AutoForm cumple 10 años acompañando a los clientes en el camino hacia el éxito del conformado en caliente
Hace aproximadamente 10 años, AutoForm lanzó al mercado su solución para simular procesos de conformado en caliente de piezas metálicas. A continuación se contrastan la visión de un usuario que conoce la solución desde sus orígenes, Borja Fernández, PH Standardization and Advance Manufacturing Manager en Gestamp, con el responsable del producto en AutoForm, Dr. Alper Güner, Technical Product Manager de esta tecnología.
Conformado en caliente de chapa metálica. Algo que en sus inicios sonaba sofisticado, ambicioso y quizás, un tanto lejano, en pocos años ha pasado a ser una realidad y una respuesta a las exigencias relacionadas con la reducción de peso del vehículo, a la vez que se mantiene o aumenta la seguridad de sus ocupantes.
Cuando se piensa en esta tecnología aparecen en la mente varios retos a superar, como el uso de aceros de muy alta resistencia, los llamados UHSS (Ultra High Strenght Steels), caracterizados por su baja maleabilidad y sus valores elevados de retorno elástico, o el elevado desgaste de las herramientas que supone este proceso.
Por otro lado, se debe tener en cuenta que el conformado en caliente no solo incluye una deformación de la chapa, sino también una transformación de la microestructura del material, por lo que es imprescindible controlar y definir correctamente el acoplamiento de los procesos mecánico y térmico.
Allá en el año 2009 Borja Fernández, que en aquel entonces trabajaba en DIEDE, una empresa de ingeniería que se dedicaba a la simulación, diseño y puesta a punto de troqueles en caliente, empezó a interesarse por AutoForm, ya que consideraba que su interfaz era muy sencilla de usar comparando con otros softwares que había entonces en el mercado. Según explica él mismo: “para nosotros, además de los estudios de factibilidad de pieza, uno de los puntos más importantes era el poder comprobar la eficiencia de los sistemas de refrigeración que se diseñaban. En aquel momento no existía un software de estampación que tuviera ese módulo incluido”.
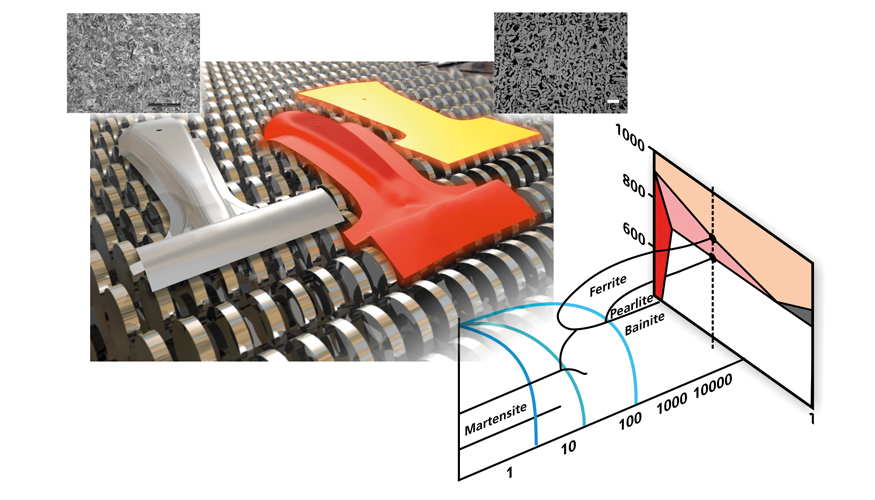
Entre el 2010 y el 2011 salió la primera versión de la solución de AutoForm para simular este tipo de procesos. Como indica el Dr. Alper Güner: “antes de que apareciera nuestra solución, la manera en la que se simulaba este tipo de procesos tenía muchas simplificaciones. Los ingenieros de proceso necesitaban tener en cuenta la variabilidad de las propiedades del material según la temperatura, o las nuevas condiciones de la chapa según su estado de microestructura. La primera versión contemplaba esos aspectos”. AutoForm modeló el proceso mecánico teniendo en cuenta las condiciones del material en una temperatura muy elevada, no solo durante el conformado, sino también durante la fase posterior de templado. Todo esto siguiendo la filosofía de AutoForm de desarrollar un interfaz intuitivo y fácil de usar, como Borja Fernández mencionaba.
Con el paso de los años el conformado en caliente se ha ido utilizando más y más. Las primeras piezas fabricadas mediante este proceso se incluyeron en el año 1984 en el modelo SAAB 9000. Hoy en día, más del 40% de las piezas de chasis se fabrican mediante conformado en caliente.
