Dos moldes estándar al mismo tiempo para duplicar la producción
Jornadas
Cuando se plantea una inversión en una nueva célula de producción es importante valorar cómo influirán las características técnicas de una inyectora en la rentabilidad de toda la célula de producción, incluyendo la máquina, los utillajes y las automatizaciones secundarias. Hay tres factores que entran en juego en la rentabilidad: los ingresos, los costes y las inversiones totales. Intentar minimizar o maximizar un factor individualmente no mejora necesariamente la rentabilidad.
Los avances en la tecnología de la inyección han llevado ya a una reducción del 30% en los costes de fabricación durante la última década, aunque los mayores ahorros le han venido dados al cliente final en forma de reducción de precios. Como consecuencia de ello, los inyectadores necesitan encontrar nuevas formas de mantener sus márgenes de beneficio, en un entorno económico mundial menos favorable que en el pasado. Y aquí los constructores de máquinas juegan un papel importante. Deben ofrecer nuevos diseños y mejorar las capacidades.
En lo que respecta a la rentabilidad, las máquinas pueden ser observadas desde tres puntos de vista diferentes: los factores que influyen en el coste, los que influyen en los ingresos y los que influyen en el nivel de inversión.
En cuanto a los primeros, reducir costes es la primera forma de aumentar las ganancias en un mercado maduro donde el crecimiento anual no es significativo y donde los clientes miran sobre todo el precio. El coste de una pieza inyectada se reparte entre el material, la máquina el molde, el personal, las labores de mantenimiento y la energía. La tecnología de la máquina tiene una influencia directa sobre todos estos factores.
Por otro lado, los ingresos de una planta de inyección dependen de la eficacia de su equipamiento. La cantidad piezas buenas producidas es el resultado de los tiempos de ciclo y de la calidad.
Y en cuanto a la inversión, una célula de producción básica contiene una inyectora, uno o varios moldes y una automatización secundaria. Una opción es elegir la máquina más barata. Otras opciones pasan por la comprensión de estos tres factores, lo cual ayudará a realizar la inversión correcta para cualquier aplicación.
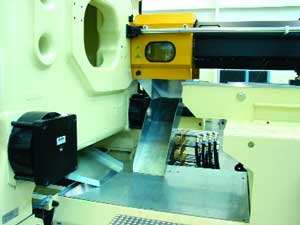
Reducción de costes
Pero, ¿cuál es el potencial de reducción de consumo energético de las máquinas eléctricas? El tema es largo y existen varios puntos de vista. En el número de Julio/Agosto de Plásticos Universales se abordará en profundidad y por lo tanto postponemos un análisis más detallado. Pero al menos unos breves apuntes: utilizar un accionamiento eléctrico para el husillo es lo más adecuado para ahorrar costes, pero el uso de otras funciones eléctricas para reducir la necesidad de energía es algo que hay que estudiar con cuidado para cada aplicación. Además, el ahorro difícilmente alcanzará un 1,5% en el coste total de la pieza.
Otra posibilidad de ahorro está en la reducción del peso de las piezas. En los últimos diez años se ha reducido el peso de muchas piezas entre un 20 y un 30%. Una envase de un litro de 48-50 gramos en 1990 puede pesar ahora 35-38 gramos y los envases de 500 ml han pasado de 20 a 15 gramos. También los ciclos han bajado entre un 10 y un 20% en la última década. Por ejemplo, un envase de yogur se moldea hoy en 5,5 segundos, frente a los 7segundos de 1990. Por lo tanto, el coste de las piezas, incluidos el material y los costes operativos, han bajado al menos un 30% en estos últimos diez años mediante la reducción del peso de las piezas.
Es interesante observar que la reducción del peso era algo muy importante en el sector de envases de paredes delgadas en la primera mitad de los 90. Sin embargo, aún siendo importante, ya no es el enfoque principal, porque muchos envases están ya cerca del límite de peso, tanto por la aceptación entre los consumidores como por cuestiones físicas. Lo que ocurrió hace diez años en el sector de los envases de paredes delgadas, está llegando ahora a otros sectores.
