Cuando la automatización encabeza la gestión de sólidos en la industria
24 de noviembre de 2009
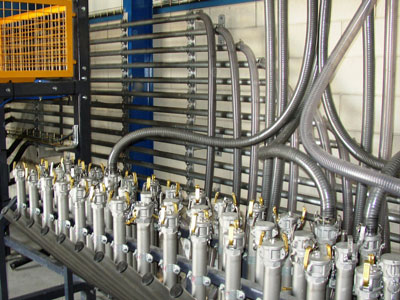
Antiguamente, en los procesos industriales donde se gestionaban productos sólidos (polvos o granulados), todo el movimiento de material y su manipulación se realizaba de manera manual. La alimentación a las máquinas, ensacado de producto, formulación y pesaje de diferentes componentes, así como el transporte a largas distancias desde el punto de recepción hasta el de proceso, se efectuaba a mano (mediante sacos, cajas o bidones) o con la ayuda de carretillas. Diversos factores inciden en que esta forma de trabajar ya no sea posible: las fuertes exigencias del mercado, la búsqueda de un mayor rendimiento de los recursos disponibles, la necesidad de aumentar la seguridad de las personas y minimizar la emisión de residuos. Actualmente, se pretende optimizar los procesos productivos automatizando maquinaria y dejando de lado antiguos procedimientos industriales. Cada instalación precisa de un sistema optimizado propio. Lo mismo sucede con el tipo de producto a gestionar. Para determinar el mejor sistema de manipulación se deberían realizar análisis de los diagramas de flujo de los materiales y de las operaciones necesarias hasta llegar al producto final. No todos los métodos son válidos para cualquier operación o tipo de producto, por lo que se deberían tener en cuenta múltiples variables así como la realización de un análisis técnico-económico de todo el proceso.
El nuevo sistema mejorará el proceso industrial, aunque no aumentará el valor del producto
Con anterioridad a la instalación de un equipo que manipule sólidos a granel, se debe prever que dicha implantación va a tener un coste sin aumentar el valor del producto. Básicamente, el nuevo sistema proporcionará una mejora en los demás procesos industriales. A fin de realizar una correcta elección, se deberían tener en cuenta los siguientes factores. En primer lugar, los traslados deben ser lo más directos y cortos posibles. En segundo lugar, y siempre que sea factible, el manejo mecanizado debe sustituir al trabajo manual.
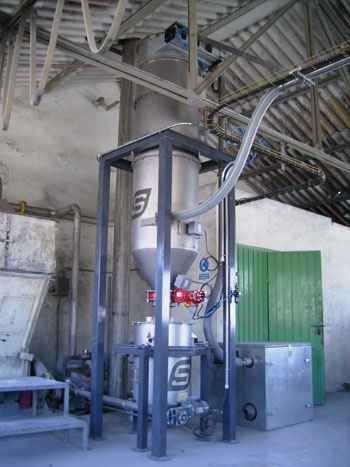
Normalmente, la selección de un equipo mecanizado para instalaciones industriales se basa en las posibilidades que ofrece el equipo para: reducir costos de manejo; abreviar ciclos de trabajo; acelerar embarques y entregas; mejorar la utilización del espacio; reducir los daños y desperdicios en el producto; aumentar la seguridad en el trabajo; ahorro de horas-hombre necesarias para trasladar materias; rendimiento de la inversión; sistemas de seguridad y condiciones medioambientales, por ejemplo.
Finalmente, el coste óptimo para una instalación no implica necesariamente un gasto mínimo. Se valorarán otros factores como los costes de mantenimiento, las piezas de repuesto, la vida de servicio prevista, la depreciación, el ahorro en mano de obra y el consumo energético.
Tecnología que evite el tráfico de producto por el recinto y reduzca accidentes laborales
El hecho de que el proveedor suministre el material a granel supone un ahorro económico que, una vez realizados los estudios pertinentes, influirá en si conviene o no, invertir capital en un sistema mecanizado de manipulación. Para grandes consumos, se ha generalizado el uso de silos de almacenamiento desde los que se suministra el material directamente al punto de venta, con lo que se evita la circulación del producto por el interior del recinto. Cuando los consumos son de menor tamaño, según el espacio disponible, se utiliza de manera habitual el Big-Bag con el que también se puede estudiar un sistema centralizado de transporte. Siempre que se suprima, en gran parte, la circulación de material dentro de las instalaciones y que el personal no realice sobreesfuerzos en manipular cargas, se evitan considerablemente el número de accidentes laborales y de enfermedades directamente relacionadas con la actividad desarrollada. Además, se puede reestructurar al personal disponible ubicando a los operarios que anteriormente manipulaban material, en otros departamentos donde se precise mano de obra.
