Tecnología de zinc lamelar, base agua, para la producción en serie de componentes de chasis de turismos
Andreas Tolz (Dipl.-Ing. FH), Technical Business Development Manager en NOF Metal Coatings Europe
31/05/2022Un factor importante en este caso es aumentar la vida útil de los componentes utilizados en la construcción de automóviles, y aquí, cuando se utilizan piezas metálicas, una protección efectiva contra las influencias ambientales juega un papel importante.
Particularmente en el área de chasis o debajo de la carrocería, las piezas metálicas están expuestas a condiciones ambientales diversas como suciedad, proyecciones de gravilla, humedad y salinidad en invierno. Por lo tanto, una protección anticorrosiva óptima y duradera es un criterio importante para mantener la funcionalidad de estos componentes.
Componentes de chasis – visión general y requisitos
Actualmente, el recubrimiento estándar para estos componentes consiste en la electrodeposición catódica, generalmente de alto espesor en torno a las 30-50 µm.
Este tipo de recubrimiento es muy eficaz como capa barrera frente a la corrosión, pero se muestra ineficiente cuando el recubrimiento se daña (por ejemplo, por proyección de gravilla) y el medio corrosivo puede alcanzar la superficie del componente. La corrosión del metal que se desarrolla en esta zona puede conducir en el peor de los casos al fallo completo del componente en cuestión.
Por esta razón, la industria de automoción busca continuamente alternativas a los recubrimientos de pintura convencional que permitan alargar de forma efectiva la vida útil de los componentes que actualmente los emplean.
Existen varias formas de aumentar el efecto protector de los recubrimientos de pintura pura. Los recubrimientos obtenidos por electrodeposición, por ejemplo, pueden combinarse con otros recubrimientos obteniéndose lo que se denomina ‘sistemas multicapa’.
Sin embargo, la aplicación de varias capas de diferentes composiciones y tecnologías conlleva por un lado un trabajo adicional con costes significativos y por otro la obtención de recubrimientos con espesores totales del orden o superiores a 100 µm.
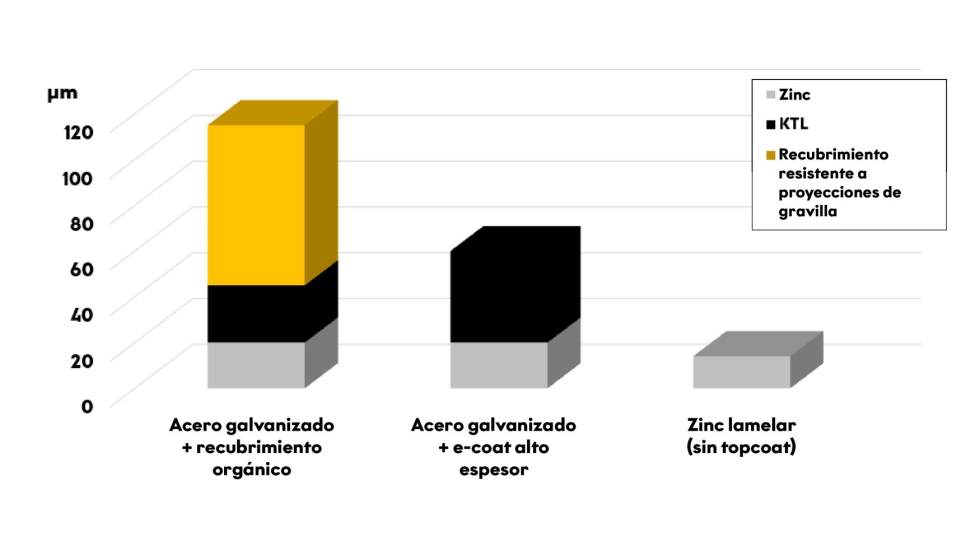
Otra opción es proteger los componentes expuestos con escudos plásticos para que estos no queden expuestos directamente a las diferentes influencias ambientales y en este caso particularmente a la proyección de gravilla.
Este método, sin embargo, además del sobrecoste que supone conlleva un incremento de peso que debe considerarse críticamente.
Una mayor resistencia a las agresiones ambientales, gracias al recubrimiento, permite reducir los espesores de chapa de las piezas tratadas y por tanto generar una reducción del peso del vehículo.
