Fabricación de álabes aeronáuticos: desafíos en el proceso de fabricación
Es importante destacar la importancia de la industria aeronáutica para la economía española, ya que supone un 0,77% del valor total del PIB nacional, el 2,6% del total de las exportaciones nacionales, con una inversión en I+D+i de 936 millones de Euros y un tejido empresarial de más de 436 empresas, 17 centros tecnológicos, 6 clusters y 12 universidades [2].
![Figura 1. Aeronáutica, industria estratégica en la economía española [2] Figura 1. Aeronáutica, industria estratégica en la economía española [2]](https://img.interempresas.net/fotos/4134008.jpeg)
Asimismo, cabe destacar que empresas líderes en este ámbito, como Boeing y Airbus, tienen previsto duplicar la cantidad de aviones fabricados para la década de 2037. Además, ambas compañías coinciden en que alrededor del 70% de los aviones producidos serán de pasillo único, lo que conlleva la necesidad de reducir el peso y el tamaño de los componentes de la turbomaquinaria [3].
Sin embargo, es importante señalar que esta industria aeroespacial está sujeta a rigurosas regulaciones europeas y debe cumplir varios compromisos, entre los cuales destacan: mejorar la eficiencia operativa, reducir el ruido generado por las aeronaves en hasta un 65% y minimizar el consumo de combustible y disminuir las emisiones de gases a la atmósfera.
Alineado con los objetivos y compromisos definidos en términos de sostenibilidad, mejora de eficiencia y aumento de la productividad, el ámbito de fabricación juega un papel muy importante puesto que es una de las etapas de la cadena de valor más costosa y larga, sobre todo para componentes rotativos de alto valor añadido pertenecientes a algunas de las etapas del motor de la aeronave. Esto es, la fabricación de este tipo de piezas de alta calidad al precio más bajo posible y en el menor tiempo posible requiere de un análisis detallado en la fase de definición y desarrollo de los procesos de fabricación. Por lo tanto, hay algunas palabras claves que debemos tener en mente y abordaremos a lo largo del presente artículo: piezas de elevada exigencia, eficiencia y competitividad, avances tecnológicos, sostenibilidad y formación y desarrollo del talento.
Componentes rotativos críticos en el motor de avión
En primer lugar, se van a describir los componentes rotativos de los motores de avión que juegan un papel fundamental en el coste de fabricación de un motor. Así, entender los desafíos que se presentan para los fabricantes tanto de máquina-herramienta, fabricantes de herramientas y de utillajes, entre otros.
Tal y como se observa en la siguiente figura, podemos diferenciar entre tres geometrías rotativas diferentes. Por un lado, tenemos un Blisk (bladed disk) con álabes integrados. Este tipo de componentes combina la rueda del compresor y los álabes en una sola pieza, lo que resulta en un diseño más aerodinámico y liviano. Sin embargo, el principal desafío reside en la recuperación de piezas tras un defecto, tanto por uso como por error en el proceso de fabricación, puesto que descartar una pieza al completo por un problema en un único álabe no es viable desde un punto de vista sostenible ni económico.
Por otro lado, un conjunto con montaje de álabes independientes consta de una rueda con álabes que se unen de manera separada, lo que permite cierta flexibilidad en el reemplazo de álabes dañados. Por último, un impeller es una rueda del compresor que se utiliza para aumentar la presión del aire en un motor, pero no tiene álabes adjuntos, lo que lo hace más simple en diseño y menos eficiente en comparación con los Blisks y los álabes independientes ensamblados en términos de rendimiento aerodinámico.
Cada uno de estos componentes tiene sus propias ventajas y desventajas, y su elección depende de las necesidades específicas de la aplicación.
![Figura 2. Componentes rotativos críticos [4] Figura 2. Componentes rotativos críticos [4]](https://img.interempresas.net/fotos/4134009.jpeg)
A grandes rasgos, las principales características comunes a todos, en términos de desafíos desde el punto de vista de la fabricación, se pueden englobar en superficies de alta complejidad geométrica y superaleaciones de baja maquinabilidad de Titanio o base Níquel.
