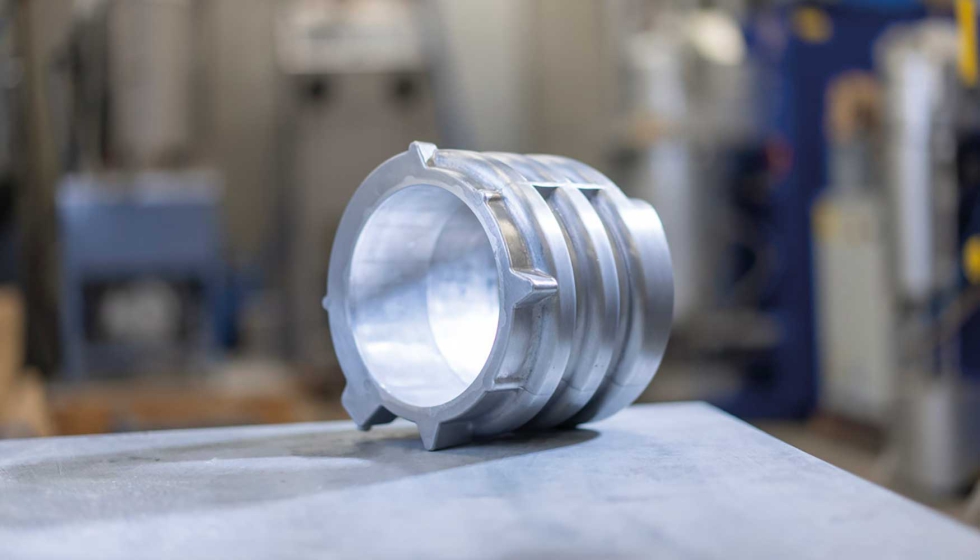
Rescatados en el mar: el ejemplo de la impresión sobre arena
El ejemplo de Hetitec demuestra de lo que son capaces los procesos actuales de impresión en arena. Esta fundición finlandesa es capaz de producir complejas piezas de fundición de hasta 600 kg en pocos días con ayuda de la impresión 3D de moldes y machos de arena. Según sus propias cuentas, esto les convierte en la fundición más rápida de Finlandia. Este enfoque híbrido de la fundición impresa permite combinar la libertad geométrica de la impresión 3D con la rentabilidad de la fundición convencional. Otra ventaja: en comparación con las tecnologías aditivas de procesamiento directo de metales, la fundición de metales tiene una diversidad de materiales significativamente mayor. Además de aleaciones de hierro, Hetitec también puede fundir diversas aleaciones especiales de acero y aluminio.
A la empresa le gusta ilustrar lo que significa la velocidad en la práctica con el ejemplo de un rompehielos varado. El buque estaba varado frente a las costas canadienses con una avería en el motor y el plazo habitual de entrega de la pieza de repuesto necesaria habría sido de cinco meses. La empresa naviera acudió a la fundición finlandesa con un plano de diseño 2D del componente, cuyo dibujo se convirtió en un archivo CAD 3D en una hora. El lunes siguiente comenzó la producción con la impresión 3D de los moldes de arena y el viernes de la misma semana, la pieza mecanizada y acabada estaba de camino a Canadá.
Cadenas de fabricación híbridas: combinar la fabricación aditiva con la fundición
El proceso de inyección de arena no se limita a la impresión de moldes, machos y modelos. Volk, experto en fundición, también ve un potencial considerable en combinar la fabricación aditiva y la fundición. “La producción híbrida, es decir, la fundición de componentes fabricados aditivamente como insertos, tiene sentido para aumentar el grado de complejidad. Aquí veo el mayor potencial en los procesos de fundición en arena construidos”. Entre los posibles campos de aplicación figuran la industria automovilística (por ejemplo, bandejas de baterías), así como la robótica o la tecnología de dispositivos médicos, afirma.
