El composite como material a mecanizar
8 de junio de 2012
Existen múltiples tipos de materiales compuestos que se distinguen, principalmente, por el origen de la matriz en la cual los agregados se incorporan (ya sea en forma de fibra larga o partículas de tamaño variable distribuidas por la matriz). Existen tres tipos principales de materiales compuestos:
- Materiales compuestos de matriz cerámica,
- materiales compuestos de matriz metálica, y
- materiales compuestos de matriz polimérica.
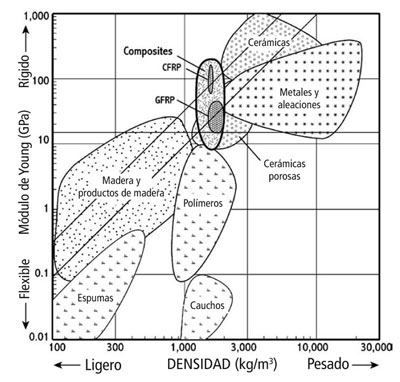
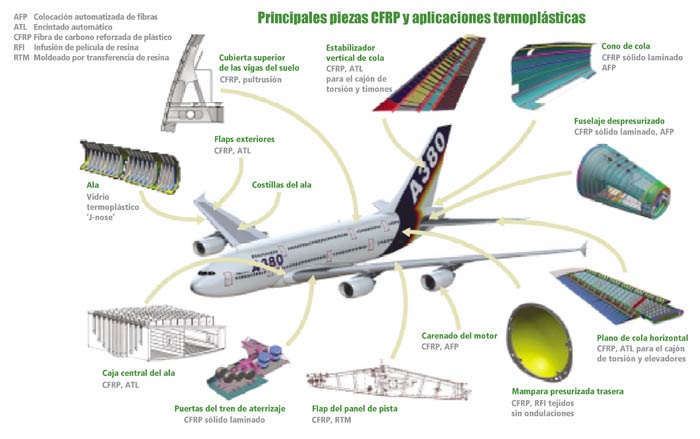
Los materiales compuestos (de matriz polimérica) presentan, por tanto las siguientes propiedades:
- Resistencia a tensión específica, entre 4 y 6 veces mayor que el aluminio o el acero.
- La rigidez específica (la relación entre la rigidez y la densidad) es entre 3 y 5 veces superior al aluminio o al acero.
- Los materiales compuestos proporcionan importantes reducciones de peso. Esta reducción depende del tipo de solicitación y es tanto mayor cuanto más uniaxiales son los esfuerzos. En este caso se pueden conseguir reducciones de peso entre el 25 y el 50% sobre el peso de la estructura de aluminio.
- Excelentes propiedades de amortiguación, gracias por un lado a la discontinuidad de fases y por otro al comportamiento viscoelástico de la matriz polimérica.
- Resistencia a fatiga superior a la de materiales metálicos tradicionales, acercándose al 60% de la resistencia a rotura (muy superior a la del acero y el aluminio).
Necesidad de mecanizado
Los procesos de fabricación de materiales compuestos hacen que su forma sea cercana a la geometría real deseada (‘near-net shape’) y por tanto con necesidades de mecanizar centradas en dos tecnologías clave:
Dotar a la pieza de la geometría final, eliminando el material sobrante que se ha depositado en los procesos manuales de deposición de fibra o telas o los procesos automáticos como pueden ser el ATL o el AFP. Para ello se utiliza el recanteado, que corta el material sobrante geométricamente. En función del acabado superficial resultante, y las necesidades de la pieza puede añadirse un proceso de rebabado.
Los componentes de materiales compuestos requieren su unión al resto de componentes de la estructura, ya sean metales o materiales compuestos. Teniendo en cuenta que la soldadura está todavía en un estado incipiente y el adhesivo es complejo (e impide el desmontaje) la unión mecánica de componentes mediante el remachado es, con diferencia, la tecnología más utilizada. Para ello es necesario el taladrado de las estructuras para la colocación de los vástagos de fijación. Las especificaciones son habitualmente diámetro, posición y geometría, así como calidad superficial obtenida.