Zinc lamelar. Propiedades generales
Una alternativa interesante a los recubrimientos y medidas de protección descritas anteriormente es el empleo de la conocida tecnología de zinc lamelar para las piezas del chasis, la cual permite obtener recubrimientos con una mayor protección a la corrosión y espesores significativamente inferiores a las de los recubrimientos convencionales descritos anteriormente.
En la aplicación de la tecnología del zinc lamelar, en primer lugar, el componente se sumerge en un medio líquido viscoso que consiste en una matriz que aglutina las láminas de zinc y aluminio. En esta etapa, sin corriente, se obtiene en la superficie del componente una fina capa en forma de película líquida. Posteriormente, gracias a una etapa de centrifugado esta fina capa se reparte de forma uniforme sobre la superficie del componente. Finalmente, en la etapa de curado a temperatura se produce la reticulación de esta fina capa, adhiriéndola firmemente a la superficie del componente.
La tecnología del zinc lamelar se emplea con éxito desde hace décadas, especialmente para recubrir pequeñas piezas a granel, como pernos, tuercas y otros elementos de fijación, o en piezas estampadas y conformadas, presentando entre otras las siguientes características:
- Excelente protección a la corrosión catódica
- Recubrimientos de bajo espesor (5-15 µm)
- Permite recubrir zonas interiores o huecas
- Exento de cromo y otros metales pesados
- Sin fragilización por hidrógeno (proceso sin corriente)
- Posibilita el empleo posterior de topcoats
Los recubrimientos de zinc lamelar Geomet que utiliza NOF Metal Coatings se obtienen a partir de productos formulados exclusivamente en base agua y, por lo tanto, ofrecen una mayor compatibilidad medioambiental que otros recubrimientos disponibles en el mercado a base de solventes.
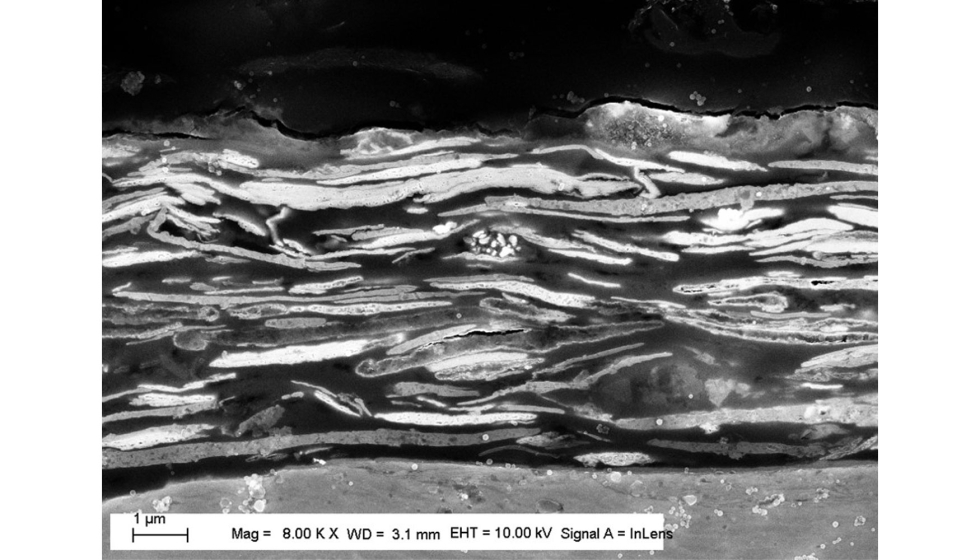
Brazo de suspensión con Geomet —recubrimiento de zinc lamelar— etapas de calificación
Debido a las ventajas del recubrimiento de zinc lamelar detalladas anteriormente, existe un gran interés por parte de los fabricantes de automoción para emplear también esta tecnología en las piezas de chasis a una mayor escala. A continuación, se explicarán las etapas transcurridas desde la calificación hasta la producción en serie con el recubrimiento de zinc lamelar conforme una aplicación específica.
En este caso se trata de los brazos de control inferior de suspensión del eje delantero de la CMP ‘Common Modular Platform’ de la empresa Stellantis.
