La evolución de la tecnología del RTM Light
17 de junio de 2010
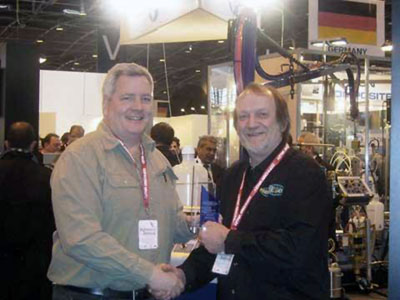
El proceso básico del LRTM, universalmente aceptado, utiliza un molde cerrado de composite, ligero de peso, en cuyo interior se colocan las fibras secas de refuerzo y que se cierra por vacío. A continuación se inyecta la resina catalizada, tipicamente fluyendo a baja presión, desde la periferia del molde hacia el punto central de vacío.
El diseño del molde LRTM
La base de cualquier operación con molde cerrado radica en el propio diseño del molde y desde sus comienzos el LRTM se ofreció como una alternativa económica a la entonces única y equivalente, los moldes RTM de alta presión. El LRTM siempre ha sido atractivo, debido a que solo necesita moldes relativamente ligeros, cerrados por vacío, por tener una excelente vida útil de producción y conseguir piezas de calidad. Su principal ventaja está en el hecho de que con solo la presión atmosférica se puede conseguir la fuerza para mantener el molde herméticamente cerrado durante todo el proceso y dar la energía suficiente a la resina para impregnar bien el paquete de fibras. La necesidad de unos cierres seguros para prevenir la pérdida de vacío y mantener la resina dentro de la cavidad del molde propició al principio muchos cambios en los materiales y diseño de las juntas.
En los comienzos hubo un punto de vista predominante que consideraba que cuanto más grandes fueran las pestañas mayor fuerza de cierre se obtendría con ellas y por tanto, mayor seguridad de cierre. Aunque esto es en parte verdad, hoy se ha demostrado que con pestañas de 130 mm. se consigue toda la fuerza de cierre requerida para mantener cerrado un molde de cualquier tamaño. También se consideraba que la capacidad de vacío de las pestañas era mejor si contenía una gran cámara abovedada entre las dos juntas de cierre. Esta filosofía requería emplear material en exceso para fabricar esas pestañas. Hoy, toda la fuerza de cierre necesaria se consigue dejando un sencillo hueco de 1 mm. entre las dos pestañas paralelas del molde y contramolde. Este sistema a su vez necesita una menor evacuación de aire para alcanzar una posición de cierre completo del molde. En consecuencia, el nuevo sistema de cierre permite un ahorro en el coste de los moldes y utiliza menos energía durante la operación.
En LTRM siempre hubo necesidad de dos juntas de cierre. Una, para impedir que salga la resina del molde (cierre primario) y que se coloca lo más cercana posible al borde de la cavidad y la otra (cierre secundario), que está situada lo mas cerca del final de la pestaña cerrando la zona de vacío. Pocos cambios han experimentado las juntas usadas para los cierres secundarios a lo largo de estos años de desarrollo del LRTM y todavía es corriente usar juntas blandas en forma de ala (wing seal). Sin embargo, hubo una gran variedad de diseños y estilos en las juntas del cierre primario.
Inicialmente se usaron juntas de silicona maciza con perfil tipo hongo (mushroom seal), que dieron un servicio razonablemente bueno pero, sin embargo, presentaron faltas de eficacia cuando se emplearon en pestañas de formas complejas, por lo que han quedado solo para uso en pestañas planas. La necesidad de juntas que tuvieran un buen cierre en moldes con pestañas de cualquier tipo llevaron al desarrollo del hoy común 'nose seal' de 12 x 14 mm. de tamaño y acabado redondeado. Se fabrican en silicona maciza o hueca. Esta última, presenta la característica de que se puede inflar y desinflar por lo que se le denomina 'cierre dinámico' (dynamic seal). Esta posibilidad de controlar la presión interna de la junta mejora enormemente la eficacia del cierre y se puede usar como ayuda en la apertura del molde, después del curado de la pieza, una vez se ha eliminado el vacío de cierre. Este tipo de apertura del molde se le ha bautizado con el nombre de 'empuje neumático'.
