Flujo más rápido y ahorro energético
15 de septiembre de 2011
Los plásticos con propiedades de flujo mejorado pueden batir a sus homólogos tradicionales cuando es necesario superar relaciones entre la longitud del flujo y el espesor de la pared. Una de las aplicaciones típicas es la producción de enchufes para la industria de la electrónica [1,2]. Las carcasas de los enchufes son cada día más complejas debido al aumento de la miniaturización de los enchufes, que integran de manera simultánea cada vez más elementos funcionales. Es característico de estas aplicaciones que las secciones con grandes espesores de pared, así como las secciones con espesores de pared muy finas se reúnan en la misma pieza.
Cuando no se podían producir estas piezas con buena calidad y con las configuraciones adecuadas, los especialistas en el moldeo por inyección solo tenían dos opciones: aumentar o bien la temperatura de fusión, o la temperatura del moldeo, o ambas, en el peor de los casos. En consecuencia, se produce un aumento del tiempo del ciclo y la producción se encarece. Aquí es donde la ventaja que aportan los materiales de flujo mejorado se hace inmediatamente patente.
Así mismo, esto plantea la cuestión de cuál es la ventaja de un polímero de flujo más libre, si ya se puede producir fácilmente una pieza con la configuración de producción existente: es decir: ¿cuáles son las ventajas en detalle de la producción a temperaturas de fusión más bajas? Para cuantificar el ahorro, Basf SE instaló nuevas herramientas en una máquina de moldeo por inyección, para recoger datos sobre todas las corrientes de materiales y energías entrantes y salientes. Esto permite obtener un balance energético total del proceso de moldeo por inyección, así como identificar la naturaleza y la magnitud del ahorro energético.
Las condiciones experimentales están basadas en las circunstancias que ocurren en la industria eléctrica. La pieza es una sencilla placa (molde de 2 cavidades) con un volumen de inyección de unos 64 cm3 (Fig.1). El material que se utiliza es un PBT con un contenido del 30% de fibra de vidrio (tipo: Ultradur B4300G6 del fabricante: Basf). También está disponible en una variante de alta velocidad, que es una versión con flujo especialmente mejorado, pero con las mismas propiedades. Una máquina de moldeo por inyección completamente eléctrica (tipo: IntElect100 del fabricante: Sumitomo (SHI) Demag Plastics Machinery GmbH, Wiehe, Alemania) funciona con un tornillo de 30mm de diámetro, dependiendo de la pieza moldeada.
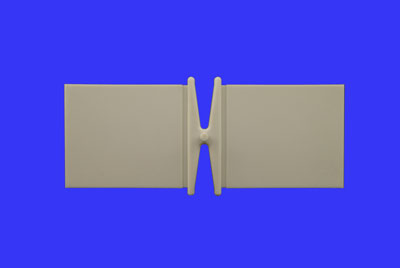
Consumo energético en un proceso cíclico
Para poder recibir información fiable sobre el consumo energético es necesario preparar un balance de energía y material para el proceso completo y medir todas las corrientes de energía, tanto entrantes como salientes. El ámbito del balance incluye la unidad y el molde de plastificación. Todos los parámetros que se introducen en el sistema están marcados con flechas rojas, mientras que las corrientes salientes de materiales y energías están identificadas en azul (Fig.2).
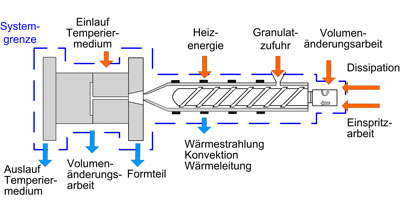
A pesar de que el moldeo por inyección es cíclico, se puede considerar como un proceso de estado casi estable y se obtiene un balance de acuerdo con la primera ley de la termodinámica [3]. La fórmula de asociación (la ecuación 1, véase el cuadro) ilustra los parámetros pertinentes para las corrientes de materiales y de energía entrantes y salientes, que se pueden normalmente registrar fácilmente mediante sensores de temperatura, o con los sensores con los que viene ya equipada la máquina.