Desde el origen hasta el o los puntos de consumo del producto, un sistema centralizado de traslado evitará material suelto en el interior de las instalaciones. También minimizará el riesgo de inhalar polvo nocivo para la salud de las personas, de ignición y explosiones debidas a la existencia de polvo conductor o de origen orgánico en suspensión. En muchos procesos industriales conviene pesar distintos productos, que se mezclan posteriormente. Hasta hace poco, estos procesos se realizaban de manera manual: un operario pesaba los productos manualmente mediante una báscula y posteriormente los introducía en el punto de consumo. Este trabajo era lento, inexacto, y obligaba a suministrar a pié de máquina el producto. Con su dosificación automatizada desde un silo de almacenamiento, una estación de vaciado de big-bag o un punto de recepción centralizado de sacos, se solucionan muchos de los inconvenientes ya descritos.
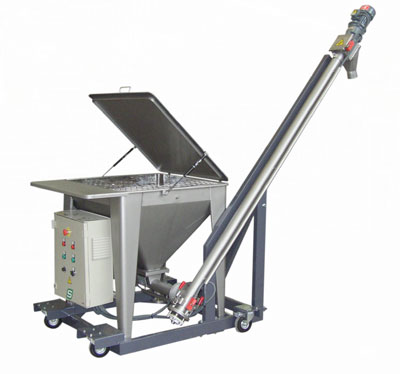
Transportadores de banda, para el paso de materiales a temperaturas extremas
Por material a granel se define cualquier sustancia suelta en forma de polvo, granza o partículas pequeñas como por ejemplo trigo, arena, harina o carbón. Estos materiales se pueden transportar, elevar y dosificar empleando diferentes sistemas. Entre ellos, los transportadores de banda. Se trata de equipos formados por bandas o correas sinfín, sostenidas y movidas de modo adecuado y dispuestas para transportar sobre ellas a las partículas sólidas. Las bandas se fabrican en lona, caucho o flejes de acero. Estas últimas son idóneas para el paso de materiales a través de hornos a temperaturas extremas. Los transportadores se adaptan a una gran variedad y cantidad de materiales, exigen poca energía y trasladan cuerpos sólidos de todos los tamaños a grandes distancias. Los dispositivos de banda se pueden alimentar mediante cualquiera de los dispositivos mecánicos auxiliares que existen en el mercado. Entre sus cualidades destacan las siguientes: se puede transportar a largas distancias gran variedad de productos, desde productos pulverulentos de finas partículas hasta materiales sólidos de varios centímetros de diámetro; existen equipos estándares en el mercado con longitudes que oscilan desde pocos centímetros a varias decenas de metros, incluso kilómetros en algunas explotaciones mineras. Como inconvenientes, los posibles problemas de suciedad y contaminación en el entorno de la cinta para productos con partículas muy finas. En este caso, aunque se puedan carenar para minimizar sus efectos, tanto en el punto de alimentación como en el de descarga se puede producir polvo en el ambiente. Además, este sistema opera en línea recta. Si queremos transportar el material a distancias considerables y debemos salvar algún obstáculo, no tememos más remedio que encadenar dos o más equipos. Finalmente, la descarga se debe efectuar a la altura de la polea de cabeza. La descarga en un punto intermedio, aunque existen sistemas más o menos ingeniosos en el mercado, no está exenta de complicaciones y automatismos complejos.
