¿Por qué no actualizar una inyectora de un solo componente a un sistema multicomponente (MVC)?
En tiempos de debilidad económica, las inversiones, con sentido de la proporción, son indispensables para garantizar la competitividad y atraer pedidos. Un fabricante de moldes en la industria de procesamiento de plásticos se lo pensará dos veces antes de comprar una máquina multicomponente para muestras especiales y pruebas de moldeado. Un proveedor de componentes de plástico para la industria del automóvil se enfrenta a esta cuestión cuando los pedidos disminuyen y las necesidades y exigencias aumentan. ¿Por qué no actualizar una máquina de moldeo por inyección de un solo componente a un sistema multicomponente (MVC)? ¿Por qué no preguntar a Windsor/Hanau qué es posible?
A lo largo de los años, Windsor ha modernizado un gran número de inyectoras (MMI) de la tecnología monocomponente a la multicomponente –con una solución muy atractiva desde el punto de vista económico: Las series PlugXPress - PxP 42 a PxP 1780– son unidades de inyección autosuficientes que prácticamente corresponden a una inyectora sin unidad de cierre. Una gran ventaja de Windsor son las adaptaciones especiales para los clientes: “Lo configuramos exactamente como encaja en la configuración del sistema”.
El resultado son sistemas individuales con añadidos individuales: El PxP se comunica con la inyectora a través de una interfaz. El cliente no tiene que cambiar nada en la máquina de moldeo por inyección, sino simplemente conectar el PxP, que funciona con un husillo de tres zonas de 16 a 105 mm, un controlador B&R y una pantalla táctil de 15 pulgadas. La unidad adicional PlugXPress para la inyección de varios componentes puede acoplarse a cualquier máquina, cualquiera que sea su procedencia.
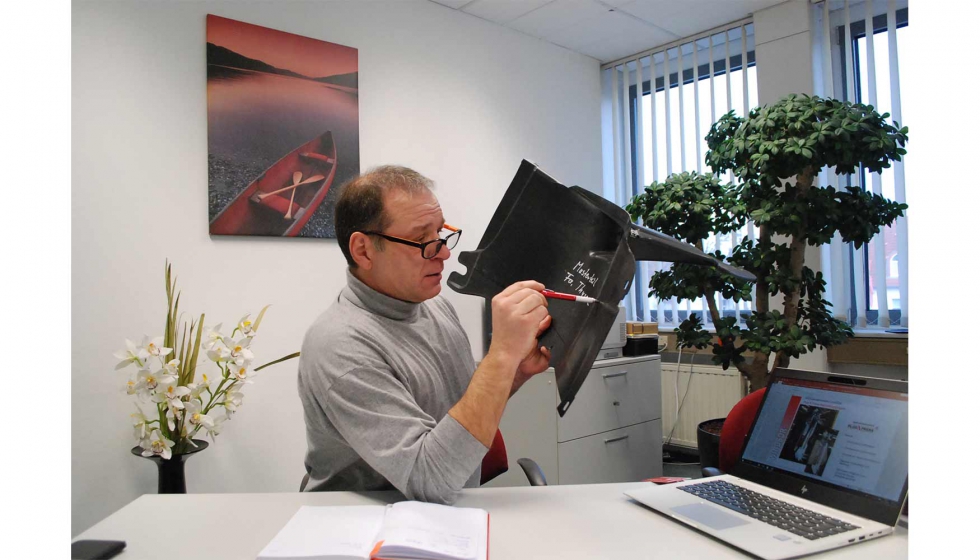
Andreas Janisch, jefe de producto Windsor.
“Uno de nuestros clientes lo usa para producir cepillos de dientes de tres materiales en cuatro colores diferentes”. La creciente demanda de 'MVC' y el éxito del PxP se reflejan en el hecho de que el número de unidades vendidas se ha más que duplicado en 2017 en comparación con el año anterior. “Nuestros puntos fuertes son las adaptaciones individuales, nos diferenciamos de nuestros competidores con un alto grado de flexibilidad. Cuando las soluciones estándar ya no funcionan, se utiliza PxP”. Y una vez que el PxP ha completado su pedido de una inyectora, puede –si lo desea– acoplarse a otras máquinas como una unidad móvil.
