La compensación geométrica de las máquinas de medición por coordenadas
Premisa
Los errores geométricos
Máquinas de puente
Los errores fundamentales (los parámetros) de los que se ocupan los algoritmos de compensación son un total de 21 en las máquinas de puente: 9 errores de traslación (6 de linealidad, 3 de posicionamiento), 9 errores de rotación y 3 errores de cuadratura.
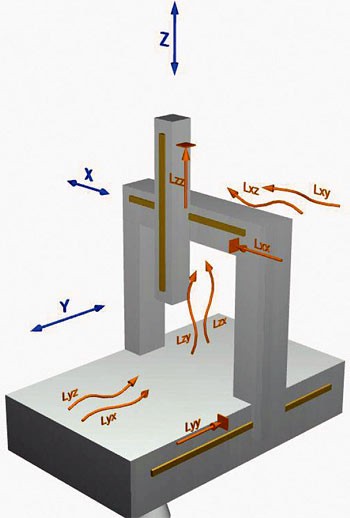
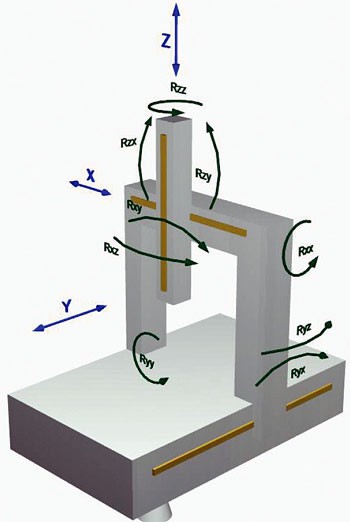
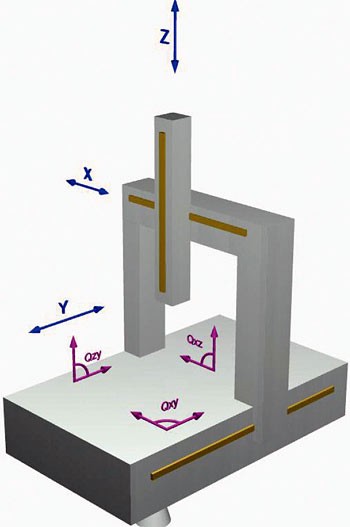
Lxx, Lyy, Lzz | Errores de posicionamiento de los ejes, debidos a la respuesta de las reglas ópti cas y a la rotación de los ejes. | Fig. 1a |
---|---|---|
Lxy, Lxz Lyx, Lyz Lzx, Lzy | Errores de linealidad de los ejes respecto a los ejes transversales. Se deben a la linealidad imperfecta de los trayectos de desplazamiento y a los efectos de rotación de los ejes. | Fig. 1a |
Rxx, Rxy, Rxz Ryx, Ryy, Ryz Rzx, Rzy, Rzz | Errores de rotación de los ejes entorno a cada uno de los 3 ejes. Con las disposiciones de una embarcación se denominan rool, pitch y jaw. Se deben a la linealidad imperfecta de los trayectos de desplazamiento y a las deformaciones estructurales producidas durante el ensamblaje. | Fig. 1b |
Qxy, Qyz, Qzx | Errores de cuadratura entre parejas de ejes. Se deben a las imperfecciones de ensamblaje de la estructura. | Fig. 1c |
Máquinas gantry
Máquinas de brazo horizontal
El primer parámetro, denominado Rcx, tiene en cuenta la rotación rígida del montante respecto al eje longitudinal causada por las deformaciones de la estructura a las que va unido el montante (Fig.2).
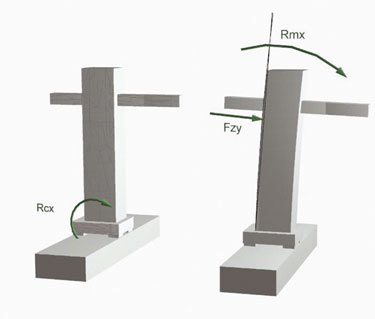
Estos 3 componentes de corrección completan, para las máquinas de brazo horizontal, el modelo de compensación que ya se ha descrito para las máquinas de brazo vertical.
En el caso de las máquinas horizontales de brazo doble son válidas, por separado, todas las consideraciones precedentes. Los errores debidos a la correlación de los dos brazos se compensan en la gestión del sistema de referencia que es común a los dos volúmenes de medición.
Medición de los errores y su compensación
Estas operaciones se hacen aplicando al cabezal de herramientas de la máquina los instrumentos oportunos que permitirán medir los errores de rotación y de traslación de cada uno de los ejes. Cada proceso se divide en pasos, que dependen del tipo de máquina y de la precisión que se quiere obtener.
Seguidamente se describen las fases principales de compensación. Al finalizar cada fase los valores que se obtienen se introducen en el mapa de compensaciones y rendición para poder corregir el efecto de estos errores.