En estos años han aparecido nuevas tecnologías, se ha buscado la reducción de tiempos de entrega de pieza acabada, optimizando al máximo el comportamiento del troquel. Uno de los aspectos imprescindibles que mencionaba Borja anteriormente era la validación del circuito de refrigeración de la herramienta. En las versiones actuales de AutoForm, nos comenta el Dr. Alper que ya es posible definir el circuito y validarlo: “algo muy importante para las troquelerías era analizar la eficiencia del sistema de refrigeración y el impacto sobre las propiedades del producto final. Por eso, introdujimos la conducción de calor 3D en nuestras herramientas, considerando los canales de refrigeración. Por otro lado, hemos visto que el uso de ‘patchwork blanks’ cada vez es más común por lo que ahora se pueden definir formatos individuales y unidos a la vez por puntos de soldadura”.
Borja considera que “la solución de AutoForm se ha tecnificado mucho más, aportando soluciones para el ámbito de la comprobación del sistema de refrigeración hasta la predicción de la microestructura de las piezas estampadas. Por otro lado, se ha desarrollado un módulo de predicción de las ventanas de proceso (AutoForm-Sigma) mediante el cual se puede validar de forma más completa la robustez del modelo simulado”. Además, destaca que “las ventajas principales que le aporta su uso es, por un lado, el poder tener un software para todo el proceso donde antes se usaban varios. Se puede simular la estampación, comprobar la refrigeración, sacar el formato pre-desarrollado y su puesta en banda y conocer cuál será la composición metalográfica de la pieza. Por otro lado, recalca que AutoForm posee profesionales muy cualificados para dar el soporte técnico del programa que facilita en gran manera su buen uso”.
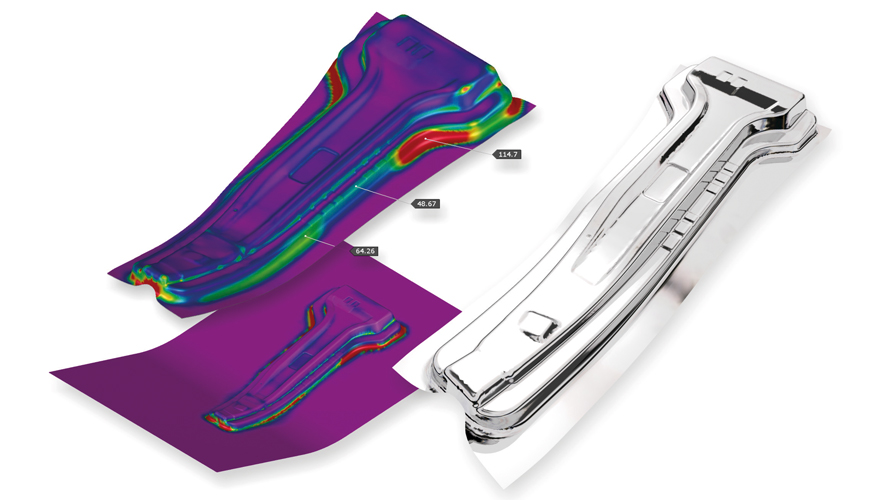
Un concepto que últimamente está a la orden del día es el de la Industria 4.0, también llamada industria inteligente o transformación digital, la cual busca transformar un proceso de negocio en una organización inteligente para conseguir mejores resultados. Desde hace años que AutoForm trabaja en esta dirección, digitalizando la cadena completa del conformado de pieza metálica. Recientemente, ha lanzado al mercado su último producto, AutoForm-TryoutAssistant, para apoyar a los equipos de puesta a punto y producción y conectar bidireccionalmente los departamentos de ingeniería y taller. El Dr. Alper concluye, “AutoForm quiere proporcionar una herramienta eficiente para los diseñadores para optimizar al máximo sus procesos. Esto incluye el flujo completo desde la fase de planificación y ofertas hasta puesta a punto y producción. En términos de conformado en caliente, buscamos una solución completa a todos los nuevos desarrollos tecnológicos y nuevos materiales que aparezcan en el sector”.
Definitivamente el conformado en caliente es una tecnología que ha llegado para quedarse, y como toda tecnología vanguardista, necesita ir acompañada de un buen software de simulación para optimizar el proceso al máximo.
Como se ve reflejado en este artículo, AutoForm sigue trabajando para responder a nuevas necesidades relacionadas con procesos, como el conformado en caliente de aluminio, y materiales, como aceros de 2.000 MPa. La empresa está en línea con los últimos avances del conformado en caliente y colabora con sus clientes para darles la mejor solución en el menor tiempo posible.