Elevadores de cangilones para el manejo vertical de materiales
Estos elevadores se utilizan para el traslado de materiales a granel, secos o húmedos, básicamente en vertical mediante unas cazoletas en las que se introducen los productos. Los transportadores-elevadores de cangilones se clasifican según el tipo de descarga o filosofía de funcionamiento. Por ejemplo, los de descarga centrífuga son los más habituales. Por su parte posterior, los cangilones se remachan a un eslabón de la cadena o a la banda. Operan de forma similar al transportador de banda, aunque se colocan en posición vertical y circulan a una velocidad de entre 1,2 y 1,4 metros por segundo. El funcionamiento de los elevadores de descarga por gravedad o continua se asemeja al de descarga centrífuga aunque la banda circula a baja velocidad, aproximadamente entre 0,5 y 1 metros por segundo y se aprovecha el propio peso del material para su descarga. Por último, el elevador-transportador de cangilones tipo ‘Z’ descarga por gravedad o de forma continua, pero con la particularidad que además de elevar el material traslada el producto de manera horizontal.
Husillos transportadores con una gama de caudales prácticamente ilimitada
Los transportadores de tornillo o helicoidales consisten en un eje sobre el que se sujeta una espiral, cuyo movimiento rotatorio dentro del conducto de transporte provoca el avance del material a lo largo del mismo. Principalmente, son equipos compactos, extremadamente versátiles ya que se emplean para mezclar, transportar, elevar o dosificar material, según su configuración. En cuanto a su coste económico, son sistemas baratos que no precisan demasiado mantenimiento. Respecto a su funcionamiento, los materiales se mezclan en cierta medida al pasar por el transportador y tienen tendencia a desmenuzarse. Por ello, se debe evaluar si esta característica puede representar una ventaja o bien un inconveniente para el material que se maneja.
Probablemente, y como ventaja diferencial, son quizás los equipos con los que se consigue mayor control del caudal dosificado que, en función de las múltiples configuraciones de husillo junto con las diferentes revoluciones a las que se puede hacer funcionar, se logra una gama de caudales prácticamente ilimitada. Las prestaciones varían desde los pocos gramos/hora hasta las toneladas/hora, en función de las unidades.
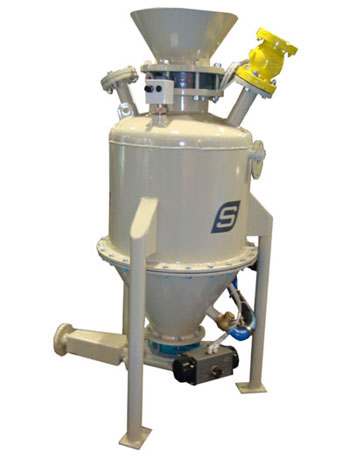
Transporte neumático: grandes distancias por medio de un flujo de gas a presión
De manera habitual, los sistemas de transporte neumático se emplean en la industria para transportar materiales secos a granel ya que son muy versátiles, económicos y adaptables a muchos procesos. Su objetivo principal es el transporte de materiales sólidos a grandes distancias desde un punto a otro por medio de un flujo de gas a presión, ya sea positivo o negativo, a través de un conducto. El rango de productos a trasladar es muy amplio: desde materiales pulverulentos micronizados a partículas de hasta 20 mm de diámetro con tuberías de hasta 500 mm de diámetro. El desplazamiento se puede efectuar en forma horizontal o vertical desde unos pocos metros de distancia hasta varios centenares de metros.
Existen algunos inconvenientes o desventajas para el uso de este tipo de transporte, y es que no todos los productos se pueden conducir neumáticamente a través de tuberías. Por ello, se suele destinar únicamente a productos secos, que no se apelmacen y que fluyan de manera correcta por gravedad. Cuando los materiales son excesivamente frágiles se pueden deteriorar durante el transporte, y en el caso de elementos muy abrasivos, estos pueden presentar un desgaste prematuro en su instalación. Este tipo de transporte requiere un consumo energético importante para grandes caudales de transporte.
El transporte neumático puede ser de dos tipos, según la proporción de gas/aire en relación al producto a manejar y a la velocidad del mismo en el interior del conducto. Por ejemplo, el transporte neumático en fase diluida y bajo presión es el que más se emplea en la industria, debido a su mayor capacidad de transporte y distancias a recorrer. El material se desplaza en suspensión dentro del conducto y las partículas se distribuyen, de forma uniforme, en toda la sección transversal de la tubería (el flujo es muy homogéneo). La concentración de sólidos es relativamente baja y la velocidad de transporte relativamente alta. Uno de los puntos débiles de este transporte reside en que las partículas de diferente masa se pueden separar durante el trayecto, con lo que es posible que el material se deposite de manera estratificada. Por el contrario, este sistema es uno de los más limpios de todos. El interior de la tubería suele quedar siempre vacía, con lo que resulta viable el paso por ella de diferentes productos con un riesgo mínimo de contaminaciones cruzadas. Las velocidades que pueden alcanzar oscilan entre 20 y 30 metros por segundo, lo que puede ser un inconveniente para partículas transportadas muy frágiles o con un punto de fusión muy bajo. Se subdivide en dos tipologías: transporte por impulsión y por depresión.