Complejidad de diseño
Este tipo de componentes rotativos están constituidos por superficies libres no desarrollables. Esto es debido a las necesidades fluido-dinámicas de funcionamiento, ya que se diseñan en base a unas especificaciones que condicionan dichas geometrías.
Esto presenta su propio desafío para el proceso de fabricación, ya que no permite técnicas de mecanizado convencionales en máquinas convencionales (2 ejes, 3 ejes, 3+1 ejes o 3+2 ejes), lo implica la necesidad de terminar dichas superficies mediante réplicas esféricas o copiado de bola.
Las superficies y las formas libres son un gran misterio que el mundo del mecanizado intenta resolver buscando un equilibrio de productividad, sostenibilidad y, alineado con la economía circular [5].
Materiales y desafíos de fabricación
Además de todas las dificultades derivadas de la geometría, tenemos que enfrentarnos a las dificultades intrínsecas del material. Este tipo de componentes, dado que trabajan bajo condiciones extremas, suelen estar compuestos de superaleaciones termorresistentes base Níquel o aleaciones de Titanio. Las primeras son capaces de trabajar y mantener las propiedades mecánicas hasta temperaturas de 600°C, y las segundas están pensadas para aligerar el peso dado que es una aleación muy ligera y que es capaz de trabajar como máximo a 400°C.
Por todo lo anterior, es imprescindible tener un proceso robusto para la fabricación de este tipo de componentes para poder asegurar y mejorar la eficiencia de los motores a corto, medio y largo plazo. Para conseguir dicho fin, no basta con simulaciones y modelos, sino que es necesario ensayar dichos componentes de manera real. Para ello, se utilizan bancos de ensayos para analizar el comportamiento de dichos componentes y, aprovechando el feedback de los resultados, realizar una optimización continua de dichos procesos.
A continuación, se presenta el desarrollo de un proceso robusto en un banco de ensayos para la fabricación de álabes aeronáuticos ensamblables, trabajando paralelamente con una metodología de medición y control. Este trabajo se ha desarrollado gracias a la financiación proveniente por el Ministerio de Ciencia e Innovación y la Agencia Estatal de Investigación del proyecto TASTE “Tecnologías aerodinámicas para turbofanes engranados (RTC2019-007194-4)”.
Proceso robusto para la fabricación de álabes aeronáuticos en un banco de ensayos
Inicialmente, hay que entender lo que implica fabricar una serie de componentes destinados a bancos de ensayos, puesto que hay unas pequeñas diferencias entre las piezas reales y las destinadas a este fin. Las piezas de bancos de ensayos son una réplica de las piezas reales de menor tamaño. Estas reducciones deben mantener las proporciones de las zonas críticas de dichos componentes, como son los radios de redondeo tanto en los extremos de los álabes como en la zona de unión con la superficie inferior. Sin embargo, el diseño de estos componentes para bancos de ensayo debe asegurar que representan el comportamiento que tienen esos componentes de tamaño real.
El proceso de fabricación en diferentes etapas que se va a mostrar a continuación, se ha diseñado para los álabes ensamblables del compresor de baja presión. Como este componente trabaja en la “zona fría” del motor, el principal interés es que sean componentes con peso reducido, por lo tanto, se elaboran en una aleación ligera de Titanio, Ti6Al4V. Este material presenta unas prestaciones que combinan alta resistencia, bajo peso, y alta resistencia a la corrosión; lo que supone una implicación directa en la eficiencia general del motor y en el consumo de combustible. Sin embargo, es conocido por los desafíos que presenta para los procesos de arranque de viruta, derivados de su baja conductividad térmica, el calor que se genera durante el proceso de corte y la alta afinidad química que conllevan una reducción de la vida útil de las herramientas de corte [6]. La figura 3 muestra la localización de este tipo de componentes dentro del motor de una aeronave.
