Aplicación de la simulación numérica a los procesos de fundición de metales
En fundición, existen dos factores determinantes para la obtención de piezas de elevada calidad:
• Diseño de colada (configuración de los canales de colada, sistemas de ataque, sistema de salida de gases, etc.)
• Equilibrio térmico del molde (temperatura superficial, temperatura de colada, tiempo de solidificación, etc.).
La optimización de estos factores entraña una gran complejidad, debido fundamentalmente al elevado número de variables que intervienen en el proceso y a la dificultad de predecir su comportamiento de antemano. En la actualidad existen herramientas de simulación que nos permiten la optimización de estos factores, a la vez que reducen considerablemente el tiempo empleado en el diseño de molde y garantizan su eficacia en producción desde las primeras coladas.
La simulación de procesos de fundición consiste en reproducir en un ámbito computacional todas las etapas involucradas en el proceso de obtención de una pieza, tanto para materiales ferrosos como no ferrosos:
• La generación del modelo,
• La generación del molde,
• El proceso (por gravedad, inyección u otra técnica).
Una de las principales razones por las que se puede destacar los beneficios de la simulación de la fundición es que la técnica prueba-error está cada vez más desestimada por antieconómica. Mediante la simulación, es posible mejorar e incluso prevenir que aparezcan defectos en piezas. Las principales ventajas de la simulación son:
• Detección en forma virtual de posibles defectos de fundición (ferrosos y no ferrosos), entre otros, micro y macros rechupes, porosidad gaseosa y mal llenado de las piezas.
• Ensayo de soluciones en forma interactiva y rápida antes de fundir.
• Minimización de la técnica prueba-error, cada vez más desestimada por antieconómica.
• Obtención de información de variables físicas (presión, velocidad, temperatura) en zonas que por lo general es casi imposible medir en un proceso real.
• Visualización del llenado del molde y la solidificación del metal, cosa imposible en la práctica.
• Estimación de las propiedades mecánicas, esfuerzos térmicos y distorsiones, así como de la microestructura resultante de las piezas.
• Se mejora la productividad y calidad del producto, disminuyendo el tiempo de desarrollo de nuevos diseños y desarrollando partes de mayor complejidad.
• Mayor fiabilidad del proceso.
Existen en el mercado numerosos programas y herramientas capaces de simular la fundición del metal en el molde y que ofrecen la posibilidad de modificar las características tanto de los materiales como del proceso en sí, simulando posibles fallos.
Con el fin de analizar las posibilidades que ofrece la simulación de procesos de fundición, se ha simulado el proceso de fundición de dos piezas de aluminio mediante el software Novaflow&Solid.
En el primero de los casos se ha simulado el proceso de una pieza fabricada mediante inyección a presión en cámara fría y en el otro caso se trata de una pieza fabricada mediante fundición por gravedad. Como resultado de las simulaciones se han obtenido el avance del metal durante el llenado, la evolución de las distintas variables del proceso durante el llenado y solidificación y la estimación de la contracción y porosidad en las piezas, comparándose los resultados con los obtenidos en el proceso real.
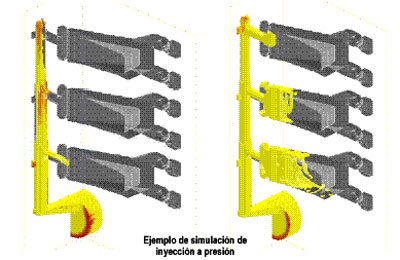
Ricat, Red de Investigación Cooperativa Aplicada Transpirenaica
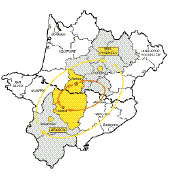
Ricat es un proyecto enmarcado dentro del eje 2: Fomentar las actividades y el empleo, y en la medida 7: Desarrollar la investigación y la transferencia de tecnologías, correspondiente al Programa Interreg IIIA Francia/España 2000-2006 de la Unión Europea.
Los socios del mismo son:
• En España,
• El Instituto Tecnológico de Aragón - ITA, jefe de filas del proyecto.
• La ASociación Aragonesa de empresas constructoras de Moldes y Matrices - Asamm.
• En Francia,
• La Escuela Nacional de Ingenieros de Tarbes - ENIT.
• La Cámara de Comercio e Industria de Tarbes y Altos Pirineos - CCITHP.
El proyecto consiste en el establecimiento y desarrollo de una estructura o red de cooperación técnica en investigación, desarrollo e innovación en diferentes temáticas relacionadas con la mecánica y los nuevos materiales, que comparta conocimientos, herramientas e instalaciones, y que genere estudios comunes sobre temáticas relacionadas, pudiendo ser utilizada por agentes económicos, especialmente pymes, de las provincias fronterizas de Huesca (España) y Haute Pyrenees (Francia) y las limítrofes a éstas.
La presentación del estudio de aplicación de la simulación numérica a los procesos de fundición de metales mostrada en las Jornadas Técnicas es uno de los primeros resultados obtenidos en cooperación entre los socios de la red Ricat.