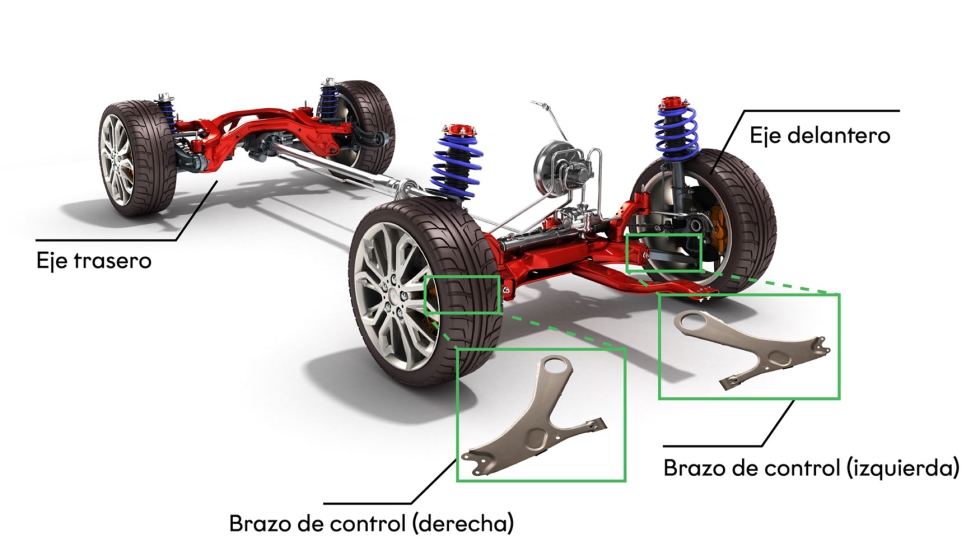
Para esta plataforma, el uso de un brazo de control inferior de suspensión de bi-coquilla ha demostrado ser la solución óptima.
Este tipo de construcción ofrece una mayor resistencia mecánica que un brazo de mono-coquilla, en las mismas condiciones de peso y espacio, pero presenta una mayor dificultad en términos de protección a la corrosión.
La zona hueca entre ambas coquillas presenta grandes limitaciones de protección a la corrosión mediante tecnologías electrolíticas por lo que en este caso se requiere también la posterior aplicación de algún tipo de cera o polímero.
El uso de acero pregalvanizado para este componente sería concebible por razones de protección a la corrosión, pero de acuerdo con el diseño de esta pieza se requiere la soldadura de las dos coquillas que conforman el brazo.
Así, la elección de este material conllevaría el riesgo de porosidad en la unión de soldadura debido a la sublimación del zinc existente a causa del calor generado durante el proceso de soldadura.
En casos extremos, esto podría conducir a la fractura de la junta de soldadura y, por lo tanto, a un fallo generalizado en la producción en serie del brazo de control.
Para reducir este riesgo, habría que ajustar los parámetros de soldadura considerando el empleo de aceros pregalvanizados y, sobre todo, habría que reducir significativamente la velocidad de soldadura, lo que tendría un efecto negativo en la productividad.
Frente a este riesgo, el recubrimiento de zinc lamelar ha demostrado ser una excelente alternativa, porque las coquillas del brazo de control pueden fabricarse en acero sin galvanizar, soldarse y finalmente aplicar el recubrimiento de zinc lamelar sobre el componente ya terminado. Esto permite alcanzar en el brazo de suspensión una excelente protección a la corrosión catódica (interna y externa) sin el riesgo de calidad descrito anteriormente, manteniendo los parámetros de soldadura inalterados.
Para calificar el recubrimiento de zinc lamelar Geomet en el brazo de suspensión, se llevaron a cabo varias series de ensayos intensivos en componentes recubiertos con el mismo. Los requisitos o criterios de ensayo por parte del OEM incluyeron varias pruebas mecánicas y de corrosión, así como una prueba de conducción dinámica.
Las pruebas de corrosión requeridas fueron la cámara de niebla salina neutra conforme EN ISO 9227 (1000 horas) y un ensayo de exposición natural (12 meses).
Para abordar mejor los requisitos de la zona bajo carrocería, a las muestras se les realizó también un ensayo de proyección de gravilla conforme EN ISO 20567-1, método B, previamente a la serie de ensayos.
