Soldadura de laminados termoplásticos reforzados por resistencia con malla metálica
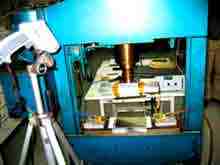
El objetivo es obtener una rápida y homogénea fusión del termoplástico, junto con el subsiguiente proceso de consolidación, ya sea en prensa neumática o hidráulica, de modo que se compatibilice una óptima calidad de la unión, con unos adecuados tiempos de proceso y costes económicos.
Descripción del proceso
Para la realización de los ensayos se toman dos probetas de laminado PPS/GF de dimensiones 25x100 mm. El ensayo consistirá en realizar la soldadura en una zona de solape entre ambas de 25 mm, siendo para ello necesario cortar una longitud de unos 200 mm de malla de acero.
Para evitar problemas de pérdida de corriente debido a la conductividad que presenta el carbono, refuerzo del laminado, se impregnará la malla entre dos films del mismo material termoplástico, es decir, PPS, seleccionándose un espesor óptimo de 120 micras. A continuación, se procede a soldar por ultrasonidos la malla entre los dos films, de dimensiones 29x25 mm cada uno. El tiempo de duración de la soldadura es de 0.54 segundos, a fin de no degradar el termoplástico. Se debe prestar especial cuidado en no dejar aire atrapado entre los films, pues puede deteriorar las propiedades mecánicas de la unión.
Mediante unas pinzas conductoras, se conecta la malla a la fuente de alimentación, y procedemos a fijar ambos laminados a la malla, introduciendo en los bordes de la unión unas tiras de material aislante (UPILEX) para no degradar los bordes de la unión, debido a las altas temperaturas alcanzadas en el proceso. Es necesario en este paso aplicar presión con un gato, para asegurar la correcta geometría.
Se conecta la fuente de alimentación, y se ajusta a unos 35 Amperios, comprobando con la pinza amperimétrica la intensidad real que circula, y se asegura que no se producen pérdidas debidas a la conductividad del carbono.
Se monitoriza la evolución de la temperatura superficial alcanzada, de acuerdo a los datos obtenidos del pirómetro y la cámara termográfica.
Una vez alcanzada una temperatura superficial del orden de unos 250ºC (la temperatura de cristalización del PPS es de 242ºC), se procede a desconectar la fuente de alimentación, y comienza el proceso de consolidación en prensa.
El modo ideal de realizar la consolidación sería en una prensa hidráulica, no obstante, en la actualidad, ésta se realiza en una prensa neumática, obteniéndose resultados aceptables. Tras la consolidación, el siguiente paso consiste en analizar la calidad de la unión obtenida.
Calidad de la unión
También se han realizado ensayos de cortadura con solape simple en algunas probetas para tener una idea aproximada de la resistencia de la unión.. Para ello se ha utilizado el esquema de la norma ASTM D 1002, teniendo en cuenta que en esta norma se producen problemas de desalineamiento que limitan la interpretación de los resultados
Entre los defectos que podemos encontrar en la unión están la presencia de poros, delaminaciones internas del material, microgrietas, quemado del material, desorientaciones en las fibras, etc. Para cada tipo de ensayo se determinan diferentes tipos de defectos.
Inspección visual
La delaminación es producida como consecuencia de una aplicación insuficiente de presión, de modo que la consolidación del termoplástico no llega a producirse de forma homogénea.
Por su parte, el quemado se debe a que se ha superado localmente la temperatura de fusión de la resina. Como se ha comentado, las mediciones que se realizan de la evolución de la temperatura en el proceso se han realizado superficialmente, pudiéndose alcanzar localmente valores más elevados
Ensayo por ultrasonidos C-Scan
Ensayo de cortadura con solape simple (ASTM 1002)
Conclusiones
Las temperaturas alcanzadas por las mallas permiten una buena unión entre piezas siempre que se produzca una consolidación suficiente para favorecer el mecanismo de autoadhesión entre las dos caras. Por lo que el siguiente paso es optimizar los parámetros de presión
La adopción del uso de resinas termoplásticas, en lugar de termoestables (utilizadas hoy en día en las piezas anteriormente mencionadas), se vería beneficiada con el tipo de unión expuesto en este artículo ya que evita la utilización de elementos más pesados como remaches.
Una posible aplicación a piezas reales, como paneles unidos a rigidizadores, podría llevarse a cabo mediante el moldeo en prensa del rigidizador (rubber forming) y seguidamente, introduciendo la longitud de malla metálica necesaria, y conectándola a la fuente de alimentación, controlando los parámetros del proceso anteriormente descritos, se produciría la soldadura entre el rigidizador y la placa plana, en unos tiempos sensiblemente inferiores a los dedicados actualmente en curado en autoclave.
Referencias
[I] Fernández, M. Frövel, L. Rubio, J. Díaz, I. González. Proc. 22nd International SAMPE Europe Conference, Paris ( 2001)
[A] Offringa, D. Myers, A. Buitenhuis. Proc. 22nd International SAMPE Europe Conference, Paris (2001)
Norma ASTM 1002-01 Ensayo a cortadura con solape simple (2001)