Máquinas de accionamiento totalmente eléctrico
¿INYECTORAS ELÉCTRICAS O HIDRÁULICAS?
La máquina de accionamiento totalmente eléctrico es el sistema que más se acerca a la solución ideal de transformación de materiales plásticos por inyección, ya que la relación de energía necesaria por unidad de trabajo de 1,20/1, es la que mas próxima a la solución “ideal”, aunque utópica, de 1/1.
Además presenta importantes ventajas con respecto a las máquinas de accionamiento hidráulico:
• Mayor precisión, debido a la transmisión rígida y directa de las fuerzas de accionamiento.
• Muy importante ahorro energético.
• Mayor fiabilidad.
• Menor nivel de ruido.
• Elevadas velocidades de trabajo.
• Ergonomía.
• Total simultaneidad de movimientos.
• Eliminación casi total del mantenimiento.
• Medioambiental: eliminación del aceite hidráulico.
Reducción del consumo y los costes operativos
• 50 por ciento respecto a los equipos hidráulicos convencionales (bombas de caudal variable con válvulas proporcionales).
• 40 por ciento respecto a los equipos con bombas de caudal variable con control digital de capacidad y presión (CANbus), y la consiguiente reducción de los costes de transformación.
• Eliminación de los aceites hidráulicos y los equipos correspondientes.
• Reducción del mantenimiento ordinario.
• Reducción de los tiempos de ciclo y mejora de la eficacia productiva.
• Reducción del agua necesaria de enfriamiento del aceite.
Considerando que el consumo energético supone normalmente entre el 15 y el 20 por ciento del precio de la pieza moldeada, el ahorro alcanzado sobre el valor absoluto de consumo específico, permite lograr una sensible reducción del coste de transformación.
Además hay que considerarla ahorro energético que también supone la no necesidad de agua de refrigeración para el aceite en el caso de máquinas hidráulicas, al eliminar el empleo de un equipo de enfriamiento, con su correspondiente consumo de funcionamiento, y su coste de adquisición.
Estudio comparativo de consumo:
Producto: Tapones
Peso total de la inyectada: 38,8 g
Ciclo: 5,9 s (620 cic/h., 23,7 kg/h).
Consumo máquina tradicional hidráulica
con bombasde caudal fijo escalonadas
21,2 kW/h (0,88 W/g)
Consumo máquina hidráulica de caudal variable con
tecnología digital “CANbus”
15,9 kW/h (0,66 W/g)
Consumo máquina all electric, serie ELMA
6,9 kW/h (0,29 W/g)
Ecología
• Ausencia de equipos hidráulicos bajo presión.
• Lubricación de los órganos del grupo de inyección mediante baño de aceite en un cuerpo cerrado de doble estanqueidad.
• Lubricación de todo el grupo de cierre mediante grasa.
• Enfriamiento por agua, en circuito cerrado y presurizado, de los motores, para eliminar los ventiladores.
• Funcionamiento optimizado de los elementos de accionamiento para la reducción al mínimo del nivel sonoro.
• Posibilidad de controles para elementos radiales eléctricos.
Control de producción y teleservicio a distancia
La conexión a la red AMICO, permite asimismo disfrutar de la monitorización periódica efectuada de forma automática por el sistema, asegurando un correcto funcionamiento de la máquina y la prevención de posibles anomalías latentes pero no evidenciadas.
Para que una máquina sea considerada “Full electric” (completamente eléctrica) debe cumplir con una serie de condicionantes básicos:
• Debe disponer de un sistema de cierre totalmente mecánico.
• Debe incorporar un sistema de accionamiento y control totalmente digital.
Grupo de cierre
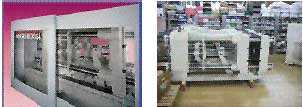
Motores para el cierre de accionamiento directo
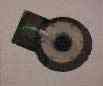
Solidez estructural
El pIato móvil esta dotado de amplías guías sobre las columnas e importantes patines de apoyo en la bancada. La rodillera de 5 puntos dispone de columnas de guiado de la cruceta, fijadas al cabezal posterior.
El grupo de inyección está diseñado particularmente rígido y discurre por guías ampliamente dimensionadas.
El armario eléctrico es de tipo comercial y fijado sólidamente a la bancada.
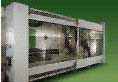
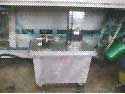
Placa de expulsión como en las máquinas hidráulicas
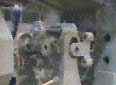
Lubricación mediante grasa de la rodillera
Grupo de inyección
En nuestro caso, se ha afrontado con ingenio e inventiva este problema, desarrollando un sistema innovador (sólidamente patentado), que permite obtener unos valores coste / prestaciones coherentes con las exigencias del mercado. El sistema, relativamente parecido al cinemática de un diferencial automovilístico, utiliza dos motores perfectamente iguales y que uniendo su fuerza garantizan la máxima potencia, tanto en la fase de inyección como durante la de plastificación. El corazón de este sistema es el husillo con recirculación de esferas con filetes contrapuestos en las dos mitades asociadas a dos madres dispuestas simétricamente; el cinemática se completa con la utilización de engranajes Gleason que unen las madres a los dos motores de accionamiento.