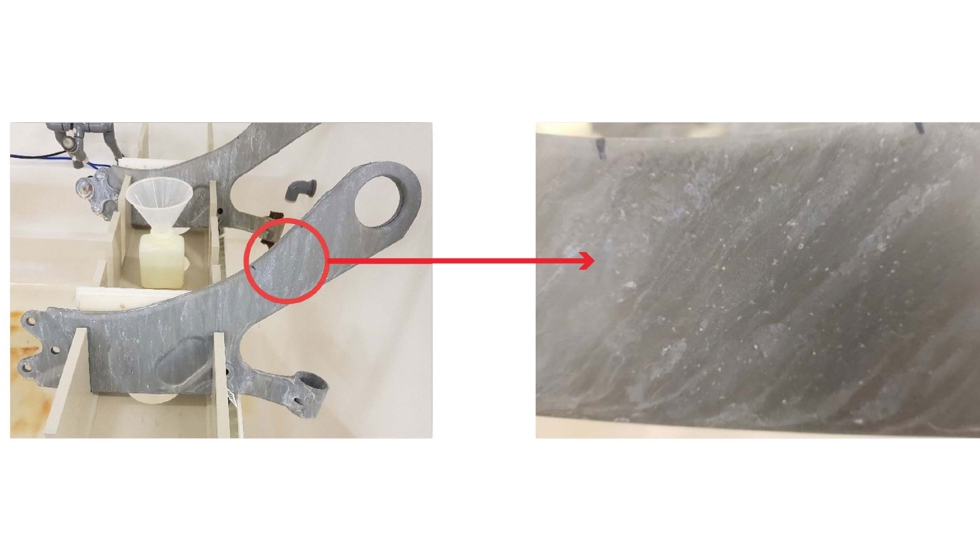
Brazo de suspensión en cámara de niebla salina con ampliación de la zona expuesta al ensayo de proyección de gravilla (tras 1.000 h).
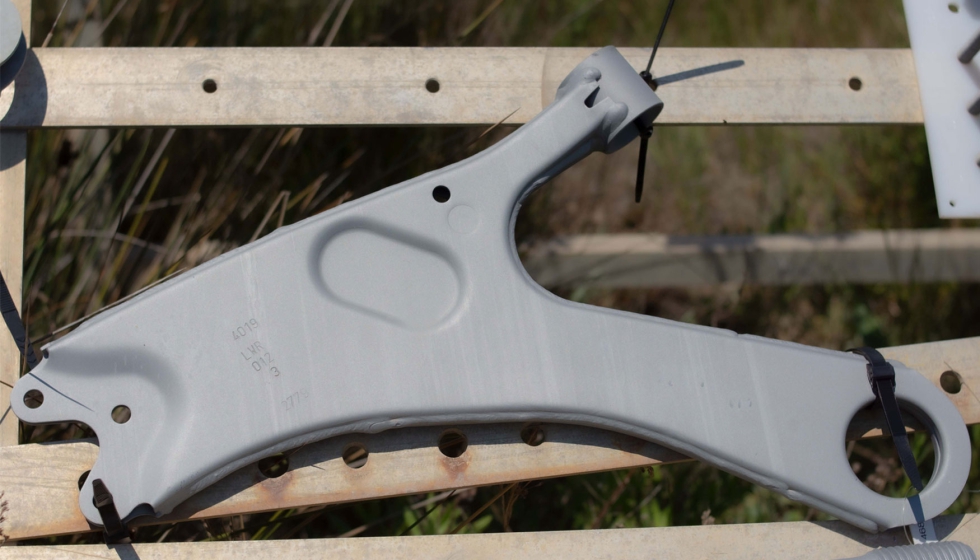
Sobre la base de estos resultados muy positivos, la tecnología de zinc lamelar fue calificada y aprobada por el OEM como la única opción posible de recubrimiento para este brazo de suspensión.
Brazo de control con recubrimiento de zinc lamelar Geomet - producción en serie
Para la producción en serie de la pieza con el recubrimiento de zinc lamelar Geomet se construyó una nueva línea, totalmente automatizada, en estrecha cooperación con el fabricante TIER 1.
La línea de producción de los brazos de suspensión se encuentra en Zaragoza - España, y el aplicador del recubrimiento ‘Aragonesa de Tratamientos’ se encuentra en las inmediaciones del TIER1, lo cual tiene un efecto positivo muy relevante en términos logísticos.
Desde España, las piezas recubiertas se envían a distintas fábricas del OEM, donde se instalan en los modelos correspondientes. La CMP se trata de una plataforma diseñada para los modelos compactos SUV, en la que cuatro modelos diferentes están siendo equipados con estos brazos de suspensión.
