Construcción del nuevo puente de arco metálico de Walterdale (Canadá)
Pilar Blanco Bailo, directora técnica UNE Carreteras, Puentes y Obras Especiales, Acciona Construcción
Laura Granda San Segundo, Gerente Técnico de Proyecto, Acciona Construcción
15/04/2019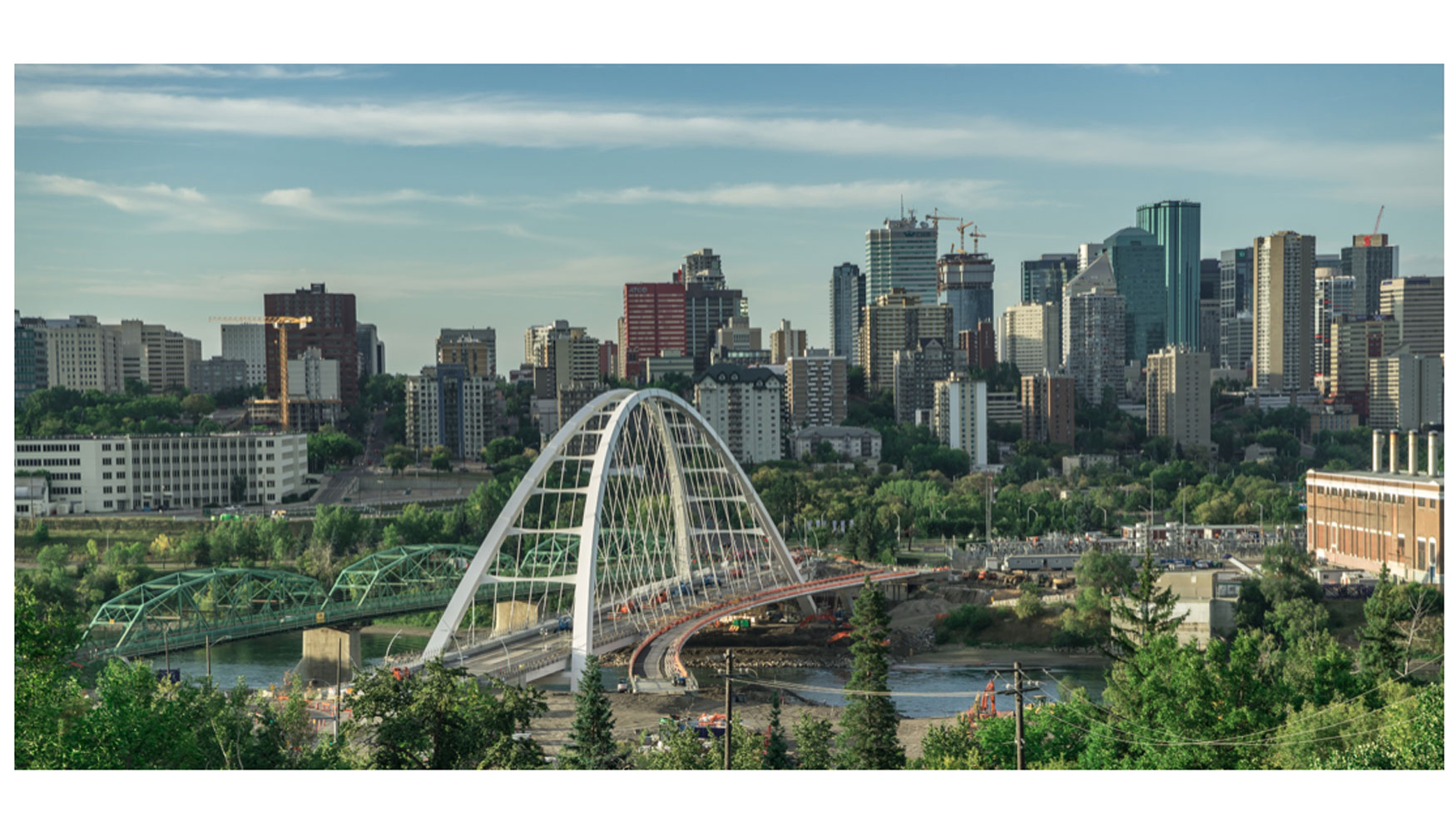
Introducción
En 2013, la ciudad de Edmonton (COE) encargó el proyecto de sustitución del puente de Walterdale al consorcio de empresas COWI International y Dialog Engineering para la realización del diseño arquitectónico detallado del nuevo puente.
La construcción del nuevo puente se adjudicó a Acciona Pacer Joint Venture (APJV), un consorcio formado por Acciona Infrastructure Canada Inc. y Pacer Mamisiwin Corporation.
El departamento técnico de Acciona colaboró estrechamente con Allnorth Consultants Ltd., empresa contratada por APJV como ingeniería responsable del montaje, para llevar a cabo los procedimientos de montaje de la nueva estructura.
El puente, que cruza el río North Saskatchewan, mide 230 metros de largo, tiene un arco de acero de 43 metros de altura, formado por dos costillas inclinadas hacia dentro, que soportan un tablero mixto de hormigón y acero de 22,40 metros de ancho, formado por dos vigas prismáticas principales que cuelgan del arco de acero mediante 32 péndolas. Una pasarela de uso compartido, peatonal-bicicletas, de sección rectangular variable metálica se conecta al arco mediante 14 péndolas inclinadas y al tablero a través de 8 vigas transversales metálicas que se conectan rígidamente a las vigas principales longitudinales. El peso total de la estructura metálica está en torno a las 5.000 toneladas. Aparte se han utilizado otras 500 toneladas de estructura metálica temporal para el izado y el proceso constructivo.
La construcción del puente se llevó a cabo en cuatro fases principales:
- Cimentación.
- Instalación del arco.
- Instalación del tablero.
- Instalación de la pasarela de uso compartido, peatones-bicicletas. SUP.
Proceso constructivo
Los procedimientos utilizados para el montaje de la estructura permanente tenían tres objetivos principales:
- Garantizar la seguridad y estabilidad estructural en cada etapa de la construcción.
- Completar la estructura permanente cumpliendo con los límites establecidos en los planos de diseño y en los documentos contractuales. Las tolerancias eran mínimas y los esfuerzos a los que era necesario dejar el arco y el tablero a tiempo cero y sin sobrecargas eran próximos al estado permanente sin haber sufrido ninguna fase constructiva. Los esfuerzos de bloqueo debían de ser casi nulos.
- Geometría final, tolerancia de 25 mm en alzado.
- Tensiones de cable de las péndolas.
- Minimizar todos los riesgos potenciales tanto para el programa de obra como para el presupuesto.
1.- Cimentación
La cimentación está diseñada para cargas horizontales, siendo ésta la que aguanta todos los empujes del arco sobre el terreno.
1.1.- Recintos estancos (Cofferdams)
Diseño original - pilotes secantes con anclajes de amarre
El diseño original contemplaba un recinto estanco de mayores dimensiones (22 m x 22 m) creado con pilotes secantes reforzados con anclajes de amarre.
Análisis de valor de los recintos estancos - Nuevo diseño con tablestacas
Se presentó una solución alternativa con tablestacas y una superficie reducida a 15 m x 15 m.
Desafíos:
- Estado de la explanada. La zona de cimentación estaba formada por material de relleno industrial. Una vez que se llegó a la roca, la velocidad de descomposición de la misma generó complicaciones.
- Instalación de un sistema de drenaje/desagüe basado en el bombeo de agua de un recinto estanco a otro en la misma margen del río, creando un ciclo que evitaba que el agua se vertiera en el río, evitando así la contaminación.
- El nivel freático ejerció una presión hidrostática por debajo de la base de los recintos estancos. Para evitarlo, se colocaron pozos de alivio y de desagüe.
- Gran presión hidrostática acumulada en el material de esquisto, poco permeable.
- El lecho rocoso expuesto se mostró muy sensible al ambiente, lo que complicó el llegar a la cota final, dando lugar a durmientes más gruesos que los diseñados en ciertos puntos.
- Seguimiento del asentamiento potencial del recinto estanco.
- Proximidad al puente existente en servicio.
1.2.- Micropilotes
Desafíos:
- Diseño y planos de taller.
- Diseño y realización de las pruebas de estanqueidad de los micropilotes.
- Estado de la explanada. Colapso del suelo, gas.
- Pozos de alivio inclinados.
- Asentamiento de lechada inyectada debido al nivel freático / nivel / presión - perforación - lechada - nueva perforación.
- Instalación de micro-pilotes bajo presión de agua subterránea (recintos estancos SW).
- Procedimiento de rehabilitación de micropilotes para instalación en circunstancias muy desfavorables.