Insertos para los moldes
En el LRTM para conseguir el vacío necesario y controlar la resina en el molde hay que considerar unos accesorios de conexión de tuberías. Al principio, muchos consideraron que estas conexiones eran sencillas y se diseñaron tantos modelos como empresas había, por lo que no se estandarizaron. Posteriormente, comenzó la demanda de accesorios e insertos profesionales con un cierto grado de estandarización que inicialmente comercializó y lideró la compañía inglesa Plastech TT Ltd. por el 2001. Insertos; desde los que se usan en la pestaña del molde para el cierre por vacío, los de la copa de vacío que recoge la resina sobrante (catchpot) y los conectores para la inyección de resina, se introdujeron y copiaron por todas partes hasta el 2007.
Hace dos años se introdujo un nuevo 'inserto universal', compatible con todas las copas de vacío 'catchpot' existentes y conectores de inyección, incluyendo en el mismo un clip de fijación de diseño patentado. Un simple inserto metálico, común para todas las necesidades y tipos de conexiones al molde, está disponible y aporta una pieza universal a esta industria. Así, por ejemplo, tanto si se usa un tubo de 10 mm. cómo una válvula de inyección automática para conectar la máquina de inyección al molde, siempre se utilizará el mismo inserto. La experiencia de muchos años de trabajo nos enseñó que los cierres de doble junta tórica y los mecanismos de simple efecto eran los mejores para la seguridad de las conexiones del molde, y estos son principios del nuevo inserto.
Cierre del molde
Para conseguir el cierre inicial de los moldes LRTM lo que permite la aproximación de la junta de del cierre secundario al molde a fin de que luego se consiga un cierre hermético por vacío, en muchos moldes solo se disponía en los comienzos la fuerza manual o el ineficiente uso de los cierres 'G' también aplicados a mano. Aún, hoy en día, no en todos los talleres, tienen resuelto el problema con una solución técnica eficiente.
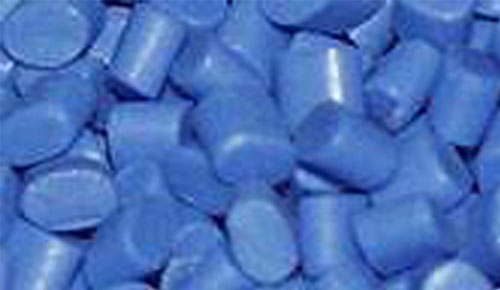
Los más comúnmente empleados en estos días son los cierres de tipo camión. Estos cierres únicamente se utilizan para proporcionar la suficiente fuerza de cierre inicial para compactar las fibras de modo que la junta exterior del contramolde (cierre secundario) se apoye totalmente sobre la pestaña del molde para luego poder hacer un vacío correcto. Otra forma de conseguir un buen cierre de la junta exterior consiste en diseñar los moldes de forma que en los bordes del molde y contramolde se hagan extensiones verticales en donde se coloca una segunda junta de cierre, que proporciona un vacío auxiliar a 50 mm. de la posición de abierto. Esta técnica se introdujo en los primeros días del Vari (Vacuum Assisted Resin Injection), allá por el año 1980 pero ha perdido popularidad por el trabajo extra que requieren los moldes. Es mejor aplicarla en el diseño moldes en los que las pestañas están en un único plano, como es el caso de cascos y cubiertas en la industria náutica.
Métodos de inyección y excesos de resina
Desde el origen del LTRM hasta la actualidad, siempre se ha considerado que la inyección de resina debe ir desde la periferia hacia el centro. Sin embargo, el 'canal' por el que la resina se distribuye por toda la periferia, para penetrar en el molde, ha ido evolucionando con los años. Al principio tenía 20 mm. de ancho por 4 mm. de alto alrededor de toda la cavidad del molde y desde él la resina penetraba libremente sin ninguna restricción en todo el molde a lo largo de sus paredes.