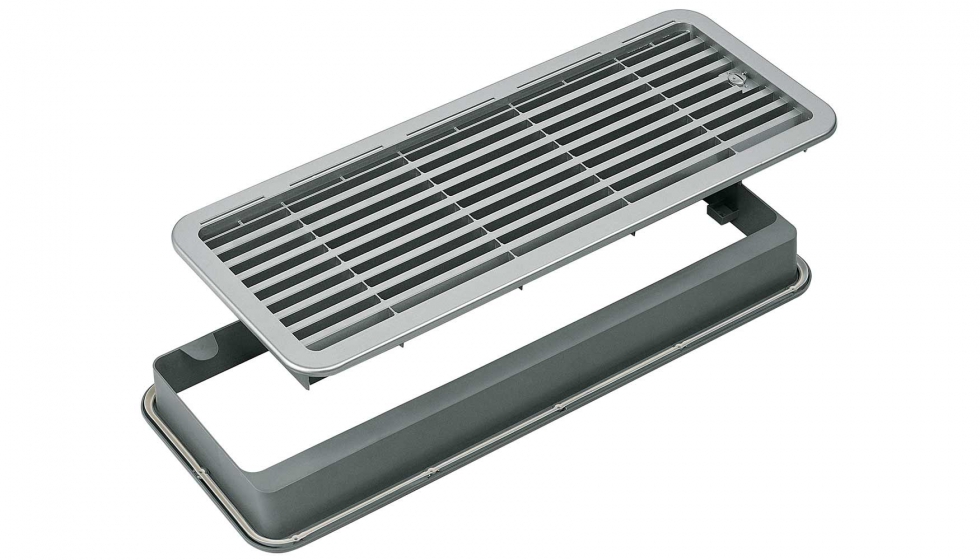
Rejilla de ventilación.
La serie PlugXPress tiene su origen en el concepto 'plug-and-play'; las unidades están listas para ser conectadas a la máquina. Como unidad de proceso autónoma, la PxP se comunica con la máquina a través de una interfaz estándar: “Todo es sencillo de manejar y simplifica enormemente el trabajo en la MMI”, subraya Andreas Janisch, director de Producto de Windsor. A pesar de su sencilla aplicación, la serie PxP es “estado del arte”: Según Janisch, para este año está prevista una actualización técnica con la que el controlador B&R funcionará a través de un protocolo abierto.
Las unidades de inyección no se simplifican, sino que se trata de una máquina móvil de inyección sin unidad de cierre que se adapta a cualquier MMI –independientemente de su origen y marca– y, por lo tanto, introduce en el molde el segundo componente o componentes adicionales: “PxP no es una versión reducida, sino una unidad totalmente funcional”, dice Janisch.
Los materiales de alta resistencia al desgaste para los husillos son estándar. Se procesan prácticamente todos los termoplásticos comunes y las mezclas especiales, incluidas las poliamidas con fibras de vidrio y los plásticos de ingeniería. “Ofrecemos un husillo estándar de tres zonas, pero también unidades especialmente adaptadas. Ofrecemos un total de nueve PxP básicos, cada uno con tres husillos”, explica Janisch.