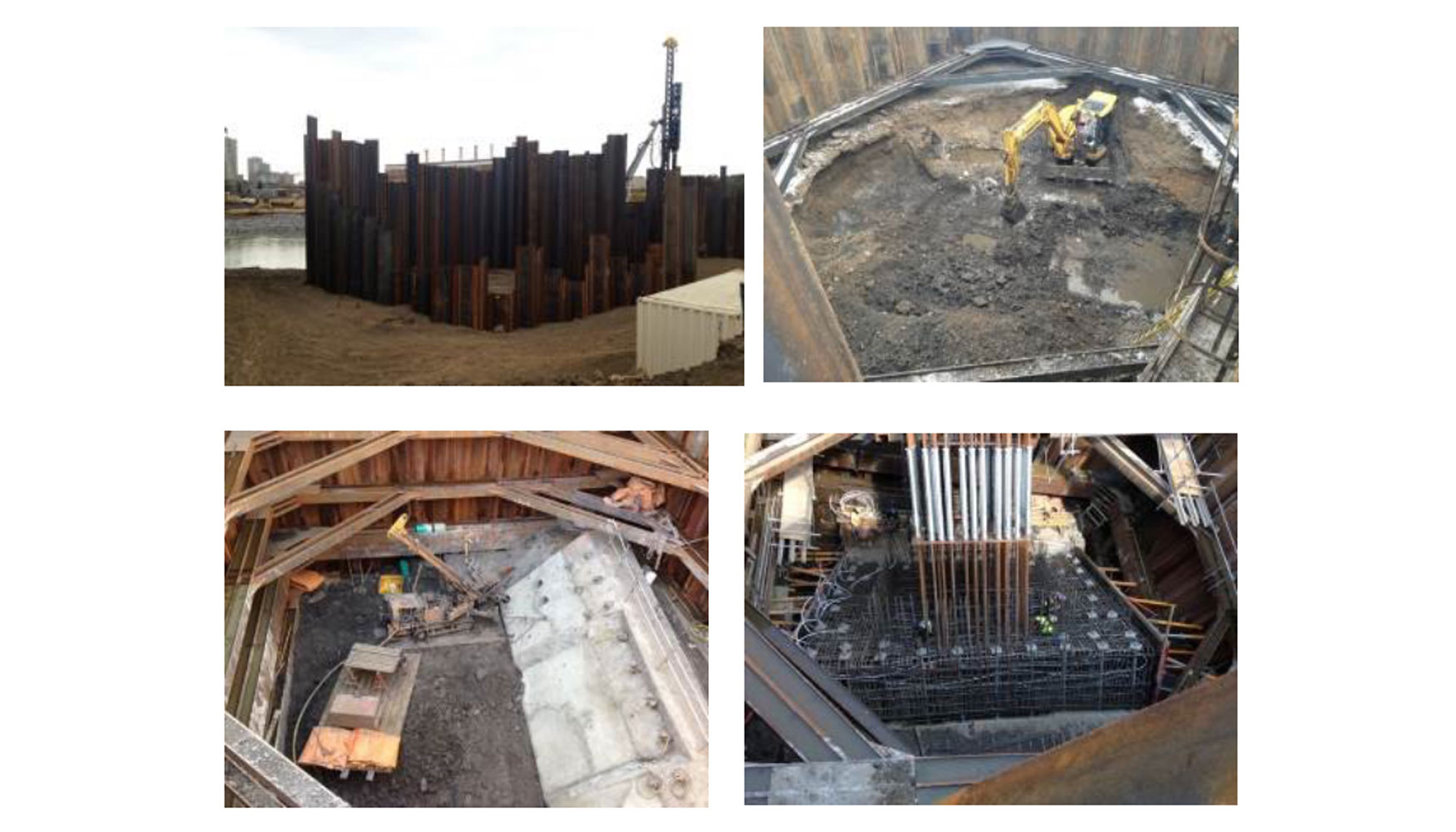
1.3.- Bloques de anclaje
Situados a 20 m de profundidad bajo el nivel del terreno, cada bloque de anclaje estaba formado por 600 m3 de hormigón y 100 toneladas de acero pasivo.
Desafíos:
- Unión a los micropilotes.
- Dificultad en la alineación de las barras de anclaje por su gran rigidez.
- Dificultad de colocación de barras de refuerzo por la su gran densidad y dificultad de acceso.
- Dificultad en el control topográfico de los elementos de anclaje.
- Plan de control térmico del hormigón en masa: instalación de tuberías de refrigeración.
- Diseño de encofrado basado en una pendiente inclinada y girada.
- Estudio de consistencia y características del hormigón y su puesta en obra, a muy bajas temperaturas.
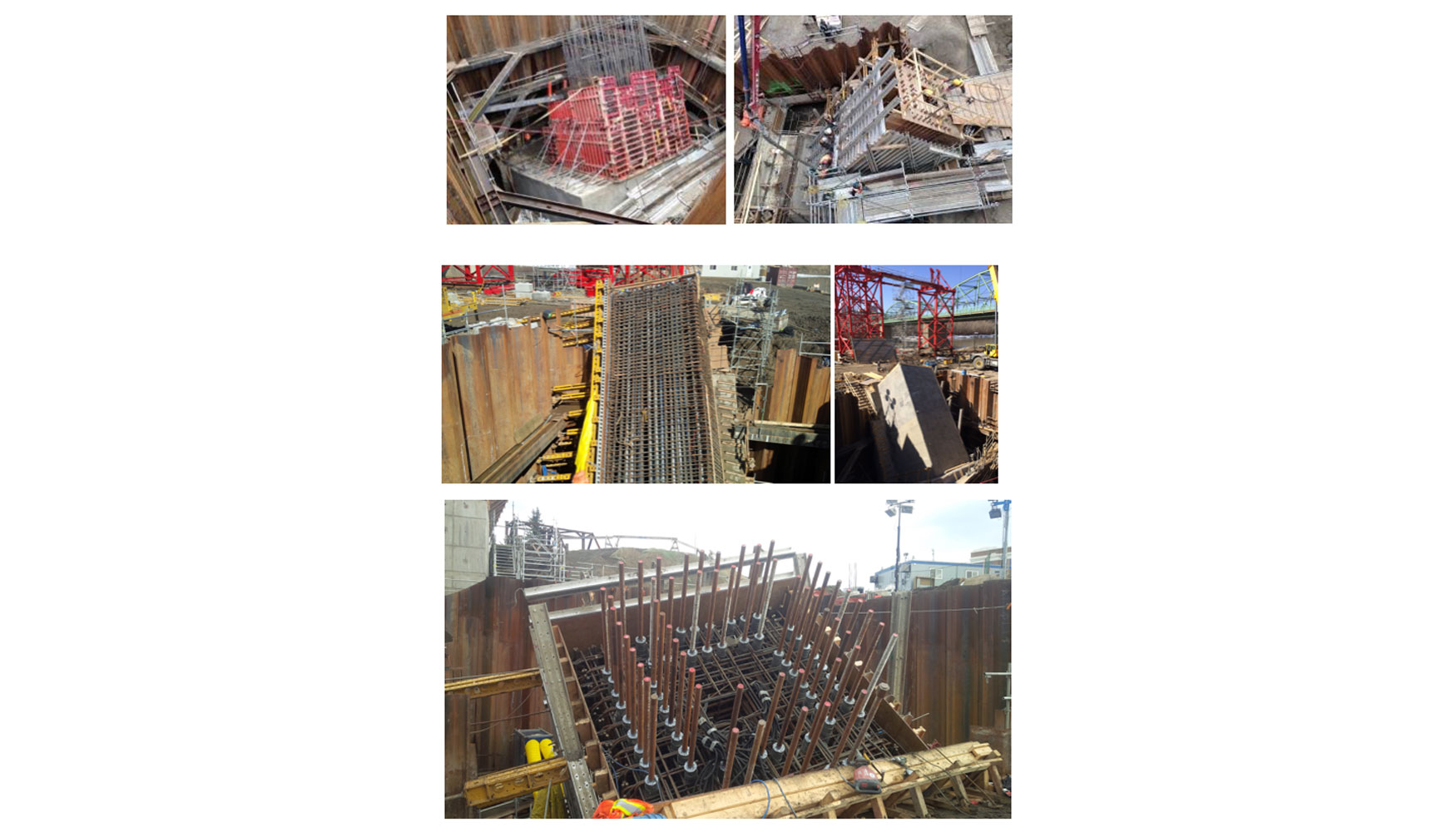
2.- Montaje del arco
El procedimiento diseñado para la construcción del arco fue, desde el punto de vista técnico, un gran reto.
El montaje del arco se puede dividir en cinco fases:
- Montaje del arco central de 86 m en la berma sur.
- Deslizamiento y navegación del arco central hasta su posición definitiva.
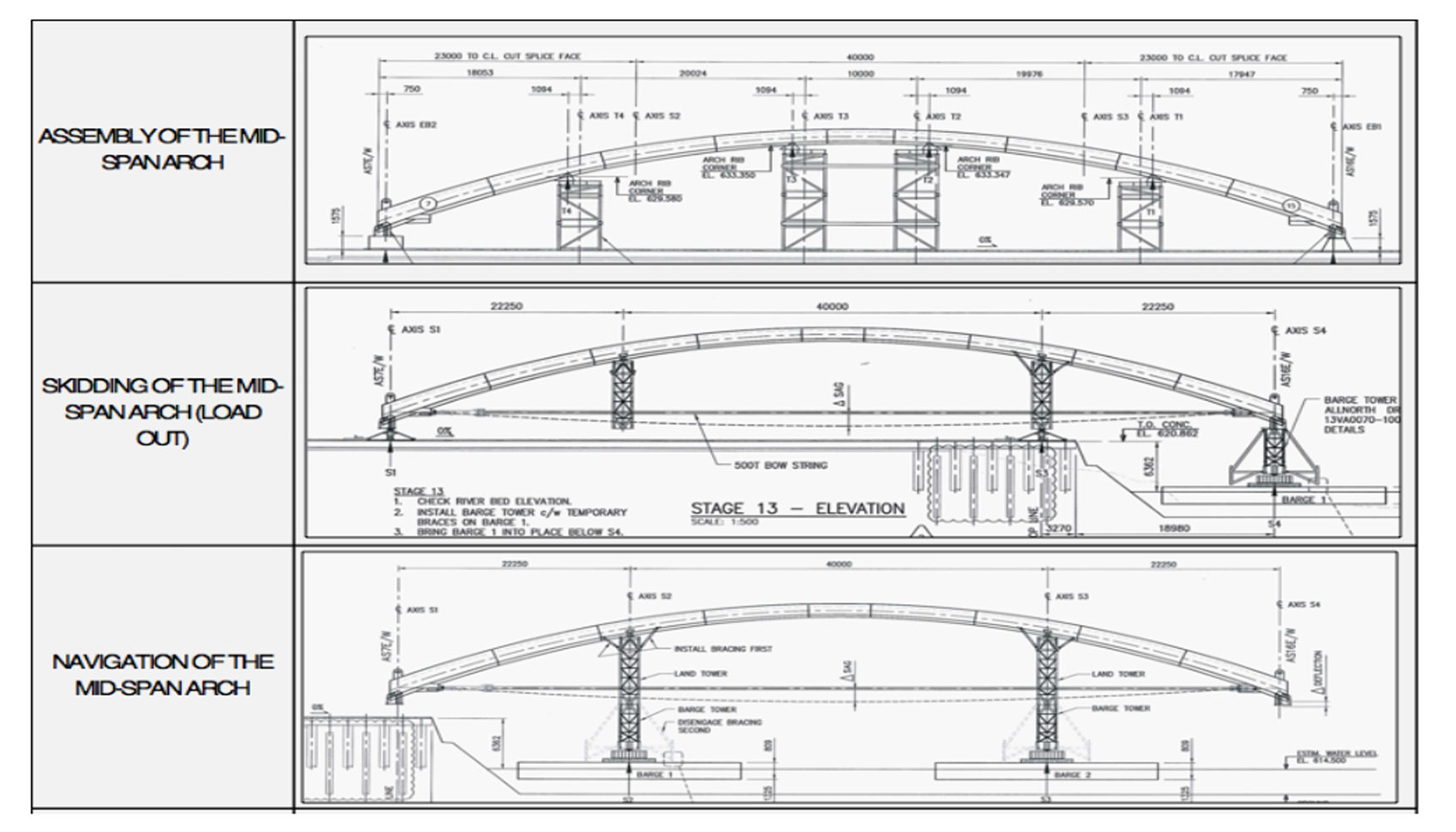
- Montaje en las bermas en dos fases del arco restante, como muñones de espera para completar el arco.
