Digitalización del proceso de control de calidad en la fabricación de componentes para automóviles
Jens Nannen, director de Tecnología de Ventas de Mecanizado Digital para Europa de Sandvik Coromant
31/05/2022Muchas de las grandes empresas del sector de la automoción están implementando procesos digitalizados para mejorar su producción. Por ejemplo, BMW ha implantado una plataforma de Internet de las Cosas (IoT) en su planta de Baviera (Alemania), que cuenta con una amplia variedad de herramientas y accesorios digitales que los empleados de BMW pueden combinar para crear sus propias soluciones «plug and play». Gracias a ello, la plataforma ha reducido el tiempo necesario para implantar nuevas aplicaciones de software en un 80 %, y ha reducido los problemas de calidad de las piezas fabricadas en un 5 %. Por su parte, Volkswagen se ha asociado con un desarrollador de aplicaciones basadas en la realidad aumentada (RA) para etiquetar sus piezas de automoción, lo que facilita la asignación de cada pieza a la mejor herramienta para mecanizarla. Esto ha aumentado enormemente la eficiencia de los técnicos de servicio postventa de Volkswagen.
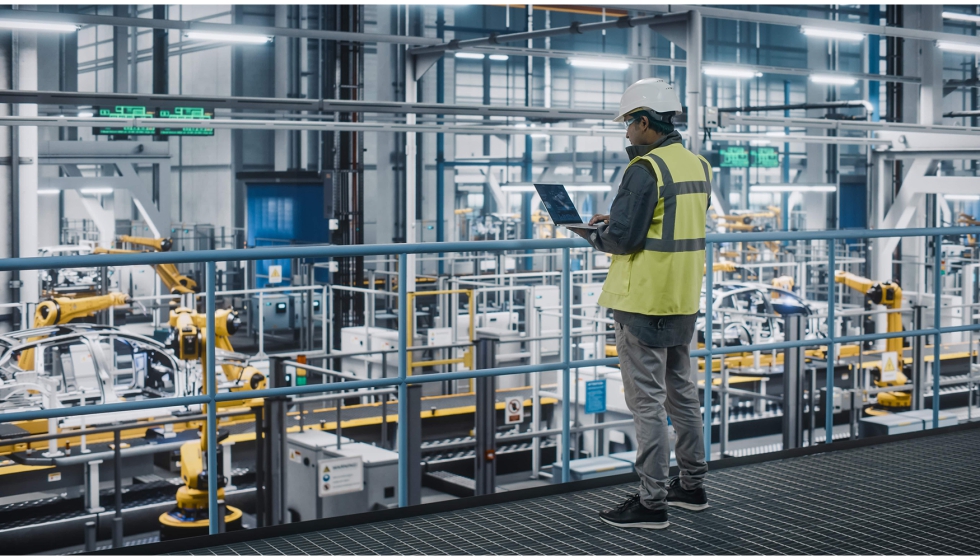
Las máquinas y los tornos CNC actuales están más conectados que nunca. Los procesos de mecanizado generan características físicas que originan información medible, mientras que los sensores y el IoT pueden utilizarse para supervisar el tiempo de productivo, el tiempo improductivo y la disponibilidad de las máquinas. Estas tecnologías también permiten ahondar en cuestiones más concretas, como las roturas de herramientas y máquinas, que son las principales causas de los tiempos improductivos en la fabricación. Se estima que un minuto de tiempo improductivo puede ser extremadamente caro, con un coste de miles de dólares por hora para los fabricantes de automóviles, según TPC.
Estas pérdidas no pueden asumirse cuando se mecanizan componentes de automoción. Los ejes de engranajes y de los árboles de transmisión suelen ser de acero forjado, que es ideal para producir piezas más grandes y resistentes, pero también dificulta el mecanizado. Los materiales forjados tienen profundidades inconsistentes que requieren diferentes tolerancias de mecanizado. Dichas tolerancias varían entre 0,5 milímetros (mm) y más de 1 mm, y estas profundidades de corte fluctuantes implican un mayor riesgo de rotura de las herramientas.
El control de calidad mediante una supervisión eficaz también puede resultar difícil cuando se mecanizan piezas de hierro forjado y fundido. Detectar las roturas de herramientas en las líneas de producción de automóviles puede ser todo un reto, ya que los cambios en las condiciones de corte, la variación de las tolerancias o las piezas asimétricas pueden provocar falsas alarmas. De hecho, si no se realiza un mecanizado adecuado en el taller, las desviaciones imprevistas pueden dañar las herramientas de corte, las máquinas-herramienta o la propia pieza.
¿Entonces, cuál es la mejor solución? Una de las respuestas está en el uso de sistemas de supervisión más sofisticados, que proporcionan un mejor control, así como de sistemas de IoT, que ayudan al trabajo esencial de los operarios en la línea de producción.
Decisiones digitales
Las soluciones que supervisan los procesos de mecanizado en tiempo real ofrecen a los fabricantes más oportunidades para solucionar los problemas que surgen durante el mecanizado. La tecnología de control de procesos emplea sensores dotados de algoritmos exclusivos que detectan y calculan las roturas de la herramienta en tiempo real, y si hay un problema, el sistema detendrá inmediatamente el avance y retraerá la herramienta. Esto ayuda a los fabricantes a resolver los problemas antes de que se produzcan tiempos improductivos.
La detección de colisiones y sobrecargas también se consigue mediante el control de la fuerza de mecanizado y de las vibraciones. El sistema supervisa la fuerza de mecanizado y las vibraciones durante la producción y detiene el avance si detecta una posible sobrecarga. Esto permite solucionar las colisiones con mayor rapidez, con lo que es menos probable que se produzcan situaciones catastróficas.
Ahora, vayamos un paso más allá en el concepto de mantenimiento predictivo. ¿Y si fuera posible asegurarse de que los recorridos de las herramientas son correctos antes de iniciar el mecanizado para mejorar el resultado final y minimizar las roturas imprevistas?
Para ello, el software CoroPlus Tool Path crea recorridos de la herramienta específicos para métodos de mecanizado como PrimeTurning, a fin de aumentar la productividad, la vida útil de las herramientas y la seguridad del proceso. El software crea códigos y técnicas de programación para configurar los parámetros y las variables correctas para una aplicación específica —como una línea de producción de automoción—, y garantizar así la máxima productividad. El software está basado en la nube y se puede acceder a él a través de un navegador, lo que permite la colaboración y el intercambio dentro de una empresa. El código de CN generado por el software puede editarse y exportarse fácilmente para su uso en la máquina, lo cual hace que los datos sean fácilmente accesibles para los trabajadores y ayuda a acelerar las operaciones y los procesos de planificación.
Los problemas de producción y las interrupciones en las líneas de producción de automóviles nunca podrán evitarse por completo. Sin embargo, la digitalización será crucial para minimizar los efectos de las paradas de producción y superar los retos de productividad, costes y tiempos improductivos a los que se enfrentan los fabricantes. Afortunadamente, a tenor de las conclusiones de IBM de que el 50% de los directivos del sector de la automoción afirman que sus organizaciones necesitan reinventarse digitalmente, parece inevitable que los beneficios de la transformación digital se extiendan por todo el sector. Las soluciones para la supervisión y el control de los procesos —como CoroPlus Tool Path— estarán a la cabeza de la digitalización de la industria de la automoción.