Por su parte, las unidades de transporte neumático en fase densa se emplean sobre todo para grandes caudales, productos abrasivos o que, por su fragilidad, se deban manipular a baja velocidad. La velocidad de transporte oscila entre 2 y 15 metros/segundo. Un sistema de estas características evita el desgaste prematuro de los elementos de la instalación como pueden ser la tubería, codos, etcétera. El equipo funciona con aire comprimido entre 1 y 5 bar y los caudales de transporte, dependiendo de la configuración de cada equipo, pueden superar las 400 t/h y los 500 metros de longitud. Respecto al sistema de fase diluida, esta tecnología posee una ventaja evidente: las partículas de diferente masa no se separan durante el transporte. En relación a los demás sistemas descritos anteriormente, requiere mayor consumo energético debido a la cantidad de aire comprimido que utiliza durante el desplazamiento.
Transportadores de arrastre con bajo consumo energético
Estos transportadores son ideales para el transporte de productos sólidos a larga distancia. El sistema funciona a base de un circuito cerrado de tuberías por cuyo interior circula longitudinalmente un cable o una cadena con unos discos inyectados sobre la misma. Estos discos son los responsables de recoger el producto de uno o más puntos de origen y descargarlo en los puntos de destino que se requieran. En resumen, sus principales cualidades son: bajo consumo energético ya que con una potencia máxima de unos 4 kW se pueden transportar caudales del orden de 20 t/h; distancias de hasta 250 metros con un solo conjunto tractor, dependiendo de la configuración de cada equipo; simplicidad mecánica y fácil mantenimiento de todos los elementos y aprovechamiento óptimo del espacio disponible ya que la tubería puede seguir el contorno del recinto, esquivando obstáculos. Otras facilidades que aporta son: no necesita aire para el transporte por lo que no se requiere ningún sistema de filtración adicional, al contrario que en los sistemas de transporte neumático, el producto transcurre empaquetado, por lo que no se producen separaciones entre las partículas de diferente masa y la velocidad de transporte es relativamente baja (entre 20 y 30 metros por minuto), por lo que se pueden trasladar materiales que no soporten bien el rozamiento con las tuberías o tengan un punto de fusión relativamente bajo. Por el contrario, una limitación evidente, respecto a un sistema de transporte neumático, es que suele quedar residuo dentro de la tubería. Ello obliga a utilizar una línea para cada producto o familia.
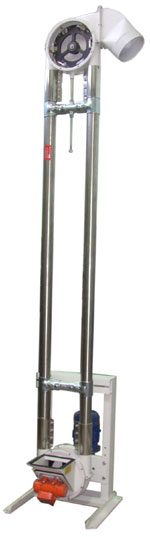
Aerotransportadores que arrastran a alta velocidad
Los aerotransportadores mecánicos por arrastre a alta velocidad son idóneos para elevar productos pulverulentos complicados, como el negro de humo o el bióxido de titanio. De manera semejante a los transportadores de arrastre, este sistema funciona con un cable de acero que circula longitudinalmente por el interior de la tubería, con unos discos de material plástico muy ajustados a la misma. Al trabajar a alta velocidad, se genera una succión en el punto de origen que provoca que el producto circule “empaquetado” entre dos discos, con cierta cantidad de aire que lo mantiene suelto y volátil. En consecuencia, no se pega a las paredes de la tubería. Los caudales de transporte oscilan entre los 15.000 litros/hora hasta los 35.000, en función de la configuración de cada equipo. En general, algunas de sus principales ventajas son: muy bajo consumo energético en relación al producto manipulado, la no separación de las partículas de diferente masa durante el proceso y el hecho de que no se precisan filtros de mangas ni aire comprimido.