- Realización de dos izados para llevar el arco a cota.
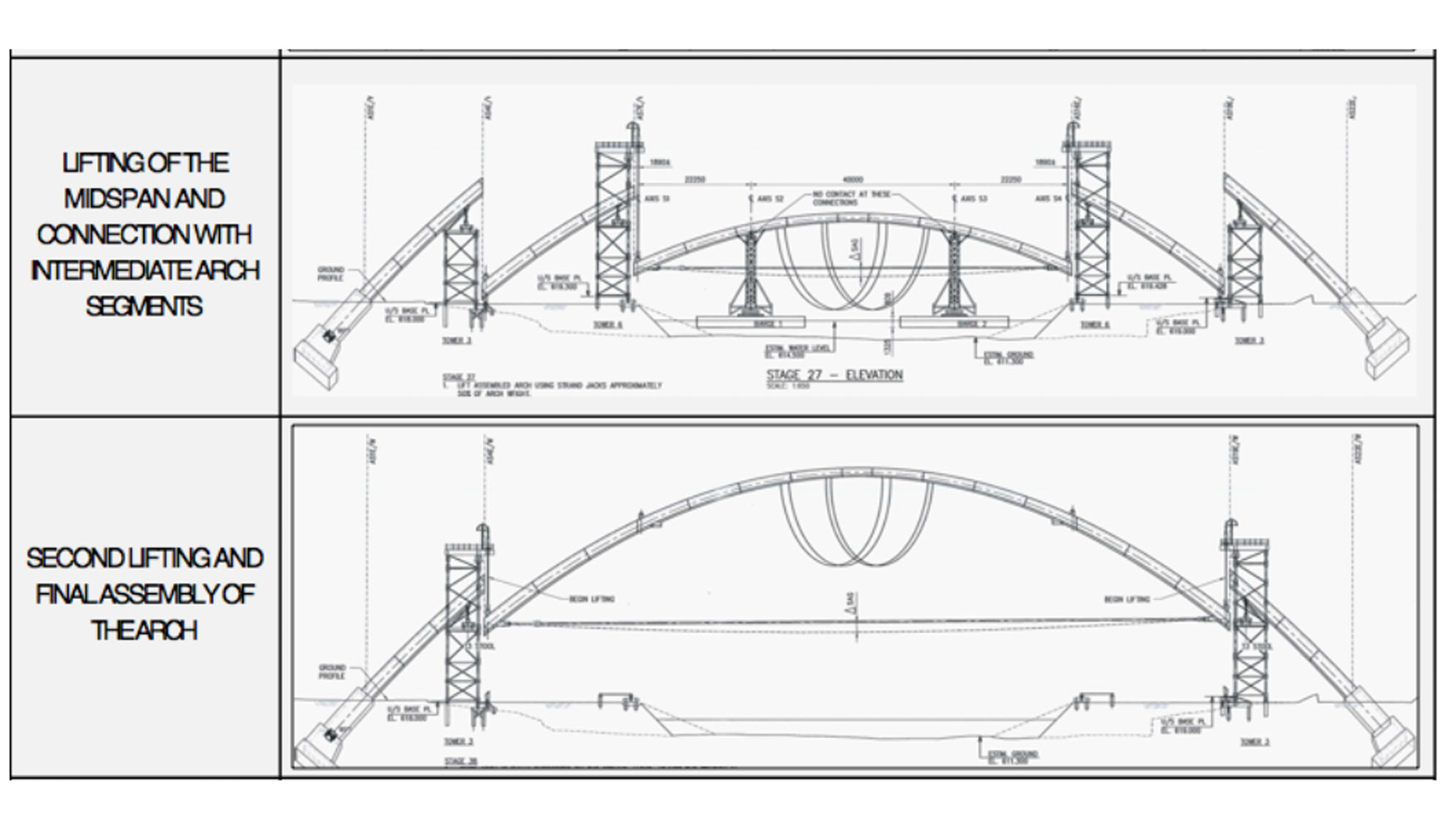
- Unión del arco a los bloques de anclaje.
Montaje del arco central de 86 m en la berma sur
En esta fase se construyó el arco central, de 86 m de longitud, en un parque de montaje, especialmente preparado para ello, situado en la berma sur. Cada arco constaba de 21 dovelas individuales. Cada dovela tenía una longitud de 10 m aproximadamente, y la más pesada alcanzaba las 120 toneladas. El peso del conjunto estaba en torno a las 1.000 toneladas. Las uniones entre dovelas de esta zona central fueron diseñadas atornilladas.
Para la realización del montaje, las dovelas se apoyaron en unos castilletes provisionales. Una vez completado el montaje, se tensaron los arcos atirantados a modo de bow-string con cables y gatos huecos hasta que, como resultado de esta acción de tirante inferior, toda la zona central del arco se descolgó de los castilletes quedando apoyada en unos patines de lanzamiento o ‘skidshoes’ situados en cada extremo de cada arco. Una vez transferida la carga del peso del arco a los soportes temporales de empuje, se retiraron los castilletes provisionales de montaje.
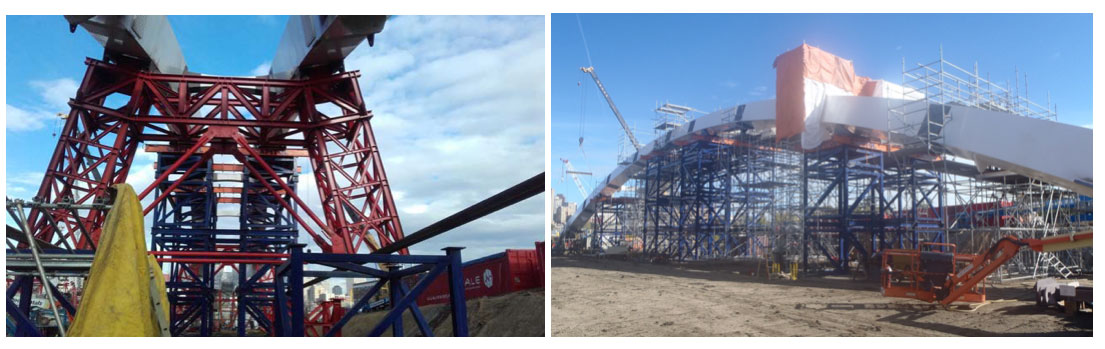
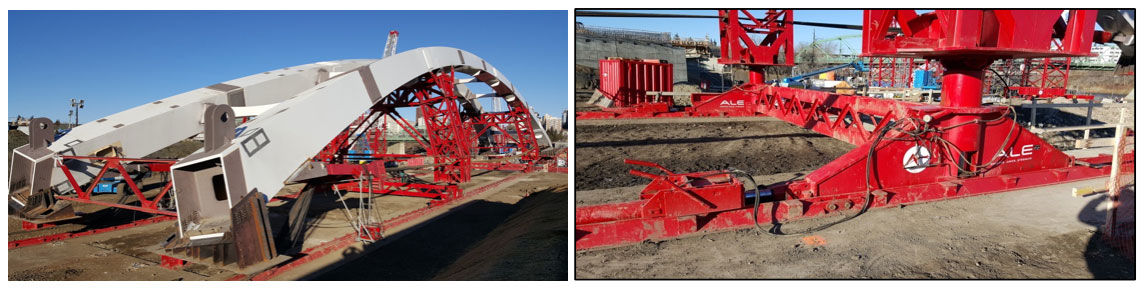
Deslizamiento y navegación del arco central hasta su posición definitiva
El siguiente paso consistió en lanzar el conjunto del arco sobre un camino de rodadura preparado para ello hasta las barcazas. Este consistía en unos patines de deslizamiento que se deslizaban sobre unos raíles de teflón colocados sobre una losa de cimentación preparada para tal fin. Los patines tenían una capacidad de 500 toneladas cada uno.