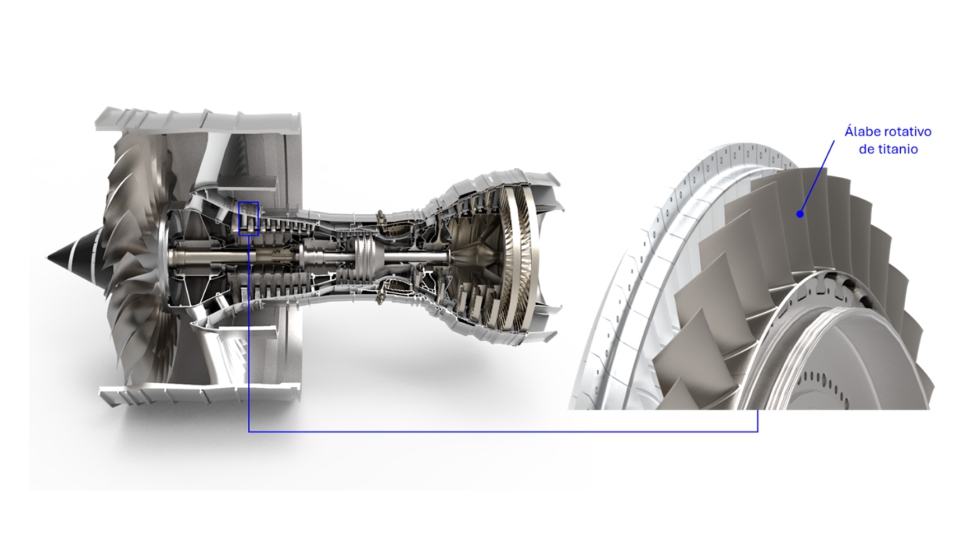
Metodología para componentes de bancos de ensayos: Simultaneando procesos
Cuando se trata de componentes de tan alto valor añadido como el que aquí nos ataña, la simultaneidad de diversos procesos o etapas de la cadena productiva con retroalimentación intercomunicada entre ellos puede ser una solución, no sólo para alcanzar los requisitos de excelencia, sino que también para optimizar el proceso de producción de una manera circular, como una rueda que no deja de girar. En este caso, se plantea un ciclo combinado de los procesos de mecanizado con los procesos de metrología y control, realizando un feedback constante entre ellos que permita realizar correctivos in situ.
La figura 4 recoge la metodología diseñada, combinando los procesos de fabricación que detallaremos más adelante con dos técnicas de inspección: máquina de medir por coordenadas (CMM) y escaneado. De esta manera, se pueden utilizar las observaciones y resultados que se van obteniendo durante el diseño del mecanizado sirven como inputs a la hora de abordar las estrategias de medición, y viceversa.
Es importante remarcar que, tal y como se muestra en la metodología, las piezas pasan por diferentes máquinas a lo largo del proceso, lo que puede suponer problemas de alineamiento y posicionamiento en cada una de las distintas etapas. Este problema se podría reducir/simplificar si las mediciones se pudiesen realizar dentro del mismo centro de mecanizado, aplicando un algoritmo con acciones correctivas y preventivas.
