Los retos en la fabricación de los componentes ‘Near Net Shape’. Sencillo pero complejo
Cada producto es un mundo, pero desde el punto de vista de su proceso de fabricación este se puede dividir en dos grandes etapas: los procesos primarios y los procesos secundarios. Los llamados procesos primarios podrían definirse como aquellos donde se le da una primera forma a la pieza. Por otra parte, los procesos secundarios serían el conjunto de operaciones que transforman parcial o completamente la preforma en la pieza final. Por ejemplo, un proceso de fabricación típico de carcasas de turbina aeronáutica parte de un anillo troncocónico forjado. Esta preforma se tornea dejando toda la geometría de revolución dentro de tolerancias. Posteriormente se mecanizan el resto de geometrías, como pueden ser taladrado de agujeros o fresado de bosses (elementos que hacen posteriormente de unión con otros componentes como pueden ser ductos o sensores). En este caso, el proceso de forja de la preforma es el proceso primario, mientras que las operaciones de mecanizado (torneado, fresado, taladrado, etc.) pertenecen al proceso secundario. Finalmente, se podrían mencionar los procesos de acabado como desbarbado o cepillado, con el fin de mejorar el acabado superficial o la precisión dimensional.
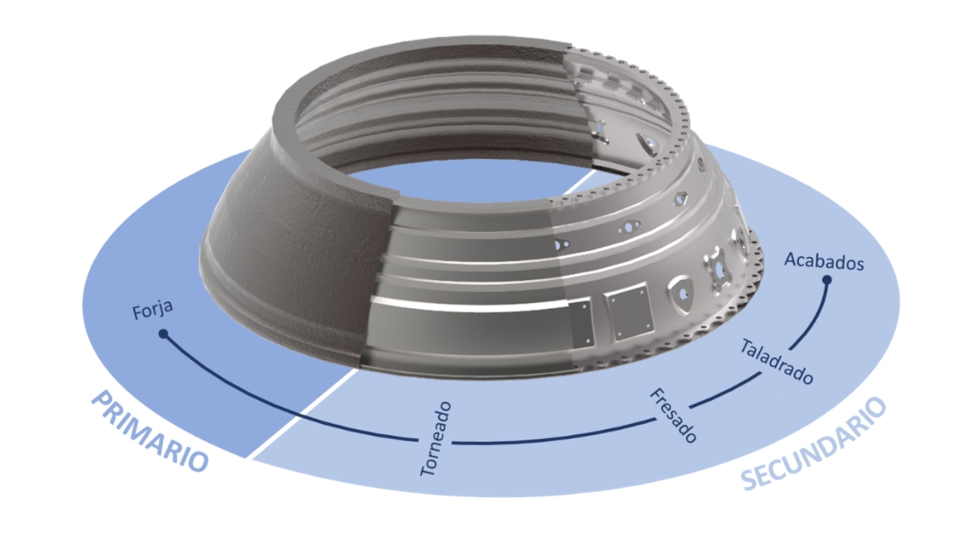
Habitualmente se habla de procesos NNS de aquellos procesos primarios donde se aplica este concepto. Un ejemplo muy popular actualmente en la industria es la fabricación aditiva, la cual tiene una capacidad para producir piezas complejas con alta precisión a partir de materiales en polvo o filamento, mediante el depósito sucesivo de capas de material. Esta tecnología permite obtener una pieza muy cercana a su geometría final, reduciendo el volumen de operaciones posteriores. No obstante, otros procesos más tradicionales como son la fundición y la forja llevan años desarrollándose en esta línea. El proceso de microfusión, también conocido como fundición a la cera perdida, es el máximo exponente del ‘Near Net Shape’ Casting, el cual permite lograr productos de geometría compleja con un gran acabado superficial. Para brindar una visión general de las capacidades del proceso, tras el desmoldeo en la microfusión, las operaciones secundarias son, en la mayoría de los casos, prácticamente de rectificado y rebabado, procesos enmarcados como de acabado, para obtener superficies más lisas, uniformes y precisas en términos dimensionales y de forma.