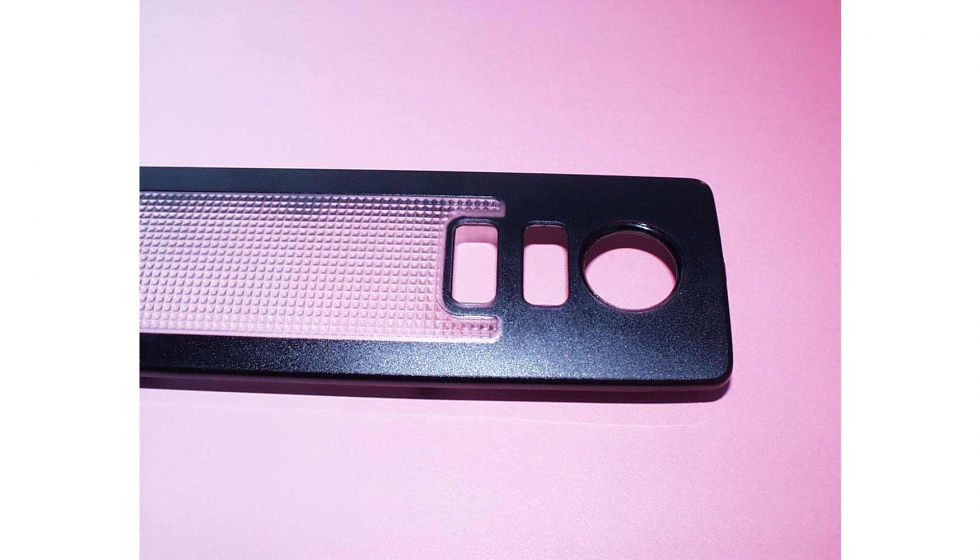
Tapa transparente blanda incrustada.
¿Cómo funciona el moldeo por inyección en el PxP?
“Primero necesitamos una pieza premoldeada, la primera inyección de la inyectora –en el proceso estándar para la pieza base– luego los otros componentes se moldean por inyección utilizando PxP”, explica Janisch. La máquina emite una señal tan pronto como se termina la preforma. Esta es la señal de inicio para la primera de las 'n' PxPs.“Los productos se registran con la máxima precisión: El PxP tiene una memoria para 1.000 programas, y una memoria USB se puede utilizar para almacenar mucho más. La ventaja del PxP es su variabilidad, lo que supone un enorme ahorro de costes para los usuarios. Janisch:”Un punto de partida típico es un máquina de inyección estándar.
El usuario produce sus piezas hasta el final del pedido, luego llega un nuevo pedido y pueden surgir problemas con diferentes moldes, especialmente cuando se trata de productos multicomponentes. La inversión en una máquina de moldeo por inyección varios componentes sería entonces necesaria. No es así con PxP: “Una actualización de la inyectora existente es posible por un tercio del precio de una máquina MVC”. De este modo, se pueden procesar varios pedidos de forma flexible. Especialmente después de la crisis económica y financiera de 2008/2009, este ahorro de costes a través de PxP benefició a muchas empresas de la transformación de plásticos.
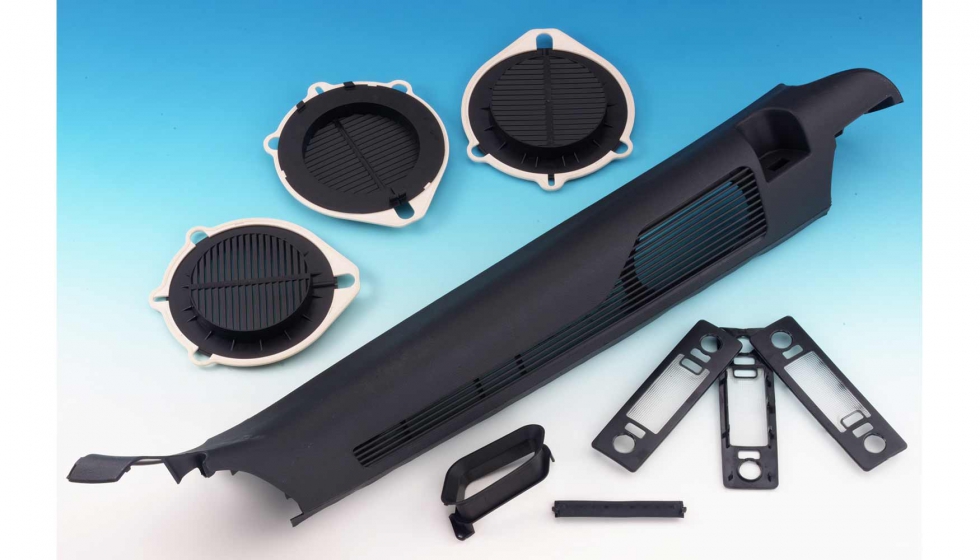
Automoción.
