Impresión 3D, futuro próximo de los EPI
Redacción Protección Laboral19/07/2016
A muchos puede parecerles una elucubración futurista basada en la ciencia ficción, pero es realidad: la impresión 3D permite crear –desde hace ya unos años- muchas cosas. Por hablar con propiedad, el usuario puede imprimirse desde la pieza de un motor de aviación, al espejo de un coche, una prótesis de cadera, o un zapato… y, por supuesto, un EPI.
Con macro-impresoras pueden imprimirse casas, que levantan paredes progresivamente con los desplazamientos de su carro ‘impresor’ (inyector de cemento). La técnica de la impresión digital –conocida también como fabricación con aditivos- existe desde hace unas décadas, y los progresos más sorprendentes nos los proporcionará el empleo de nuevos materiales para imprimir (aleaciones de materiales polímeros, aleaciones metálicas inéditas…). En este campo cabe admitir que nuestra imaginación está más limitada que las posibilidades reales de la tecnología. En lo sucesivo, podemos esperar desarrollos inéditos que chocarán con nuestra cosmovisión actual, poniendo a prueba nuestra capacidad de asimilación.
3D: fabricación aditiva
La impresión tridimensional, o fabricación con aditivos, construye objetos sólidos en tres dimensiones por capas sucesivas mediante un utillaje (impresora) que usa un modelo digital como fuente o plano. Básicamente los diseñadores crean una plantilla del producto que cobra cuerpo y forma por medio de materiales como el plástico, cristal, cerámica o acero.
Al principio comparábamos la impresión 3D con los tornos de control numérico (CNC). Si bien ambos sistemas proporcionan una pieza, su funcionamiento es inverso: el torno produce la pieza a partir de un bloque (madera, acero…) eliminando material, mientras que la impresora 3D produce la pieza desde cero aportando el material en capas sucesivas.
El futuro de la tecnología 3D vendrá marcado precisamente por la irrupción de nuevos materiales en la escena de la fabricación. Actualmente en los procesos industriales de impresión 3D se están usando materias primas procedentes de polvos metálicos y aleaciones, geles poliméricos, materiales hidrófobos y los llamados ‘polímeros inteligentes’. En un futuro próximo la lista de materias se verá engrosada con copolímeros, bio-inks (tintas bio) y materiales bio-miméticos, por citar algunos. La versatilidad y variedad de los productos del futuro cercano serán directamente proporcionales al número de materiales disponibles, lo que nos abre la puerta a un futuro difícil de imaginar hoy día.
Sin adelantar acontecimientos, en el cuadro adjunto, se citan algunos de los materiales para impresión 3D más usados actualmente, agrupados por familias.
Construir-fabricar-imprimir por capas
La impresión (fabricación) 3D permite crear objetos sólidos y tridimensionales (ejes x, y, z) depositando capas sucesivas de material (nylon, plástico, metal). Cada capa impresa es una sección transversal, cortada en finos segmentos. Este método, conocido también como la fabricación con aditivos, se ha usado en variadas formas durante décadas.
Orejas, riñones e incluso piel se han impreso con éxito. La NASA cuenta con un proyecto para imprimir comida 3D, y no pocas personas se han enfrentado a cargos judiciales por posesión de armas de fuego que no habían salido de una armería, sino de una impresora 3D.
La posibilidad de imprimir (fabricar) productos de cualquier forma o tamaño tiene el doble efecto de desafiar y complementar la fabricación tradicional contemporánea y, por supuesto, la fabricación de Equipo de Protección Individual. Actualmente, la mayoría de los EPI tienen una producción masiva y formato idéntico. Sin embargo, el importante problema del ajuste encuentra un aliado en esta técnica que permite la personalización en función de los parámetros singulares de cada individuo. Los cascos de seguridad, por ejemplo, impresos a partir de escaneado 3D, tienen un coste de producción unitario que no varía en función del número de unidades (las series cortas no cuestan más que las largas). Y, dado que la tendencia de estos costes es a la baja, la producción masiva empleando impresoras 3D tenderá a incrementarse.