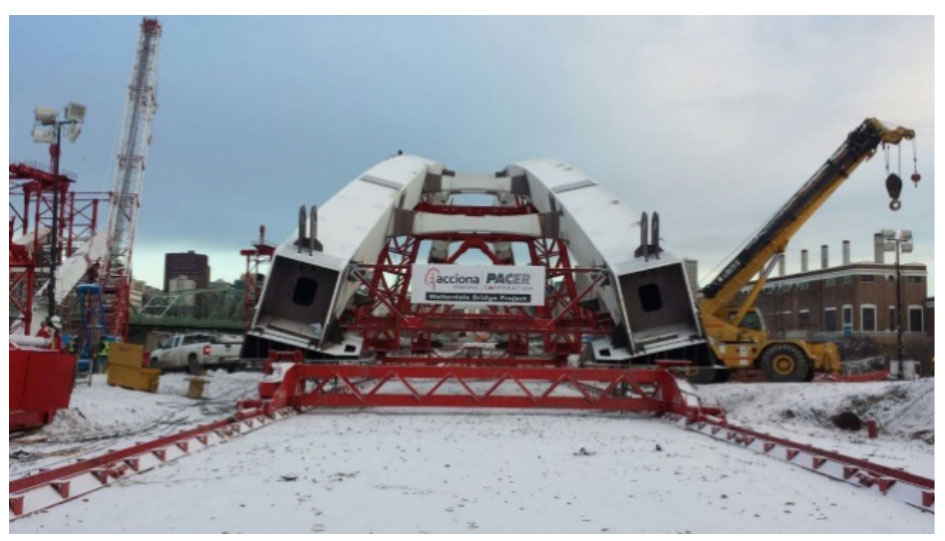
Para la navegación se utilizaron dos barcazas de tipo modular, de 36x21 m cada una, que se dispusieron al final de la zona de lanzamiento. En ellas se instaló un sistema de lastrado de 720 m3 por hora. Un equipo altamente experimentado de ALE Heavylift se encargó de operar las barcazas y de realizar los trabajos de deslizamiento del arco hasta estas últimas.
En el centro de cada una de las barcazas se instaló una torre de recepción del arco. Cada torre estaba conectada al arco por una conexión atornillada con capacidad a tracción y momentos y la parte inferior de la torre contaba con una conexión articulada fija a la barcaza para no transmitir momentos a esta. Esta configuración minimizó el potencial de vuelco de la barcaza y permitió dimensiones de barcaza más eficientes.
En una primera fase el conjunto del tramo central se cargó en su extremo más cercano al río en una primera barcaza a medida que seguía deslizándose por el camino de rodadura mediante los gatos horizontales de los patines. La transferencia de carga a la barcaza se realizó ajustando el izado mediante gatos en tierra y lastrando las barcazas.
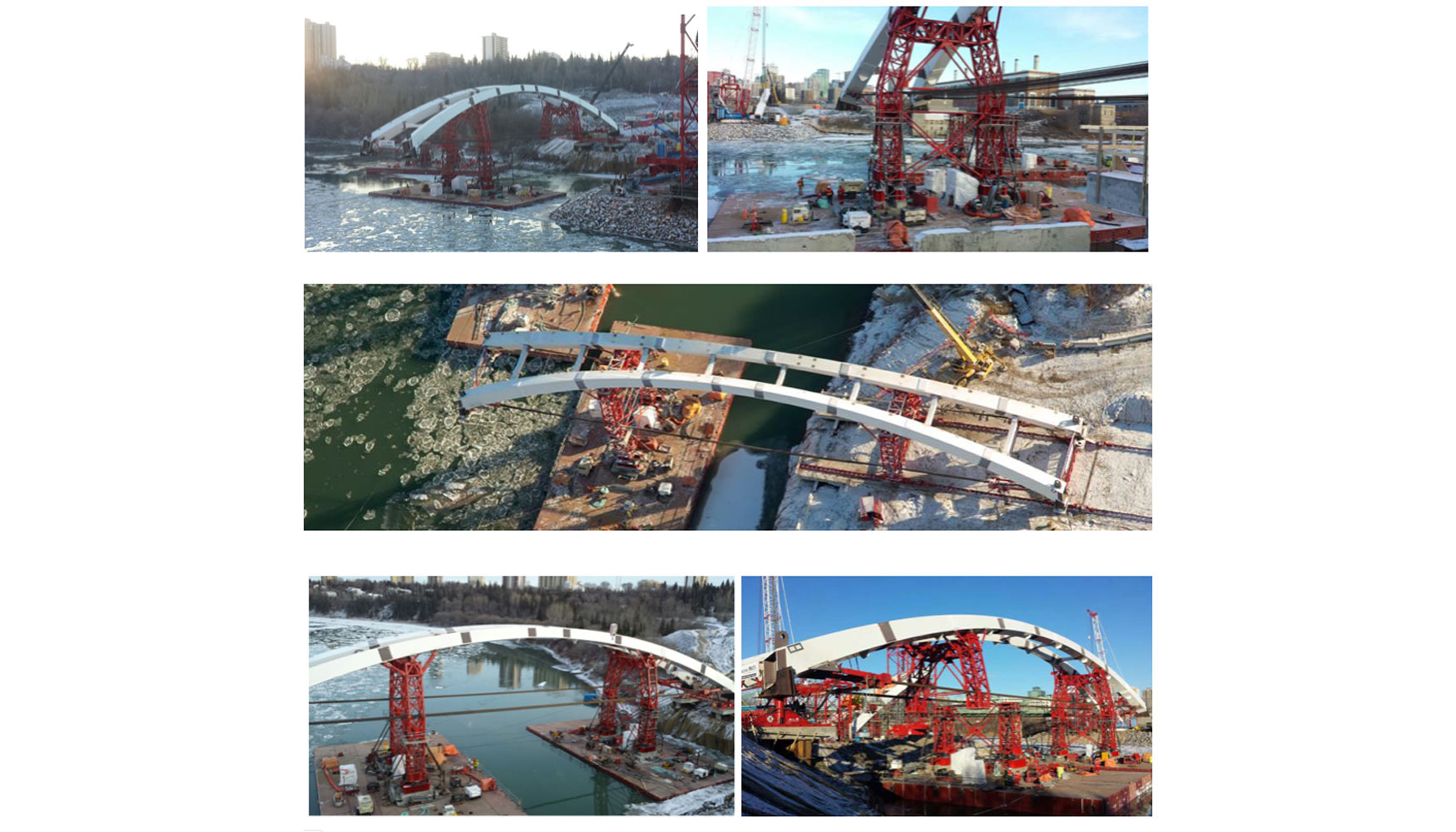
Una vez instalado el conjunto sobre las dos barcazas, se comenzó la navegación del arco como un conjunto rígido por medio de un sistema de cabestrantes anclados a cada barcaza. Cada barcaza contaba con dos cabestrantes principales, con una capacidad de 20 toneladas cada uno, y dos cabestrantes auxiliares de 10 toneladas cada uno para la estabilidad y para la navegación. Fue necesaria casi una semana para desplazar el arco desde la ubicación inicial de montaje hasta la alineación definitiva.
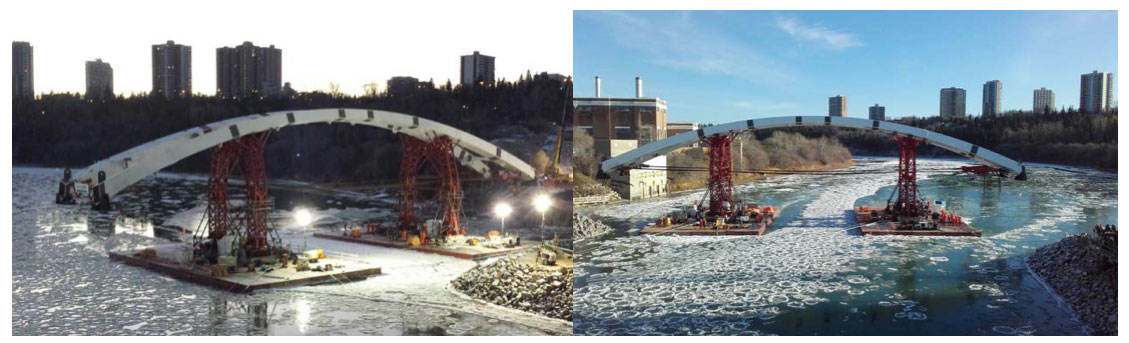
Efectuar una maniobra de este tipo en un río tiene un riesgo inherente por la naturaleza dinámica del sistema ribereño. El año en el que se llevó a cabo la operación, el río registraba los niveles de agua más bajos de su historia. Por ello, hubo que dragar el río para asegurarse de disponer del suficiente espacio debajo de la quilla para poder realizar la maniobra. Por otro lado, el invierno llegó con antelación y la semana anterior a la realización de la operación comenzó a helarse el río. Para hacer frente a estos desafíos adicionales se realizaron distintas pruebas y se contó con la presencia de una máquina de dragado y una rompedora de hielo a lo largo de toda la operación. Cuando el conjunto llegó a su emplazamiento definitivo, se colocó el arco sobre unos soportes temporales apoyados en los encepados de las torres de izado temporales en los extremos de cada arco. Para la realización del transvase de cargas fue necesario el lastrado de las barcazas mediante el bombeo de agua, operación que llevó toda una noche.