Hoy en día, las empresas se benefician de PxP –nueve unidades con tres diámetros de husillo cada una con pesos de 20 gramos a 4 kilogramos– además de unidades especiales que se pueden añadir fácilmente a la máquina.
¿Qué fabricantes ya trabajan con éxito con la serie PxP? Por ejemplo, una empresa suiza utiliza PlugXPress Plus 4 para fabricar cepillos de dientes de varios componentes. La pieza premoldeada es de PP blanco. A continuación, un componente blando y un componente de acabado. ¡Todo se hace en una sola máquina en un total de cuatro colores diferentes!
Janisch explica: “En el pasado, la empresa tenía que producir primero un millón de cepillos de dientes azules, seguidos de un millón de verdes, un millón de amarillos y un millón de rojos. Ahora los cepillos de dientes multicomponentes en cuatro colores vienen directamente de la MMM, a la línea de montaje y a la línea de envasado. Se producen cuatro cepillos de dientes diferentes en un ciclo. ”En comparación, se trata de una revolución y proporciona un enorme ahorro de tiempo y costes con una calidad constante", subraya el jefe de producto de Windsor. Se utiliza una máquina de 350 toneladas con cuatro PxP42 y un husillo de 18 mm. Los pesos por inyección para el segundo componente son de unos 30 gramos. Con la unidad de control independiente de cada unidad PlugXPress Ag, se pueden controlar/regular y supervisar diversos equipos adicionales, como núcleo de tracción, plataformas giratorias, sistemas de canal caliente y funciones en cascada.
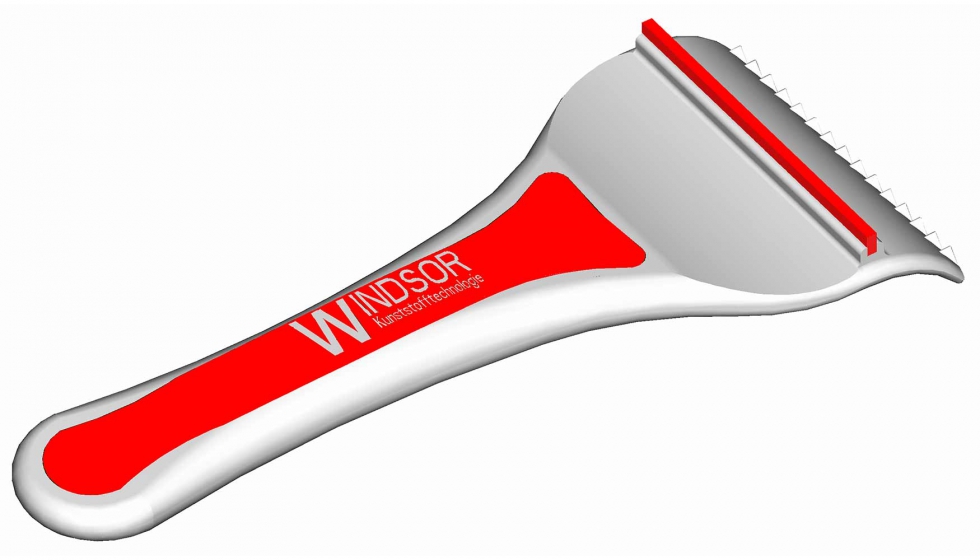
Rascador de hielo.
Otra aplicación PxP
Un proveedor de la industria automovilística fabrica carcasas para vehículos alemanes de gama media. Tarea: después del primer proceso de inyección, se inyecta un componente blando en el borde. Y había problemas de espacio. Era necesaria una integración especial en la máquina. Solución: un PxP 257 montado entre los largueros de la máquina y la puerta trasera de seguridad, cuerpo base de PP con labio de estanqueidad de TPE - peso inyectado 40 gramos.
