Máxima precisión en componentes de plástico
Ya desde su fundación en el año 1961, la empresa Borscheid+Wenig GmbH se dedica al mecanizado de goma. Desde 1985, la empresa opera también en el sector del moldeo por inyección y produce para la industria. Su gama de productos abarca desde componentes para frigoríficos y lavadoras para la industria del electrodoméstico hasta el suministro de productos para el sector automovilístico. A día de hoy, la empresa Borscheid+Wenig GmbH tiene en uso 40 máquinas de moldeo por inyección del tipo Sumitomo Demag (representada en España por Mecman). “Hasta el año 2009 nuestra producción contaba exclusivamente con robots lineales. El aumento de los pedidos, de la variedad de componentes y de la complejidad de los procesos ha exigido el reequipamiento de nuestras instalaciones con robots industriales”, explica Carlo Wenig, gerente técnico de Borscheid+Wenig GmbH. Nuestra empresa cuenta hoy en día con nueve instalaciones con robots Kuka de brazo articulado. —Con SAR Elektronic GmbH, sita en Gunzenhausen y compañía colaboradora de Kuka, hemos encontrado un socio fiable que nos ha asesorado y asistido durante las fases del proyecto— continúa Carlo Wenig.
Ciclos más rápidos, menos piezas defectuosas
Las características tridimensionales y la gran variedad de variantes de los nuevos componentes de plástico para los vehículos todo terreno de Porsche y Volkswagen hacen que su producción sea mucho más exigente que la de sus predecesores. Estos retos fueron el criterio decisivo para que la gerencia tomara la decisión de emplear por primera vez en el año 2009 robots de brazo articulado en las máquinas de moldeo por inyección. —Hacerlo de forma manual habría sido imposible —cuenta Johannes Spatz, ingeniero en Borscheid+Wenig. El proceso en la primera instalación empieza con la colocación de dos casquillos en el molde de inyección y con la rápida retirada del artículo directamente de los eyectores. Con la pieza en la garra de descarga, el robot de consola Kuka KR 60 L30-4KS Speed se desplaza con máxima precisión hasta cada uno de los dispositivos periféricos fijos y completa, así, los artículos con hasta ocho pernos roscados. En el siguiente paso, se introduce una tuerca de presión que debe haber superado satisfactoriamente un control de calidad. A continuación, la pieza se coloca sobre una cinta transportadora y el proceso empieza de nuevo.
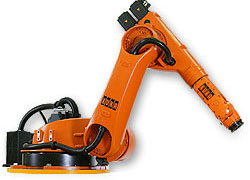
El innovador paquete de opciones de Kuka: la unidad de medios
Los robots lineales no bastaban para hacer frente al aumento del número de piezas a fabricar. —Sin la automatización, habríamos producido muchas menos piezas el año pasado —apunta Johannes Spatz. Los robots Kuka se emplean especialmente para fabricar los componentes elaborados a partir de dos materiales. —Los criterios que nos motivaron a realizar el reequipamiento fueron la reducción considerable de los tiempos en los que el molde está abierto, la extrema precisión de posicionamiento, la rigidez al cambiar de cavidad 1 a cavidad 2, así como el desmoldeo firme y fluido —describe Carlo Wenig—. En comparación con la técnica lineal, se producen menos fallos en las instalaciones, los tiempos de preparación son mínimos, no se dan intervalos de mantenimiento y el desgaste de las herramientas es menor. También el número de piezas defectuosas ha disminuido notablemente —continúa Carlo Wenig. La empresa Borscheid + Wenig apuesta no sólo por robots de consola de peso, alcance y velocidad optimizados, sino también por las opciones estandarizadas que ofrece Kuka, como la unidad de medios. Ésta está instalada sobre el eje A3, siguiendo sus movimientos, y se ocupa de realizar el intercambio de señales eléctricas y neumáticas en la garra. En comparación con un robot lineal, los modelos de consola pueden instalarse en naves más bajas y requieren una superficie de instalación menor.
El robot Kuka cambia de herramienta de forma autónoma
La gran variedad de piezas que se producen exige el empleo de garras diferentes. —Hacer frente a las nuevas exigencias era para un robot lineal, limitado por su sistema cartesiano, muy difícil —explica Christian Müller, jefe de aplicaciones de moldeo por inyección en Borscheid+Wenig GmbH—. Los costes de equipamiento eran enormes y los empleados tenían que ocuparse de cambiar la garra del robot lineal.
SAR, la compañía colaboradora de Kuka, se ocupa de instalar la completa periferia para el robot de brazo articulado, así como de poner las garras a disposición en una especie de estación donde esperan a ser recogidas y aplicadas en el proceso. El robot de seis ejes coloca en esta estación la garra que ya no necesita y, con ayuda de un código, busca otra de entre las seis disponibles. —Desde un principio, nuestros empleados mostraron gran iniciativa en trabajar en las nuevas máquinas y ya cuentan con los conocimientos necesarios para mantener e instalar las garras —cuenta orgulloso Johannes Spatz.
El robot de consola en máquinas pequeñas
Tras la exitosa automatización de la máquina de moldeo por inyección de 650 t de fuerza de cierre, Borscheid+Wenig GmbH decidió automatizar también una máquina pequeña de 150 t de fuerza de cierre y dos componentes (blando y duro) empleando un robot de seis ejes. El robot empleado fue un modelo de consola pequeño, el KR 6 KS. El proceso incluye la inserción precisa y oblicua de dos anillos metálicos en una posición de definición flexible.
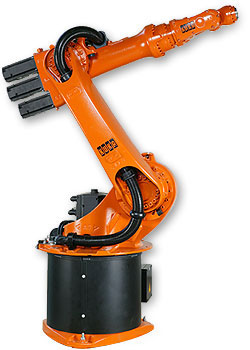
Los mejores empleados – los mejores robots
Las empresas dedicadas al moldeo por inyección cuentan con fuertes competidores a nivel mundial. Borscheid+Wenig GmbH va a apostar también en el futuro por robots Kuka: ya hay un nuevo proyecto en planificación. Se ha realizado el pedido de otros tres robots de consola a SAR GmbH, cuya puesta en servicio está prevista para principios del verano de 2011. —Nuestras piezas de plástico son complejas y tienen que producirse en grandes lotes y variantes. Por eso nos hemos decidido por robots Kuka. Sin la flexibilidad de los robots Kuka, la puesta en práctica no sería ni rentable ni cualitativa —nos dice Christian Müller.
Hasta finales del 2011 se prevé formar en las instalaciones a casi todo el personal especializado de Borscheid+Wenig. Carlo Wenig está convencido: Nuestro objetivo es tener los mejores empleados. Y esto es igualmente válido para nuestros robots. Nuestros colegas los robots trabajan, al igual que nosotros, en crear un valor añadido. Y las cifras, los datos y los hechos lo dicen todo.