Hoy en día, se considera mejor hacer un canal de más caudal pero alimentar desde el mismo al molde por una restricción de solo 0,5 a 1 mm. La razón para este cambio está en que así se consigue un llenado más rápido del molde y es más fácil el recorte de las piezas obtenidas. Ahora, el diseño es un canal abovedado de 20 mm. da ancho por 10 mm. de altura máxima. Para los moldes de un perímetro inferior a 4 m. hay disponibles secciones menores. Existen juntas de silicona reutilizables para fabricar los moldes con ambos tipos de canal, siguiendo el mismo sistema que se emplea para el calibrado de los moldes.
Se ha comprobado recientemente que, al reducir la distancia entre el canal de distribución de la resina y la cavidad del molde a 1 mm. ó menos como forma económica de moldear al conseguir piezas acabadas de molde al terminar el borde de la pieza en 1mm. ó menos. Esto requiere vestir el molde con las fibras de forma meticulosa, pero es más fácil hacer esto que no luego tener que desbarbar las piezas en todo su espesor. El nuevo sistema consigue piezas acabadas en su contorno, haciendo más rápida la operación de desbarbado, produciendo menos polvo, menos desperdicios y como resultado mucho más económicas. El borde de la pieza de 7 mm. no necesita desbarbado final.
Nuevo sistema de alimentación central de resina
Se ha enfatizado suficientemente que el sistema LRTM emplea la alimentación de la resina por la periferia y hace fluir la resina de forma convergente hacia el centro de la pieza. Sin embargo, hay casos en los que vale la pena invertir este sistema de alimentación. Consideremos un molde que tenga 3 m de largo por 0´5 m de ancho. La vista en plano de este molde se presenta en cuatro dibujos. Los dos de la izquierda corresponden a como se llena este molde con el sistema típico de llenado desde la periferia y los de la derecha como se hace si la alimentación de resina se hace por el centro hacia la periferia.
En el primer caso se observa claramente que las posibilidades de la resina para alcanzar el centro simultáneamente y de manera controlada no son muy altas y en consecuencia quedan huecos en el centro sin llenar o que bien habrá que perder material en exceso por el rebosadero. La experiencia ha demostrado que en moldes de esta geometría su llenado desde la periferia es complicado sin un sistema de vacío múltiple que reduzca las probabilidades de dejar zonas secas.
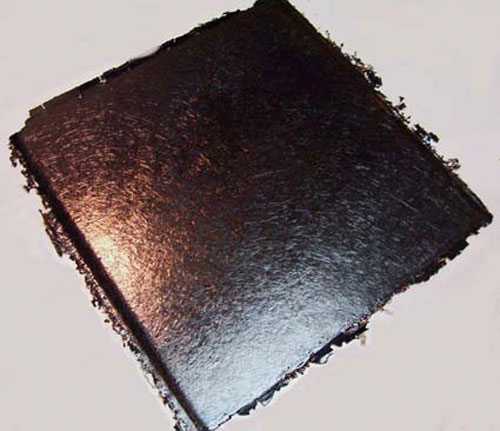
La alternativa de usar el punto central para inyectar la resina comporta un riesgo notoriamente menor de llenar el molde de forma incompleta o de perder un exceso de resina evacuando el aire del molde a través de su junta primaria, que impide cualquier paso de resina pero sí permite extraer el aire.
La introducción de la inyección por el centro ofrece ahora una alternativa a la inyección para fabricar largas palas eólicas, donde los altos porcentajes de fibra usados acortan la velocidad del flujo. En estos casos se pueden usar una serie de puntos de entrada estratégicamente colocados formando un canal en el contramolde para irradiar la resina dentro del molde tal como lo hacen las hojas a través de sus venas y obtener velocidades de flujo predecibles, incluso en piezas de mas de 50 metros. Las obvias ventajas del proceso LRTM sobre la infusión están en que todo el material es reutilizable y no hay consumibles de film, peel-ply, tuberías, etc. En el año 2006 en otra presentación demostré que el proceso LRTM resulta más económico que la infusión por vacío, siempre que se fabriquen series superiores a 17 – 20 piezas.