En la producción en serie, el recubrimiento de zinc lamelar se obtiene gracias a un proceso DDS ‘Dip-Drain-Spin’. Aquí, el diseño del bastidor y el posicionamiento de las piezas son factores decisivos para obtener la máxima productividad con el menor número de puntos de contacto de las piezas. Al mismo tiempo, debe garantizarse un correcto escurrido de las piezas y un reparto perfecto sin acumulación local de Geomet.
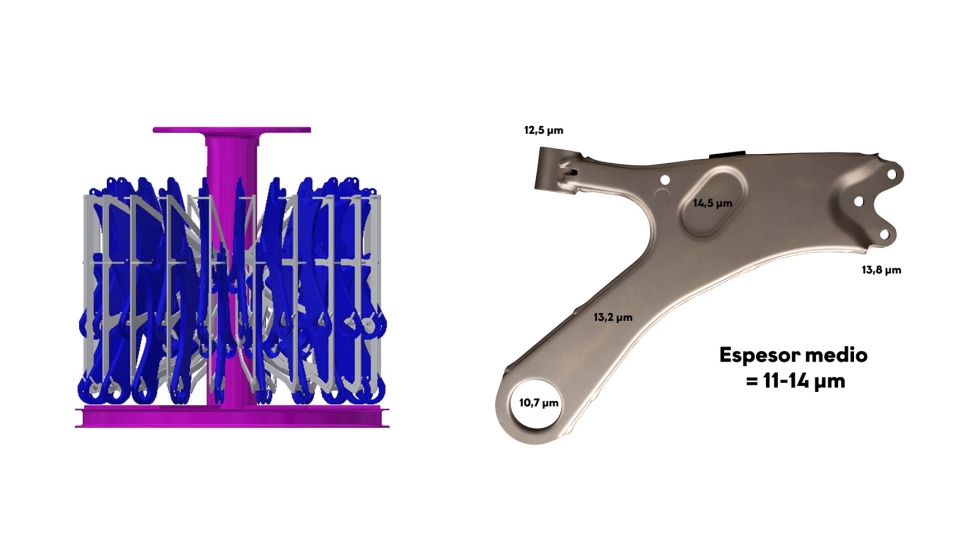
Las diferentes etapas de proceso se detallan a continuación:
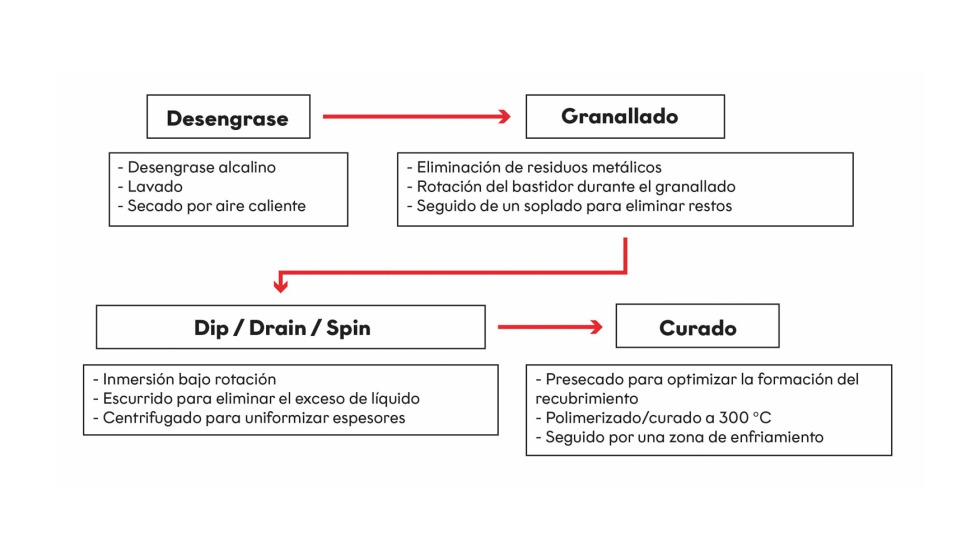
En esta aplicación, las etapas de ‘Dip-Drain-Spin’ y de curado se repiten para que el recubrimiento final está constituido por dos capas de zinc lamelar. En este caso no se requiere la aplicación de un topcoat adicional.
