La máquina de moldeo por inyección IntElect 1000 kN de Sumitomo (SHI) Demag trabaja a pleno rendimiento en la planta piloto de moldeo por inyección de BASF
Sumitomo (SHI) Demag y BASF desarrollan una nueva célula para la fabricación de polímeros de alto rendimiento
En la planta piloto de moldeo por inyección y extrusión de BASF en Ludwigshafen (Alemania), especializada en la comprobación del rendimiento químico y mecánico y de las condiciones de procesamiento de los materiales, cuenta con una nueva célula de moldeo por inyección totalmente automatizada de Sumitomo (SHI) Dema, que ya ha comenzado a dar los primeros resultados, repetibles en más de 4.000 configuraciones de prueba al año.
Aunando conocimientos de ingeniería y recursos tecnológicos, la división de materiales de BASF, en colaboración con Sumitomo (SHI) Demag y H + S Automatisierung, han creado una celda de fabricación innovadora para producir una amplia gama de muestras de prueba diferentes para el desarrollo de productos polímeros termoplásticos y compuestos.
El centro de la célula es la inyectora IntElect 1000 kN de Sumitomo (SHI) Demag, de gran precisión. Ha sido seleccionada por su diseño compacto, su eficiencia energética y su capacidad de repetición. El equipo de 30 operarios de investigación de la instalación en BASF valoran las características mejoradas de bienestar y seguridad de la IntElect. Entre ellas, las soluciones progresivas para automatizar los cambios de molde y las bajas emisiones de ruido combinadas con soluciones de procesamiento robótico totalmente digitalizadas.
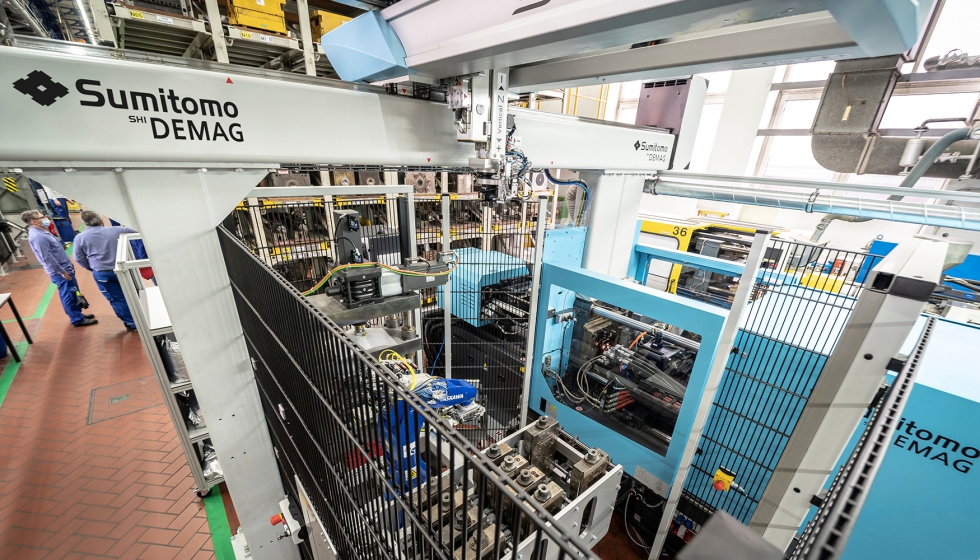
Sumitomo (SHI) Demag y BASF han desarrollado una nueva célula de fabricación de polímeros de alto rendimiento. Imagen de BASF
La instalación cuenta con un robot lineal SDR 5-35S que cumple dos funciones. Una novedad es la automatización total de la selección y colocación de uno de los 12 insertos de molde intercambiables de un almacén situado dentro de la célula. Una vez moldeada la pieza, el mismo robot, dotado de una pinza multifuncional, extrae suavemente la muestra del molde y la pasa al pequeño robot Yaskawa GP8 de brazo articulado de seis ejes para cortar con precisión las muestras de la compuerta mediante una punzonadora de servohusillo.
La instalación, que integra el concepto de inserción de moldes y las características especiales de BASF en la unidad de inyección, también incluye una unidad de control térmico de la temperatura existente y un nuevo sistema digital de ejecución de la fabricación (MES) para trazar cada secuencia de prueba. Reinhard Jakobi, director de Procesamiento de Materiales de Alto Rendimiento de BASF, describe el proyecto como un logro de la ingeniería avanzada que combina una tecnología madura con la automatización más avanzada y la precisión del moldeo. Atribuye a la dedicación, la flexibilidad y el enfoque orientado a las soluciones de todo el equipo la realización de un proyecto tan pionero.
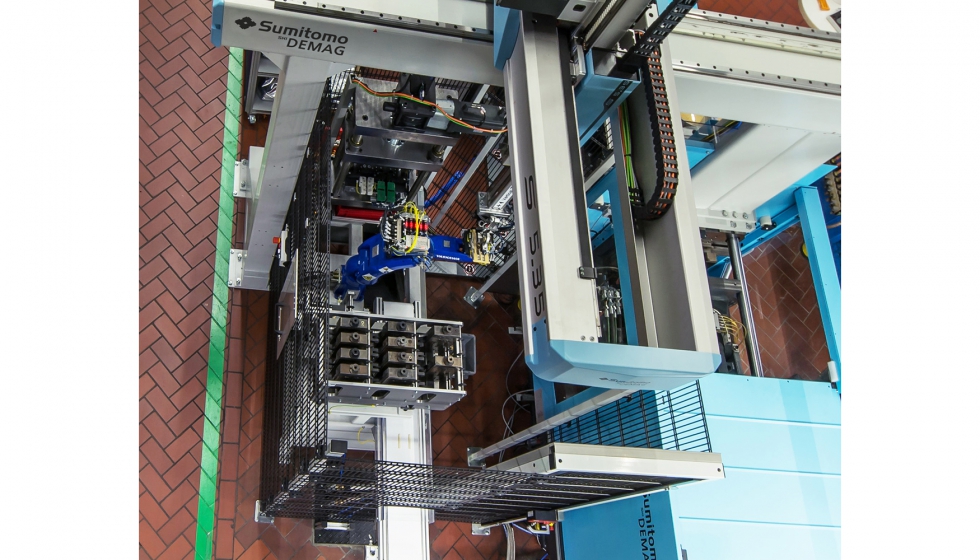
Sumitomo (SHI) Demag y BASF han desarrollado una nueva célula de fabricación de polímeros de alto rendimiento.