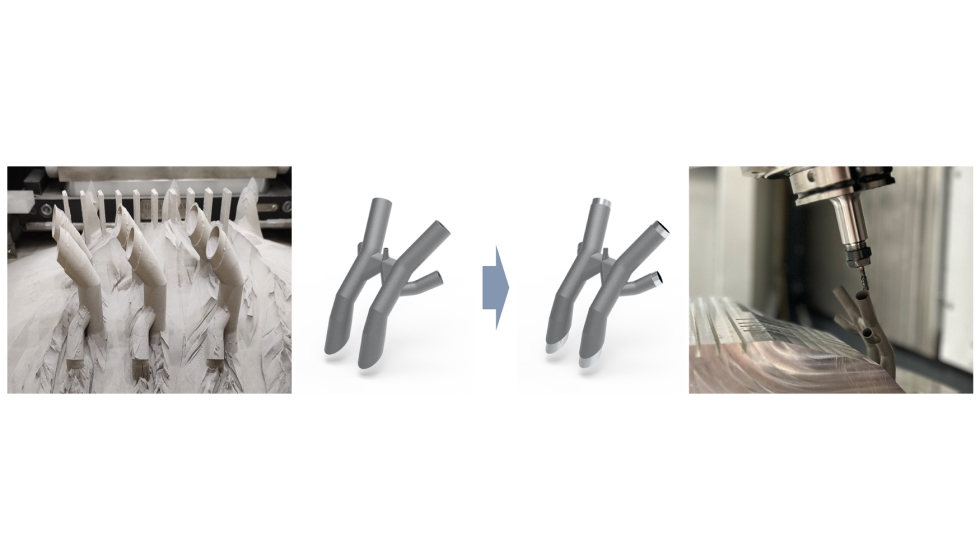
Aunque el concepto ‘Near Net Shape’ es casi elemental y que todo fabricante lo aplica de manera consciente o inconscientemente a la hora de mejorar o definir su proceso, su solución entraña numerosos retos. En primer lugar, las tecnologías de procesos primarios NNS tiene como objetivo avanzar en:
- Optimización de la geometría: lograr la geometría más cercana posible a la forma neta es clave para reducir el tiempo y los costes de las operaciones de acabado posteriores. Para ello, es necesario desarrollar nuevas técnicas de diseño y simulación que permitan optimizar la geometría de la pieza desde la fase de diseño, considerando las operaciones que se aplicaran a esta.
- Control del proceso: los procesos primarios de fabricación suelen ser muy complejos y se ven afectados por numerosas variables como la temperatura, la velocidad de enfriamiento, la composición del material. Para mejorar el NNS es necesario controlar todas estas variables de forma precisa y constante, lo que requiere de nuevas tecnologías de monitorización y control de procesos que permita garantizar un proceso estandarizado y uniforme.
- Reducción de residuos: aunque el NNS permite reducir la cantidad de material utilizado en la fabricación de una pieza, aún se generan residuos en la operación de acabado posterior. Para minimizar el impacto ambiental, es necesario desarrollar nuevos procesos de fabricación y acabado que reduzcan la generación de residuos y permitan su reciclaje o reutilización.
A todo ello se debe sumar que no solo los procesos de fabricación se desarrollan en este sentido, sino que el propio diseño del producto también busca optimizar material y geometría ajustándose a sus funciones, sobre todo en sectores como el aeronáutico donde el peso es un factor fundamental.
Los componentes NNS en los procesos secundarios
Hasta ahora se ha hablado de los procesos primarios, que son los que proporcionan las preformas. Sin embargo, si separamos el proceso primario del secundario, como sucede en gran parte de la industria, el secundario ha de asumir una responsabilidad mayor, ya que es este quien normalmente proporciona la pieza final. Los procesos secundarios tienen que ser capaces de absorber errores o desvíos en la pieza proveniente de proceso primario. La geometría final ha de quedar comprendida dentro del bruto o preforma, por lo que el mecanizador ha de conocer y tener la habilidad de trabajar con la incertidumbre del proceso primario. Por otro lado, las piezas traen consigo un estado tensional desconocido por lo que al ser procesado en el mecanizado la liberación de estas tensiones puede hacer que la pieza se deforme, pudiendo suponer el rechazo de esa pieza en el peor de los casos. Téngase en cuenta que cuanto más cercana sea la preforma a la forma final el margen de acción/corrección es cada vez menor, por lo que no solo las operaciones y herramientas han de ser muy precisas, sino que también las técnicas y elementos de fijación, así como el posicionamiento y referencia de pieza en máquina tiene que velar en la misma sintonía.
La aproximación de preformas a la geometría final hace que algunos conceptos cobren mayor importancia:
- Tensiones residuales. Las tensiones residuales son fuerzas internas que quedan dentro de un material sólido después de haber sido fabricado, procesado o deformado plásticamente. Estas tensiones pueden ser causadas por una variedad de factores, incluyendo la variación de temperatura durante el proceso de fabricación, la deformación plástica en la materialización de una forma o la eliminación asimétrica del material durante el procesamiento. Las piezas provenientes de procesos primarios no son ajenas a estas tensiones, por lo que los procesos secundarios parten de una pieza tensionada. Por cada operación de transformación que se realiza sobre ella, estas fuerzas internas evolucionan de manera que pueden distorsionar la pieza de manera indeseada. Normalmente estas tensiones son desconocidas, pero no por ello inexistentes. Se trata de un problema muy común en la industria del arranque de viruta que tras mecanizar la pieza y liberarla de sus fijaciones, esta se deforma. Llegar a predecir la evolución de estas distorsiones en función de las estrategias de mecanizado permitiría trabajar con demasías de material mucho más ajustadas.