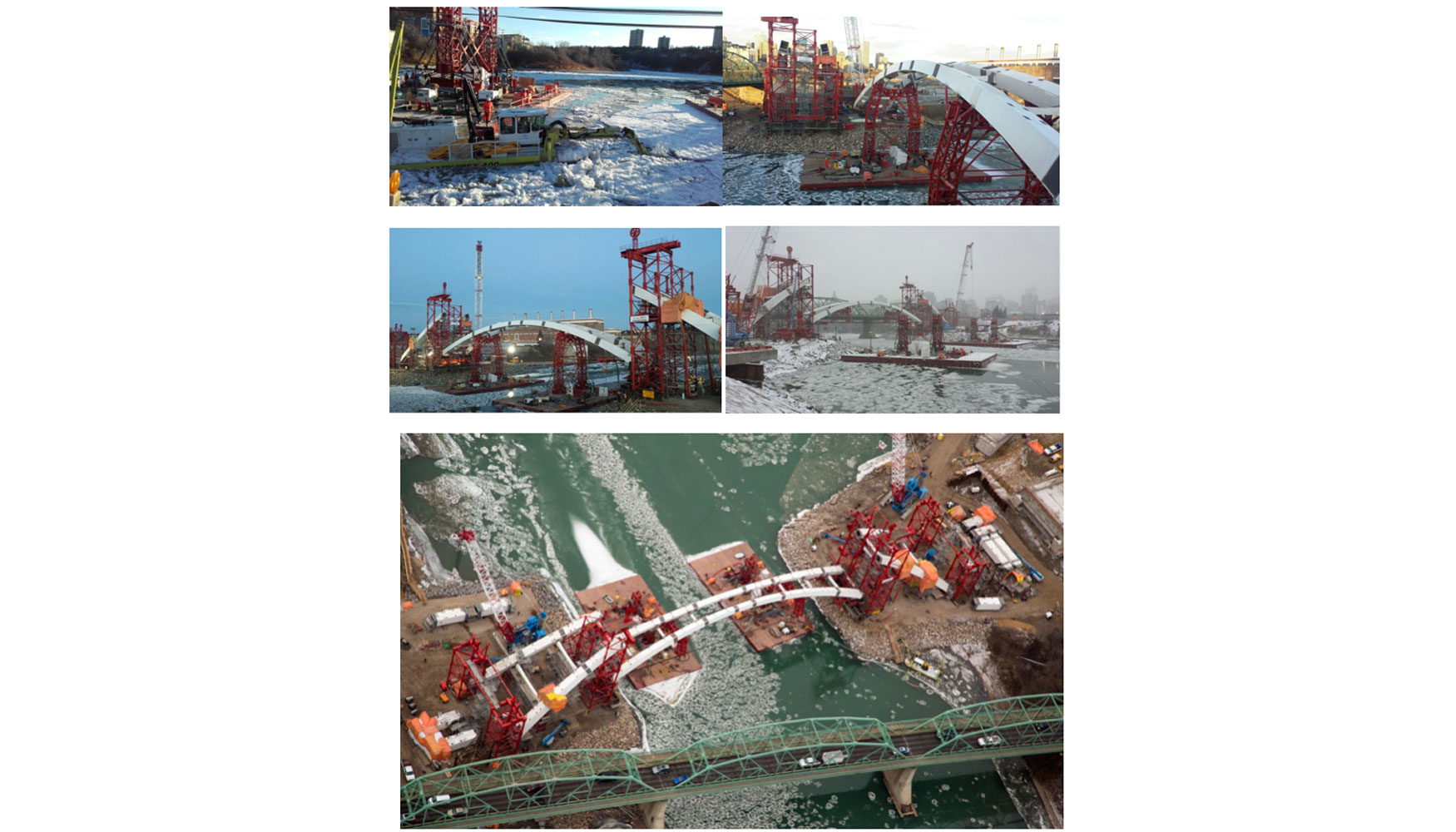
Figura 8. Rotura de hielo en el río y llegada del arco a su posición.
Montaje en las bermas en dos fases del arco restante, como muñones de espera para completar el arco
El resto del arco, para completar la estructura, se dividió en dos tramos para su montaje. Una primera parte formada por tres dovelas, que se apoyaba directamente en su posición definitiva en el arranque de los arcos sobre las bermas y en unos castilletes provisionales y otro segundo tramo formado por otras tres dovelas, colocadas en la base de su posición definitiva en el suelo, que también se apoyó sobre unos castilletes.
Estos dos tramos se montaron al mismo tiempo que se realizaba el montaje del tramo central.
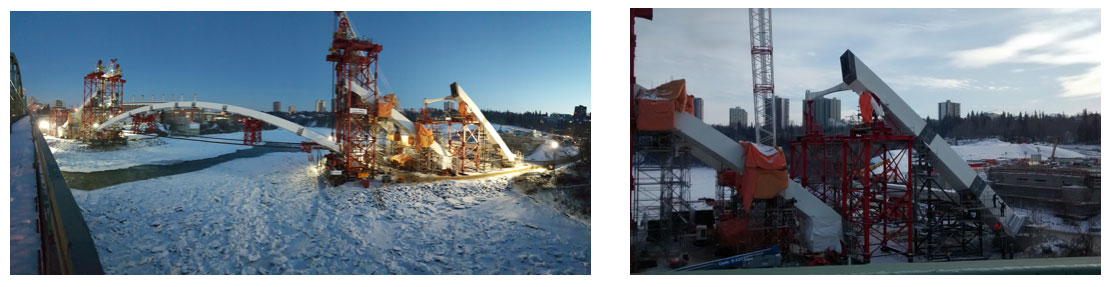
Figura 9. Premontaje de dovelas en los extremos de las bermas.
Realización de dos izados para llevar el arco a cota
Para realizar la elevación del arco central, se colocaron cuatro torres de izado en cada una de las cuatro esquinas del primer tramo central. Estas torres soportaban los arranques de los arcos, así como los gatos de izado, con una capacidad de 860 toneladas cada uno.
Para completar el arco fueron precisos dos izados (heavy-lifting) mediante gatos huecos y cables. El primer tramo central, de 1.000 toneladas de peso, se izó 20 metros. A esa altura, se atornilló cada extremo de cada arco a los arranques de arco adyacentes, previamente montados, de 30 m de largo.
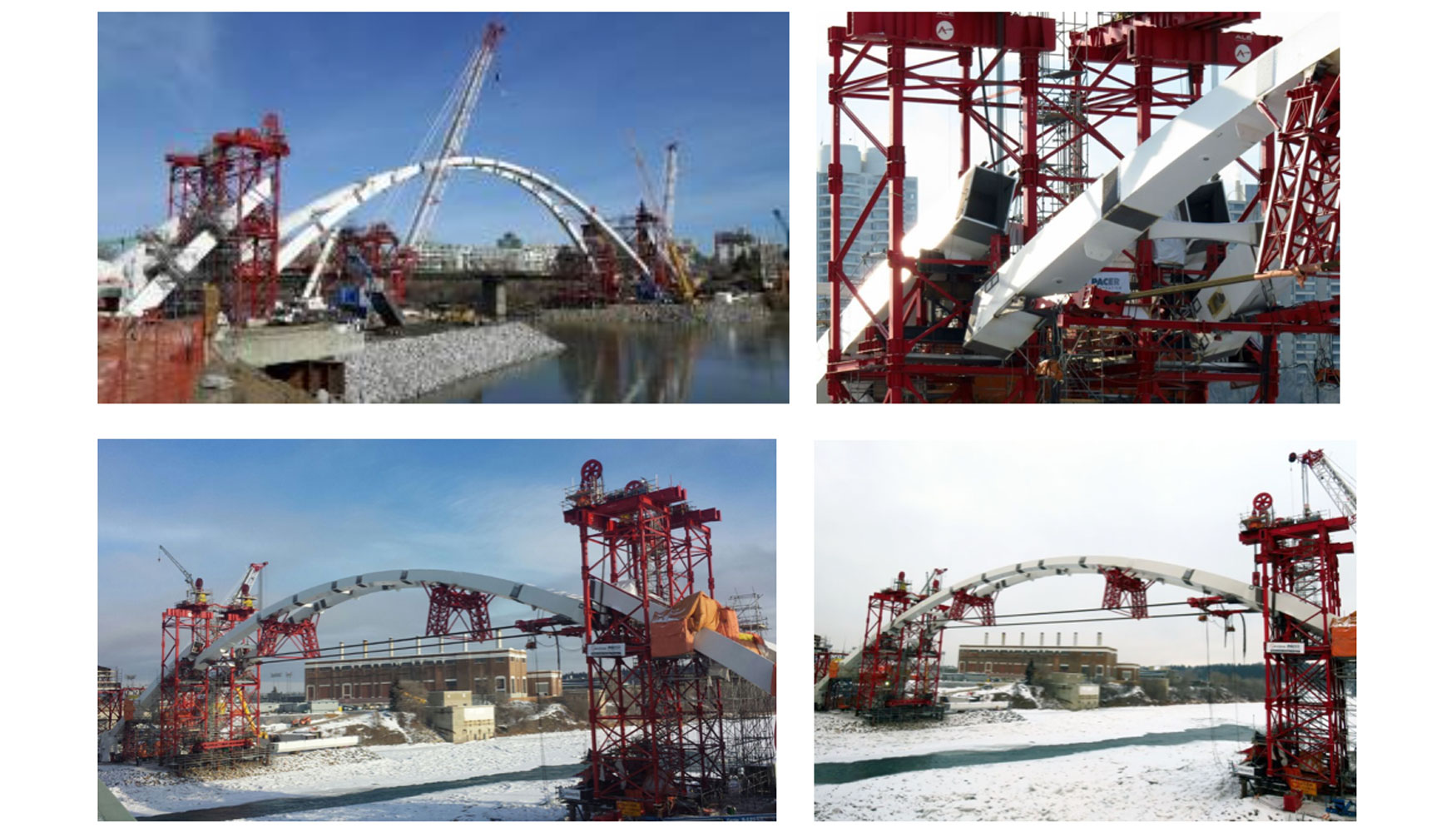
Una vez realizado este izado y atornilladas las piezas, fue necesario transferir la tensión del tirante superior a un tirante inferior para evitar sobrecargar la estructura permanente y para que el arco se mantuviera dentro de los límites geométricos establecidos por las estructuras temporales y por las tolerancias constructivas exigidas por el diseñador.
El izado del segundo tramo de arco central, ya de 154 m, supuso elevar 2.000 toneladas a una altura de 20 m. Para ello hubo que trasladar las torres de izado de su posición inicial en las torres del primer izado a las nuevas torres de izado. Cuando se completó el izado, los segmentos adyacentes se unieron temporalmente mediante unos bulones situados en el interior del propio arco. Las uniones para estos segmentos en vez de ser atornilladas eran soldadas, ya que fue un requisito exigido por el arquitecto, por un tema estético, ya que podían verse desde el propio tablero o pasarela. Esta operación complicó mucho los trabajos, al ser necesaria una mayor exactitud de colocación.