Angelika Homes, ingeniera de proyectos senior de BASF, amplía: “Aunque tenemos una amplia experiencia colaborando con el equipo de Sumitomo (SHI) Demag en la producción de piezas de prueba estándar, desde el principio todos los socios apostamos por abrir nuevos caminos. A pesar de la complejidad del proyecto, Sumitomo (SHI) Demag y H + S entregaron un innovador diseño de célula de producción en un espacio y energía mucho más reducidos”.
Demasiado caliente para manipularlo
Muchas de las muestras que se procesan en el centro técnico de BASF son termoplásticos de alta temperatura, reforzados con fibra y a menudo ignífugos. En consecuencia, las temperaturas de fusión pueden alcanzar los 400 °C y las temperaturas de los moldes llegan a los 180 °C. En cualquier momento, se pueden cargar hasta 12 insertos intercambiables en el almacén lateral y, a continuación, cambiarlos automáticamente en la inyectora. Mediante la integración de un sistema de control de temperatura HB-Therm con el control de la máquina de Sumitomo (SHI) Demag, los cambios automatizados de las plaquitas del molde pueden llevarse a cabo de forma segura y eficiente, incluso cuando el proceso se realiza a altas temperaturas del molde.
El ingeniero senior de sistemas de automatización de Sumitomo (SHI) Demag, Markus Hausmann, explica: "Para bajar la temperatura a 80 °C y despresurizar el inserto para garantizar que el robot SDR pueda retirar el inserto del molde de forma segura, nuestro control de la máquina tiene que hablar e interactuar sin problemas con el MES de BASF.
El MES de BASF informa a la célula cuando el ajuste de la muestra producida en ese momento está a punto de terminar, alineando la siguiente aplicación del molde. Inmediatamente después de que el proceso de inyección se detenga, el enfriamiento del inserto del molde es dirigido por la interfaz de la unidad de control de temperatura integrada.
Perforar con precisión
Para BASF, resolver el reto del punzonado ha sido uno de los mayores logros de la ingeniería. Debido a su amplio perfil de aplicaciones, BASF prueba una gran variedad de materiales, desde polímeros blandos y resistentes hasta rígidos y frágiles. También hay muchas geometrías de muestra diferentes, incluyendo espesores que varían de 0,8 mm a 4 mm. Todas las muestras de ensayo de BASF se fabrican de acuerdo con la norma ISO 294. Esta especifica la precisión del sistema de bebederos y los requisitos específicos que debe cumplir cada geometría de muestra. “La extracción mediante punzón es un requisito previo, ya que no modifica las propiedades del material y elimina las partículas de polvo”, explica Markus Hausmann.
La pinza multifuncional garantiza que todas las geometrías de las muestras se coloquen con la máxima precisión en la placa de punzonado. Esto es complejo en sí mismo debido a que muchos de los materiales con los que trabaja BASF tienen un alto contenido de fibra de vidrio que puede causar alabeo. Markus Hausmann describe cómo la pinza de perforación paralela servoaccionada supera el reto de colocar las piezas de forma segura en la placa de perforación: “Si las probetas no se sujetan lo suficientemente bien en su sitio, los punzonados podrían estar torcidos o no ajustarse a los estándares de calidad especificados”.
Integración digital
Al tratarse de una planta piloto, el equipo de investigación de BASF suele establecer 20 configuraciones de prueba diarias en esta máquina. Eso significa que el programa de control de la célula tiene que adaptarse a diferentes materiales, geometrías de muestras, temperaturas y parámetros de procesamiento. Cada uno de los ajustes que se realizan se registra y documenta digitalmente.
Angelika Homes comenta: “A diferencia de nuestros anteriores sistemas MES, éste registra todos los aspectos de un ensayo y los resultados, lo que nos permite conocer cada una de las tomas. Estos datos son muy valiosos, ya que representan toda la secuencia de procesamiento y nos permiten sacar conclusiones más profundas sobre el rendimiento de los materiales en determinadas condiciones y sobre cómo podría procesarlos posteriormente un cliente”.
Resolver los retos de nuestro tiempo
Sin embargo, como ha descubierto BASF, el éxito también depende de que todos los socios combinen su visión industrial y de ingeniería y compartan sus respectivos conocimientos sobre automatización, procesamiento e integración. Reuniendo estos conocimientos, BASF, Sumitomo (SHI) Demag y H + S Automatisierung han desarrollado un sistema que lleva la producción de muestras de ensayo y los experimentos con materiales a un nivel completamente nuevo.
“A medida que BASF continúa intensificando sus esfuerzos para desarrollar productos y soluciones sostenibles para la industria, esta célula de moldeo por inyección automatizada ya está demostrando ser indispensable. La capacidad de llevar a cabo más de 4.000 configuraciones de prueba sistemáticas en polímeros de alto rendimiento con formulaciones complejas cada año y el seguimiento de los resultados digitalmente a través del sistema MES acelera este esfuerzo de innovación”, finaliza Markus Hausmann.