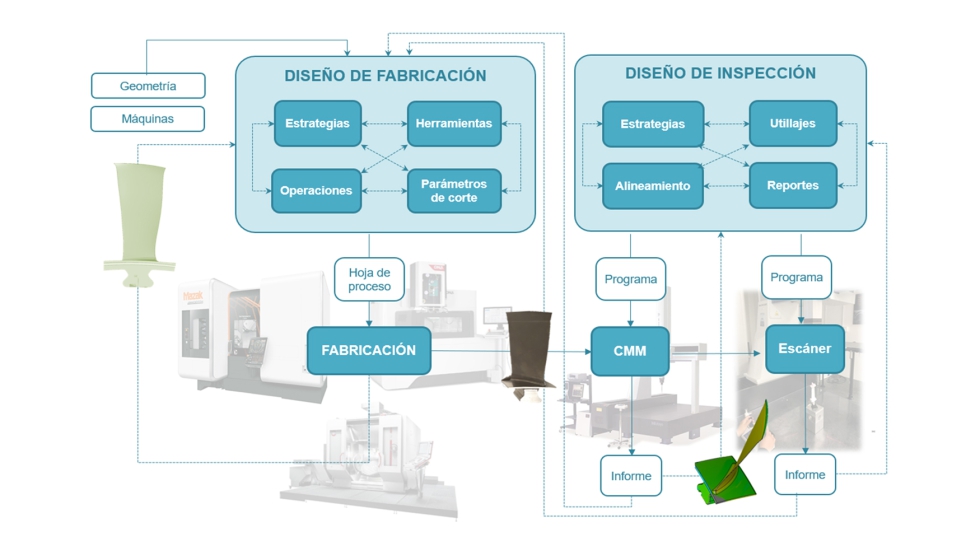
Comportamiento aerodinámico y elementos de unión: dos grandes quebraderos de cabeza
A nivel de calidad, las cotas de mayor exigencia dimensional se encuentran en aquellas zonas de contacto con otros elementos o críticas para el funcionamiento. Por lo que vamos a centrarnos en abordar la óptima fabricación del perfil aerodinámico que se genera en la superficie (exigencia de funcionamiento) y la cola de milano que permite ensamblar el elemento en un disco rotativo (zona de unión).
Por un lado, el perfil aerodinámico supone uno de los mayores retos debido a su complicada geometría. Dicha geometría combina los desafíos derivados de las paredes delgadas (gran esbeltez, vibraciones, marcas de mecanizado, flexión tanto de herramienta como de pieza durante el corte, etc.). Para lograr un acabado preciso y consistente, se ha mantenido una trayectoria constante en la operación de acabado, garantizando que la herramienta mantenga un contacto continuo con la pieza en todo momento. Esto es fundamental para evitar discrepancias en la superficie final, conocidas como discontinuidades o mismatches. El sobreespesor es relativamente alto en comparación con otras operaciones de acabado en diferentes piezas, lo que se traduce en una mayor rigidez de la pieza, mejorando la estabilidad en el corte. Sin embargo, un mayor sobreespesor también puede aumentar las fuerzas de corte y deformar la pieza, lo que se compensa con un paso pequeño que reduce las fuerzas y mejora la rugosidad teórica. Además, las vibraciones durante el proceso afectan negativamente a la rugosidad y aumentan el error dimensional en la pieza final. Por lo tanto, se ha buscado una orientación que reduzca la fuerza transversal normal a la superficie, que es la que genera flexiones en la pieza.
Para abordarlo y alcanzar las tolerancias adecuadas, se ha planteado una serie de ensayos con diferentes orientaciones de herramienta realizando operaciones de torno-fresado, para poder seleccionar las condiciones y situaciones óptimas y más productivas para dicha fabricación, tal y como se muestra en la figura 5.