Las varias fases operativas, inyección, giro del husillo, plastificación, descompresión, son efectuadas pudiendo disfrutar de muy diversas combinaciones de trabajo y velocidad de los motores.
Veamos como se efectúan todas estas fases:
La fase de inyección
El control de la velocidad linear del husillo es efectuado por medio de los encoder de los motores y controlado, para su verificación, 10.000 veces por segundo por un transductor lineare de tipo magneto estrictivo.
La fase de rotación del husillo y plastificación
Esta fase, que en las prensas hidráulicas es efectuada por un motor coaxial al husillo, hace que el material plástico sea plastificado y dosificado. El material, a causa de la geometría del husillo, del calor y de la compresión a la que es sometido, plastifica y aumenta de volumen ocasionando sobre el husillo una presión que lo empuja hacia atrás.
El husillo, de esta manera, deja libre el espacio al material plastificado que se acumula en la parte anterior del cilindro. Esta fase, que es fundamental para determinar la calidad de la plastificación, en las máquinas hidráulicas es controlada estrangulando (con una válvula de contrapresión), la descarga del aceite hidráulico del pistón de inyección. La válvula de contrapresión es por lo tanto determinante durante la fase de plastificación del material.
En una máquina eléctrica en general y en nuestro sistema en particular, no existe la posibilidad de controlar indirectamente la contrapresión del husillo como en las máquinas hidráulicas. Estamos por tanto limitados a controlar la presión que el material plástico ejercita sobre el husillo para intervenir dinámicamente sobre el sistema, en modo de poder parar el sinfín de recirculación de esferas (y por consiguiente el husillo de plastificación), de forma que la presión del material sobre el husillo mantenga el perfil programado.
Esta operación se obtiene diferenciando la velocidad de los dos motores y manteniendo el mismo sentido de giro. En realidad el husillo retrocede si se aumenta la velocidad del motor y consecuentemente (para mantener constantes las rpm de rotación), diminuye la velocidad del motor que la empuja hacia adelante. Manteniendo constantemente controlado el valor de contrapresión, se opera entonces sobre la velocidad de los dos motores haciendo que se lleve a término la fase de plastificación. Durante esta fase, la posición del husillo (verificada también por el encoder de los motores) es constantemente monitorizada por el transductor lineal del transductor lineal magneto estrictivo.
Obviamente un sistema como este (en donde coinciden 5 parámetros: velocidad motor 1, velocidad motor 2, velocidad giro del husillo, valor de contrapresión, posición husillo) necesitaría un modelo matemático de control extremadamente complejo si fuese accionado por un sistema analógico. La lógica del sistema CAN, en el cual todos los elementos son inteligentes y en grado de intercambiar información vía directa, ha permitido el desarrollo de un modelo de software mas simple y extremadamente mas eficaz.
Prestaciones superiores en el eje de inyección
• Velocidad inyección 200 mm/s
• Velocidad giro husillo 400 rpm
• Par en plastificación de 500 a 1600 Nm
• Presión sobre el material 2000 bar.
Para obtener una economía de escala y permitir una
completa integración productiva, se ha pensado y realizado el nuevo grupo de inyección de forma a utilizar los mismos cilindros y husillos de las máquinas hidráulicas.
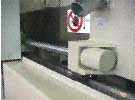
Dobles guías de aproximación y retroceso
El movimiento del grupo de inyección se efectúa mediante dos guías que son al mismo tiempo los elementos que accionados por dos cadenas bien guiadas y movidas por un motor situado bajo la bancada. Estos tirantes deben vencer la resistencia de un muelle situado en la base de las guías.
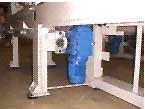
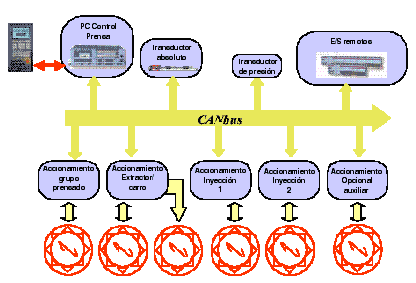
Versión totalmente eléctrica
Utilización del sistema CAN
Como ya hemos mencionado, el uso de la tecnología CAN, ha permitido superar las complejas problemáticas ligadas a la gestión del eje de inyección con un mecanismo simple en su cinemática pero complejo en el modelo matemático que administra las diferentes fases. En un sistema CAN todos los componentes principales son inteligentes y en grado de comunicarse entre si y dejando al PC (cerebro de la máquina) solo la importación y supervisión de las secuencias.
Como ya se ha comprobado ampliamente, esta solución aporta importantes ventajas en la velocidad de respuesta y gestión de datos, reducción del cableado, y en general un menor número de componentes, reduciendo el riesgo de anomalías, no congestiona la CPU principal, compartiendo de forma equilibrada las cargas de trabajo y simplificando el diagnóstico.