El avance de las impresoras 3D tiene una importancia capital en el producto. Los modelos de impresoras industriales pueden usar hasta 10 materiales (aditivos de fabricación) simultáneamente para fabricar objetos complejos y multi-componente a precios relativamente bajos. Ello brinda a los desarrolladores industriales de EPI la posibilidad de usar nuevos materiales con diversos grados de flexibilidad y resistencia para crear EPIs más seguros y resistentes.
La eclosión de esta revolución fabril aplicada a la fabricación de EPI plantea problemas de carácter normativo, control de calidad, métodos de prueba y evaluación, que se habrán de ir resolviendo sobre la marcha. En cualquier caso, es preciso constatar que la revolución está aquí y que nadie duda que las impresoras 3D llegan para transformar la industria de fabricación de los EPI y otras industrias.
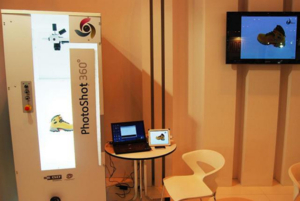
Imprimir el EPI
Estamos leyendo bien, aunque, inicialmente, una inercia nos impide captar el concepto. Dando por supuesto lo que es una realidad, podemos poner el foco en los beneficios, por ejemplo, se puede tener en stock cada estilo, talla color, etc. de cualquier EPI, y nunca llegar a la rotura de stock. En pocas palabras, flexibilidad.
Imprimir EPIs es crear dichos objetos a partir de un fichero digital que contiene el diseño virtual creado mediante CAD (Computer Aided Design – Diseño Asistido por Ordenador). Dicho modelo se ha creado superponiendo ‘rebanadas’ (capas en dos dimensiones) de imagen del objeto mediante un escaneado. Al imprimirse el fichero, el proceso se invierte y, en cada barrido, la impresora crea cada una de las ‘rebanadas’; es decir, crea el objeto superponiendo cada una de las capas (o imagen 2D) para crear un objeto tridimensional completo y sin signo alguno que delate la fabricación por estratificación de capas.
Experiencias industriales en el campo de los EPI demuestran que es posible imprimir múltiples (20 o más) variedades de monturas de gafas de seguridad, combinados con los diferentes tipos de ópticas, con tallas en el intervalo XXS (extra-pequeña) a XXL (extra-grande), en cualquier color o combinación de colores. Otro EPI susceptible de la fabricación aditiva actualmente son los tapones auditivos, sin limitaciones de estilos, formas o colores. Los trabajadores aprecian la variedad, que es más fácil mediante la fabricación flexible que es el 3D, y que se puede aplicar a guantes, cascos, equipo respiratorio, ropa, como veremos a través de ejemplos reales.
La experiencia de Scott Safety
Hay dos factores que son determinantes en las intervenciones de los bomberos: la calidad de la respiración y de la visión. Cuando entraron en vigor las nuevas normas de seguridad de bomberos en Estados Unidos, Scott Safety se planteó un objetivo bien definido: reducir los niveles de CO2 re-inspirado por debajo del 1% con un cambio mínimo de componentes y permitir que los cuerpos de bomberos cumplieran la nueva normativa de seguridad sin costes onerosos. También se planteó mejorar la experiencia general del usuario (mayor confort, mejor visión y flujo de aire sin cambios ni herramientas).
El avance del prototipado fue rápido, pasándose en pocos días de los diseños CAD y la stereo-litografía a los proto-modelos que se ensayaron sobre el terreno en instalaciones de Scott. Las pruebas confirmaron que la re-inspiración del CO2 había caído al 0,75%, con el simultáneo aumento del confort de uso y el campo de visión.
Design Reality, la empresa encargada de la modelización-impresión 3D, con sede en Gales, manifiesta que “sabemos que un buen diseño no siempre tiene que salir más caro”.