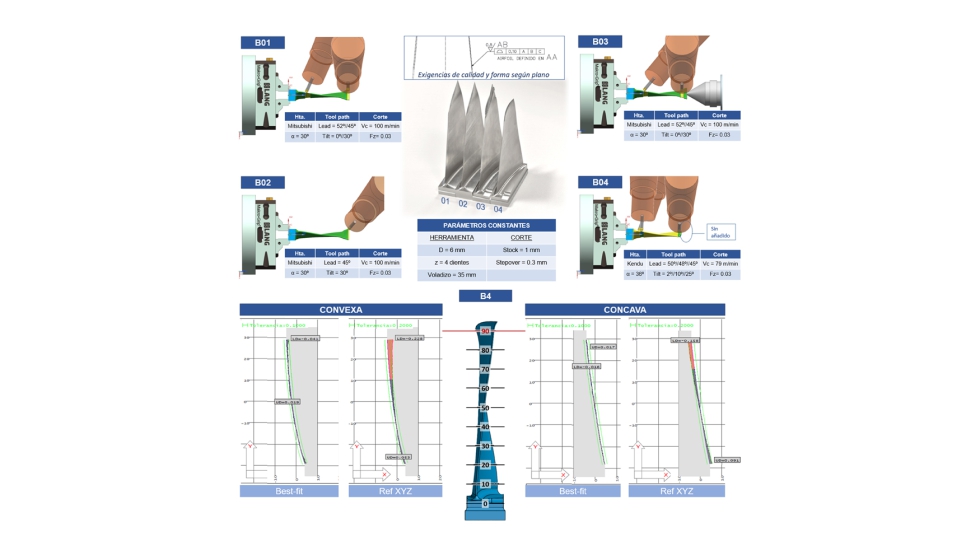
Por otro lado, la cola de milano, conocida como ‘dovetail’ tiene unas exigencias geométricas por debajo de las 10 µm, algo que no se puede conseguir fácilmente con cualquier proceso de mecanizado. Este elemento de unión va a ser ensamblado en un disco que dispone de los negativos de dichas geometrías. Esos negativos se realizan mediante el proceso de brochado, donde una herramienta (brocha) dispone de unos dientes que van aumentando su tamaño para llegar a alcanzar la forma final de las ranuras, dentro de tolerancias y asegurando una alta repetitividad a lo largo de todas ellas. Las técnicas de Electroerosión por penetración (SEDM) y Electroerosión por Hilo (WEDM) pueden ser un gran aliado para la fabricación de estas colas de milano, dado que son procesos que nos ofrecen unos acabados del orden de micrómetros y con una calidad superficial difícil de alcanzar por otro tipo de procesos. La principal desventaja es el elevado tiempo que implica dicho proceso.
A continuación, se muestra cómo se ha abordado el ajuste y la compensación del hilo en WEDM para poder asegurar que las geometrías alcanzaban las tolerancias exigidas. En la figura 6 se presentan los diferentes ensayos realizados para definir los parámetros de proceso que se recogen en la tabla.
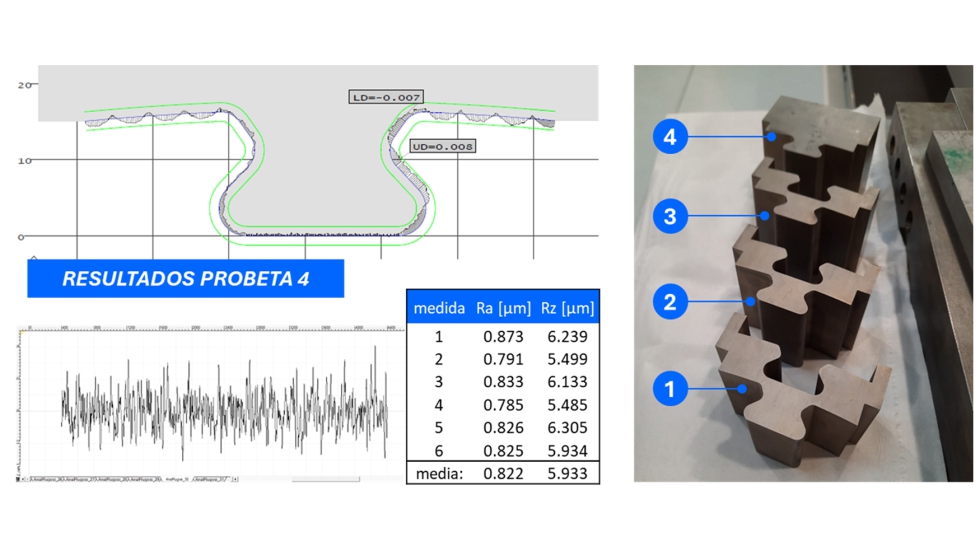
Fabricación híbrida: una realidad para aumentar la productividad
Uno de los avances más significativos que tienen repercusión directa en la productividad es la fabricación híbrida. La fabricación híbrida consiste en combinar diferentes procesos de fabricación para alcanzar diferentes objetivos, como puede ser reducir el desperdicio de material (fabricación aditiva y sustractiva), optimizar tiempos de fabricación (fabricación sustractiva y otros procesos no convencionales) o conseguir mejores acabados superficiales (fabricación sustractiva con procesos abrasivos).
