Estándares internacionales para la seguridad en las plantas industriales
7 de julio de 2010
El objetivo de la seguridad funcional es, precisamente, reducir los riesgos asociados a una planta o instalación industrial a un nivel aceptable. Para lograr una reducción suficiente de los riesgos pueden combinarse distintos tipos de medidas, entre ellas, emplear un sistema instrumentado de seguridad (SIS) que ejecute de forma automática funciones de protección.
Un sistema instrumentado de seguridad es una combinación de sensores, módulos lógicos (controladores) y actuadores que detectan condiciones anormales de funcionamiento y automáticamente llevan la planta a condiciones de operación seguras. Cada una de las funciones de seguridad implementadas en un SIS es una función instrumentada de seguridad (SIF).
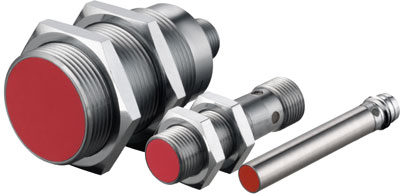
Determinar los riesgos
¿Cómo se determina si un riesgo es aceptable o si la reducción del riesgo lograda con un SIS es la necesaria? Generalmente, tanto en la industria como en otras actividades, se considera que un riesgo es aceptable si las personas implicadas o la sociedad pueden tolerarlos. Sin embargo, a la hora de implantar sistemas de seguridad para una instalación son necesarias definiciones más precisas. Con esta finalidad se han desarrollado normas y estándares que dan las directrices para la evaluación de los riesgos y la determinación de estos límites aceptables. Estos estándares recomiendan procedimientos para gestionar el ciclo de vida de seguridad de la planta y describen los requisitos que deben cumplir los equipos empleados para la implementación de las funciones de protección.
Estándares de seguridad
En el campo de la automatización, la más relevante de estas normas es la IEC 61508 “Seguridad funcional de sistemas eléctricos/electrónicos/electrónico programables (E/E/PES) relacionados con la seguridad”. Esta norma es un estándar básico, aplicable a todo tipo de industria, en el que se describen los requisitos de diseño para el desarrollo de hardware y software destinados a la implementación de funciones instrumentadas de seguridad.
La IEC 61508 describe el nivel necesario de reducción del riesgo según una escala de cuatro niveles, SIL 1, SIL 2, SIL 3 y SIL 4, siendo SIL 1 el menor nivel de seguridad y SIL 3 el máximo que se aplica a la industria. Cada SIL (Safety Integrity Level) se alcanza con el conjunto de todas las medidas tomadas para reducir los riesgos en la planta.
Para la industria de procesos, existe además el estándar IEC61511 ‘Seguridad Funcional– Sistemas instrumentados de seguridad para el sector industrial de procesos’.
La IEC 61511 describe cómo aplicar los componentes de hardware y software desarrollados y validados según IEC 61508 al desarrollo de sistemas instrumentados de seguridad específicos para la industria de procesos.
Además de los requisitos y recomendaciones para el diseño robusto de los componentes que constituyen los SIS, en las normas IEC sobre seguridad funcional se describen recomendaciones enfocadas a prevenir fallos de sistema y al desarrollo de procesos robustos para el ciclo de vida.
El FSM (Functional Safety Management) establece un marco de referencia para la organización de todos los métodos y actividades necesarias para lograr el nivel requerido de seguridad funcional.
Dentro de la gestión necesaria para asegurar la seguridad funcional, se incluye el ciclo de vida de seguridad (Safety Lifecycle), que detalla las distintas fases dentro de etapas en la vida de un planta: análisis, implementación y operación.
A partir de los riesgos identificados en la fase de análisis se evalúa si el nivel de riesgo es aceptable o es necesario implementar sistemas de seguridad para reducirlo. Para la implementación de funciones de seguridad basadas en sistemas E/E/EP existen componentes hardware y software certificados hasta SIL 3 que facilitan el desarrollo de los SIS requeridos.
¿Cuándo es necesario un sistema de seguridad?
Según el tipo de instalación, existen directivas que exigen un determinado nivel de seguridad o un nivel SIL preestablecido. Sin embargo, en la mayoría de los casos, la necesidad de un sistema de seguridad se deduce de un análisis de riesgos. De modo simplificado, la dimensión de un riesgo viene dada por la probabilidad de ocurrencia de un suceso peligroso y por las consecuencias de éste. La norma IEC 61508 describe métodos cuantitativos para realizar este análisis y calcular el nivel de riesgo de una instalación. Existe, además, un modo cualitativo para realizar el análisis de riesgos y la asignación del nivel SIL.