Precisamente debido a su estructura y composición, el mecanizado de los polímeros reforzados con fibras de carbono difiere en gran medida del mecanizado convencional de metales. Destacan, de esta forma, la presencia de fibra altamente abrasiva que da lugar a un notable desgaste de las herramientas, y a una resina, en general blanda, y que limita la temperatura máxima que puede generarse durante el mecanizado. Por una parte, la resina es cortada, mientras que la fibra puede ser cortada o fracturada. La orientación de la fibra, además, da lugar a comportamientos distintos y, por tanto, acabados distintos.
Los principales problemas asociados al mecanizado de los materiales compuestos son la delaminación, el astillamiento o el daño térmico:
- La estructura laminar de las piezas de materiales compuestos hace que sus propiedades de adhesión entre las mencionadas capas sean menores que en la dirección de las fibras. De esta forma, un problema a evitar durante el taladrado de las mismas es la delaminación, en la que las fuerzas de corte en la dirección de avance de la herramienta superan las fuerzas existentes entre capas. En el taladrado, dicha delaminación se produce principalmente en la entrada o a la salida de la herramienta.

- Daño térmico: las propiedades térmicas de los materiales reforzados hacen que el calor generado durante el proceso sea absorbido principalmente en la herramienta de corte (50%), mientras que en mecanizado de metales, el 75% del calor es evacuado en las virutas. Esto genera dos problemas distintos: por una parte, la temperatura de trabajo lleva a un aumento del desgaste de la herramienta, y por otra parte, puede generar daño térmico en la resina que está mecanizándose.
- Otro posible defecto generado durante el mecanizado es el astillamiento. El mecanismo de fractura de la fibra de carbono puede dar a lugar a que el corte de la fibra no sea completo.
Finalmente, es necesario mencionar que la elevada diversidad de fibras existentes, así como de resinas, y la presencia de fibras en distintas orientaciones respecto a la pieza conlleva necesariamente una importante variedad de técnicas de mecanizado, así como materiales y geometrías de herramientas, según las propiedades de resina y fibra.
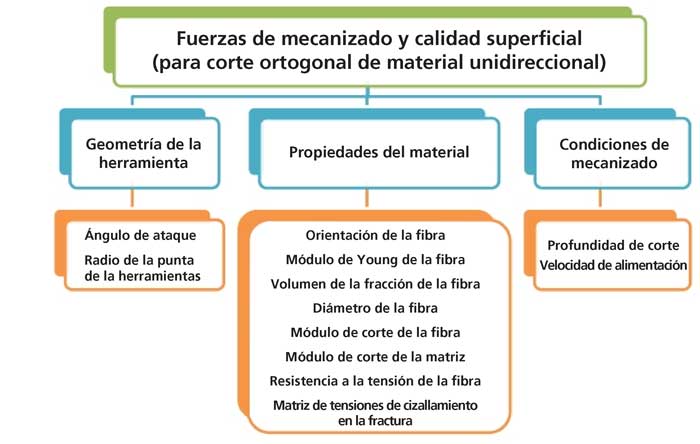
Para solucionar esta problemática, es necesaria una aproximación integral al proceso de corte de materiales compuestos en los que se analizan los siguientes factores:
Herramientas de corte:
Hay que distinguir en este aspecto dos componentes diferenciadas: el material de las herramientas de corte, y su geometría.
Desde el punto de vista de material, las herramientas tradicionalmente empleadas para el taladrado de aluminio y CFRP (Carbon Fiber Reinforced Plastics) han sido brocas de metal duro, el acero rápido no es capaz de soportar el carácter abrasivo de la fibra de carbono. La posibilidad de recubrir el metal duro con recubrimientos que protejan el filo como AlTiN o diamante puede servir para incrementar la vida de la herramienta, pero no parece mejorar la calidad de los orificios realizados ni los esfuerzos de corte. Las brocas con dientes de PCD, ya sean ‘veined’ insertados o simplemente soldados, no mejora los resultados.
En cuanto a su geometría, los principales parámetros que influyen en el corte de composites son el ángulo de inclinación, el radio de la punta de la herramienta y el ángulo de la hélice. El ángulo de inclinación es el ángulo entre el filo y el corte. A modo general, ángulos positivos permite reducir las fuerzas de corte, mientras que ángulos negativos permiten generar una cuña en la pieza.
Por otra parte, para materiales compuestos, son preferibles las herramientas con radio muy pequeño, siendo objetivo que su radio sea menor que el diámetro de las fibras (su diámetro oscila entre 5 y 20 µm). Sin embargo, un radio excesivamente pequeño puede debilitar el corte y producir la plastificación de la herramienta de corte.