Para la fabricación de la cola de milano, se plantea el siguiente esquema combinando electroerosión por hilo (WEDM) para conseguir las geometrías más críticas con un acabado menor a 10 µm. Sin embargo, se ha combinado con un fresado convencional para mecanizar las zonas de menor accesibilidad para el hilo, y por tanto mayores tiempos de fabricación (cambios de posicionamiento, diferentes amarres, etc.). El esquema que se muestra a continuación contiene las etapas que se han realizado en la fabricación de dichos componentes. Cabe destacar que, puesto que es una de las zonas con tolerancias más estrictas, entre el mecanizado y el corte por EDM se realiza una medición mediante la cual se busca reducir al máximo los errores de posicionamiento.
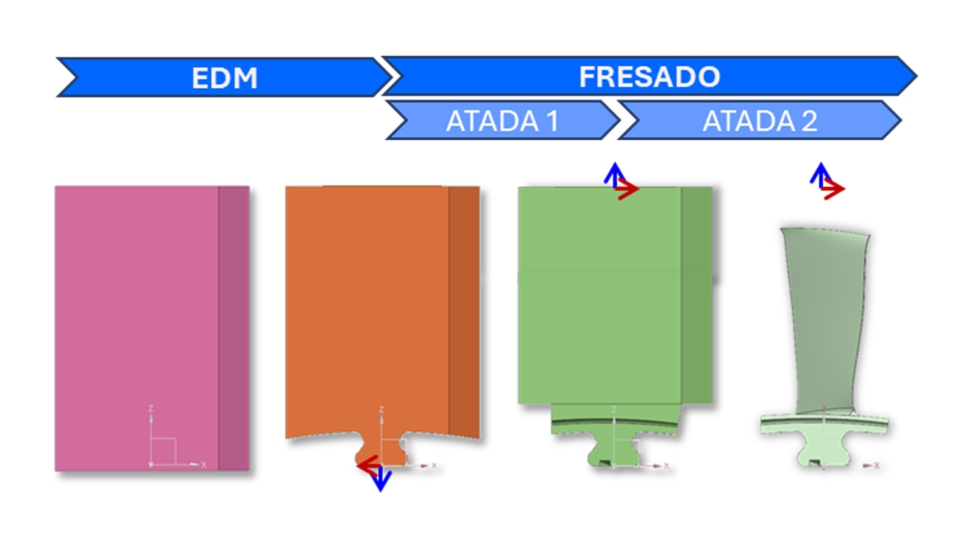
Conclusiones
Como se ha podido apreciar, los constantes avances en el ámbito de la aviación, conllevan desafíos constantes en los procesos de fabricación, ya que tienen que ir mejorando día a día (eficiencia, productividad, sostenibilidad, etc.). En esta situación, innovar en procesos de fabricación de álabes para los bancos de ensayo juegan un papel fundamental puesto que permiten, no sólo someter a ensayos este tipo de componentes en la fase de desarrollo y en la evaluación final de sus propiedades mecánicas, sino también logran avanzar en la búsqueda de nuevas técnicas de fabricación que se traduzcan un aumento de la productividad permitiendo a Europa continuar como líder en el sector aeronáutico.
Referencias
[1] Agenda estratégica de investigación, desarrollo e innovación en aeronáutica 2019 – 2030, Plataforma Tecnológica Aeroespacial Española.
[2] Agenda sectorial de la industria aeronáutica, Tedae (Defensa, Seguridad, Aeronáutica y Espacio), Ministerio de Industria, Comercio y Turismo del Gobierno de España.
