Ventilación de moldes o salidas de gases: conceptos (Parte 2)
José Ramón Lerma, escritor técnico y docente
22/04/2025En la primera parte de este artículo, exploramos los conceptos fundamentales sobre la ventilación de moldes y la importancia de las salidas de gases en los procesos de inyección. En esta segunda parte, nos enfocaremos en un problema recurrente en la industria: el efecto diésel o quemados. Analizaremos sus causas, cómo identificarlo y qué medidas pueden tomarse para minimizar su impacto en la calidad de las piezas inyectadas.
Efecto Diésel o Quemados
Si el aire no encuentra una vía de escape adecuada, se genera una sobrepresión o compresión. Aunque esta presión puede ayudar a forzar la salida del aire, su efecto negativo es predominante: la compresión provoca un sobrecalentamiento debido a un efecto de calor adiabático, donde las moléculas de aire, al estar más juntas, chocan entre sí con mayor intensidad.
Además, cuando el aire se calienta, tiende a expandirse. Sin embargo, si no tiene una vía de escape, la presión y la compresión dentro de la cavidad aumentan aún más.
El aire atrapado en un molde de inyección puede comprimirse a tal punto que su temperatura se eleva rápidamente, provocando la combustión instantánea del plástico adyacente. Este fenómeno se conoce como efecto diésel. De hecho, los motores diésel de automóviles generan la ignición del combustible mediante una compresión extrema, alcanzando una relación de 20:1.
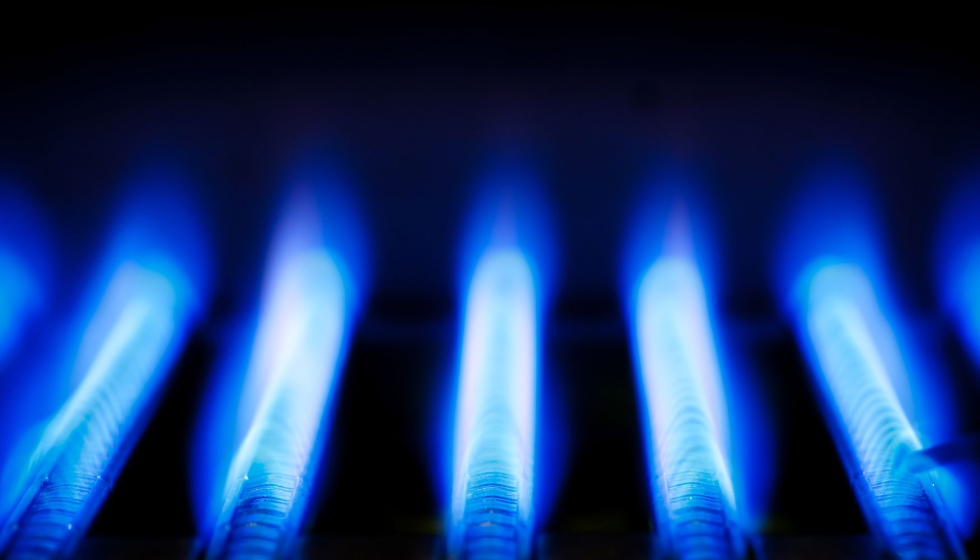
Gas.
Este sobrecalentamiento localizado, o supercalentamiento, no solo quema el plástico, sino que también puede dañar la superficie del molde, provocando su erosión progresiva.
Cuando comienzan a manifestarse los síntomas del efecto diésel, como depósitos oscuros, material ligeramente quemado o piezas con un brillo anómalo en la zona final del llenado, es crucial intervenir de inmediato. La erosión del molde avanzará rápidamente en las áreas más expuestas, comprometiendo su integridad y reduciendo su vida útil.
La única ventaja de este fenómeno es que, al comprimirse, el aire se vuelve más denso, lo que permite evacuar un mayor volumen en menos tiempo. Una vez que este aire comprimido atraviesa las salidas de gases o los canales de ventilación, se expande libremente hasta recuperar su presión atmosférica, así como su densidad y volumen normales, en el canal de salida de mayor tamaño.