Control de la temperatura del molde
La necesidad de fabricar piezas con resinas epoxi o fenólicas por el método LRTM, no es más complicado que hacerlo con resinas de poliéster o de vinylester, siempre que se controle la temperatura de los moldes. Al igual que con los moldes de RTM, los de LRTM se pueden fabricar para que incluyan cerca de la superficie, calefacción eléctrica o un sistema de intercambiador de calor/frío. Los sistemas de recirculación de agua son los más frecuentes y aportan condiciones ideales de temperatura para los sistemas epoxi de dos componentes. Los métodos y técnicas para fabricar piezas en composites usando moldes con temperatura controlada están ya estandarizados y los incluimos siempre en nuestros cursos internacionales para la fabricación de moldes.
Si consideramos la forma en la que se aporta la resina al molde, es evidente que han habido mejoras evidentes, desde los tiempos en los que al terminar el llenado del molde las tuberías de resina se cerraban con tenacillas, debiendo reemplazarse estas después de cada proceso. Este viejo sistema ha quedado completamente eliminado con la válvula automática de inyección de control neumático, que se monta en el perímetro del molde. La máquina de inyección envía una señal que abre esta válvula y permite que la resina fluya libremente dentro del canal de alimentación del molde hasta que el proceso se haya completado. En ese momento la válvula se cierra.
Entonces la válvula se limpia automáticamente con una mezcla de disolvente y aire que entra a gran velocidad. No hay ningún consumo de tuberías ni se vierten restos de resina. Gasta pequeñas cantidades de disolvente y el último diseño de válvula consigue más de 1.000 inyecciones en servicio. Este sistema permite una operación limpia y segura.
Control de baja presión en la máquina de inyección
Unas de las mejoras tecnológicas más importante que se han producido en el LRTM han sido los diversos métodos de controlar la presión de salida de las máquinas inyección de resina, de forma que no se exceda a la presión atmosférica. La industria ha contemplado muchos sistemas con diversos grados de éxito. La mayor preocupación ha estado en que algunos sistemas de inyección, presentes en el mercado, pueden superar el vacío del cierre del molde por su excesiva presión, obteniendo piezas de demasiado espesor, fugas de resina, entrada de esta en el sistema de vacío del cierre y en los peores casos, distorsiones de la cavidad del molde y fallos para moldear piezas buenas.
Muchos prueban dejar que el operador decida y controle el flujo de salida y así controlar la presión con que la resina entra en el molde. Desgraciadamente, aunque la boquilla de la máquina tenga un sensor de presión, no es posible durante la etapa de llenado controlar el llenado del molde de una forma definitiva sin la ayuda del operador. En los equipos más modernos se usa un contador del volumen de llenado, pero esto solo controla el volumen de resina que entra pero no su velocidad de flujo ni su presión. El único medio seguro es emplear en el molde un sensor de su presión interna, suficientemente sensible para actuar en el rango de milibares. Un sensor, situado en el canal de distribución de la resina del molde, permite conocer exactamente cual es la presión dentro del molde en cada instante.
Esta señal de presión se puede transmitir a la máquina que está diseñada para responder automáticamente, modificando la velocidad del flujo según se esta llenando el molde, de acuerdo a la presión de seguridad. Así se tiene una operación de inyección totalmente controlada que da suficiente confianza al operador para dejar que el molde se llene automáticamente y de forma segura por si mismo. A modo de ejemplo diremos que algunos moldes necesitan 300 kilos. o más de resina para llenarse en un tiempo de más de 50 minutos. En estos casos, lo mismo que en otros moldes más pequeños, su llenado se hace controlando la presión del molde sin necesidad de que intervenga el operario
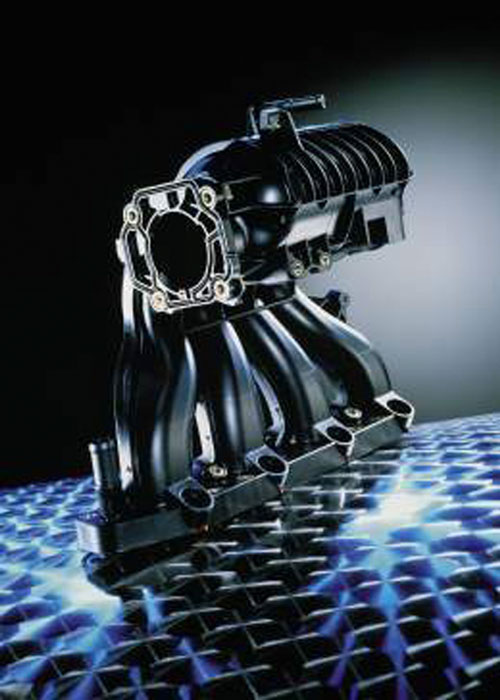
.
