La importancia del tiempo de permanencia, el parámetro oculto
El 'tiempo de permanencia' es un factor que a menudo no se ha tenido suficientemente en cuenta en las plantas de inyección, sin embargo, es determinante en la calidad del proceso en tanto que puede afectar a las propiedades del material, y por tanto, a las piezas fabricadas.
En el entorno de la fabricación es reconocida la influencia en la calidad y en la productividad de los factores, persona, material, máquina, método. Centrándonos en el factor material, al margen de la selección correcta del material y del secado o de su tratamiento previo, el factor determinante en el proceso de inyección será la temperatura del material fundido y el tiempo de permanencia del material en la unidad de inyección.
En un proceso de inyección ideal, una vez que el proceso ha sido definido, con el paso de los minutos desde el arranque de la fabricación, el proceso se sitúa en una estabilidad térmica, tanto del molde como del material. Los inputs térmicos se equilibran en un determinado punto con los outputs, es decir, la aportación térmica de las resistencias de la unidad de inyección, de la energía térmica generada en el interior de la unidad de inyección por el husillo, se compensa con la refrigeración del molde, de la traversa, etc.
Cuando se produce un defecto en el proceso, normalmente centramos la búsqueda de la causa en múltiples posibles causas, tales como, parámetros de inyección, secado del material, diferencias de características del material, estado del molde, sistema de refrigeración, etc.
Sin embargo, existe un factor que a veces pasa desapercibido en la búsqueda de la causa raíz del problema. Se trata del 'tiempo de permanencia'. Tiempo que no controlamos directamente y que algunos llaman “El parámetro oculto".
¿Qué es el tiempo de residencia? En mis seminarios siempre explico que este concepto es el tiempo que tardaría un pellet de material en entrar por el agujero de la tolva en el husillo y salir convertido en pieza. Es por tanto el tiempo que el material está siendo sometido a temperatura y presión.
Los fabricantes de polímeros suelen informar de los tiempos máximos de permanencia de sus materiales a las temperaturas de proceso. Esto es debido a que la degradación molecular y de los aditivos incluidos en la formulación del polímero se producirá en un tiempo determinado en función de la temperatura utilizada. Se trata de una relación inversa tiempo-temperatura. A mayor temperatura menor tiempo de permanencia disponible para procesar el plástico antes de que entre en zona de degradación.
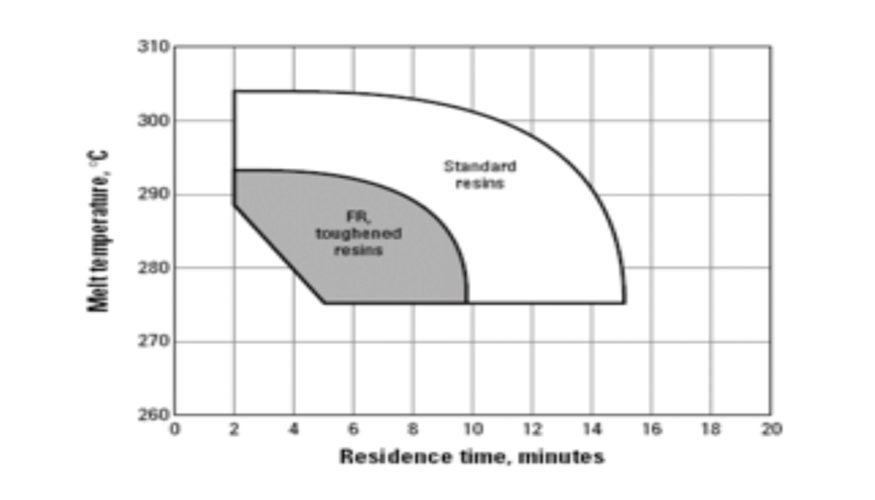
En la figura podemos ver que este material estándar entraría en zona de degradación a los 10 minutos de 'tiempo de permanencia' a 280 °C y a los 8 minutos a 290 °C. Para material retardante de llama' los tiempos son menores debido a la degradación más rápida de los aditivos ignifugantes.
Entrar en la fase de degradación térmica del material por exceso de 'tiempo de permanencia' provoca irremediablemente una serie de consecuencias.
Inicialmente tendremos una pérdida de propiedades del material por pérdida de peso molecular y degradación de los aditivos de la formulación, es decir propiedades mecánicas, térmicas, etc se verán irremediablemente afectadas.
Podremos observar también un aumento de la fluidez del material, consecuencia esta también de la degradación molecular producida. Esto puede provocar, rebabas, gases, marcas de expulsión, etc.
La presión necesaria para llenar la cavidad será menor como consecuencia de la perdida de viscosidad.