Otra división de las herramientas es según la hélice existente. La presencia de una hélice genera una mayor fuerza axial. De esta forma, promueven la delaminación. Para evitarla, los fabricantes de herramientas están introduciendo soluciones basadas en una doble hélice, que se oponen mutuamente y generan compresión del material, dificultando de esta forma la delaminación. Otra alternativa para esto es utilizar dientes raunurados, que modifican localmente el ángulo de la hélice y evitan, también la delaminación.
Para operaciones de taladrado, por otra parte, la geometría de la punta es de elevada importancia para mecanizar los materiales compuestos en las condiciones adecuadas. Destacan en este aspecto, las herramientas helicoidales convencionales, las de diente recto, y las herramientas escalonadas rectas o chaflanadas.
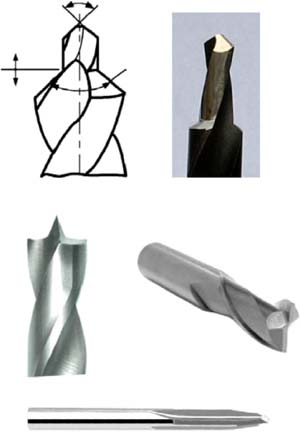
Estrategia de corte:
Dos parámetros principales marcan la calidad superficial así como la generación de delaminación en la zona de corte: la velocidad de corte y el avance.
De esta forma, un aumento en la velocidad de corte conlleva una reducción de la fuerza ejercida y el torque, debido al calentamiento de la herramienta y el material mecanizado, aunque hay que tener en cuenta que temperaturas demasiado elevadas perjudican la calidad del material resultante. Valores elevados de avance generan daños similares a los producidos por impacto (delaminación escalonada, grietas intralaminares…). Con valores intermedios de avance, los fallos se producen especialmente en los momentos de entrada y salida de la herramienta. En particular, el factor relevante para el taladrado de materiales compuestos es la relación entre la velocidad de corte y el avance. Para relaciones elevadas, la superficie obtenida es suave y regular, con mínima delaminación. Para valores pequeños de esta relación, existen daños significativos, con delaminación que afecta a distintas capas, y puede producir desunión entre las fibras.
En cuanto a su influencia en la rugosidad, existen dos tendencias distintas según el porcentaje de fibra y resina. En compuestos de fibra de vidrio con epoxy, la calidad de la superficie mejora con la velocidad de corte y la fracción de fibra. Por el contrario, composites con un gran porcentaje de fibra, se comportan de forma contraria, siendo mejor elevadas velocidades de corte y avances.
Esta notable influencia de los parámetros de trabajo en los inicios y finales de los agujeros hace habitual la modificación de los parámetros de trabajo según su altura en la pieza. Este efecto es todavía más acentuado en los sandwiches metal-composite, en los que se alternan capas de metal y de material compuesto, y metal, con elevada resistencia al impacto, comportamiento a fatiga. En estos materiales, es habitual utilizar estrategias de entrar hasta un determinado punto, para luego retroceder y volver entrar. Tanto en los materiales laminados, como en materiales compuestos, es habitual utilizar velocidades de salida más lentas para reducir la delaminación a la salida del agujero.
Adicionalmente a los problemas ya detallados de calidad resultante, las características resultantes de las partículas generadas durante el mecanizado, que pueden dar a lugar a problemas de salud de los operarios, así como limitar la flexibilidad del sistema debido a la presencia de partículas en el entorno de trabajo. A pesar que en la actualidad los métodos de extracción externos son los más habituales, se están introduciendo sistemas de extracción de viruta a través de la herramienta con mayores porcentajes de viruta absorbida.
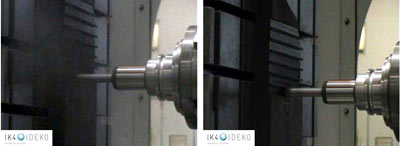
De esta forma, los materiales compuestos requieren principalmente recanteado y taladrado. A pesar de las grandes diferencias con los metales convencionales, los materiales compuestos pueden ser mecanizados sin defectos a partir de un control del material y la geometría de la herramienta, así como la estrategia de corte. Finalmente los problemas de viruta existentes en los compuestos de fibra de carbono o de vidrio son solucionables a partir de la extracción de viruta.