La poliamida 6 permite mejorar el efecto barrera de los depósitos de combustible
Debido a su baja densidad, los plásticos son relativamente permeables a los gases y líquidos. Al emplear estos materiales poliméricos para la fabricación de depósitos de combustible se aceptó durante mucho tiempo, como contrapartida a la reducción de peso, la difusión de cantidades significativas de vapores de combustible a través de las paredes del tanque. Sin embargo, este proceso ―conocido como permeación― pasó a recibir una mayor atención por parte de los investigadores de materiales ante la tendencia general de reducción de emisiones nocivas. En particular, el objetivo de lograr un automóvil de cero emisiones y la consiguiente legislación actual sobre emisiones exigían desarrollar un plástico que, además de satisfacer las exigencias mecánicas y térmicas, ofreciese una función de barrera mejorada frente a los hidrocarburos.
California, pionera en cero emisiones
Sorprendentemente, los valores límite más radicales en cuanto a emisión de gases de escape y evaporación rigen actualmente en los Estados Unidos, concretamente en el estado de California. La autoridad competente en cuanto a control de emisiones, CARB (California Air Recourse Board) estableció ya en 2003 y 2004 valores límite extremadamente bajos para las emisiones, que llegan incluso hasta los vehículos con cero emisiones (ZEV, Zero Emission Vehicle).
La Oficina de Protección del Medioambiente de los Estados Unidos (EPA, Environmental Protection Agency) establece en su norma EPA 40 CFR un valor límite de permeación para depósitos de combustible para motocicletas fabricados con plástico (Fig. 1) de 1,5 gramos diarios por metro cuadrado de superficie interna (g/m²/d). Este límite se aplica también a los bidones de carburante y a los tanques de pequeños motores de explosión como los empleados en maquinaria de jardín, motosierras, maquinaria de construcción, grupos electrógenos, lanchas y otros vehículos acuáticos.
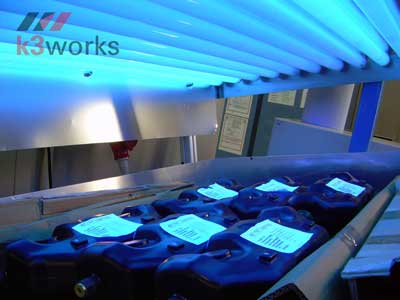
En Europa, los valores límite para los depósitos plásticos de combustible para motocicletas se encuentran aún en 20g/m²/d, según la Directiva 97/24/CE del Parlamento Europeo y la Comisión Europea. Sin embargo, es previsible que, en breve, la Comisión Económica para Europa (CEPE) de las Naciones Unidas reduzca significativamente dicho valor límite, orientándose muy de cerca por el establecido por la EPA.
Los materiales alternativos alcanzan sus límites
Los depósitos de muchos aparatos y vehículos accionados por motores de gasolina, entre ellos los de las motocicletas, se fabricaban hasta ahora en su mayoría con polietileno de alta densidad (HDPE). Sin embargo, el comportamiento de permeación de este material dista mucho de cumplir las estrictas normas de la EPA. Sin embargo, su efecto de barrera contra los hidrocarburos puede ser mejorado sustancialmente mediante la fluoración posterior de los depósitos moldeados por soplado. No obstante, esto hace necesario en el proceso de elaboración un paso adicional que, debido a la agresividad química del flúor y teniendo en cuenta la protección medioambiental, implica el uso de aparatos y técnicas de seguridad de alto coste.
Los tanques de HDPE tienen la desventaja de que en sus paredes se acumula gran cantidad de combustible, lo que dificulta el reciclaje de los depósitos.
Las mezclas poliméricas, como la combinación de HDPE y poliamida, tampoco cumplen todas las exigencias que se plantean al material, ya que, a pesar de suponer una mejor barrera contra los hidrocarburos que HDPE, resultan frágiles y, por consiguiente, más susceptibles a los impactos y los choques.
Desarrollo de materiales a la medida
Como desarrollador y fabricante de plásticos, Lanxess afronta los nuevos y estrictos límites de emisiones para los depósitos de combustible sin perder de vista las propiedades mecánicas en el proceso de optimización del material. Para ello, partiendo de la poliamida 6 se ha desarrollado un nuevo material para la elaboración de depósitos de combustible: Durethan TP 142-011 no reforzado y con resistencia al impacto modificada. Su efecto de barrera contra la gasolina está significativamente por debajo de los límites máximos de permeación establecidos en la correspondiente norma de ensayo de la EPA. Con el telón de fondo de las estrictas exigencias establecidas por la Sociedad Americana de Ingenieros de Automoción (American Society of Automotive Engineers) en su recomendación SAE J1241, por ejemplo en cuanto a la resistencia al impacto de los depósitos de gasolina de las motocicletas, para el desarrollo del material se prestó especial atención a la resistencia al impacto de las poliamidas. El material para los tanques debe presentar una resistencia al impacto tal que en los tanques envejecidos no aparezcan fugas tras ser sometidos a las pruebas prescritas de impacto con péndulo bajo diferentes ángulos -20 °C y 60 °C.
Durethan TP 142-011 representa una alternativa económicamente viable frente a los plásticos laminados, ya que el proceso de coextrusión y soplado para unir varias capas de diferentes plásticos es complejo y costoso. El bloqueo de la permeación en estos plásticos laminados se basa en su mayor parte en una capa polar de copolímero de etileno / alcohol vinílico (EVOH).
