Ventilación de moldes, venting o salidas de gases, un problema a resolver (Parte 1)
José Ramón Lerma, dpto. técnico de Biesterfeld Ibérica
01/10/2019Cuando pregunto en mis seminarios a los asistentes "qué sucede si hacemos el siguiente experimento". Con una bomba de inflado de ruedas de la bicicleta, procedemos a tapar la salida del aire. Hacemos presión en el émbolo para comprimir el aire dentro de la bomba y hacerlo salir, ¿qué es lo que sucede entonces?
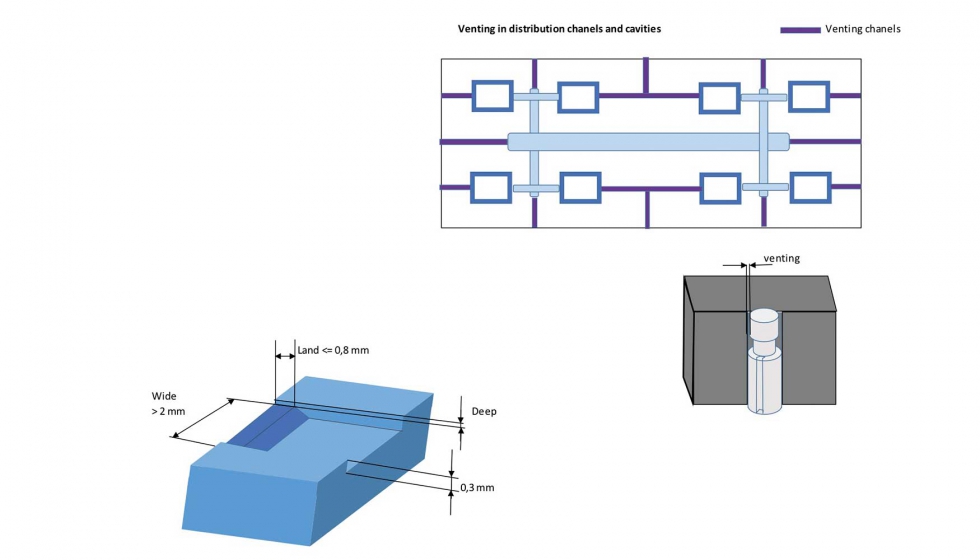
Imaginemos que hemos cerrado la bomba de inflado con un grifo que podemos regular.
En la media en que abrimos el grifo, nuestro esfuerzo para hacer salir el aire será menor. Es decir, la presión para desplazar el émbolo será inversamente proporcional a la sección de salida del aire en el grifo. A mayor sección de salida menor presión, y viceversa, a menor sección de salida de aire mayor presión necesaria.
Otro efecto que sucede y que pasa un poco más desapercibido, principalmente debido a que la presión que ejercemos en el aire dentro del pistón es baja, es que el aire al presurizarlo se calienta por efecto adiabático ya que las moléculas están muy juntas y chocan entre ellas.
Pues estos efectos, entre otros, se producen en el interior de la cavidad cuando la llenamos de polímero fundido y no tenemos un buen sistema de salidas de gases.
Venting
El aire que hay atrapado dentro de las cavidades (y colada o canal de distribución, esto lo comentaremos más tarde en este mismo artículo), al cerrar el molde y aplicar la fuerza de cierre, debe ser evacuado durante el llenado de las mismas, de lo contrario se producirá el mismo efecto que comentábamos en el párrafo anterior.
Para evacuar el aire durante el llenado, se mecanizan las llamadas ranuras de salidas de gases, en adelante 'venting'.
Estas ranuras de venting ayudan enormemente a facilitar el llenado de las cavidades y, como consecuencia, aumentar nuestra ventana de proceso. Esto es motivo suficiente para que las analicemos un poco más en profundidad.
Diseño del venting
Las dimensiones de las ranuras de venting son cruciales para un buen funcionamiento de las mismas.