Este modo cualitativo se basa en evaluar para cada uno de los peligros que se presenten en la instalación: cuál es el grado de daños que se pueden llegar a producir, la duración de la exposición al riesgo, las posibilidades de eliminarlo y la frecuencia o probabilidad con la que se presentan.
A partir del nivel de riesgo (calculado cuantitativamente o estimado cualitativamente), se asigna el SIL necesario para el sistema de seguridad de la instalación. Cuanto mayor sea el riesgo en una instalación, mayor será el nivel de seguridad SIL que se le exige al sistema instrumentado de seguridad, de modo que el riesgo se reduzca hasta un nivel aceptable.
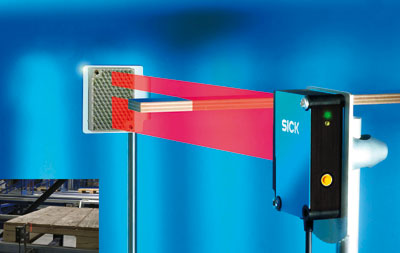
‘Higiene Industrial’: gestión vs medición
Si hasta ahora los criterios de diseño se basaban en las necesidades que demandaba el propio proceso productivo (necesidad de una cierta resistencia mecánica para alcanzar un determinado nivel de presión o temperatura), cada vez se hace más necesario también contar con las necesidades que surgirán en el momento de que los trabajadores deban acometer sus tareas en dicho medio. Esta necesidad surge no sólo debido a las exigencias legales al respecto, sino también desde el compromiso empresarial y de la propia sociedad. Cada día con mayor frecuencia demandan y abogan por una gestión integral de la seguridad y los riesgos, haciendo más partícipes a las personas.
La estrategia que se propone es la de realizar auditorías de ‘higiene industrial’. De esta manera, el trabajo comienza con una identificación de puestos y tareas dentro de ellos con posible exposición a agentes químicos peligrosos, para seguidamente identificar las exposiciones. Con ello se podrían proponer medidas de control de las situaciones de riesgo detectadas y las primeras mediciones irían destinadas a verificar su validez. Si este planteamiento se aplica desde el diseño, lógicamente será menos costoso y más fácil implantar las medidas necesarias y por tanto se corregirán las situaciones de riesgo desde el origen.
El proceso tradicional dentro de la gestión de los riesgos asociados a los agentes químicos había seguido el orden diagnóstico-intervención. Es decir, en primer lugar se realizaban mediciones para determinar los niveles de exposición de los trabajadores y, en función de los resultados, se decidía la siguiente actuación (nuevas medidas, intervención en los equipos de proceso, etc.).
Este orden tradicional se ha visto desplazado por un nuevo enfoque. En primer lugar, partiendo del conocimiento del proceso, se adoptan medidas de control para eliminar los factores de riesgo existentes. Posteriormente se realizan evaluaciones para comprobar si las medidas adoptadas han sido apropiadas y son suficientes para obtener un nivel de exposición aceptable.
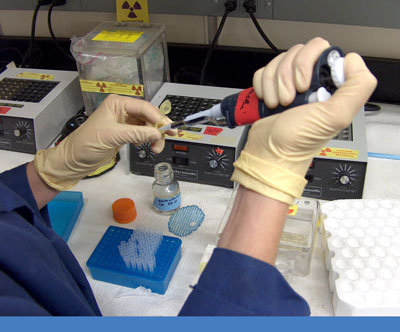
Las razones de este nuevo enfoque
En primer lugar, es conocido que el tiempo necesario para hacer mediciones y obtener y analizar los resultados no es pequeño. Por eso, si se espera a hacer las mediciones en primer lugar, se estará demorando la adopción de medidas, lo que puede ir en detrimento de la salud de los trabajadores.
Por otra parte, el coste que supongan las mediciones puede hacer que disminuya la inversión en medidas de control que probablemente ya sabíamos que era necesario implantar. Además, una vez que se hayan adoptado las medidas de control, seguirá siendo necesario volver a medir, lo que supondrá un nuevo desembolso.
Cuanto mayores son los niveles de riesgo, mayor será la frecuencia de las medidas periódicas que haya que realizar. Esta situación se puede corregir si se adoptan medidas previas para reducir los niveles de riesgo.
En instalaciones con un elevado número de agentes químicos, la estrategia que debe plantearse para realizar las mediciones suele ser muy complicada y no puede satisfacer a corto plazo la demanda de información.
Además, no son raros los casos de sustancias sin un valor límite ambiental definido (caso por ejemplo de los principios activos de la industria farmacéutica) en los que la tradicional medición deja de tener sentido.
Por último, hay numerosas referencias legales en las que la misma existencia de factores de riesgo motiva la adopción de medidas.