Dicho sea de paso, la expansión súbita que ocurre después de la salida de gases en el partage provoca una caída de temperatura en el aire. Este enfriamiento es, en parte, responsable de que algunos de los volátiles presentes en el flujo puedan condensarse dentro de los canales de salida, ensuciándolos y, en algunos casos, llegando a obstruirlos.
Cuando los plásticos se calientan y funden para su moldeo, liberan gases. Estos gases provienen del paquete de aditivos, plastificantes, estabilizantes y otros componentes de la fórmula del polímero en cuestión. Algunos de estos compuestos son NAV (Non-Aqueous Volatiles), es decir, volátiles no acuosos.
La mayoría de los NAVs no se adhieren a las paredes del molde ni son absorbidos por el plástico. En realidad, son empujados hacia afuera por el frente del flujo fundido. Sin embargo, al mezclarse con el oxígeno del aire atrapado en el molde, pueden convertirse en un combustible, de manera similar al diésel en un motor.
De manera general, algunos materiales generan más NAVs o volátiles que otros. Por ejemplo, el PS (poliestireno) libera pocos, mientras que materiales como POM (acetal), PC (policarbonato) y PVC (policloruro de vinilo) generan una cantidad considerable. Asimismo, los polímeros altamente aditivados para mejorar su resistencia a la radiación UV, como el ASA (acrilonitrilo-estireno-acrilato), pueden producir un alto volumen de volátiles debido a la gran cantidad de aditivos presentes en su formulación.
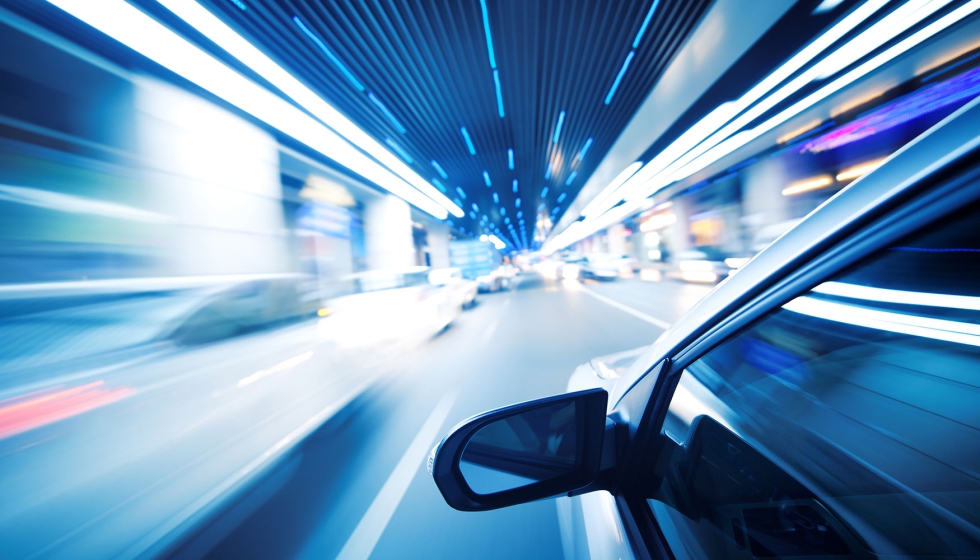
La mayoría de los NAV, al mezclarse con el oxígeno del aire atrapado en el molde, pueden convertirse en un combustible, de manera similar al diésel en un motor.
Punto de vista del proceso
Cuando un técnico de inyección detecta un efecto diésel o quemado debido a la falta de ventilación, suele actuar reduciendo la velocidad de inyección o el caudal de llenado del molde. Esto facilita la salida del aire al exterior y, en muchos casos, soluciona el problema. Sin embargo, ¿es realmente la acción más adecuada?
Como medida de contención inmediata, esta estrategia puede ser útil, pero es fundamental entender que la causa raíz del problema no es la velocidad de inyección, sino la insuficiente ventilación del molde. Reducir la velocidad de inyección puede traer consigo una serie de efectos colaterales no deseados, tales como:
- Aumento de la viscosidad del plástico.
- Menor generación de calor interno por cizalla.
- Reducción del área de paso del material fundido a través del espesor de pared de las piezas debido al mayor enfriamiento de la capa fría.
