Sandvik desarrolla una nueva fresa de planear para producir estantes de batería de aluminio
Fernando Oliveira, gestor global de Aluminio para la Automoción del especialista en corte de metales Sandvik Coromant
13/06/2023En los próximos años, los sistemas de batería continuarán evolucionando y serán necesarios nuevos desarrollos y formas. Para los fabricantes de equipos originales, esto supondrá producir piezas de sistemas de batería próximas a la forma final a partir de diseños más complejos. El mecanizado de estos diseños requerirá herramientas de corte eficaces y más ligeras, para minimizar el impacto en la máquina herramienta y garantizar que la pieza conserve su forma.
El papel de los fabricantes de equipos originales también está evolucionando a medida que se implican más en la producción de baterías, lo que McKinsey & Company atribuye a “la integración hacia atrás de los fabricantes de equipos originales desde los packs y módulos hasta la producción de células”. A su vez, la carrera por fabricar vehículos eléctricos (VE) más ligeros y eficientes que recorran distancias más largas con la máxima autonomía por carga ha comenzado.
Además, los fabricantes deben producir estas piezas más complejas con la máxima calidad y productividad. ¿Cómo pueden los fabricantes lograr eso manteniendo un bajo coste por pieza? La respuesta está en unas herramientas de corte más eficaces, que tengan una buena accesibilidad y sean lo más ligeras posible para permitir cambios de herramienta rápidos.
Reducir las emisiones de CO₂
Los fabricantes recurren al ‘aligeramiento’, que consiste en fabricar coches y camiones menos pesados para mejorar el consumo de combustible y la manipulación.
Otro estudio de McKinsey & Company, Lightweight, heavy impact (Peso ligero, fuerte impacto), estima que “las medidas de aligeramiento pueden ayudar a reducir las emisiones de CO₂ hasta cierto punto (aproximadamente 0,08 g de reducción de CO₂ por kilogramo ahorrado)”. Concluye que “si un fabricante consigue reducir el peso del vehículo en 100 kg, ahorra aproximadamente 8,5 g de CO₂ cada 100 km”.
Al ser uno de los metales más ligeros del mundo, el aluminio es una solución de aligeramiento consolidada. El aluminio es casi tres veces más ligero que el hierro y, aunque de menor resistencia que este, sigue siendo muy fuerte y resistente a la corrosión. Desde el punto de vista de la ingeniería de diseño, se ha observado que la sustitución de piezas convencionales de fundición por aleaciones de aluminio puede reducir el peso total del bloque motor hasta en un 40-55%.
Otra ventaja del aluminio es que es muy reciclable y puede fundirse y reutilizarse sin ningún daño ni cambio en sus propiedades mecánicas. De hecho, aproximadamente el 75 % de todo el aluminio producido se sigue utilizando hoy en día, lo que demuestra la utilidad de este material en las estrategias de sostenibilidad de los fabricantes de equipos originales.
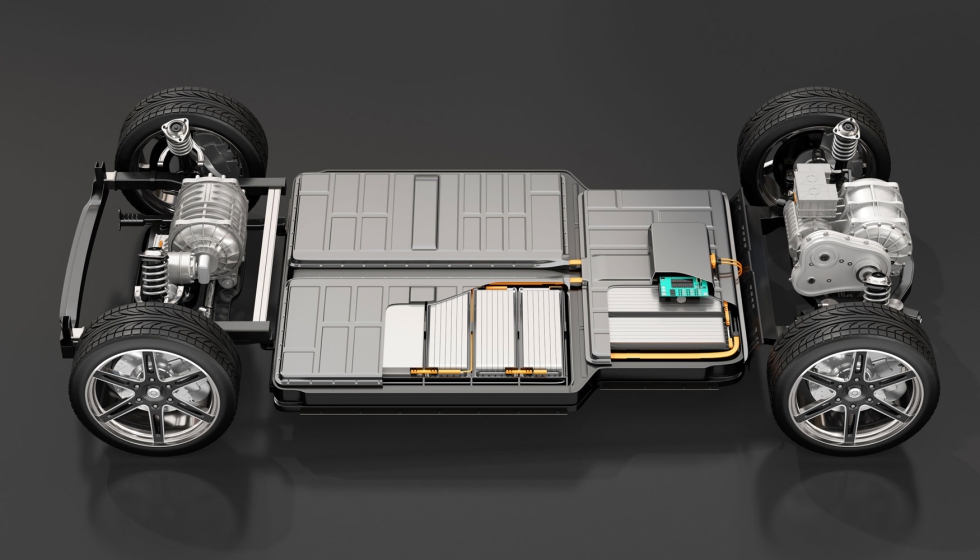
Caras más pequeñas
El sistema motopropulsor de un turismo europeo habitual contiene en torno a 80 kilogramos de aluminio, lo que significa que estas piezas, el motor; la caja de cambios; las suspensiones y los alojamientos, son una clara área de interés para la aplicación de medidas de reducción del peso. El aluminio también puede utilizarse en las propias baterías: la Plataforma de Cooperación Energética UE-China (PCECE) recomienda las baterías de aluminio-aire (AI-aire) como alternativa ‘barata, ligera y potente’ a las de iones de litio (Li-ion).