- Spirit SX
Este respirador motorizado PAPR (Powered Air Purifying Respirator), uno de los más avanzados del mercado, permite al usuario adaptarlo mediante la programación en función de la situación que debe afrontar. El confort y ajuste se complementan con el diseño y la portabilidad. Este sistema inteligente de protección respiratoria ofrece la posibilidad de ajuste del flujo de aire y unos bajos costes en su ciclo de vida. Opera con filtros de gas, partículas o combinados con una nueva y actualizada gama de calotas versátiles para ofrecer protección en ambientes peligrosos.
La pantalla de visualización proporciona una indicación clara del rendimiento y la capacidad restante. Existen versiones que reconocen automáticamente y muestran el tipo de filtro, impidiendo el uso de filtros inadecuados o mal acoplados.
Guante impreso 3D
Forma parte de esta nómina de EPIs de última generación. Se trata de una órtesis que, según definición de ISO, es “un apoyo u otro dispositivo externo aplicado al cuerpo para modificar los aspectos funcionales o estructurales del sistema neuromusculoesquelético”. Según su función, las órtesis pueden ser estabilizadoras, funcionales, correctoras y protectoras.
En la línea de montaje de la planta de BMW Group (Munich) están evaluando este guante pensado para prevenir el estrés de las articulaciones de dedos y manos por acumulación de presiones y movimientos repetitivos. Los prototipos de estos guantes especiales se han fabricado mediante impresión 3D, hecho que permite confecciones a la medida a partir de la exploración o escaneado de la mano.
En la fabricación de automóviles, las manos son insustituibles como herramienta de trabajo. Los mayores esfuerzos suelen soportarlos los dedos pulgares. En las tareas manuales de montaje, los pulgares soportan esfuerzos hasta cuatro veces superiores a los de los otros dedos. Una operación común es la de introducir tapones de goma en los orificios por los que se ha drenado la pintura del suelo del coche. En la misma, cuando se efectúa de forma manual, el pulgar actúa como lo haría la cabeza de un martillo. Ese movimiento hace que la articulación del pulgar llegue a sufrir fuertes extensiones al doblarse hacia atrás. La repetición del movimiento centenares de veces al día supone una prueba para la articulación que puede acabar afectada.
Los operarios han experimentado una mejora de sus condiciones de trabajo, según la primera evidencia.
Trajes espaciales de última generación
La incipiente conquista del espacio tiene el punto de mira puesto en marte, proyecto que se irá perfilando durante las próximas décadas. Además de la comida (ya hemos citado un proyecto de la Agencia en este campo), otro de los asuntos fundamentales es el de los trajes espaciales, que, más allá del concepto del vestido, son equipos de soporte vital. El reto es conseguir trajes no sólo funcionales, sino también ligeros, confortables y personalizados. Con tales premisas, el uso del escaneado y de la impresión 3D aparecen como las tecnologías ideales. La tecnología 3D permite la creación de prototipos que están sometidos a un proceso de mejora y optimización permanente, con la gran ventaja de que el prototipado y las modificaciones son más rápidos que en procesos de fabricación convencionales.
El traje Z-2 de la NASA es el prototipo más nuevo de su serie. Con la vista puesta en Marte, el trabajo de desarrollo de las tecnologías que los astronautas usarán algún día para vivir y trabajar en dicho planeta ya se están desarrollando hoy día. Así, cada logro de la Serie Z nos acerca las tecnologías que se incorporarán en los trajes espaciales de los humanos que lleguen a pisar el planeta rojo. Hay muchos avances en el traje Z-2 si lo comparamos con su predecesor. El más significativo es que el Z-1 tenía un torso superior blando, que ahora es de composite duro en el Z-2. Este cambio proporciona una durabilidad a largo plazo que es un requisito esencial para un traje destinado a trabajos conocidos como “EVA” (Extravehicular Activities – Actividades fuera de las naves principales). Las articulaciones de los hombros y las caderas difieren significativamente respecto al desarrollo anterior en un intento de optimizar la movilidad. Las modificaciones también incluyen al calzado y, en general, los materiales del Z-2 son compatibles con un entorno de vacío total.