Para otro fabricante los parachoques se fabrican con la ayuda de PxP. La unidad de inyección, en la versión de 45 grados, tenía que estar apoyada en la columna (larguero) para poder conectarla al molde. El diámetro del husillo en la versión de 45 grados puede ser de hasta 43 mm. En otro producto de automoción, se atornilla un bastidor o un carril de deslizamiento en la máquina de inyección: la unidad PxP puede “desplazarse” con el lado móvil del molde.
En la fase de proyecto de una conocida empresa sueca, la producción de palets con recubrimiento antideslizante está en marcha: se aplican almohadillas antideslizantes a los palets mediante moldeo por inyección, ¡todo en un solo molde! Una máquina MVC se utiliza para el cuerpo básico y los componentes blandos - PxP es responsable de estos últimos. Un juego de husillos de 105 mm funciona en la máquina de 2300 toneladas y proporciona un peso de inyección de 3,5 kilogramos.
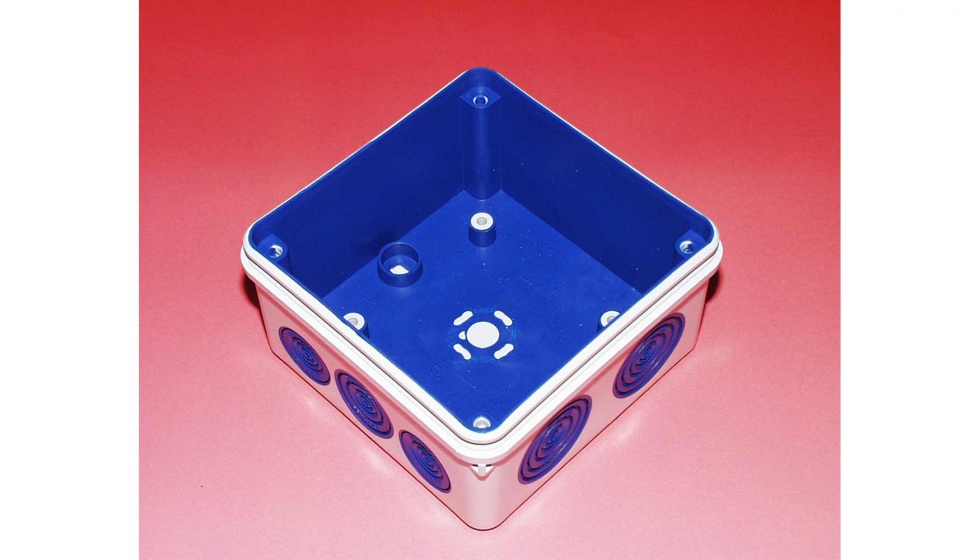
Caja de conexiones con incrustaciones blandas.
Las unidades PxP también se utilizan para materiales compuestos: por ejemplo, para el acabado interior de las puertas de los coches. “Anteriormente, las alfombras de fibra tenían que ser presionadas y perforadas. Ahora todo va de una sola vez”, indica Janisch. “Las piezas en bruto entran en la prensa, se hornean, se perforan y, en el segundo paso, se inyectan en la misma máquina los nervios de refuerzo y los accesorios de tornillo. Suministramos el paquete completo: las prensas no tienen que ser cambiadas, el control de la válvula de cascada y el control de la temperatura del canal caliente están disponibles como una oferta completa con husillos de 50/55 mm”. Conclusión: este fabricante no tiene que preocuparse por el moldeo por inyección, puede empezar la producción directamente sin tener que adquirir nuevos pasos del proceso.
Una característica única de la serie PxP, con la que los transformadores de plásticos pueden prepararse para tiempos y tareas especiales, es su eficacia y movilidad con la máxima calidad. Gracias a sus versátiles posibilidades de aplicación e instalación, la unidad PxP es también indispensable para los fabricantes de moldes que desean probar productos de varios componentes y producir pequeños lotes en rápida sucesión sin tener que invertir en un gran parque de máquinas.