Vamos a centrarnos en los estantes de baterías de aluminio. Estas piezas suelen tener caras más pequeñas con más roscas, agujeros y otras características. Otra consideración importante son los estantes de baterías eléctricas para camiones, especialmente los modelos más grandes que se alejan de las áreas urbanizadas y que miden hasta dos metros de longitud.
Los estantes de baterías requieren una gama de máquinas herramienta y aplicaciones como fresado, rebordeado y mucho más. Sin embargo, incluso los estantes para baterías más grandes no requieren grandes herramientas y, en su lugar, están formados por caras más pequeñas con más características, roscas y agujeros. Por lo tanto, necesitan herramientas de fresado en escuadra y planeado o escariadores que puedan producir piezas con la calidad y las tolerancias requeridas.
Eliminar vibraciones
Para el mecanizado de estantes de baterías, Sandvik Coromant recomienda utilizar su familia M5 de fresas de aluminio específicas para la automoción, incluida la fresa de planear M5F90, diseñada para mecanizar piezas sin rebabado, arañazos ni astillamiento. La fresa está especializada en el mecanizado de piezas de aluminio de pared delgada y, para ello, está equipada con un cuerpo de la fresa más pequeño de 25-80 mm o 0,98-3,15 pulgadas de diámetro. La M5F90 también contiene puntas de diamante policristalino (PCD) con soldadura de cobre, por lo que no precisa ningún ajuste y garantiza unas desviaciones muy reducidas. Esto permite velocidades de alto avance y, al mismo tiempo, elimina las vibraciones de corte.
En una ocasión, la M5F90 se utilizó para mecanizar una bandeja de batería de aluminio. Se trataba de una aplicación ideal para el nuevo concepto de fresa de planear, ya que la aplicación requería que la herramienta se utilizara para limpiar superficies en la primera fase de mecanizado de la nueva pieza de fundición de aluminio en una sola operación, sin rebabado.
Sus dimensiones eran de aproximadamente 980 x 600 x 130 milímetros (mm). En total, se utilizaron 48 herramientas para mecanizar la pieza: brocas de metal duro integral, fresas de ranurar de metal duro integral, machos de roscar de acero a alta velocidad (HSS, por sus siglas en inglés), escariadores de PCD con soldadura de cobre, fresas de PCD con soldadura de cobre y, por último, la fresa M5F90. La pieza de aluminio se mecanizó en un centro de mecanizado de 5 ejes, equipado con un portaherramientas de alta velocidad HSK 63.
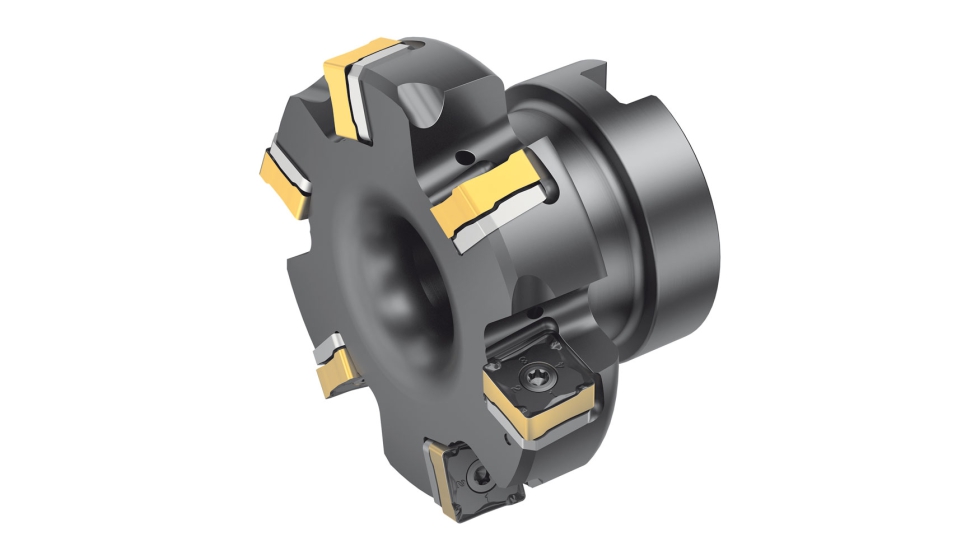
En definitiva, la aplicación de mecanizado de bandejas de baterías ha evidenciado una ventaja clave de la M5F90. De manera específica, permite el desbaste y el acabado en una sola operación, con el consiguiente ahorro de tiempo. Esto se demostró con el mecanizado de la bandeja de aluminio de la batería; la pieza se mecanizó en 20,3 minutos. Con este mejorado rendimiento de la herramienta, los fabricantes de equipos originales pueden implicarse más en la producción de sistemas de baterías, a la vez que se diferencian de sus competidores.