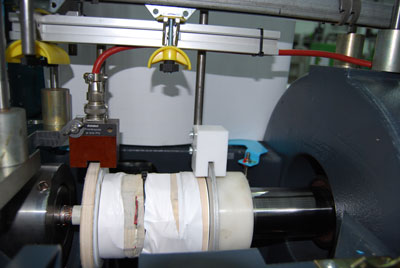

Primärspule = Bobina primaria
Sekundärspule = Bobina secundaria
Führungsschiene = Raíl guía
Mitnehmer = Portadora
La energía calorífica se determina mediante la electricidad alimentada al calentador, en base a la hipótesis de que toda la energía se convierte en calor. Las pérdidas de calor debidas a la radiación y a la convección son muy difíciles de medir y es necesario realizar un cálculo estimativo, de acuerdo con los principios de transferencia de calor. Por ejemplo: la transferencia de calor causada por la convección puede estimarse a partir de las temperaturas de la superficie y asumiendo que se utiliza un cilindro con convección libre [4].

Drehmoment = Par de apriete
Frequenzwandler n = 270 = Convertidor de frecuencia n = 270
DMS n = 270 = Galga extensiométrica n = 270
Zeit = Tiempo
Mayor ahorro gracias a la reducción del tiempo de ciclo
El objetivo de los ensayos es trazar una comparación entre un PBT estándar (Ultradur B4300G6) y la alternativa de flujo rápido. Para lograrlo, los dos grados se procesan con la misma viscosidad. El hecho de que el material de alta velocidad alcance la viscosidad de los grados estándar a una temperatura de fusión más baja debido a que su flujo es mejor, se refleja en las temperaturas de procesamiento (de 255 a 285 °C).
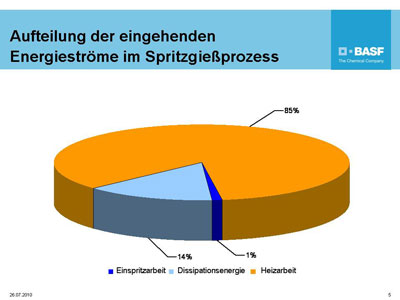
Einspritzarbeit = Trabajo de inyección
Dissipationsenergie = Energía de disipación
Heizarbeit = Trabajo de calentamiento
Se llevaron a cabo ocho ensayos por cada grado (Tabla 1). La proporción de la energía total suministrada al plástico que se produce a causa de la energía calorífica es muy elevada, alcanzando el 85% (Fig.5). La energía de disipación introducida por las labores de cortadura e inyección desempeña un papel más secundario. Las distintas configuraciones de la máquina ejercen una influencia prácticamente inexistente en la distribución. Estos resultados son aplicables a un tornillo con un diámetro de 30mm, mientras que a los diámetros de tornillo más grandes les corresponderá una distribución de la energía diferente.
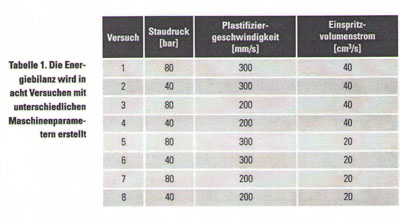
Versuch = Ensayo
Staudruck = Presión posterior
Plastifiziergeschwindigkeit = Velocidad de plastificación
Einspritzgeschwindigkeit = Velocidad de inyección
Los resultados de la comparación de materiales demuestran que simplemente con la utilización de un grado de flujo más libre se puede obtener un ahorro energético de hasta el 13% (Tabla 2). Para la metodología experimental, el tiempo de ciclo se mantuvo constante a 38 s para ambos materiales. La comparación entre los puntos de ensayo demostró a su vez que el ahorro energético es mayor a velocidades de inyección altas. Esto es posible gracias a que el flujo mejor de un material se hace más patente aquí. No obstante, las diferencias entre los ensayos individuales son bastante pequeñas, ya que la mayor parte de la energía de entrada se suministra a través del calentador. Un flujo mejor se hace más patente en el trabajo de inyección, aunque solo representa una pequeña proporción del consumo energético total.
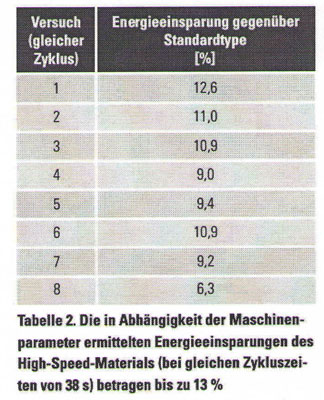
Versuch = ensayo
Energieeinsparung gegenüber Standard-Type = Ahorro energético comparado con el grado estándar
Si ahora además tenemos en cuenta que la utilización de un material de flujo mejorado puede acortar el tiempo de ciclo, ya que la temperatura de fusión es menor, el resultado es un ahorro energético adicional. En base a la temperatura de 255 °C que se utiliza y con la misma temperatura de desmoldeo de los grados estándar y de alta velocidad, se puede calcular una reducción del tiempo de ciclo de 6s para la pieza a través de la formula del tiempo de enfriamiento. Como el tiempo de calentamiento también se reduce para los tiempos de ciclo más cortos, la gran proporción de energía calorífica se refleja de manera especialmente positiva en el balance general (Tabla 3). En el mejor de los casos, es posible alcanzar un ahorro energético total de casi un 30%.