- Mayor caída de presión durante el llenado.
- Aumento del tiempo de inyección y, por ende, del ciclo de producción.
Además de verificar la cantidad, posición y dimensiones de las salidas de gases, es recomendable revisar otros parámetros que pueden influir en la generación de gases, como:
- Contrapresión excesiva durante la carga.
- Velocidad tangencial alta.
- Temperatura elevada en la unidad de inyección.
- Tamaño inadecuado de la unidad de inyección.
- Ratio de compresión del husillo incorrecto.
- Diseño deficiente de entradas y canales de distribución.
En definitiva, cualquier condición que implique mayor cizalla y temperatura del material incrementará la generación de gases, lo que a su vez dificultará su evacuación durante el llenado de la cavidad.
En algunos casos, se recurre a la reducción de la fuerza de cierre, lo que permite que los ajustes entre las placas del molde se relajen ligeramente, facilitando la salida del aire. Sin embargo, si la fuerza de cierre ya está correctamente ajustada, esta práctica puede aumentar el riesgo de rebabas en las piezas.
Chequeo de salidas de gases
El método más utilizado para verificar la ventilación del molde es el azul de Prusia. La técnica consiste en aplicar el pigmento y cerrar el molde aplicando la fuerza de cierre de manera progresiva, en incrementos del orden del 10%, hasta alcanzar la presión de cierre deseada. Con este procedimiento, es posible determinar si las salidas de gases están siendo excesivamente comprimidas o si se cierran debido a la flexión de las placas y a dimensiones excesivas en la anchura del canal de ventilación.
Este método de comprobación permite evaluar tres aspectos clave:
- Cuánta presión de cierre se requiere para que ambas mitades del molde entren en contacto y sellen correctamente alrededor del perímetro de la cavidad o la línea de partage.
- Cuál es la presión mínima de cierre necesaria para evitar la formación de rebabas.
- En qué estado se encuentran los canales de ventilación.
Para optimizar la ventilación, se recomienda realizar simulaciones de inyección en software especializado, permitiendo identificar las ubicaciones óptimas de las salidas de gases antes de mecanizar el molde.
Si el molde ya está construido, un análisis del proceso mediante la metodología Decoupled Molding ayudará a identificar las zonas críticas donde se requiere una evacuación eficiente de los gases atrapados.
Según documentos técnicos de DuPont, existe una técnica adicional para detectar problemas de ventilación: Aplicar un spray a base de hidrocarburo o queroseno sobre el molde justo antes de la inyección. Si la ventilación es deficiente, el hidrocarburo provocará la aparición de puntos negros en las zonas donde el aire queda atrapado.
Esta técnica resulta especialmente útil en moldes de varias cavidades, ya que facilita la detección de zonas con ventilación deficiente. Además, el spray de hidrocarburo actúa como antioxidante, ayudando a proteger las superficies del molde.
Conclusión
Dado que el sistema de ventilación del molde es un factor crítico que influye en múltiples problemas de calidad de las piezas, su eliminación debe ser prioritaria cuando se detectan defectos relacionados.
El venting es una de las causas raíz más comunes de problemas en el proceso de inyección, pero afortunadamente, es una de las más fáciles de descartar dentro del análisis de posibles factores que afectan la calidad del producto final.
José Ramón Lerma es autor de los libros: 'Libro Manual Avanzado de Inyección de Termoplástico', que tiene como objetivo ser, por un lado, una herramienta para la formación y, por otro, un manual de ayuda para todo el personal de una empresa de inyección de plásticos y, del recientemente editado, 'Scientific Injection Molding Tools. Productividad a través del dominio del proceso'. Ambas publicaciones, comercializadas por Plásticos Universales / Interempresas (libros@interempresas.net), consta de detallados casos prácticos, amplia información de moldeo científico y un ‘pendrive’ con 20 hojas de cálculo y herramientas de SC Molding o Scientific Injection Molding, además de optimización y definición de proceso, lo que lo hacen único en el mercado. El libro Manual Avanzado de Transformación de Termoplásticos ha sido editado y comercializado en inglés a nivel mundial por la editorial Hanser Publications. Página web sobre Scientific Injection Molding: www.asimm.es