El esquema representado aquí muestra claramente la simplicidad de la estructura CAN-Bus. Todos los accionamientos están conectados a la línea CAN, así como los transductores, los módulos I/O y el PC (Pentium 300 o superior). Los protocolos de comunicación son simplemente dos, uno para el programa operativo y secuencial que es igual para todos los modelos y uno para las señales I/O que, dependiendo de la dimensión de la maquina es diferenciado en función del modelo. Esta diferenciación facilita de una forma extremadamente simple la actualización del software operativo de la máquina, que puede ser puesto al día sin problemas y a cada nueva edición o mejora del mismo, cualquiera que sea el modelo para el que esa modificación haya sido estudiada.
Transmisión directa sin cintas dentadas
En este caso se utilizan exclusivamente accionamientos directos que proporcionan precisión y eficacia con los husillos sin fin, que si bien son mas costosos vienen avalados por muchos años de experiencia en las máquinas herramienta que introdujeron este sistema hace ya muchos años.
En vista de las notables cargas de trabajo a que se someten los componentes mecánicos en las máquinas de inyección, se ha decidido utilizar sinfines con circulación de esferas cerámicas, que no sufren calentamientos debido a las altas velocidades y disfrutan de una vida mucho mas larga.
Refrigeración por agua de los motores de accionamiento
Ausencia de lubrificante en el lado de la inyección
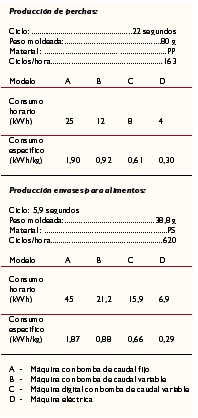
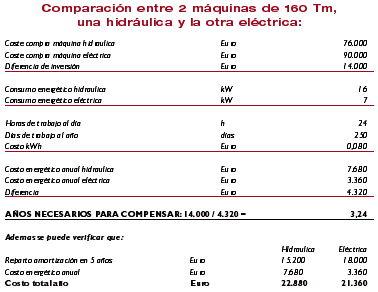
El consumo energético
Vamos a efectuar una comparación entre modelos equivalentes, que han sido puestos a trabajar en igualdad de condiciones de producción, de una máquina electromecánica con sistema hidráulico con bomba de caudal fijo, una máquina digital, con bomba de caudal variable y una máquina eléctrica. Con el condicionante de utilizar los mismos valores y el mismo producto en máquinas equivalentes pero de diferente tecnología, como hemos mencionado, se ha penalizado la máquina con mejores prestaciones y a pesar de eso se han obtenido resultados sorprendentes:
De estos datos se evidencia claramente que la sustitución de máquinas incluso producidas durante los años 90 está ya justificada únicamente evaluando el ahorro energético obtenido. Obviamente, las máquinas digitales con bomba de caudal variable, los modelos evaluados tienen prestaciones decididamente inferiores a las máquinas de accionamiento eléctrico que, además de la ventaja del consumo, aportan una mayor productividad y una mayor calidad y fiabilidad.
Valoración coste-beneficio
Esta comparación efectuada sobre la base del consumo necesario en la fabricación de envases producidos en ciclos de menos de 6 segundos se evidencia que, aparte la mejores condiciones técnicas de transformación y repetitividad, no se obtiene el mismo ahorro que en el caso de piezas técnicas de mayor ciclo de trabajo. Sin embargo se puede comprobar que la diferencia del precio de inversión ya se puede compensar durante el periodo habitual de amortización de una inyectora. Además deberemos adicionar las ventajas de una menor rumorosidad, mejor impacto ambiental, superiores prestaciones, etc., aunque a veces estas son cualidades difíciles de cuantificar y no siempre muy valoradas. Considerando sin embargo otras ventajas adicionales de la máquina eléctrica sobre la hidráulica (siempre comparando las versiones de 160 t), a las expuestas en la tabla anterior, podemos resumir que:
Otras ventajas a considerar por elementos o funciones eliminadas:
para una máquina hidráulica de 160 Tm
• Sustitución del aceite hidraul.
2,5/kg para 175 kg cada 10.000 horas.
• Sistema refrig. Aceite
4740 Fr/h que ocasionan un consumo de 2 kW/h
En este punto la valoración muestra una relación coste/ beneficio netamente favorable a la versión eléctrica como solución destinada a consolidarse en el futuro próximo pero afirmarse ya en el presente
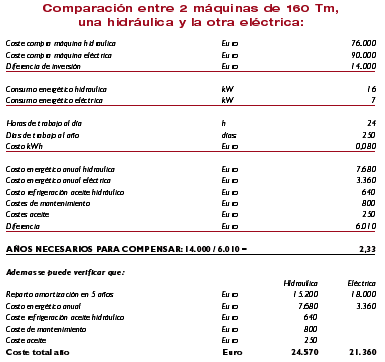