Secado de productos químicos para la industria farmacéutica
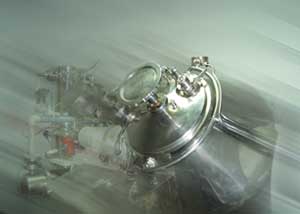
Rolabo ha confiado en Ingeniería Itekna para la automatización de un secadero bicónico en vacío que la empresa posee en sus instalaciones y que está destinado al secado “multipurpose” de diversos productos fabricados por el cliente.
Tras la fabricación de los productos químicos en la zona de reacción y una posterior centrifugación, el lote pasa a este secador bicónico donde se le elimina totalmente la humedad. El sistema de secado/pulverización en vacío tiene la capacidad de extraer completamente el agua o cualquier otro disolvente de los polvos húmedos provenientes de procesos de separación líquido/sólido (filtración o centrifugación): ya sean productos intermedios farmacéuticos o de química fina, productos delicados, más o menos finos, degradables, fotosensibles o también estériles, inyectables, principios activos o químicamente reactivos.
El cuerpo central de estos secaderos está formado por una cámara bicónica de secado, que gira a velocidad variable, en cuyo interior trabajan uno o dos grupos de cuchillas que, girando también a velocidad variable, rompen los bloques húmedos para facilitar y acelerar el proceso de secado, así como para favorecer la homogeneidad del producto.
Zona de alto riesgo
La segunda parte importante de la instalación son las bombas responsables de proporcionar depresión en el secadero y que se encuentran situadas en el exterior del edificio, con el fin de cumplir normativas GMP. Trabajando con estas bombas se consigue disminuir el punto de evaporación del disolvente base del producto, disminuyendo el tiempo de secado y el coste energético.
El sistema está controlado por una instalación automatizada compuesta de cuatro armarios; tres de todos ellos están situados fuera de la zona con riesgo de atmósferas explosivas, con el fin de abaratar costes y reducir tiempo de ejecución (los materiales utilizados en zonas de riesgo tienen plazos de entrega largos y costes muy elevados frente al material eléctrico de uso habitual).
El armario de visualización de variables de proceso es el único situado en Zona 1, por necesidades de proceso. Está fabricado en acero inoxidable y dispone de cuatro visualizadores de las variables del sistema (temperaturas de proceso y presión en el interior del secadero), tres lámparas que indican el estado de funcionamiento y una seta de emergencia. Estas señales hay que tratarlas de forma especial utilizando elementos de seguridad intrínseca o barreras de aislamiento según la norma EN 50020.
Ya que el armario se encuentra situado en zona ATEX, todas las señales de este armario están aisladas galvánicamente a través de módulos especiales ó barreras. Respecto a los visualizadores, tienen la característica de que son específicos de seguridad intrínseca.
El cableado de los motores situados en zona ATEX también requiere de un tratamiento especial y deben de ser cables armados con recubrimiento metálico que impiden la propagación del fuego y son capaces de aislar el cortocircuito. Estos cables parten del armario principal que hay fuera de la sala.
Automatización del sistema
Incluyendo el relé de estado sólido G3PB, se evita un prematuro desgaste del elemento de potencia mejorando la conmutación y evitando los picos de tensión innecesarios que conjuntamente con la implementación del control PID hacen un sistema de control excelente.
El último armario de conexiones, es el que se encuentra más alejado de la instalación y corresponde al conexionado de las bombas encargadas de crear el vacío en el interior de la cuba.
De esta manera, la instalación queda perfectamente automatizada y supervisada con elementos de gran calidad como son los productos Omron.