La profundidad de la ranura o 'deep' (o altura) debe ser lo más grande posible siempre que no produzca rebabas o filtraciones de material indeseadas. Esta profundidad por tanto dependerá de diferentes aspectos, tales como geometría de la pieza (espesores que darán lugar a velocidades de inyección adecuadas al espesor), diseño de la construcción del molde, parámetros de inyección y por supuesto, tipo de material y fluidez del mismo.
En cuanto a la profundidad a aplicar en el mecanizado del molde, la mayor parte de los fabricantes de plásticos de prestigio pueden indicarnos sus recomendaciones para cada grado y tipo de material. Estas recomendaciones oscilan entre las 1,5 centésimas a las 3 centésimas de milímetro dependiendo del tipo de material.
Hay recomendaciones genéricas para materiales en diferentes libros, manuales, etc., pero deben ser tomadas como lo que son, recomendaciones. Es el fabricante de material quien nos puede recomendar para cada material concreto en función de su nivel de cargas de refuerzo, aditivos, etc., las medidas de profundidad adecuadas.
Factores de influencia
Espesor de la pieza
El espesor de la pieza es un factor muy importante para seleccionar la profundidad de la salida de gases ('deep del venting').
Se han realizado ensayos documentados en moldes con cavidades idénticas excepto en el espesor de la pieza ('Suhas Kulkarni') que prueban que cuanto mayor espesor de pared de las piezas, el 'deep' de las salidas de gases puede ser incrementado sin tener rebabas. Una de las explicaciones es que en espesores mayores, el polímero está menos forzado a fluir y se produce un menor 'shear' o cizalla, con lo que la viscosidad del polímero con menos 'shear' (debido a su comportamiento no newtoniano o 'shear thining') aumenta o no disminuye en gran medida, con lo que hay mucha menos tendencia a obtener flashes o rebabas. En el caso contrario, las paredes estrechas hacen que la cizalla aplicada en el material aumente generando una caída de la viscosidad y por tanto, con mayor tendencia a que se produzcan rebabas.
Es por tanto un factor a tener muy en cuenta. Podemos diseñar las profundidades, alturas o 'deep' de nuestras salidas de gases en función de los espesores variables de nuestra pieza. Así pues, en las zonas estrechas, junto a la entrada, cambios de espesor, en la profundidad de un nervio delgado, aplicaremos un 'deep' en la banda baja de las recomendaciones del fabricante del material, mientras que en zonas de espesores mayores, en el canal de distribución o colada, etc., aplicaremos la profundidad del venting en la zona alta de la recomendación del fabricante del polímero. También es interesante observar que las ranuras de ventilación que están situadas en dirección perpendicular al sentido del flujo de llenado permiten una mayor profundidad o 'deep' que las que se encuentran en dirección paralela al flujo.
Velocidad de llenado
Claramente, el volumen de aire que debe ser evacuado por cada salida de gases variará en función de la velocidad aplicada en la salida, es decir, el caudal de aire en cm3 por segundo afectará al diseño del sistema de ventilación de un molde. En procesos con altas velocidades de inyección, sea por paredes estrechas de las piezas, sea por largas longitudes de flujo, etc., es muy importante la correcta ubicación y dimensiones de los canales de ventilación.
Cuanto más velocidad de llenado, más necesidad de venting o salidas de gases adecuadas.
Dimensiones del canal de ventilación. Longitud. Land length
Cuanto mayor sea la longitud de la salida de gases mayor será la presión necesaria para hacer pasar el aire a través de ella y a su vez, cuanto mayor sea esta presión, mayor será la compresión del aire en la cavidad por tanto mayor será la presión de inyección necesaria para llenar la cavidad y también mayor la posibilidad de que se produzca el efecto diésel o incineración del material con posible desgaste de los aceros del molde, pulidos, texturizados, etc.
Además, las longitudes de canales de ventilación más cortos favorecen que no se acumulen restos del polímero en la ranura, mientras que los canales más largos favorecen el depósito de restos del monómero y del pack de aditivos en las superficies de la ranura.
