Presenta soluciones de estanquidad para la industria del hidrógeno, cojinetes de fricción ultrabaja con una extraordinaria resistencia a la compresión y soluciones de estanquidad para mejorar el rendimiento de la próxima generación de vehículos eléctricos
Trelleborg presenta plásticos, elastómeros y materiales compuestos y materiales compuestos en Global Industry 2024
Trelleborg mostró sus últimas tecnologías innovadoras, entre las que se incluyen nuevas soluciones de estanquidad para la industria del hidrógeno, cojinetes de fricción ultrabaja con una extraordinaria resistencia a la compresión y soluciones de estanquidad para mejorar el rendimiento de la próxima generación de vehículos eléctricos. Trelleborg trabaja con sus clientes para desarrollar soluciones óptimas que cumplan los requisitos de rendimiento más exigentes, como temperaturas y presiones extremas y la presencia de productos químicos agresivos.
Jean-Philippe Perrot, director de soluciones, afirma: “Con nuestras insuperables soluciones de polímeros para la estanquidad, amortiguación y protección de aplicaciones críticas en entornos exigentes, desarrollamos soluciones innovadoras diseñadas a medida que aceleran el rendimiento de nuestros clientes de forma sostenible. Trabajamos en colaboración con ellos desde los conceptos de diseño iniciales hasta el desarrollo de la solución adecuada para su aplicación, lo que les permite reducir el tiempo de comercialización y añadir valor a los procesos y productos".
En el stand se exhibió la gama H2Pro de soluciones de sellado diseñadas específicamente para acelerar la innovación de la tecnología sostenible y ofrecer soluciones para cada aplicación de la cadena de valor del hidrógeno. Adecuada para la producción, el transporte y el almacenamiento de hidrógeno, así como para su uso final, la gama H2Pro ha demostrado su capacidad para soportar entornos de aplicación exigentes. Resisten altas presiones, bajas temperaturas y resistencia a la permeación, al tiempo que muestran excelentes propiedades de desgaste y extrusión.
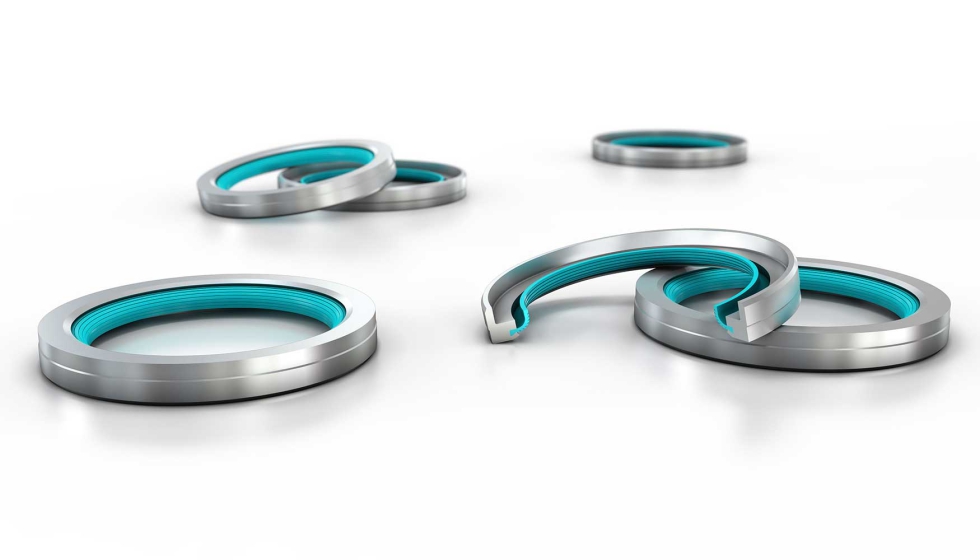
Otra solución innovadora presentada es Orkot C620, un material de cojinete de fricción ultrabaja con una resistencia a la compresión excepcional que amplía los límites de la tecnología de compuestos. Se trata de un compuesto termoestable de alta especificación, con un fuerte soporte de fibra de vidrio y un revestimiento Orkot de baja fricción, que cumple los requisitos de las aplicaciones de alta carga más exigentes en todos los sectores del mercado, incluidos el energético, el de vehículos todoterreno y el industrial. A pesar de su resistencia y ligereza, soporta grandes cargas y tensiones durante una larga vida útil.
Mark Hampton, director de productos e Innovaciones, afirma: “Las propiedades optimizadas de Orkot C620 proporcionan a los clientes un cambio radical en los cojinetes compuestos, ofreciendo una combinación única de fricción ultrabaja y una resistencia a la compresión de 470 MPa, cinco veces la resistencia de los materiales Orkot estándar. Es más resistente y tiene mejores características de fricción que los materiales compuestos de la competencia, e incluso puede desafiar a muchos cojinetes metálicos en cuanto a resistencia, ofreciendo a industrias como la aeroespacial las soluciones más ligeras y de menor fricción que demandan cada vez más".
En el stand también se presentaron las juntas rotativas de alta velocidad HiSpin, diseñadas para mejorar el rendimiento de los ejes de nueva generación de los vehículos eléctricos, que representarán el 30% de todo el tráfico en 2030. El eje eléctrico, que combina el motor eléctrico y la caja de cambios en una sola unidad, es un elemento fundamental de un coche eléctrico, pero plantea graves problemas de estanquidad, como velocidades de rotación de hasta 16.000 RPM y un uso limitado de la lubricación.
Las soluciones HiSpin están diseñadas específicamente para destacar en el sellado de ejes eléctricos, apoyando el objetivo de la industria del automóvil de producir un coche eléctrico capaz de igualar a un vehículo de gasolina en autonomía con una sola carga. La junta HiSpin PDR RT tiene unas excelentes características de sellado a velocidades de hasta 60 metros por segundo. La combinación de un material único, un proceso de fabricación innovador y un diseño especializado del labio de estanquidad reduce la fricción hasta un 75% en comparación con las juntas de PTFE tradicionales, lo que se traduce en una reducción significativa del consumo de energía.
En la feria también se presentó Seal-Glide, un tratamiento superficial a nanoescala que mejora las prestaciones de fricción de los revestimientos convencionales. Aplicado mediante un proceso innovador, produce un acabado hasta 50 veces más fino que muchos revestimientos convencionales. Esta técnica también permite el tratamiento de componentes con geometrías y características complejas, como socavados, que de otro modo sería imposible con revestimientos a base de laca.
Incluso después de ser estirado, Seal-Glide recupera un acabado liso sin roturas, manteniendo sus propiedades de deslizamiento mejoradas. Seal-Glide puede aumentar la vida útil de todo el sistema de estanquidad, impulsar el montaje y el funcionamiento de su producto y mejorar el rendimiento mediante una reducción significativa de la fricción y la adherencia.
Para más información sobre las últimas innovaciones de Trelleborg, visite: https://www.trelleborg.com/en/seals/products-and-solutions/latest-innovations