- Posicionamiento en máquina. El posicionamiento de la pieza en la máquina es fundamental en los procesos secundarios. Se trata del enlace entre lo virtual y la realidad. En mecanizado, todas las operaciones se programan en base a una referencia ideal, que posteriormente se reproducen respecto a una referencia real, “palpable”. Dicha referencia, conocida como referencia de pieza o cero-pieza, normalmente se sitúa en esquinas escuadradas o sobre elementos de simetría que la sonda puede medir. No obstante, el bruto o preforma real siempre tiene su error, bien de forma o dimensional, por lo que siempre se va a inducir cierto error entre la referencia real y la virtual. Si las demasías de la preforma respecto a la pieza final son superiores a este error, este mismo desaparece. Puede decirse que el sobreespesor determina el margen de maniobra que se tiene en el mecanizado para absorber los errores provenientes del proceso primario, por lo que si la preforma es muy cercana a la pieza final, este margen es muy pequeño y su posicionamiento se vuelve fundamental para que la pieza quede contenida en ella.
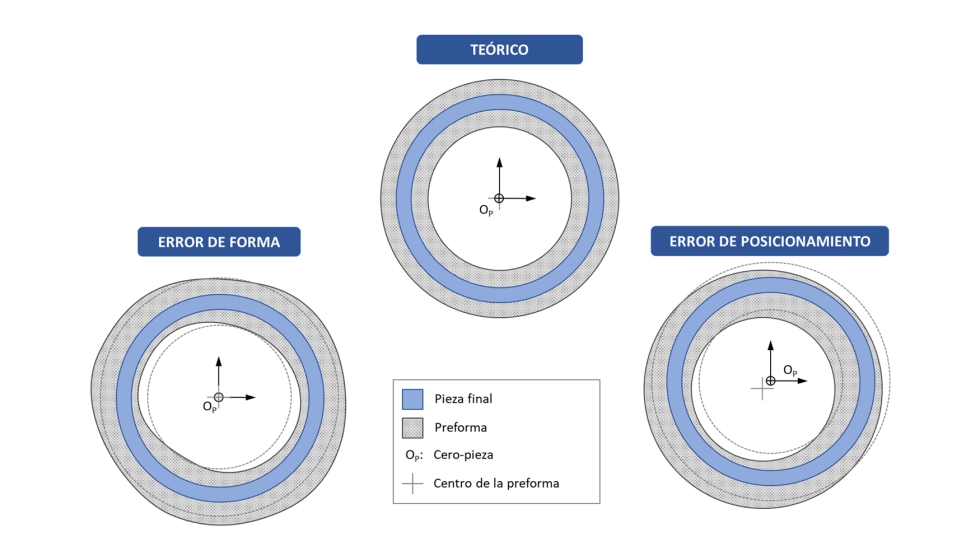
- Complejidad geométrica. Las piezas a mecanizar a menudo presentan varios retos debido a la geometrías o tolerancias ajustadas del diseño. Ejemplo de ello, son las paredes delgadas, susceptibles a vibraciones y deformaciones durante el proceso de corte, lo que dificulta el proceso y puede llevar a piezas dañadas o defectuosas. Por otro lado, las superficies libres, que dificultan una sujeción sólida, puede vibrar dañando la superficie a mecanizar. Para superar estos desafíos, es importante seleccionar la herramienta y el enfoque adecuados para cada pieza y garantizar un proceso de mecanizado preciso y eficiente.
- Utillajes y elementos de sujeción. En línea con el punto anterior, la geometría muchas veces carece de planos, caras paralelas u otras características en las que se apoyan los elementos convencionales de sujeción, si no que se han de emplear utillajes ad hoc para su fijación en máquina. Por ejemplo, componentes del sector aeronáutico como los álabes de turbina o de compresor emplean este tipo de herramientas no solo para su fijación, sino también sirven de referencia para el posicionamiento o para rigidizar los componentes en operaciones críticas.