Con el proceso descrito, se obtiene en los brazos de suspensión un recubrimiento Geomet uniforme de 11-14 µm de espesor en toda la pieza incluida la zona interior del brazo.
Desde el inicio de la producción en serie en España, a principios de enero de 2019, ya se han recubierto con éxito más de 1,5 millón de brazos de suspensión, por lo que ya están en circulación más de 750.000 vehículos con estos componentes.
Las investigaciones de campo a gran escala sobre el brazo de suspensión no fueron sencillas de realizar debido al entorno COVID-19, aún persistente, pero sin embargo fue posible revisar algunos vehículos durante las inspecciones rutinarias de los mismos.
Se adjuntan algunas imágenes de dos vehículos inspeccionados (ambos construidos en 2019) que han sido conducidos por el cliente final durante más de dos años. No se ha detectado corrosión en ninguno de los componentes inspeccionados por lo que repetiremos este tipo de inspección a intervalos regulares para documentar aún más las prestaciones de nuestro recubrimiento.
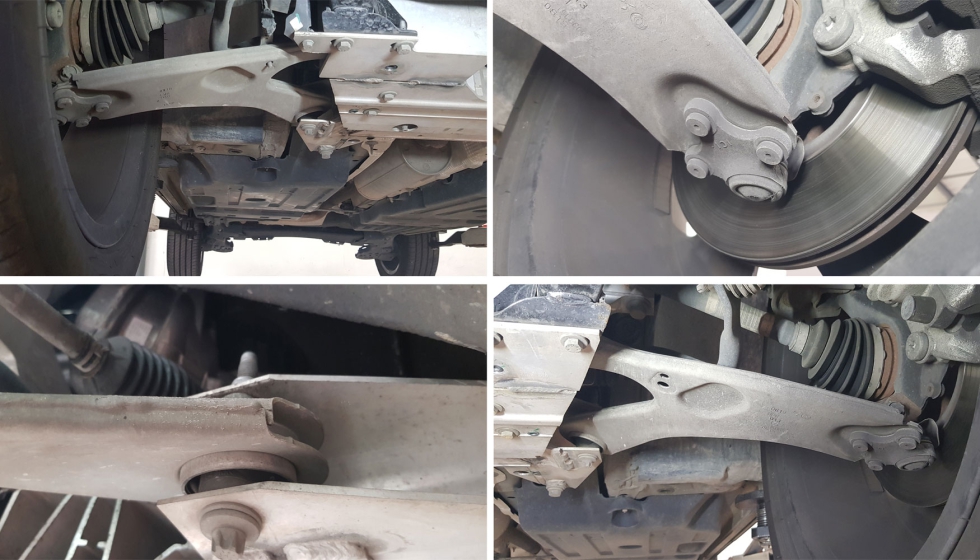
Sumario y visión
He aquí un breve resumen de los resultados:
- Los requisitos para las piezas del chasis están aumentando tanto en términos de una mayor vida útil de los componentes como de reducción de peso
- El uso de nuevos materiales como aceros de alta resistencia y/o nuevos métodos de construcción (estructura multicapa) presenta nuevos retos, especialmente en términos de protección a la corrosión a largo plazo y reducción de peso
- Los recubrimientos clásicos solo pueden cumplir parcialmente estos nuevos requisitos.
- La tecnología de zinc lamelar constituye una alternativa que permite obtener recubrimientos de bajo espesor con una mayor protección a la corrosión y compatibilidad medioambiental comparativamente a los recubrimientos empleados actualmente.
- La investigación de campo inicial de los brazos de suspensión con un recubrimiento de láminas de zinc Geomet confirman los resultados positivos de las pruebas de homologación realizadas por el OEM.
En el futuro, vemos una expansión de la plataforma actual a otros modelos del Grupo Stellantis y, por lo tanto, un incremento del volumen actual de producción del brazo de suspensión.
Además, se han completado con éxito varias series de pruebas sobre otros componentes recubiertos con Geomet, por lo que estamos en conversaciones intensivas con otros OEM/ TIER 1 para su implantación en otros tipos de vehículos.
En general, cabe decir que hay un gran potencial para el uso de la tecnología de zinc lamelar en el área del chasis y que están surgiendo nuevas oportunidades de aplicación, también a consecuencia de la electromovilidad.