Aluminium scales improve the appearance of the roofs of engines
Michael Schäufele, director of key accounts - automotive of Albis Plastic GmbH, Hamburg,
Albert Fendt, responsible of the company and director of key accounts, Faist Automotive GmbH, Krumbach
reiner schmid, engineer of development of components of plastics of the engine, BMW Group Division.15/09/2005
This situation can be illustrated through the collaboration between the BMW, the systems Faist Automotive supplier Group GmbH & Co. KG, Kulmbach, Germany, and the supplier of raw materials Albis Plastic GmbH, Hamburg, Germany. All of them came to the conclusion that only could occur the optimal components at a favorable price through the close collaboration of a team as soon as possible in the phase of the project. The case specific question had to do with an acoustic screen and a cover of air to the current series 3 BMW with diesel engine four-cylinder direct injection power of 110 kW (330 n·m). The underlying philosophy was to introduce the functionality and design sophisticated in the engine compartment. The demands of components were beyond an elegant design of the engine compartment. Functions such as noise attenuation, decoupling of components and specific routes are taken into account in the design and development of these components of the air intakes to allow that the vehicle can drive through high water levels.
For design reasons, the middle section of the cover of air intake also is moulded by injection in the polyamide of color aluminum silver metal supplied by Albis. This is produced by moulding by injection of two components: in the frontal region shapes a flange of PP/EPDM to provide a function of fixing and decoupled with the body. Both components are delivered preacabados to the automaker production lines.
Previous engine covers were uniformly black and were manufactured in PA6 GF10 MR20 standard with printed silver bars.
PA6-GF10-MR 20 black (Alcom 6 PA 900/8 GF10) (Black MR20 12-957) | PA6-GF10-MR20 aluminium (Alcom 6 PA 900/8 GF10 MR20) (Silver metallic 12-778) | |
Traction resistance to breakage (MPa) According to DIN EN ISO 527 | 106 | 109 |
Module voltage (MPa) according to DIN EN ISO 527 | 6169 | 6190 |
Elongation at break (%) according to DIN EN ISO 527 | 3.85 | 3.38 |
Module flexion (MPa) according to DIN EN ISO 178 | 6190 | 6240 |
Resistance to impact (23 ° C) according to DIN EN ISO 179/1eU | 30.5 | 28.7 |
Impact resistance with entalla (23ºc) According to DIN EN ISO 179/1eA | 5.2 | 4.4 |
Appearance of homogenous quality
On the basis of the characteristics required of the materials addressed product development in the area of metal plastic color for use in the attenuation of noise and air cover. ALBIS developed a technology of process which allowed the complex composition of a hybrid plastic achieving the desired metal effect introducing aluminium flakes and the appropriate color. The results presented a significant improvement on the homogenous appearance of the surface compared with the metal plastics used so far.
Were preliminary experiments with 6PA GF10 MR20 material specified by the manufacturer of the car; However, this plastic required greater optimization in regard to his appearance. The sequences of correction consisted of vary the shape and size of the scales with a simultaneous control of color during the preparation of the compound until obtaining the desired appearance and the necessary thermal stability to ageing. After this series of experiments, the product had to be able to play the laboratory to production. A fundamental problem in this context is the consistency and reproducibility of the color as a result of the use of extrusion machines of different sizes. In order to guarantee the quality characteristics, Albis developed a special for the molding mold injection of this material. Incorporated in this mold geometries enabled evaluation continued visibility of joints and lines of flow during production.
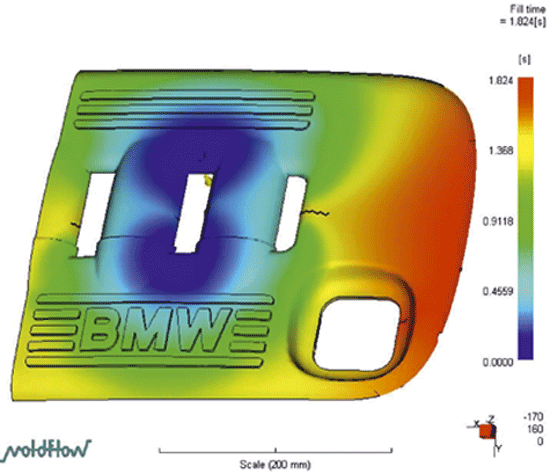
According to Albert Fendt, responsible for authorized company and director of key accounts for Faist: "the corresponding specialized departments were involved in an initial stage of the development of the product." We had intensive discussions and discuss the possibilities and risks. Faist has a line of data especially for the car manufacturer. Exchange CAD data, there are drawings, our design engineers have to transform the designs into tools and functions of the components should validate. Another task is to develop reliable sets of parties and individual components that conform to the specifications of the client. We updated the CAD data of the system to avoid the collision between interconnected parts and to ensure a direct and logical sequence of mounting in production lines. Cost-effective production of the two covered only could be achieved by injection by moulding. Only problems can occur when there are openings in one piece; which lead to unions, which may be visible as flow lines on the surface. "It is necessary to have a great experience in the design of molds and the injection moulding to produce a visible components and design with an appearance of such high quality".
At the preliminary stage of the construction of the mold is invested considerable effort to ensure that the demands of quality of the components met with the help of a presentation by computer and simulation of delay by Moldflow carried out by the Department of falls from Albis. The sets were produced with the help of six individual moulds, designed and produced by Faist Tooling. The sets were built in Faist in Ziemetshausen, Germany facilities, machines of injection moulding with up to 10,000 kN clamping forces. Assembly workshops were prepared for the ultrasonic welding process and the final assembly of sets.
The selection of materials is not only critical to achieve the necessary properties, but it also has economic implications. The BMW Group established the maximum expenses for raw materials of aluminum metallic silver color. The work of development with the supplier of raw materials started during this phase. Since that could not meet the requirements with the standard materials, developed a plastic with specific properties. Technical knowledge in the preparation of compounds of Albis proved a great advantage.