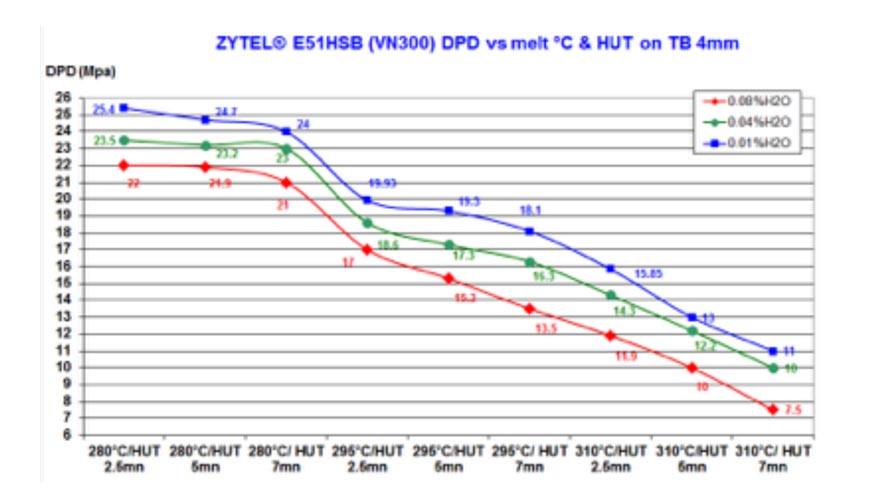
En el gráfico podemos ver la caída de presión necesaria para llenar la cavidad con diferentes tiempos de permanencia (HUT) y diferentes temperaturas. Esta caída de presión necesaria para llenar la cavidad está relacionada directamente con la pérdida de peso molecular.
Generalmente cuando hay un defecto en las piezas procesadas, el ingeniero de proceso mira en múltiples direcciones buscando la causa, cuando esta podría estar en el 'tiempo de permanencia' excesivo.
Los defectos típicos que puede provocar un exceso de tiempo de permanencia pueden ser:
- Rebabas: Causa raíz, la caída en la viscosidad debida a la degradación molecular y perdida de aditivos.
- Quemados, marcas de gases: Causa raíz, incremento de los volátiles en el frente de flujo, más fluidez del material.
- Piezas con fragilidad: Causa raíz, la caída de peso molecular hace que las propiedades mecánicas caigan drásticamente, impacto, flexión y tracción se verán drásticamente reducidas
- Decoloración, olor: Causa raíz, degradación de aditivos y monómeros.
Cálculo del tiempo de permanencia: El cálculo del tiempo de permanencia teórico se puede realizar con diferentes hojas de cálculo.
En teoría el cálculo debe tener en cuenta, el volumen o peso del material contenido en la unidad de inyección (complejo cálculo al disponer de material en diferentes estado de fusión, semi fundidos, etc., por tanto , con diferentes densidades y contenido en un cilindro con un husillo o enrollamiento helicoidal con diferentes alturas de filete en función de la zona del husillo). Debe tener en cuenta el volumen o peso de la inyectada y por supuesto el tiempo de ciclo en curso.
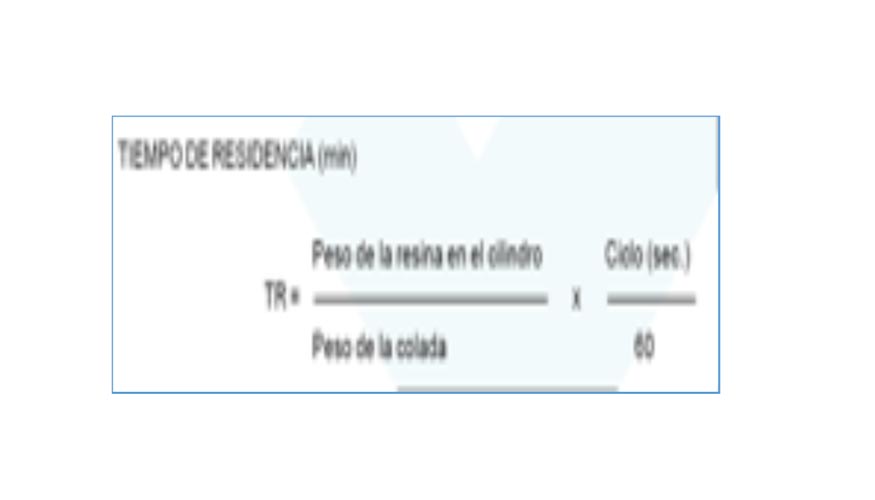
Claramente si el 'tiempo de permanencia' de nuestro proceso es excesivo, tenemos que intentar reducirlo de diferentes modos:
- Reduciendo el tiempo de ciclo (No siempre es posible)
- Reduciendo el volumen de la unidad de inyección (Utilizar una máquina con unidad de inyección menor)
- Aumentar número de cavidades (No siempre es posible)
- Aumentar el tamaño de los canales o coladas (Improductivo).