Un enfoque de proceso secundario ideal que dé respuesta a los avances en componentes NNS sería el siguiente: supóngase un fabricante experto mecanizador que debe realizar una nueva pieza cuya preforma proviene de un proceso NNS. En primer lugar, el fabricante realiza una serie de pruebas para conocer el estado inicial de su pieza, tanto geométrico como tensional. Su resultado son los datos de partida para el diseño del proceso de fabricación, donde a través de simulaciones es capaz de predecir la evolución de las tensiones y distorsiones generadas a lo largo de las sucesivas operaciones. Gracias a este análisis es capaz de elegir una estrategia óptima en la que las distorsiones están controladas. Además, la pieza se trabaja en un centro avanzado de mecanizado de la que se extraen señales junto a las que proporcionan sus utillajes sensorizados y con las que se puede replicar en un entorno virtual todo el proceso. Estas señales no solo sirven para monitorizar y controlar el proceso activo, sino que también entrenan al modelo de predicción de distorsiones.
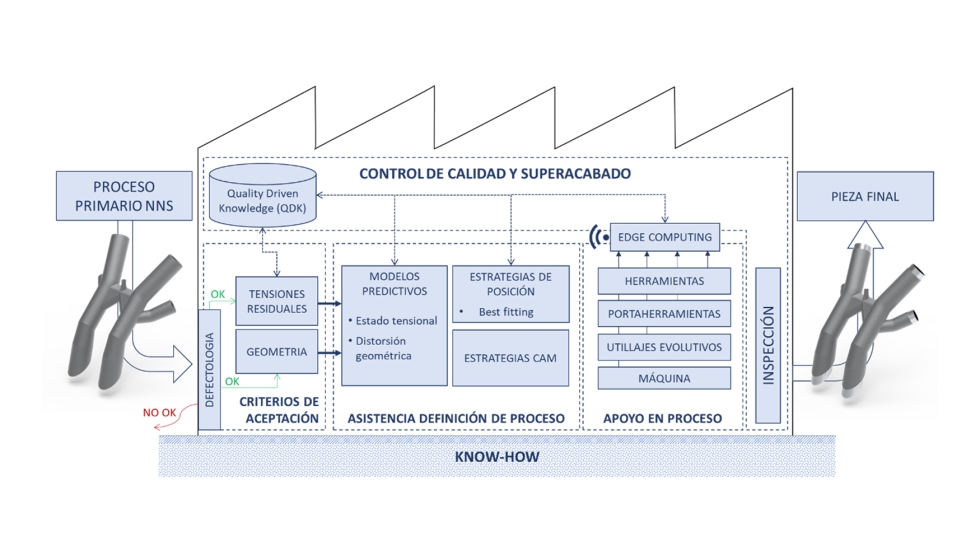
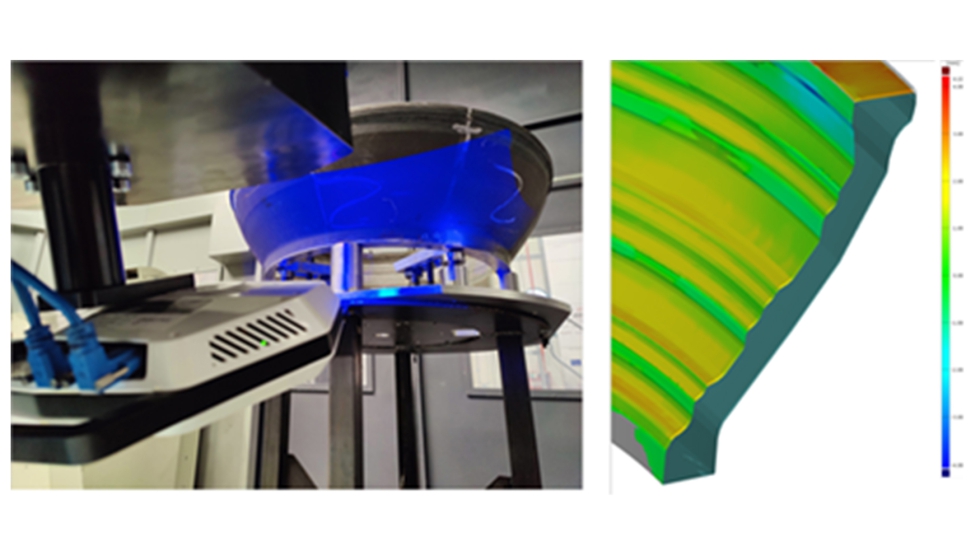
En conclusión, el concepto ‘Near Net Shape’ es fundamental en la industria moderna, ya que permite obtener piezas con geometrías complejas y reducir costos y tiempos de producción. Para lograrlo, se requiere una optimización en el diseño de la pieza y en el control del proceso de fabricación, así como un desarrollo en los procesos secundarios de acabado y mecanizado para absorber los errores y desvíos de las preformas obtenidas en los procesos primarios. La aproximación de preformas a la geometría final requiere de herramientas y técnicas precisas, y de un correcto posicionamiento y fijación de las piezas en las máquinas de mecanizado. En definitiva, el concepto ‘Near Net Shape’ supone un desafío constante para la industria, que requiere de un constante desarrollo y mejora en los procesos de fabricación y acabado. Menos material, menos tolerancias, menos operaciones, menos costes implican un mayor desarrollo en tecnología y conocimiento y más valor añadido. ‘Menos es más’.