También la calidad de las piezas y los índices de material desperdiciado, influenciados por la repetibilidad del proceso, influyen en los costes
En resumen, unos parámetros del proceso repetibles y la inversión en una inyectora más precisa puede tener una influencia directa en el coste de la pieza moldeada y en la rentabilidad. Reducir el índice de material desperdiciado de un 3% un 1% puede bajar el coste de la pieza en un 1,5%.
Bajar el coste de la máquina
Hay otras formas de reducir el coste de la máquina, como utilizar una máquina más pequeña y más barata para una aplicación determinada. En muchos casos la selección de una máquina no se deriva de la fuerza de cierre necesaria para la aplicación, sino por el tamaño físico del cierre en relación con las dimensiones del molde. Un cierre de 8.000 kN puede ofrece un espacio entre columnas de 950 mm a 1.320 mm. Esos 370 mm representan una diferencia del 39%, lo cual puede tener un impacto enorme en la selección de un cierre.
Una máquina con mayor espacio para el molde permite un incremento en el número de cavidades y por lo tanto una mayor capacidad de producción.
En lo que respecta a la selección de un modelo más pequeño, en base a unas exigencias menores de fuerza de cierre, es de destacar que la distribución de la fuerza de cierre por la cara del molde impacta también en la fuerza de cierre necesaria. Una distribución desigual de las cargas por la ubicación de las uniones de la rodillera causa una deformación en el plato y el tonelaje debe ser aumentado para corregirla. Esta deformación también perjudica a la calidad de la pieza.
El plato tipo Reflex de Husky ha sido patentado. Está pensado evitar la deformación cuando se somete a toda la fuerza de cierre. Las fuerzas que imparten las columnas se aíslan en los bordes del plato, impidiendo así la deflección en la zona del molde.
Las máquinas Hyelectric incorporan las fuerzas de cierre detrás del plato móvil y utilizan el diseño Reflex en la parte fija. Una distribución regular de la presión superficial reduce la cantidad de presión necesaria para el blocaje.
Aumentar la capacidad de producción
Los avances en la productividad de las máquinas durante las últimas dos décadas se muestran en este ejemplo real: una empresa (cliente de Husky) producía a principios de los 80 unos 235 millones de preformas para botellas de dos litros con tecnología avanzada, con 17 máquinas de 4.000 kN de fuerza de cierre, equipadas con moldes de 16 cavidades y con ciclos de 35 segundos. Hoy en día, un solo sistema de 6.000 kN, con un molde de 144 cavidades, alcanza la misma producción.
Esta tendencia continúa hoy en día con la generalización de moldes apilados que no obligan a un gran aumento del tamaño de la máquina, pero que duplican la producción.
En algunos casos los transformadores también quisieran aprovecharse del aumento dela productividad que proporcionan los moldes apilados, pero las producciones no tienen el volumen suficiente como para justificar un inversión en moldes apilados específicos. Este podría ser el caso de grandes piezas para electrodomésticos o similares, donde se prefieren normalmente moldes sencillos por la flexibilidad que ofrecen en la producción.
Y es aquí precisamente donde los soportes multimolde de Husky encuentran su verdadero beneficio: en la conversión de estos moldes estándar en configuraciones flexibles de dos niveles. Se pueden instalar dos moldes estándar, de una sola cara, en una sola inyectora, pero que funciona con una configuración de dos moldes. De esta forma la capacidad de producción de una máquina se duplica, al igual que ocurre con un molde apilado.
Conclusiones
En este artículo sólo se han considerado las cuestiones relativas a la inyectora y su influencia en la rentabilidad. Pero no hay duda de que existe un potencial enorme también en el campo de la logística, la gestión de materiales, la automatización.