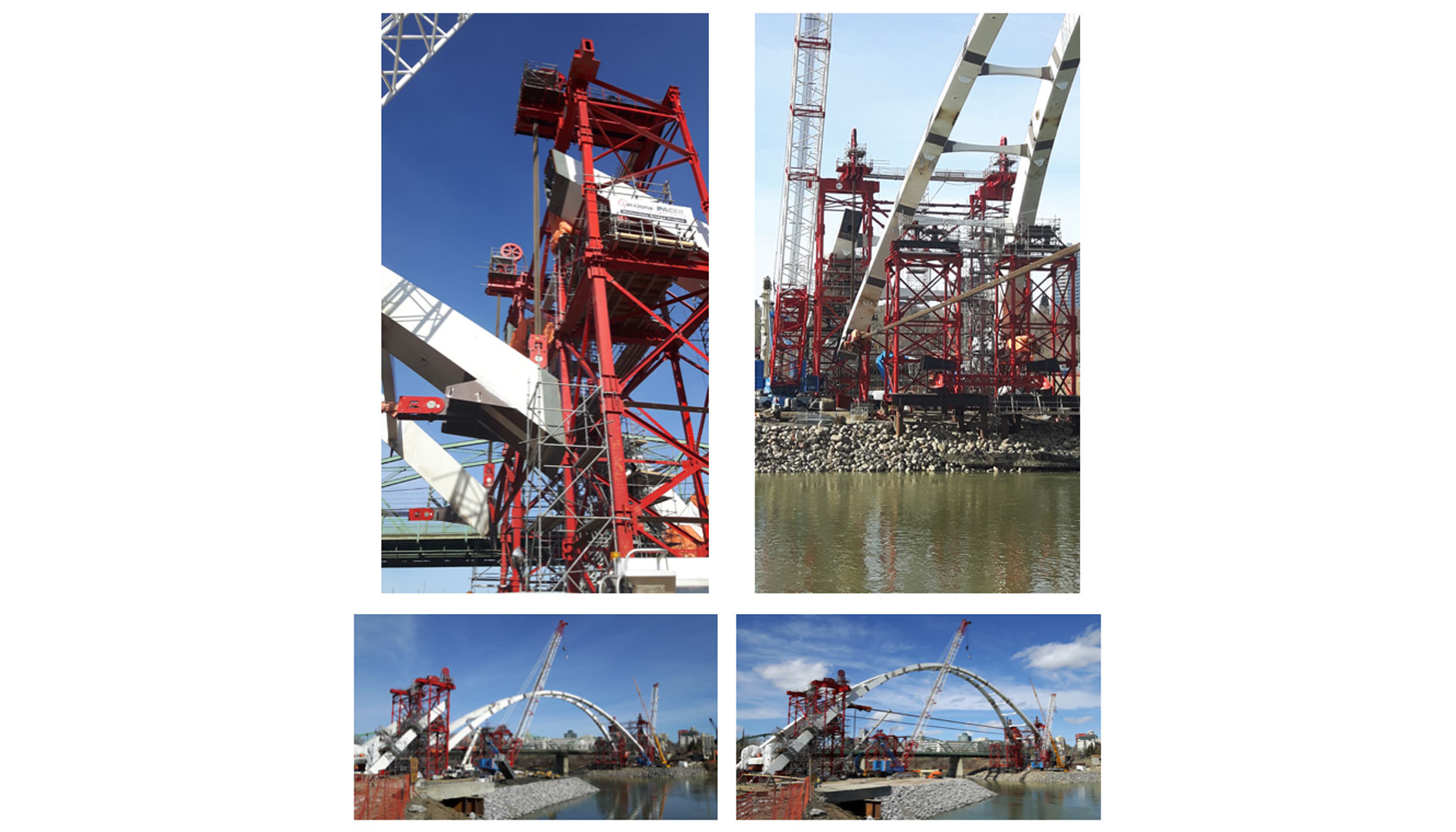
Después de cada izado, los empalmes, primero se aseguraron con una unión temporal para luego completarse uno por uno a medida que se alineaban; estas uniones temporales se dejaron como seguridad adicional. A medida que avanzaba la operación, se monitorizaron y analizaron las acciones para evitar bloquear un esfuerzo excesivo en la estructura permanente ya que era una exigencia de contrato el dejar la estructura con tensiones residuales de construcción mínimas.
Unión del arco a los bloques de anclaje
La unión entre la base y la cimentación, bloques de anclaje, se dejó incompleta hasta este momento para permitir realizar una alineación precisa de la unión mediante gatos horizontales y verticales y así reducir esfuerzos de enclavamiento y dejar en tensiones nulas el arco frente a cargas distintas de las de peso propio, como si el arco se hubiera construido sin historia de proceso constructivo siguiendo las especificaciones de proyecto. Como medidas para el cierre del arco y reducción de los esfuerzos residuales inherentes del proceso constructivo, una vez conectado el arco se realizó un tiro hacia arriba desde los puntos de izado y se enclavó el arranque, reduciendo casi a cero los esfuerzos de construcción. Esto fue posible porque la conexión se situaba exactamente en el punto de momento nulo del propio arco en cargas permanentes, incluso de servicio, por lo que tirando de ese punto se controlaban algebraicamente los esfuerzos para poder reducir a cero los flectores. Además, se instaló un sistema de gatos verticales bajo la base para poder ajustar la alineación de los arranques con el segundo tramo central.
Tras los izados (heavy-lifting), la finalización de las costillas de unión fue una etapa crítica de la construcción. Los segmentos izados y los que estaban en tierra formaban dos sistemas estructurales diferentes e independientes. Había que igualar la diferencia de deflexión en la ubicación de las uniones aplicando fuerza, minimizando al mismo tiempo las tensiones de enclavamiento. Determinar esos ajustes requirió un importante esfuerzo de ingeniería y construcción. En el diseño del procedimiento fue crucial proporcionar una capacidad de ajuste suficiente para completar los empalmes y tener en cuenta las características de los segmentos fabricados, así como las pequeñas desalineaciones que podían existir al llevarlos a su posición definitiva. Para permitir la alineación y terminación correctas del empalme, se proporcionaron los siguientes grados de ajuste:
- Verticalmente, los gatos de izado (heavy-lifting) permitieron el ajuste en la elevación del segmento izado, mientras que los gatos de las torres proporcionaron el ajuste en el sentido radial y circunferencial.
- Longitudinalmente, los gatos de izado de los arcos atirantados permitieron ajustar la longitud total de los tramos centrales elevados. La capacidad de ajuste también se proporcionó en los emplazamientos de los arranques utilizando gatos localmente en las ubicaciones de soporte.
- Torsional y lateralmente, se utilizaron gatos y eslingas con piezas metálicas rígidas para alinear las caras de cada empalme definitivamente.
Mientras se completaba el último empalme soldado, se rellenó de mortero la base de los arcos y se tensaron las varillas de anclaje a la cimentación.
Una vez la estructura permanente del arco estuvo completa se retiraron los gatos de izado de elevación y los tirantes, concluyéndose así la primera fase de construcción.
A continuación, se llevó a cabo un estudio detallado del arco para confirmar su geometría final.
3.- Montaje del tablero
La instalación de la estructura metálica del tablero se realizó en dos partes:
- En la primera parte, la estructura de acero del tablero se instaló sobre unas torres provisionales en la zona de bermas, tanto norte como sur. Una vez completado su montaje, se izó el conjunto para unirlo a las péndolas previamente suspendidas del arco con holgura suficiente para poder ajustar en cota. Luego se instalaron los anclajes de las péndolas, se retiró el soporte de las torres inferiores y el tablero quedó suspendido del arco.
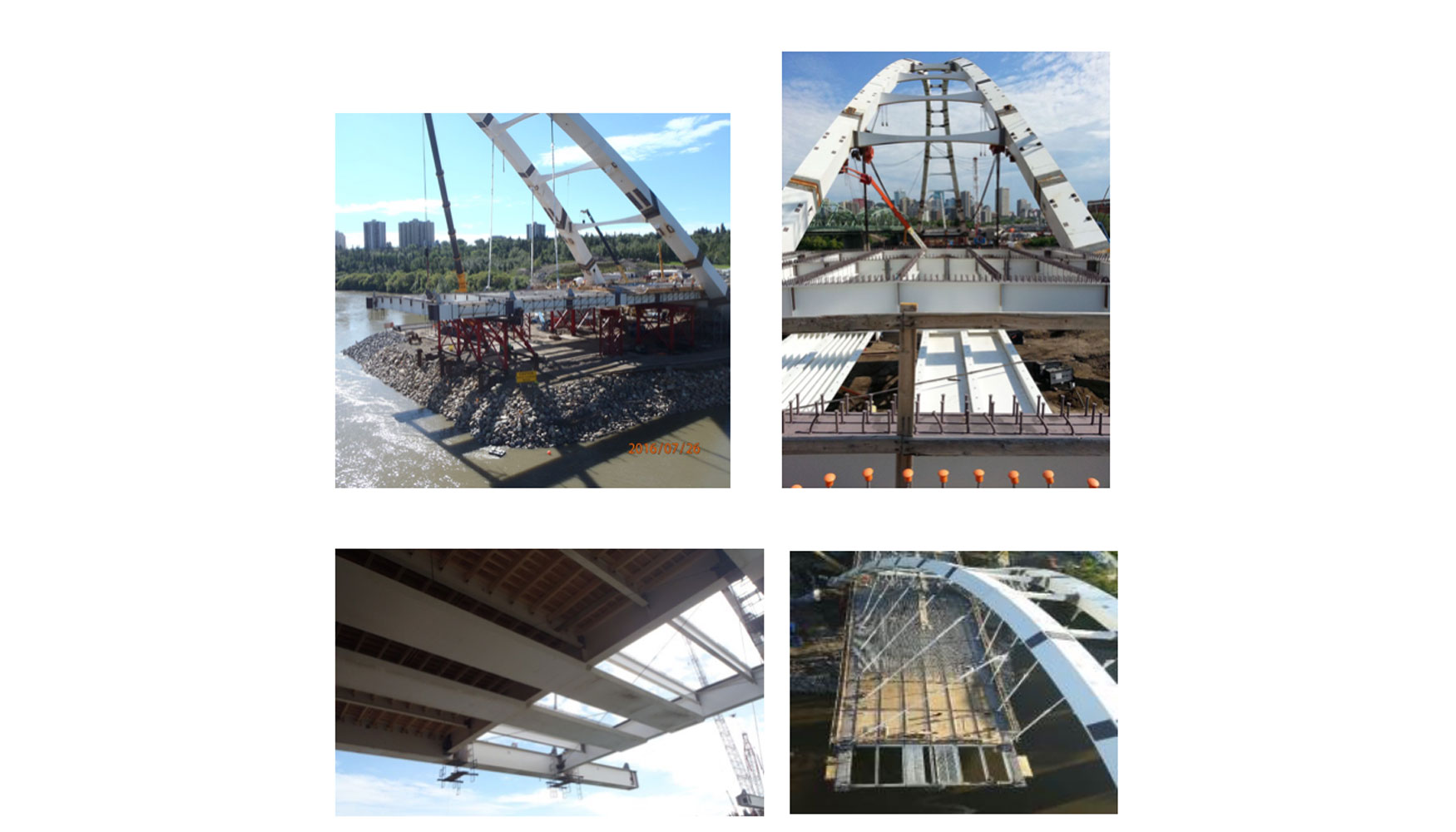
- La segunda parte se montó por voladizos sucesivos colocando unas grúas de 500 ton en las bermas e izando pieza por pieza todos los elementos metálicos del tablero. Después de ensamblar cada módulo en voladizo, de unos 10 m de longitud, un sistema diseñado específicamente para ello, tiraba del tablero y de la horquilla de suspensión inferior de la péndola para juntarlos y así permitir el anclaje de esta última. A medida que se completaba cada entramado, los frentes de izado del lado norte y sur se acercaban entre sí en el centro.