Ha habido y todavía hoy existe, un error de concepto al pensar que la presión en la boquilla de inyección es la misma que la presión dentro del molde. Esto es falso. Considerando que hay un cierto recorrido - longitud del tubo y accesorios intermedios - que la resina ha de atravesar antes llegar al canal de distribución del molde, siempre habrá una caída de presión entre ambos puntos durante la inyección por lo que siempre será mayor la presión en la boquilla de la máquina que en el interior del molde. Esta caída de presión depende del flujo de inyección. Cuanto mayor sea el flujo, mayor es la caída de presión.
Si, por ejemplo, un molde se comienza a llenar a una velocidad de 4 kg/min, la presión en la boquilla puede llegar a ser de de 2 bar. Dado que el molde LTRM solo acepta presiones inferiores a la atmosférica, para no sufrir distorsión, es claro que si mantenemos esa presión de forma continua, podemos alcanzar sobrepresiones internas y llegar a distorsionar el molde. En esas circunstancias el operario deberá estar constantemente reprogramando la velocidad de la máquina a medida que se va llenando el molde y aumenta la presión interna.
El operario solo puede hacer esas correcciones basado en su experiencia, ya que no es la presión en la boquilla sino la interna del molde la que se debe controlar. Solo si se conoce esta presión el operario sabe el nivel de presión de seguridad para reajustar el caudal de la máquina. Esta necesidad ha llevado a desarrollar un sensor de presión robusto que permite conocer la verdadera presión interna del molde. Es también es muy útil el disponer de indicadores de nivel de vacío de cierre del molde y de llenado de la resina que han sido muy bien acogidos por los fabricantes que así pueden disponer de medios fiables para llenar sus moldes y prescindir de las suposiciones.
Ultimas sofisticaciones en el control de la máquina
Los equipos actuales han alcanzando un gran refinamiento en los procesos de control. Esto no es más que las mejoras introducidas en las máquinas de LRTM. Ahora se comercializan máquinas con cabezales automáticos muy sofisticados con bloqueos de seguridad internos, contadores dosificadores de resina, alarmas de gelificación de la resina y por parada de bomba y más recientemente un control neumático para variar el porcentaje de catalizador a medida que se va llenando el molde.
Para las resinas de poliéster y de vinylester el porcentaje de catalizador a emplear se ajusta a un nivel para toda la operación de llenado, sin embargo, ya hay en el mercado un sistema que puede fácilmente ir aumentando el porcentaje de catalizador a usar a medida que se va llenando el molde. Este grado de sofisticación ya existía en las máquinas de alta gama dotadas de PLC. Sin embargo, ahora también se encuentran en equipos de inyección estandar. La bajada de precios, del variador de catalización, se ha conseguido por el uso de un motor de aire. Un ejemplo de este sistema es el MotoCat, que tiene un diminuto motor de aire reversible para modificar el nivel de catalizador. Se puede colocar externamente y manejar manual o automáticamente usando un microcontrolador.
La ventaja de poder ajustar el catalizador 'sobre la marcha' está en que la reactividad de la resina se puede ir modificando a medida que se llena el molde, mejorando mucho la productividad del molde. A medida que se va llenando el molde se aumenta la reactividad de la resina con lo que se acortan los tiempos de gel y curado de la pieza. El sistema se puede programar para aumentar el nivel de catalizador en cantidades discretas a medida del llenado del molde. El uso de un motor de aire aporta con seguridad el movimiento mecánico de la máquina evitando la energía eléctrica y cumpliendo con las legislaciones vigentes más exigentes en máquinas de mezcla química.