La poliamida 6 representa una ventaja frente al aluminio y la chapa de acero que también se usan para la construcción de tanques. La geometría de los tanques, a menudo muy compleja, requiere un amplio margen de maniobra en el diseño de la forma. Los elevados costos de troquelado y soldadura asociados, por ejemplo, al procesado de chapa de acero, no se requieren con este termoplástico. Además, las posibilidades de integración del plástico representan un potencial de ahorro adicional, ya que en el proceso de elaboración del tanque es posible integrar elementos de fijación, y las correspondientes piezas insertadas pueden moldearse con facilidad.
Compatible con la nueva generación de combustibles
Por otra parte, los tanques de aluminio presentan la desventaja de que reaccionan con gran sensibilidad al etanol contenido en los biocarburantes. Como el etanol es higroscópico, estos combustibles tienen un contenido en agua mayor, lo cual puede provocar procesos de corrosión en el tanque con la consiguiente formación de partículas que obstruyen los filtros y conductos, provocando una merma en el rendimiento del motor. Este efecto puede ser contrarrestado mediante el recubrimiento interno del tanque o con la utilización de aleaciones de aluminio, lo que, sin embargo, incrementa notablemente los costos de fabricación. En el caso de la poliamida 6, que no contiene plastificantes, es posible repostar ecológicamente sin problemas con las proporciones de etanol habituales en los biocarburantes actuales. En estudios a largo plazo, Lanxess ha demostrado que este material es igualmente apropiado para la fabricación de depósitos destinados a gasolina de tipo E85 (85% de etanol).
La poliamida también resulta interesante para la fabricación de tanques para embarcaciones. Los depósitos de combustible, hasta ahora fabricados en su mayor parte con materiales compuestos duroplásticos, eran frecuentemente, incompatibles con carburantes que contienen etanol. Dicha incompatibilidad conducía en algunos casos a una disolución de los componentes de la matriz del plástico y a su posterior sedimentación en las válvulas de admisión, con los consecuentes daños al motor.
Indeformable, pintable y reciclable
Con su perfil de propiedades, la poliamida 6 presenta ventajas ya durante su procesado. Los procesos de extrusión y moldeado por soplado requieren una rigidez elevada de la masa fundida a bajas velocidades de cizallamiento, ya que la preforma extruida no debe deformarse ni alargarse bajo su propio peso antes de ser soplada en la herramienta. En el caso de las variedades de Durethan moldeables por soplado, la elevada rigidez de la masa fundida deriva de las ramificaciones de cadena larga en la estructura del polímero, que permite moldear por soplado piezas huecas de gran tamaño. La conformación de carcasas para tanques permite así diseños muy variables desde el punto de vista de la geometría y de las dimensiones deseadas.
La baja velocidad de solidificación de la poliamida fundida da lugar a buenas cualidades superficiales y de soldadura por compresión que permiten un pintado directo. Los residuos resultantes del proceso de producción pueden ser reincorporados al proceso productivo sin grandes mermas en sus propiedades.
Servicio personalizado al cliente
Los polímeros de alta tecnología desarrollados por Lanxess para aplicaciones altamente exigentes están asociados a una amplia variedad de servicios. Bajo la denominación comercial HiAnt, la empresa presta apoyo con sus amplios conocimientos en todas las etapas de la ejecución de las piezas. Así, por ejemplo, nuestros diseñadores ayudan a proyectar correctamente la geometría de los sistemas de tanque mediante el uso de herramientas CAE a fin de que cumplan con las exigencias mecánico-dinámicas. Igualmente pueden ser simuladas pruebas de impacto, choque y caída de bola. La asistencia al cliente incluye también pruebas de las piezas, tales como ensayos de presión alternante o de permeación (Fig. 2).
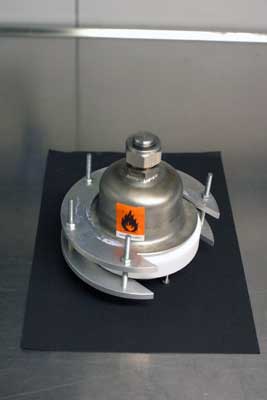
En el centro técnico de vibración de Lanxess (Fig. 3) existe la posibilidad de someter las piezas a las más diversas pruebas de vibración, que pueden combinarse con ensayos climáticos.
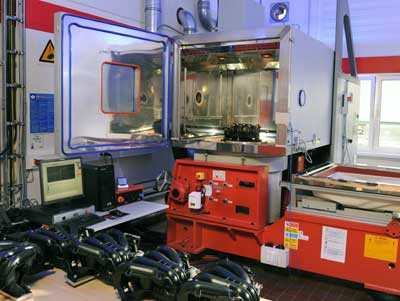
La fuerte tendencia al uso de biocombustibles es de especial importancia para Lanxess a la hora de apoyar a los fabricantes de tanques mediante el desarrollo de materiales y la realización de pruebas a largo plazo aceleradas. En estas pruebas, diferentes mezclas de poliamida 6 y 66 permanecieron sumergidas por periodos de hasta 5.000 horas a 60 °C en combustibles con etanol E10, E24, E85 y E100. Estos estudios demostraron que los plásticos analizados se mantienen estables ante estos combustibles. En este sentido hay que tener en cuenta un efecto de acondicionamiento reversible debido a la absorción de agua y etanol.