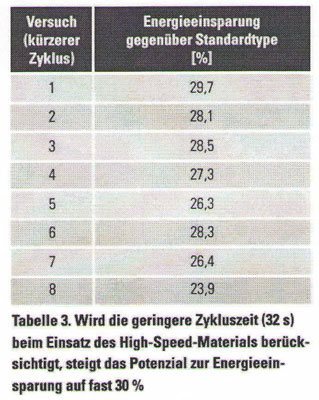
Versuch = Ensayo
Energieeinsparung gegenüber Standard-Type, kürzerer Zyklus = Ahorro energético comparado con el grado estándar, ciclo más corto
Resumen
La utilización de polímeros de flujo más libre, además de lograr un rellenado de molde y una reproducción de la superficie mayores, permite alcanzar un ahorro energético importante. Uno de los prerrequisitos de este logro es que debería también ser posible rellenar la pieza con un grado estándar. Con diámetros de tornillo relativamente pequeños, como los que se utilizan y son característicos de los enchufes y de las piezas pequeñas similares de la industria eléctrica, existen grandes potenciales de ahorro de hasta un 30%, como resultado de la contribución de la energía calorífica elevada. Estas piezas suelen fabricarse con PBT, como por ejemplo Ultradur (High Speed) de Basf. Cuanto mayor sea el diámetro del tornillo, menor será la influencia de la energía calorífica y menor será el potencial de ahorro, ya que las proporciones de energía de disipación aumentan.
Para piezas grandes, como los componentes tradicionales del compartimento del motor (fundas del motor, manguitos de entrada de aire) que no están fabricados con PBT sino con PA (poliamida, preferiblemente PA6), los grados de flujo mejorado aportan otras ventajas. Como la presión de inyección y la fuerza de bloqueo son inferiores, el procesador puede realizar la fabricación con máquinas más pequeñas. Esto también aporta un valor añadido significativo, ya que los costes operativos de una máquina de moldeo por inyección crecen de manera desproporcionada con su tamaño. Estos argumentos han convencido a Basf para ampliar su gama de plásticos de ingeniería de flujo mejorado [7,8]. Tras Ultradur High Speed (PBT) y Ultramid A High Speed (PA66), Basf acaba de presentar ahora su primer compuesto de PA6 de flujo mejorado, Ultramid B3WG6 High Speed, en la feria K2010.
Reconocimientos
Los estudios se llevaron a cabo con la colaboración de la Universidad de Ciencias Aplicadas Karlsruhe. Agradecemos la labor de Niko Weber y del catedrático Frank Pöhler por llevar a cabo y supervisar el trabajo.
- Stransky, R.; Bernnat, A.; Reinfrank, K.-M.; Völkel, M.; Zeiher, V.: Ever More Electricity and Plastic. Kunststoffe international 99 (2009) 6, págs 49–53, PE110133
- Rosenau, B.; Fernández-Rodiles, R.: Polyamides (PA). Kunststoffe international 98 (2008) 10, págs. 82–85, PE104380
- Baehr, H. D.; Kabelac, S.: Thermodynamik. 14. Auflage, Springer Dordrecht, Heidelberg, Londres, Nueva York 2009
- Baehr, H. D.; Stephan, K.: Wärme- und Stoffübertragung. 6. Auflage, Springer-Verlag, Berlin, Heidelberg 2008
- Fritzensmeier, T.: KEB-Antriebstechnik Karl E. Brinkmann GmbH, Schneeberg. Comunicación personal, 2009
- Weber, N.: Untersuchung der Möglichkeiten zur Energieeinsparung durch den Einsatz leichter fließender Kunststofftypen im Spritzgießprozess. Diploma Thesis, Karlsruhe University of Applied Science, 2010
- Bernnat, A.: Alles fließt. Press conference at BASF on K 2010, Frankenthal, 22.–23. junio 2010
- Eipper, A.; Stransky, R.: Small Particles – Big Effect. Kunststoffe international 98 (2008) 1, págs. 65–67, PE104165