La Agencia tiene previsto evaluar la movilidad del traje en un área específica del Johnson Space Center (Houston) que reproduce las condiciones de la superficie rocosa de Marte. Los científicos valorarán el confort y nivel de prestaciones. Sus conclusiones guiarán a los ingenieros a diseñar el traje que condense dichas mejoras, el Z-3, con el valioso auxilio de la tecnología 3D. Significativo es el hecho de que el entorno 3D está presente también en las misiones espaciales, lo que confirma el hecho aceptado de que la tecnología 3D es la tecnología de fabricación de un futuro en el que ya estamos dando los primeros pasos.
Proyectos precursores en España
La tecnología 3D incluye el patronaje, o confección digital del modelo (CAD), y su ejecución o impresión, que es la parte más novedosa del proceso.
En España también se están desarrollando proyectos 3D en el sector de la protección, siendo el sub-sector del calzado el que lleva la delantera, a través de sus institutos tecnológicos. Al respecto, cabe citar:
- CTCR: innovación en la fabricación y desarrollo de productos
Frente a la elaboración artesanal de bocetos y construcción manual de prototipos, el Centro Tecnológico del Calzado de La Rioja (CTCR) ofrece un servicio novedoso y que asegura inmediatez y fiabilidad al proceso de fabricación de prototipos de suelas del calzado.
El procedimiento comienza con el diseño en 3 dimensiones del modelo que se pretende prototipar para, a continuación, realizar un prototipo de la suela en material rígido. Éste se utiliza para construir un molde a partir del cual se obtienen prototipos del piso original en material flexible. Para su construcción, el CTCR utiliza una novedosa impresora 3D que va depositando sucesivamente capas de un material similar a la escayola, a la vez que su cabezal incorpora un fluido que, a modo de adhesivo, actúa en las zonas específicas. A continuación, se hace el correspondiente procedimiento para conseguir las dos partes del molde en silicona, caracterizado por la gran calidad que ofrece en los detalles. Finalmente, se procede a fabricar el elástico con poliuretano (PU), un material idóneo para la obtención de los prototipos, ya que es fácilmente manipulable y no requiere de elevadas temperaturas ni presiones para su solidificación.
La construcción de moldes para inyección y vulcanización de pisos es costosa y tiene plazos de varias semanas. Sin embargo, con el servicio del citado instituto, cualquier empresa del sector del calzado puede beneficiarse de este nuevo proceso de prototipado rápido de moldes, que permite generar en la fase de diseño maquetas flexibles y muy económicas.
El CTCR también cuenta con servicios de desarrollo de producto en 3 dimensiones (3D), realidad aumentada, así como en la visión artificial. Sobre este particular, basta citar el sistema Photoshop 360º, solución tecnológica, pionera en España, que permite recrear simulaciones tridimensionales virtuales de objetos físicos reales, a partir de la toma automatizada de fotografías y su procesado por ordenador, ofreciendo una visión del producto en todo el arco de la circunferencia.
- Inescop: novedades en el diseño de calzado en 3D
Los sistemas de diseño CAD tridimensional constituyen una herramienta innovadora que aporta flexibilidad a los diseñadores, a la vez que permite un ahorro considerable. Suponen un cambio de paradigma: las industrias tradicionales y manufactureras pasan a ser industrias de base tecnológica.
El programa Icad3D+ de Inescop incentiva la creatividad. Permite crear modelos virtuales de calzado que fácilmente pueden pasarse a la fabricación, ya que se desarrollan sobre una horma con sus dimensiones reales. Incluye una nueva herramienta para la creación de componentes (pisos, plataformas, cuñas, tacones, tapas, suelas con espiga, etc.) adornos y complementos de calzado (cordones, cremalleras, hebillas, ojales, tachas, etc.).
Asimismo, también destaca un nuevo módulo que permite eliminar la rigidez de los modelos utilizando técnicas basadas en deformaciones globales, además del módulo de renderizado de imágenes, totalmente integrado en la aplicación, y con el cual es posible generar imágenes hiperrealistas de altísima calidad, así como videos de los modelos en movimiento. En definitiva, esta tecnología 3D permite no sólo imaginar el calzado, sino verlo y evaluar su comportamiento antes de fabricarlo.