Está consensuada la longitud del canal de ventilación idóneo en un máximo de 0,8 mm a 1 mm, mientras que otros manuales hablan de 0,03 pulgadas máximo. También se establece como media máxima 3 mm. En cualquier caso hay quien mecaniza las ranuras con una longitud de 2 a 3 mm y después, si aparecen efectos diésel o una presión de inyección excesiva puede reducirse esta longitud.
Dimensiones del canal. Anchura. Width
La anchura del canal de ventilación frecuentemente dependerá más del volumen de la cavidad. No es lo mismo una pieza del tamaño de un paquete de cigarrillos que una pieza del tamaño de un televisor. Se establecen medidas en la banda baja de la anchura en 5 a 6 mm para piezas pequeñas y de 10 a 12 mm para piezas grandes. En cualquier caso hay que tener en cuenta que anchuras menores provocan mayor frecuencia en las limpiezas y que la aparición de rebabas es más por la profundidad de la ranura de ventilación que no por la anchura.
Acabado superficial de la ranura de venting
Las ranuras de ventilación mecanizan con electroerosión. No debemos dejar el acabado de erosión en las ranuras, incluso aunque sea un acabado fino. Debemos pulir las ranuras con piedra para mejorar el acabado, pulir en la dirección de la salida de los gases es conveniente. Acabados de la superficie pulidos con pasta de diamante alargan la periodicidad de las limpiezas de mantenimiento.
Canales de ventilación secundarios
Se llaman canales secundarios de ventilación a aquellos que recogen el aire, gases y volátiles de la salidas de gases y los conducen hacia la atmósfera. Estos pueden ser más generosos en la profundidad y la anchura.
La anchura o 'width' de estos canales secundarios deben ser al menos de la anchura del canal de salida de gases. La profundidad puede llegar a ser de hasta 10 veces la del canal de salida de gases o 'deep'. Esto nos llevará a unas dimensiones de aproximadamente 0,3 mm.
Puede ser necesario en función del 'lay-out' diseñado de los canales de ventilación, más sistemas de canales para llevar finalmente los gases a la atmósfera.
Ventilación de canales de distribución o coladas
Es importante no dejar de lado el aire que queda atrapado en los canales de distribución o coladas y que debe ser evacuado también durante el llenado del molde. Este aire, si no lo hacemos correctamente, impulsado por el material fundido al entrar en el molde, acabará entrando en la cavidad y aumentando la necesidad de ventilación de la misma.
Por ello es fundamental mecanizar salidas de gases en las coladas. En cada giro de 90 grados del canal aprovechar para hacer salir el aire a la atmósfera. Esto facilitará el trabajo a las salidas de gases mecanizadas en la cavidad del molde.
José Ramón Lerma es autor del Libro Manual Avanzado de Inyección de Termoplástico, que tiene como objetivo ser, por un lado, una herramienta para la formación y, por otro, un manual de ayuda para todo el personal de una empresa de inyección de plásticos. El libro, comercializado por Plásticos Universales / Interempresas (libros@interempresas.net), consta de detallados casos prácticos, amplia información de moldeo científico y un ‘pendrive’ con 20 hojas de cálculo y herramientas de SC Molding o Scientific Injection Molding, además de optimización y definición de proceso, lo que lo hacen único en el mercado. Página web sobre Scientific Injection Molding: www.asimm.es
El volumen de aire que debe ser evacuado por cada salida de gases variará en función de la velocidad aplicada en la salida, es decir, el caudal de aire en cm3 por segundo afectará al diseño del sistema de ventilación de un molde
Cuanto más velocidad de llenado, más necesidad de venting o salidas de gases adecuadas
Está consensuada la longitud del canal de ventilación idóneo en un máximo de 0,8 mm a 1 mm, mientras que otros manuales hablan de 0,03 pulgadas máximo