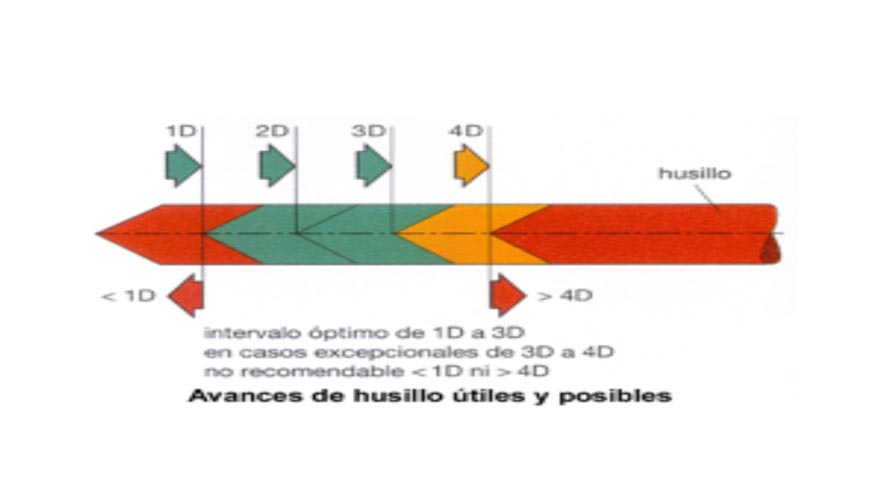
Por eso es tan importante la selección de la máquina a utilizar en un proyecto como se explica en el artículo publicado en esta misma revista …. “¿Qué máquina utilizar?”
Cuando el volumen a inyectar en un molde para un nuevo proyecto nos obliga a invertir en una nueva máquina, es importante al definir la unidad de inyección, tener en cuenta el tiempo de permanencia que tendremos en la fabricación.
Esto es especialmente importante con materiales sensibles térmicamente. He visto algún caso de unidades de inyección sobredimensionadas con tiempo de permanencia excesivos que han provocado no poder fabricar piezas con repetitividad, calidad, robustez y productividad suficientes.
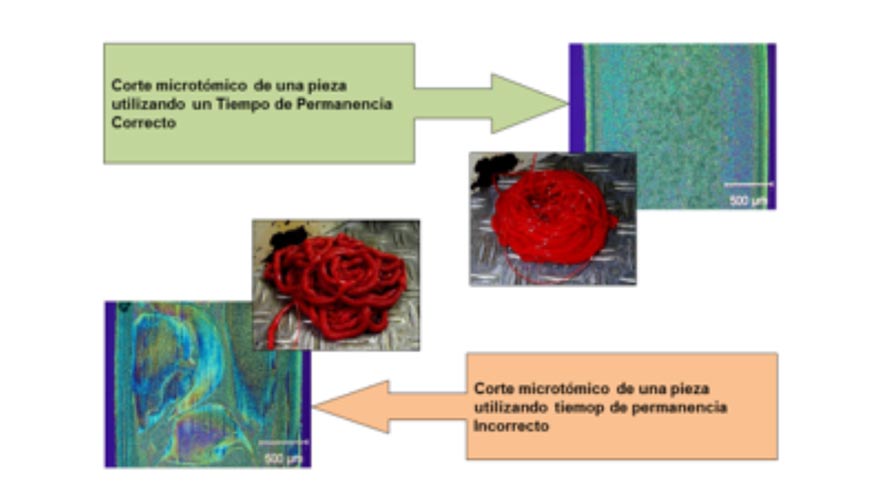
En resumen, el 'tiempo de permanencia' es un factor, en realidad es un out-put que frecuentemente está oculto en el proceso y puede provocar serios problemas de calidad en las piezas fabricadas. Es interesante centrarse en él cuando aparecen defectos como los comentados con el fin de descartarlo en el caso de que el valor sea correcto o por el contrario detectarlo en el caso de ser el causante del problema.
José Ramón Lerma es autor del Libro Manual Avanzado de Inyección de Termoplástico, que tiene como objetivo ser, por un lado, una herramienta para la formación y, por otro, un manual de ayuda para todo el personal de una empresa de inyección de plásticos. El libro, comercializado por Plásticos Universales / Interempresas (libros@interempresas.net), consta de detallados casos prácticos, amplia información de moldeo científico y un ‘pendrive’ con 20 hojas de cálculo y herramientas de SC Molding o Scientific Injection Molding, además de optimización y definición de proceso, lo que lo hacen único en el mercado. Página web sobre Scientific Injection Molding: www.asimm.es
Más información sobre los cursos Scientific Molding online impartidos en Inefco, en los que José Ramón Lerma es tutor https://www.ieaula.com/home/31-procesos-avanzados-de-inyeccion-de-termoplasticos.html