El ‘vaciado’, es decir, la incrustación de componentes, lleva años probándose. Con éxito, por ejemplo, en el Fraunhofer IFAM de Bremen, donde se desarrolló la integración directa de sensores electrónicos y elementos funcionales adaptrónicos en el proceso de fundición a presión con la llamada tecnología Casttronics. Combinando la fundición a presión y la fabricación aditiva, el IFAM pudo presentar hace dos años una carcasa de motor eléctrico con un canal de refrigeración ‘fundido’ integrado.
En otro proyecto de investigación, los institutos Fraunhofer IWS e IWU investigaron cadenas de fabricación híbridas para aplicaciones de automoción. Junto con el proveedor de la industria automovilística Edag Engineering y la fundición Trimet Automotive (hoy Bohai Trimet), se investigó el ‘colado’ o ‘colado’ de componentes metálicos producidos de forma aditiva. El objetivo del proyecto de investigación CastAutoGen era aprovechar la ventaja de costes (economías de escala) que se produce durante la fundición para lograr una mayor eficiencia económica con la fabricación aditiva, incluso para grandes cantidades. Mediante la fundición de componentes metálicos fabricados aditivamente, por ejemplo como intercambiadores de calor o como refuerzos, se puede aumentar la funcionalidad de un componente. Aunque esto también eleva los costes de fabricación en comparación con un componente de fundición a presión pura, los costes son significativamente inferiores a los de la fabricación aditiva pura.
Un ejemplo del valor económico añadido generado por la combinación de los métodos de fundición a presión y fabricación aditiva fue la fundición en un componente de aluminio de un núcleo de refuerzo fabricado con una aleación de cromo, níquel y molibdeno. Con la ayuda de insertos y refuerzos metálicos, así como de la soldadura por deposición láser, se siguió desarrollando un soporte de accesorios para el frontal de Audi en aluminio fundido a presión hasta convertirlo en un producto variante e integrado en la función con el mejor rendimiento posible.
El resultado tiene potencial, por ejemplo, para las cadenas cinemáticas eléctricas. La combinación de fabricación aditiva y fundición a presión también puede servir como proceso de fabricación con visión de futuro para productos de menor volumen, como los vehículos de alto rendimiento, que requieren nuevos componentes con funciones muy integradas.
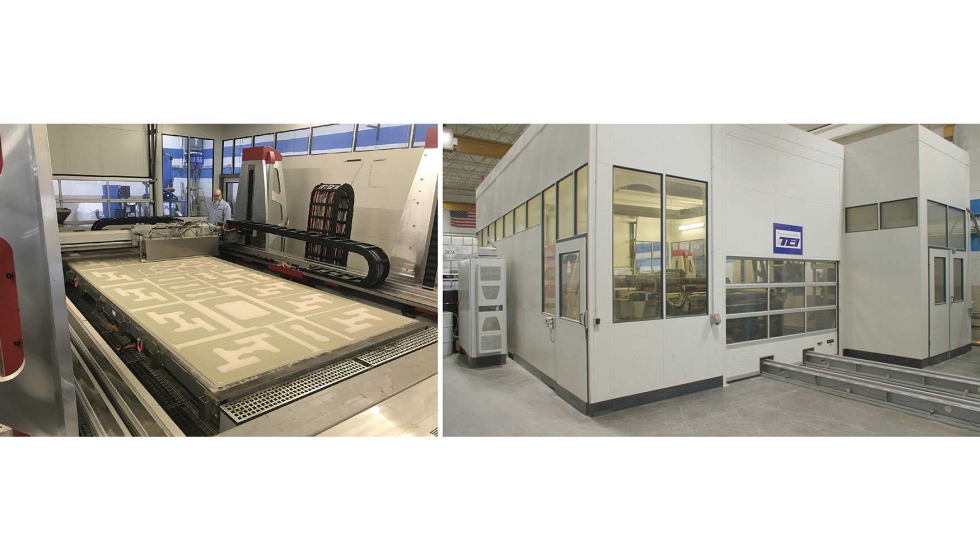