1ª fase: Errores de rotación
Para medir los errores de rotación Rxx, Ryy se utilizan niveles electrónicos de precisión montados en el cabezal de la máquina. Estos valores se pueden medir de forma diferencial respecto a los que se obtienen de otros niveles (niveles de referencia) situados en la mesa.
Para medir el resto de errores de rotación se utiliza un láser interferométrico.
La rotación relativa entre el retrorreflector (óptico que, en este caso está montado en un cabezal de la máquina) y el interferometro (óptico de referencia) la lee el láser mediante los diferentes pasos de compensación que se consiguen a través del eje que se está midiendo.
Así como por el nivel de referencia, incluso el óptico de referencia tendrá que ser sólido con la mesa de las piezas.
2ª fase: Error de roll del eje Z
Esta fase es delicada y compleja. Esta rotación no se puede medir con los métodos que ya hemos descrito.
Normalmente se mide la linealidad láser (esto se describe más adelante). El óptico montado en el cabezal de la máquina se aplica a saltos, algo que puede ser más o menos largo. Así, la lectura diferencial entre dos mediciones obtenidas con el espaciamiento (offset) oportuno del óptico ofrecerá los valores que se buscan.

3ª fase: Errores de linealidad (rectilinealidad)
Se miden con el láser interferométrico. Para detectarlos se utilizan unos componentes ópticos que permiten tomar las desviaciones transversales que el óptico móvil (montado en el cabezal de la máquina) cumple respecto a un óptico de referencia durante los movimientos por el eje de medición. El óptico fijo (retrorreflector) se sitúa normalmente en el lado opuesto del cabezal láser.
4ª fase: Errores de posicionamiento y errores de cuadratura
Los errores de posicionamiento normalmente se detectan con el láser interferométrico. De forma parecida a las rotaciones, el retrorreflector se monta en el cabezal de la máquina y el interferometro será el óptico de referencia. Este se sitúa cerca del cabezal láser.
En la fase de detección de los errores de posicionamiento, es importante tener en cuenta la temperatura de las reglas ópticas, a causa de su expansión térmica. El procedimiento de compensación prevé que la temperatura a la que la máquina hace mediciones correctas es de 20 ºC. Cuando se midan los errores de posicionamiento se tendrán en cuenta las diferentes temperaturas de las reglas ópticas y su coeficiente de dilatación.
Los errores de cuadratura se obtienen de mediciones diferenciales de un calibre, que se pondrá en dos posiciones para cada uno de los 3 planos coordinados en el volumen de medición. El calibre se medirá haciendo una diagonal del plano y luego haciendo una diagonal opuesta en el mismo plano.
Verificación de la fórmula de la incertidumbre de medición
Una vez acabada la fase de corrección de las cuadraturas y activada la última parte del algoritmo de compensación, se repiten las mediciones de las diagonales volumétricas en los calibres de referencia. A través de estas operaciones se verifican las prestaciones de la máquina de medición respecto a la fórmula de incertidumbre de medición prevista.
Verificación periódica de las prestaciones metrológicas del sistema
Dea recomienda que las máquinas de medición se verifiquen y se reparen anualmente. Dadas las pocas necesidades mecánicas de las máquinas de medición, la intervención se resuelve en la mayoría de los casos con una verificación normal de las prestaciones, a no ser que haya variaciones estructurales o funcionales ocurridas durante el uso de la máquina a causa de:
- Hundimientos de la estructura mecánica (improbables a no ser que se produzcan colisiones accidentales)
- Uso indebido de la máquina
- Olvido de las operaciones de mantenimiento preventivo
- Hundimiento del pavimento
- Efectos de vibraciones provocadas por el ambiente (máquinas en funcionamiento, el paso de carriles transportadores, etc.). La máquina no está bien aislada.
- Uso de los rodillos de desplazamiento cuando están presentes
- Deterioro de las prestaciones de los sensores o de las reglas ópticas.
- La calibración periódica consiste en una serie de operaciones de mantenimiento y de verificaciones funcionales y metrológicas:
- Control del estado de los órganos mecánicos y estructurales
- Verificación general de las condiciones de funcionamiento de la máquina
- Limpieza de las guías de desplazamiento
- Limpieza de las reglas ópticas
- Tensión de las correas de transmisión
- Control y reparación
- Verificación de las prestaciones metrológicas (véase el párrafo “Verificación de la fórmula de incertidumbre de medición”)
Sólo en caso de una diferencia apreciable con relación a la última verificación se procede a la reparación de la máquina con los instrumentos necesarios
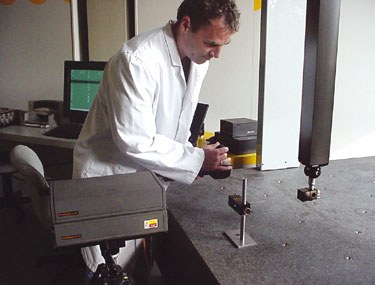