Proyecto CRESCENDO en el CFAA. En busca de calidad
Con el auge y rápido desarrollo de procesos primarios cada vez más eficientes y cercanos a la geometría final, como por ejemplo la fabricación aditiva o la microfusión, son varios los nuevos proyectos relacionados que se abordan en el CFAA. Un claro ejemplo es el proyecto liderado por Ibarmia de título “Sistemas de producción para control exhaustivo de calidad en componente mecanizados desde nuevos procesos primarios” en el que participan Ibarmia, UPV/EHU y Tecnalia como desarrolladores de tecnología. Se trata del proyecto de acrónimo CRESCENDO, referencia CPP2021-008932, financiado por MCIN/AEI/10.13039/501100011033 y por la Unión Europea ‘NextGenerationEU’/PRTR.
A diferencia de otros proyectos relacionados con componentes NNS que se focalizan en el desarrollo de tecnologías de proceso, el proyecto CRESCENDO plantea una visión más transversal. Su enfoque coloca la calidad de la pieza final en el centro del proceso de mecanizado, considerándolo como un largo camino que comienza con un proceso primario emergente que produce una pieza UNNS. Normalmente, el enfoque se centra en la etapa intermedia del estado de la herramienta o de la propia máquina. Sin embargo, CRESCENDO propone un enfoque radical que permitirá definir un modelo desde los datos del proceso hasta la calidad final de la pieza, mediante la vinculación de los datos con la calidad final. La siguiente gráfica muestra las tecnologías involucradas para componentes de muy alta precisión, desde una perspectiva holística, donde se incluye la tecnología de sensores virtuales y físicos, y el uso de sistemas de gestión de información local (edge computing) y la nube, que se utilizarán para la integración de datos del proceso.
Las tecnologías clave que se desarrollarán dentro del proyecto CRESCENDO y que contribuirán a esta solución holística para componentes de alta precisión son:
- Caracterización de tensiones residuales de preformas ultra-near-net-shape.
- Simulación de fenómenos poco estudiados, como la evolución de tensiones residuales en una preforma cuando se elimina parte del material por mecanizado, y las distorsiones geométricas asociadas.
- Estrategias de control para la acción correctiva en tiempo real de deformaciones estáticas y dinámicas sufridas por preformas UNNS.
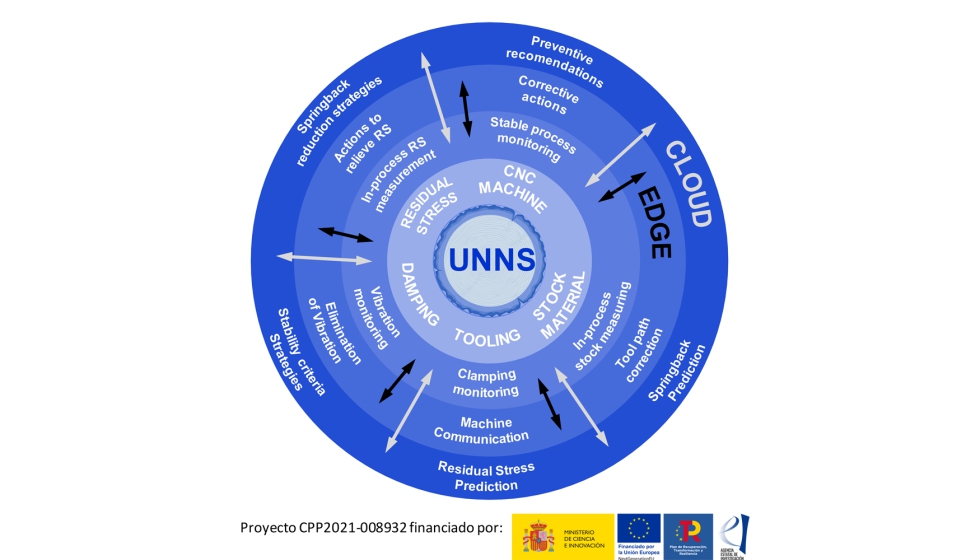