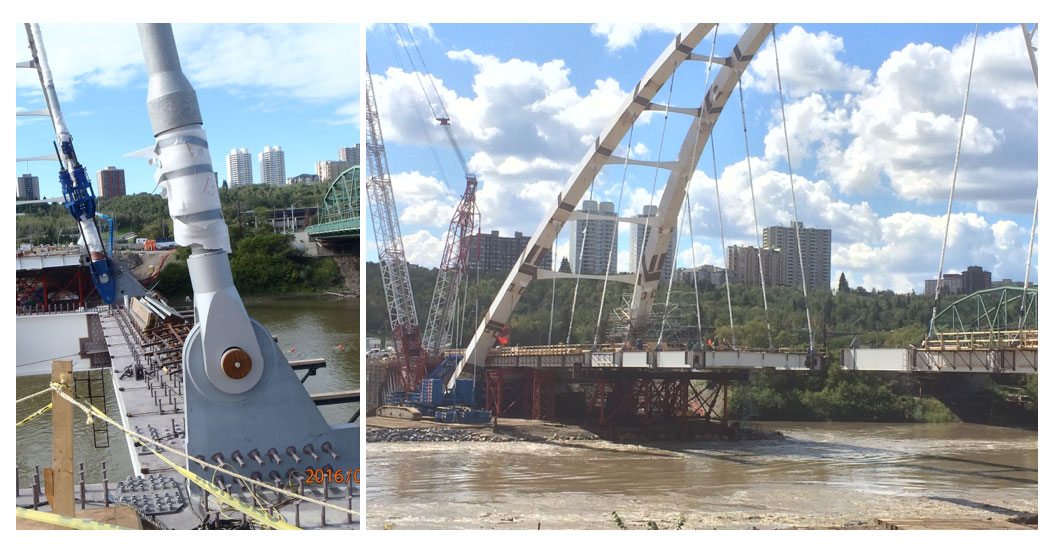
Las longitudes de corte de los cables de las péndolas se establecieron en los planos de diseño teniendo en cuenta la geometría del puente y las diferentes temperaturas en que se podía estar trabajando. A medida que avanzaba el procedimiento de instalación, se ajustaron estas longitudes para tener en cuenta la geometría real de la estructura permanente, tanto del arco como del tablero apeado. Como ya se ha mencionado con anterioridad, antes de comenzar la instalación del tablero, se llevó a cabo un estudio detallado de la geometría del arco. Las longitudes de corte finales de los cables de las péndolas se ajustaron para tener en cuenta esta geometría.
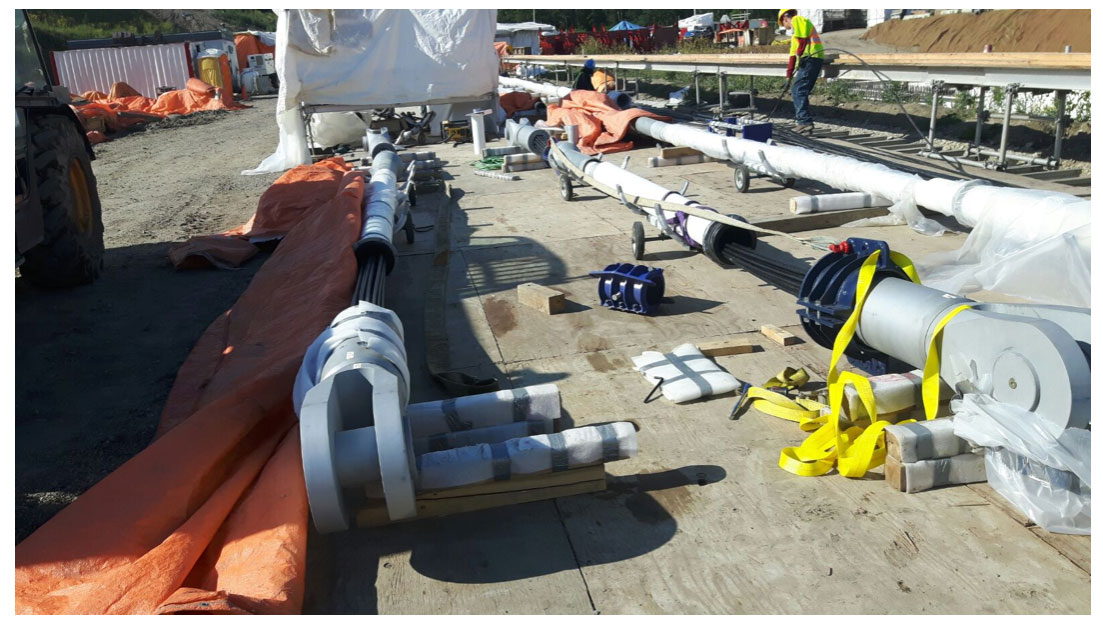
En cada etapa de construcción, se comprobaba la geometría de la estructura permanente. Esta comprobación implicó un estudio de la ubicación de cada uno de los anclajes de las péndolas y el perfil de las vigas longitudinales de borde del tablero. Se comparaba esta geometría con la geometría anticipada de la estructura basada en un modelo escalonado no lineal, que se fue ajustando constantemente para adaptarse a las condiciones en la ubicación real. Las horquillas de las péndolas permitían un ajuste de +/- 50 mm de la longitud de los cables de péndola en cualquier etapa de la construcción. En caso de desviación en cualquier etapa de la construcción, se recurría a la capacidad de ajuste de la horquilla para situar la estructura permanente a la tolerancia geométrica. El objetivo del procedimiento de instalación del tablero era mantener la gama completa de ajuste de +/- 50 mm hasta el final de la construcción.
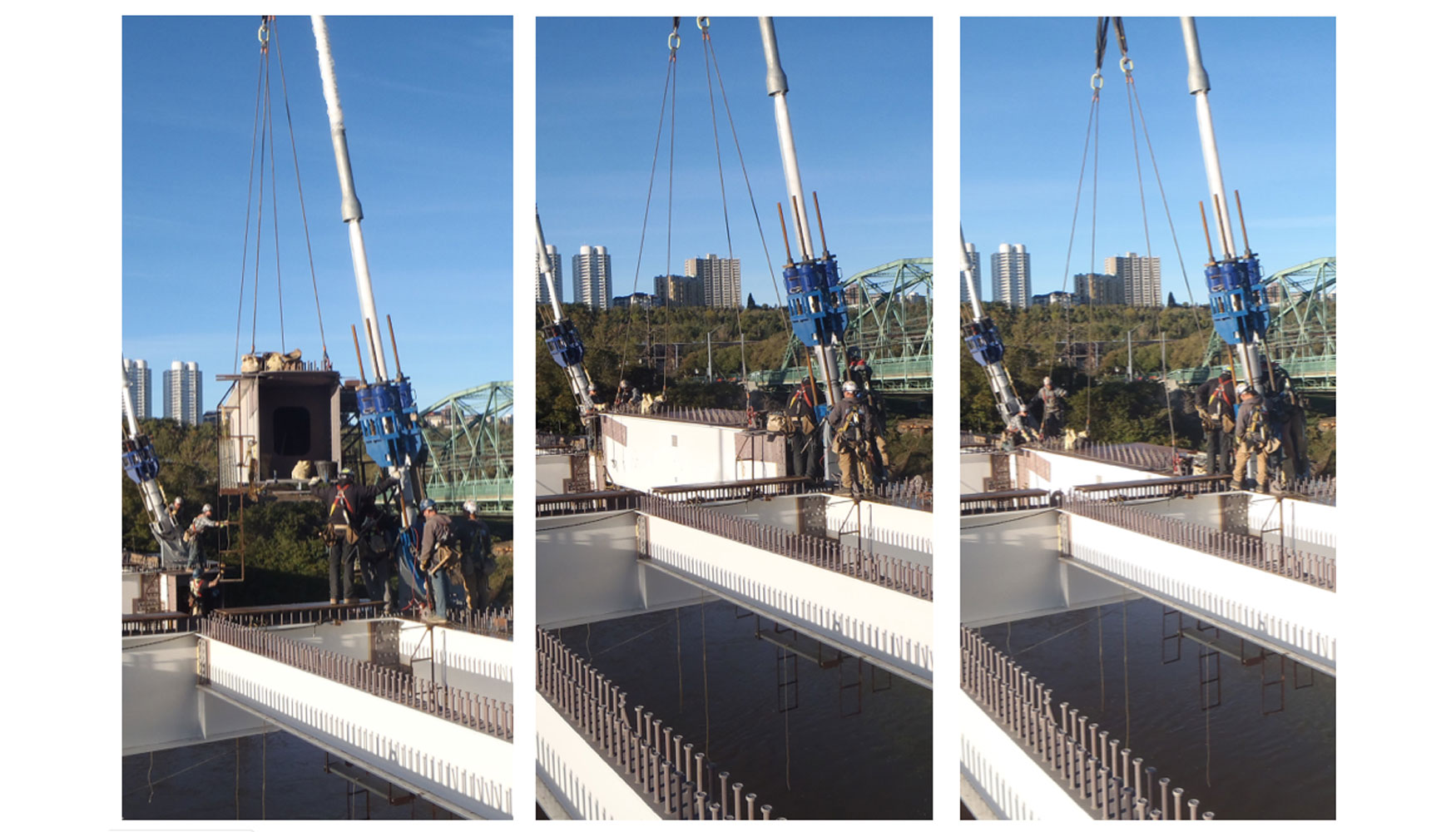
En su estado final, la losa de hormigón es la que aporta estabilidad lateral al tablero del puente. Hasta que se pudo colocar el hormigón de la losa, el tablero se apoyó lateralmente en las esquinas y bajo el tablero, sobre un sistema de arriostramiento lateral temporal.