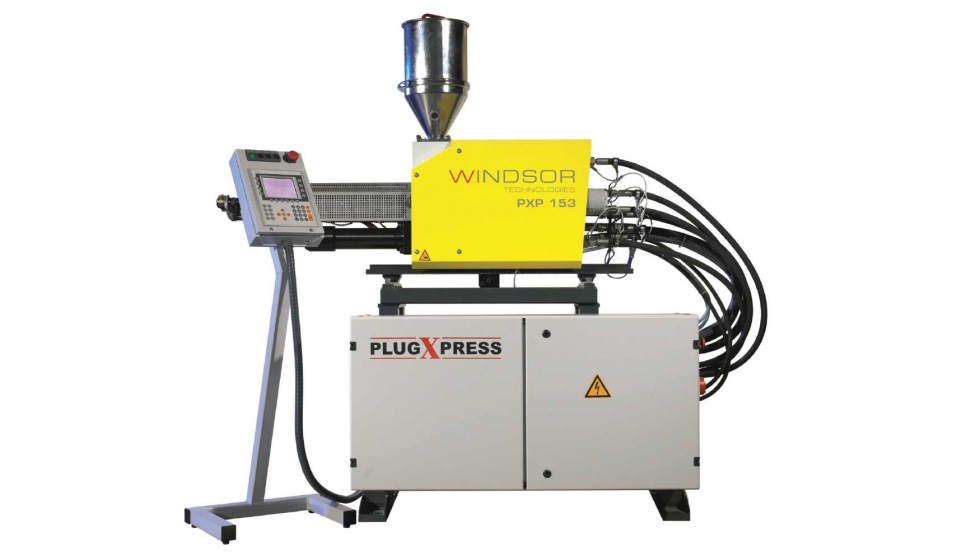
PlugXPress.
Acerca de Windsor
En 1945, poco después de la fundación de la empresa, R. H. Windsor Ltd., Chessington (Reino Unido), construyó una de las primeras máquinas de moldeo por inyección con accionamiento hidráulico. 1959 Fundación de R. H. Windsor GmbH en Frankfurt/Main. Durante la K 1963, la empresa presentó el “SP12” con accionamiento totalmente hidráulico, un producto pionero de esta tecnología. En 1969, el grupo inglés de ingeniería mecánica GKN se hizo cargo del grupo Windsor. En 1972, GKN Windsor GmbH construye en Bischofsheim una fábrica de última generación para la construcción de máquinas de moldeo por inyección. Klöckner AG, Duisburg, adquiere el grupo Windsor de GKN en 1982. Hasta el cierre de la planta de producción en 1994, Windsor desarrolló máquinas de moldeo por inyección completamente hidráulicas con fuerzas de cierre de hasta 75.000 kN, incluyendo grandes máquinas verticales de tres columnas con fuerzas de cierre de hasta 10.000 kN, que se utilizaban principalmente en la tecnología de fusión de machos.
Desde 1994, la empresa se ha concentrado en el servicio postventa y en los desarrollos en el área de los multicomponentes. La unidad auxiliar PXP, que se introdujo en 1999, tiene una gran demanda en la actualidad. Especialmente en el sector de la automoción, estas unidades auxiliares especialmente desarrolladas se utilizan para el procesamiento de los tableros de fibra de la NFPP. Desde 2007, la empresa, que tiene su sede en Hanau desde 1994, pertenece al Grupo Windsor, Inc, Mason/OH, EE UU. Windsor es socio comercial oficial de JSW, The Japan Steel Works Ltd., Tokio, desde 2007 y de FCS, Fu Chun Shin Group, Tainan, Taiwán, desde 2016. Windsor también vende varias unidades hidráulicas de fabricación propia, así como las unidades de inyección auxiliares flexibles PlugXPress. Windsor colabora con varias agencias en Europa.