[3] ‘Airbus 2017 Global Market Forecast: Global Networks, Global Citizens 2018-2037’
[4] González, H.; Calleja, A.; Pereira, O.; Ortega, N.; López de Lacalle, L.N.; Barton, M. Super Abrasive Machining of Integral Rotary Components Using Grinding Flank Tools. Metals 2018, 8, 24. https://doi.org/10.3390/met8010024
[5] G. Gómez-Escudero y H. González Barrio, A. Del Olmo, G. Urbikain, Amaia Calleja Ochoa); y L.N. López de Lacalle Marcaide, ‘Superficies y formas complejas: siempre un reto’
[6] Kahya et al. Precision and energy-efficient ball-end milling of Ti6Al4V turbine blades using particle swarm optimization. International Journal of Computer Integrated Manufacturing 2021. Vol.34 pp.110-33. https://doi.org/10.1080/0951192X.2020.1858504.
Congreso Nacional de Ingeniería Mecánica (CNIM XXIV): Innovación, Ciencia e Industria
El Congreso Nacional de Ingeniería Mecánica se realiza bianualmente y es el principal lugar de encuentro para el intercambio de conocimiento científico y técnico, de experiencias profesionales y de proyectos competitivos en el campo de la Ingeniería Mecánica a nivel nacional.
La asistencia y participación en este entorno científico-industrial permite consolidar alianzas entre los diferentes expertos para seguir trabajando con el objetivo de dar solución a los desafíos presentes y futuros de este tipo de componentes. Así como el análisis de nuevos materiales, procesos y enfoques para dar un valor añadido adicional a la industria estatal.
Alineado con los desafíos aquí presentes, desde el Centro de Fabricación Avanzada Aeronáutica (CFAA-UPV/EHU) se presentaron los avances significativos relativos a otro componente rotativo crítico del motor de avión, una carcasa aeronáutica. Este componente comparte gran parte de los desafíos que se citan en el presente artículo, como son los materiales de baja maquinabilidad, vibraciones y amarres derivados de paredes delgadas y las complejidades presentes en las geometrías. Todo ello sin sacrificar la integridad superficial de dichos componentes.
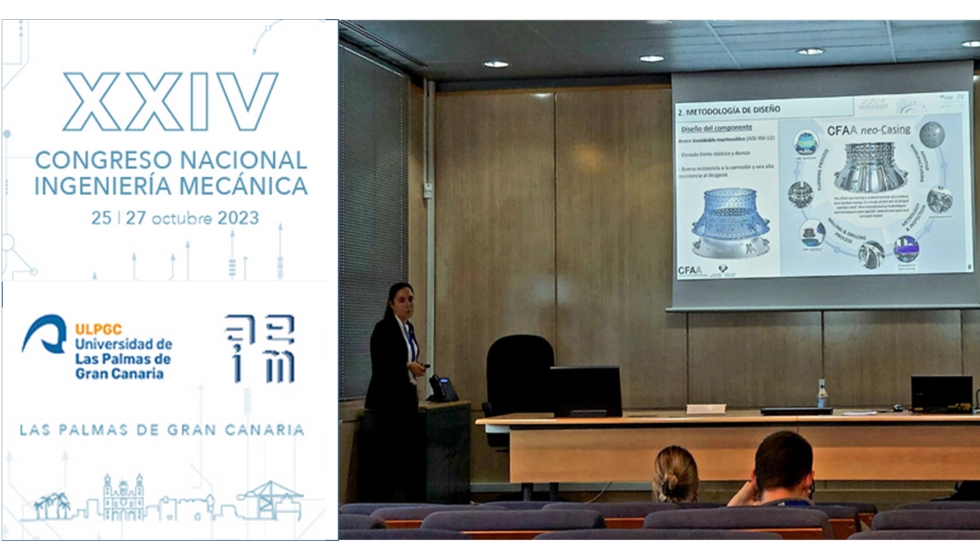