La operación de hormigonado de la losa se realizó una vez que el tablero alcanzó una geometría aceptable, tanto en planta como en alzado, según las tolerancias especificadas en el proyecto.
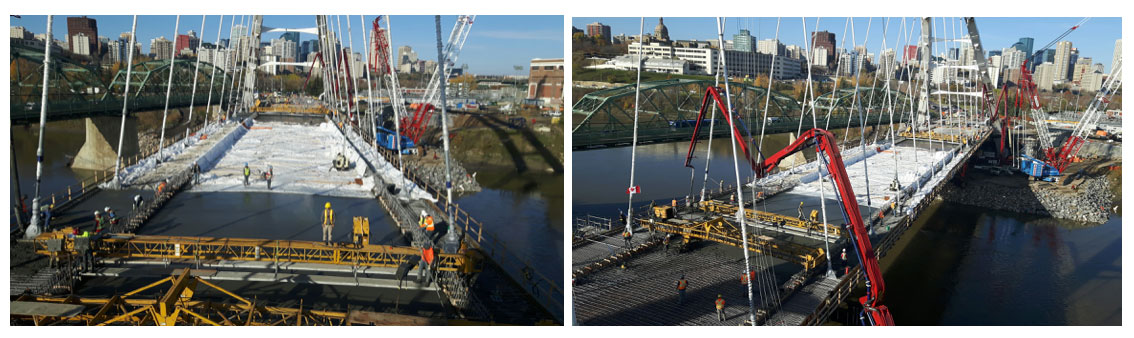
El montaje de la viga de la pasarela adyacente al puente provoca una deformación lateral en el tablero. El diseño del puente completo tiene en cuenta esta deflexión lateral dando una curvatura lateral en las vigas metálicas longitudinales y transversales del tablero, de 25 mm en su tramo central. Esta curvatura no se aplicó durante la fabricación de los elementos de acero del tablero, sino que se aplicó al tablero al final de su montaje, antes de la colocación del hormigón. Una vez instalados por completo los elementos metálicos del tablero, se realizó una medición minuciosa de su perfil lateral y se ajustó de manera incremental mediante el uso de gatos entre las vigas de soporte y las torres provisionales de soporte, para cumplir con el objetivo de curvatura lateral establecido en los planos de diseño.
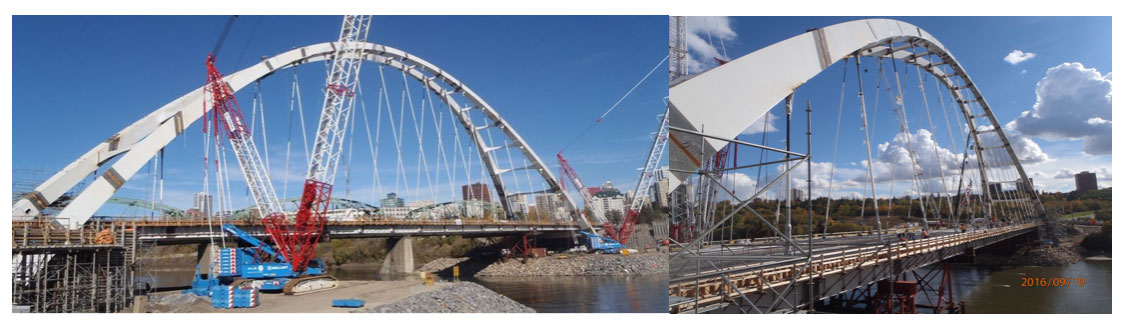
4.- Instalación de la pasarela de uso compartido
La pasarela estaba compuesta por una viga de acero prismática trapezoidal, de sección variable, de la que se hizo un montaje en blanco en una posición adyacente al tablero en la tercera y última fase de construcción, durante la primavera de 2017.
Al igual que el arco metálico, las vigas de la pasarela se fabricaron en 25 segmentos individuales, que se soldaron por partes antes de su instalación definitiva sobre el río. La fabricación fue complicada debido a la compleja geometría de las vigas.
La pasarela se montó primero sobre unas torres provisionales sobre la berma, un proceso similar al que se usó para el tablero. Una vez completado el tramo de la estructura de la pasarela sobre las bermas, se levantó para conectarlo con las extensiones de las vigas del tablero y las péndolas.
Después, unas grúas de alta capacidad levantaron los tramos de la pasarela sobre el río y los colocaron en su lugar. Las extensiones de las vigas, las péndolas y el empalme con la estructura previamente instalada se llevaron a cabo antes de soltar los segmentos de la grúa, al final de cada izado.
Una vez instalada la totalidad de la pasarela, se procedió a instalar las barandillas, a impermeabilizar el tablero del puente y la pasarela de uso compartido y a asfaltar el tablero.
Una vez colocado todo el peso permanente sobre la estructura, se procedió a afinar el ajuste de los cables. Se ajustaron los tensores para modificar la longitud no tensada de los cables, utilizando un equipo de tesado de cables similar al utilizado para la instalación de las péndolas durante el montaje del tablero. Con este ajuste se consiguió encajar la geometría dentro de las tolerancias establecidas en los planos de diseño y los documentos contractuales. Además, los cambios en las longitudes no tensadas de los cables modificaron la distribución de tensiones entre los cables. Así se pudo estar en conformidad con los valores de tensión de los cables según la documentación contractual del proyecto.
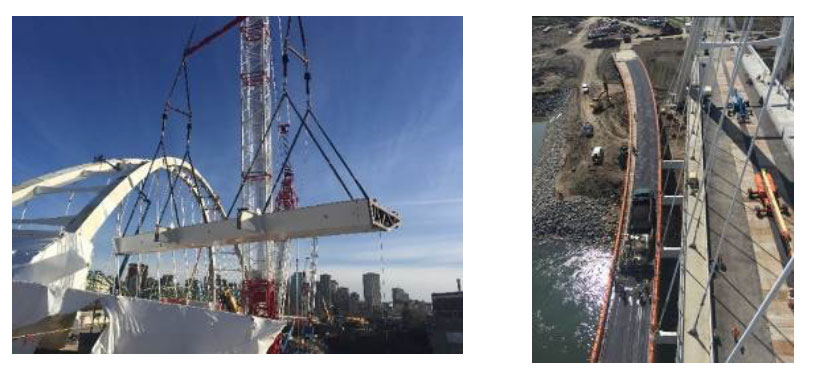
Conclusiones
El procedimiento de montaje del puente descrito en este artículo, llevó el nivel de tensión-deformación, las tensiones de las péndolas y la geometría de la estructura permanente (arco + tablero + pasarela) a un nivel final que cumplió con las expectativas y requisitos contractuales del cliente. Toda la ingeniería de montaje fue un trabajo de equipo entre los servicios técnicos de Acciona Construcción y All North.
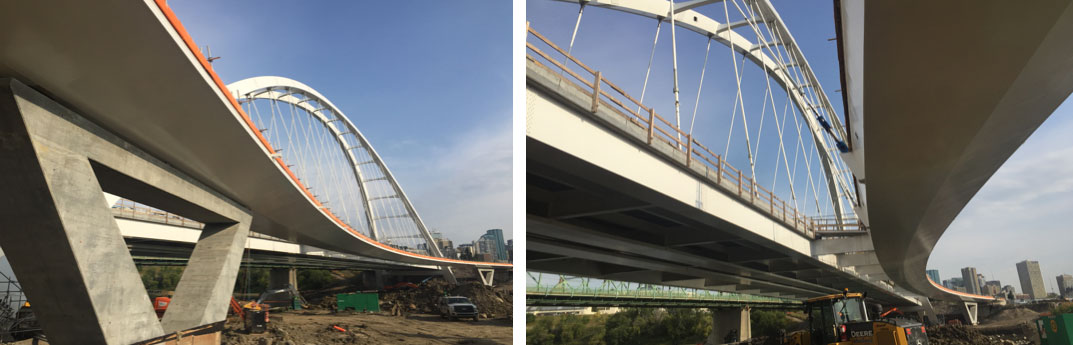