Sistemas de vacío en planta
Tradicionalmente, los fabricantes de LRTM seleccionan una bomba de vacío comercial y la completan con la necesaria instalación para usarla en varios puntos de su fábrica. Muchos han elegido una bomba de vacío de alto volumen para obtener los dos niveles de vacío que se requieren en esta tecnología y los ajustan con controladores de vacío. También existe la tendencia a colocar un gran tanque de vacío en el sistema. Pocos medidas se han tomado en sistematizar un método rutinario para las tomas de vacío de cada molde. Muchos han usado tuberías de plástico con juntas resistentes a los disolventes y una gran variedad de conectores no diseñados especialmente para vacío.
Un problema de seguridad con estos primitivos sistemas es que si el operario quería alcanzar rápidamente el vacío en un molde podía verse adversamente afectado otro molde ya inyectado y llenado u otros moldes conectados en la línea. Problemas mayores existen con los grandes recipientes acumuladores de vacío que cuando se pierde el vacío se necesita mucho más tiempo para recuperarlo que en un sistema sin grandes acumuladores. En el sistema tradicional de termoconformado se usa habitualmente este sistema pero eso no quiere decir que este sea el adecuado para el LRTM.
Se ha desarrollado un método más sencillo que no emplea grandes depósitos de vacío y la línea de vacío de cada molde dispone de su válvula de seguridad automática para proteger el vacío en cada molde, con independencia de las variaciones en la línea principal de vacío y las periódicas pérdidas de vacío que se producen. Las tuberías de las instalaciones de vacío se prefiere que sean transparentes y flexibles, con sencillos conectores de abrir/cerrar con juntas de cierre, proporcionando la seguridad del vacío a cualquier temperatura. Cada línea de vacío tiene su filtro interno, como los primeros sistemas, pero sin la absorción de fibras y las consiguientes pérdidas de tiempo por el bloqueo en juntas y uniones de las tuberías opacas y rígidas de entonces.
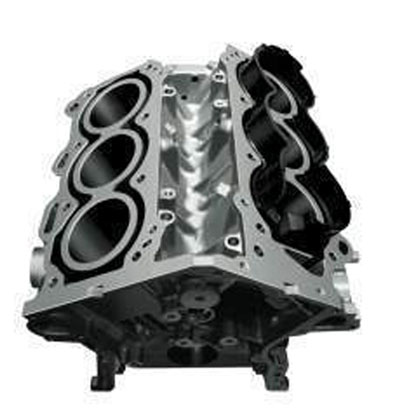
En aquellas circunstancias, los usuarios no podían saber donde estaba el boqueo y se tenía que renovar todo el conjunto con un coste muy elevado. Los actuales proveedores de LRTM suministran todos los materiales y accesorios para usar en estos equipos. Con un brazo articulado de soporte sobre cada estación de moldeo, eliminamos del área de trabajo todas estas tuberías.
Manipulación de los moldes
En los días del pesado RTM clásico, los moldes que se empleaban necesitaban de maquinaria industrial de elevación igualmente pesada para manejarlos. Se ha observado que este mismo sistema se está empleando en muchas plantas donde se manejan moldes LRTM. Es cierto que algunas de estas plantas pueden necesitar elevadores de 1 – 2 toneladas, pero no en la mayoría de las plantas, incluso cuando se manejan moldes de hasta 10 metros cuadrados. La tendencia actual se aparta del sistema clásico con la introducción sistemas industriales de elevación eléctricos de coste muy inferior. Están certificados para manejar hasta 220 kilos y se están empezando a usar ampliamente por esta industria por ser actas para este uso y muy económicas.
Conclusiones
No hay duda de que el LRTM continúa siendo el método más popular de producción, a molde cerrado, en la industria de los plásticos reforzados. Los desarrollos tecnológicos conseguidos a lo largo de esta última década lo demuestran así como las inversiones realizadas junto con el deseo de llevar este sistema de trabajo a nivel cero -emisiones de compuestos orgánicos volátiles (VOC)- y al más alto nivel profesional. Constantemente la prensa profesional nos presenta evidencias de los éxitos del LRTM consiguiendo piezas mayores y más sofisticadas. La tendencia hacia la total automatización es evidente y ha elevado la calidad de las piezas de PRF sobre las que se obtienen por moldeo manual ó proyección, llevando a los clientes que usan piezas de plásticos reforzados PRF a preferir los nuevos grados de calidad.