Entendiendo los alabeos y deformaciones en piezas inyectadas (Parte 2)
José Ramón Lerma, dpto. técnico de Biesterfeld Ibérica
14/12/2020En materiales semicristalinos se puede testar el nivel de cristalinidad, a nivel de taller, calentando las piezas inyectadas con molde frío (la temperatura dependerá de cada material) a niveles de temperatura donde el material pueda cristalizar. Si las piezas a la salida de este calentamiento han reducido sus medidas o se han alabeado, significa que se ha producido una post cristalización la cual no había tenido posibilidad de generarse durante el enfriamiento dentro del molde frío. Si el plástico alcanza una determinada temperatura que permita la movilidad de las moléculas del polímero, este intentará estructurarse como no pudo hacerlo debido a la baja temperatura del molde.
El efecto que provocamos en este calentamiento forzado para el test puede suceder en la vida real de una pieza en su aplicación o uso. Sucede que una pieza con baja cristalinidad obtenida en el proceso de inyección posteriormente en su aplicación, al alcanzar temperaturas que permiten esta post cristalización, se deforman y dejan de funcionar. Si son piezas funcionales con ajustes estrechos dejaran de funcionar, o se agrietan por estar fijadas, clipadas o atornilladas y no podrá eliminar el stress deformándose.
Es evidente que no es posible durante un proceso de inyección de plásticos y dentro de un proceso industrial obtener el máximo de cristalinidad que el material es capaz de obtener, ya que para ello, las temperaturas de molde y los ratios de enfriamiento deberían ser tales que no obtendríamos procesos productivos rentables.
Por ejemplo en laboratorio, cuando se hacen test de cristalinidad se puede enfriar el material a una velocidad de enfriamiento del orden de 10 a 20 grados por minuto, mientras que en un proceso, por ejemplo de inyección de POM a temperatura de masa fundida de 210 °C y con una temperatura de molde de 80 °C, temperatura muy por encima de su Tg que es de – 80 °C, si estamos enfriando la pieza durante 25 segundos antes de extraerla, podemos calcular que el ratio de enfriamiento aplicado ha sido de 312 grados por minuto, más de 30 veces más rápido que en el laboratorio. Sin embargo, con estas condiciones descritas el POM tendrá una suficiente estructura de cristales como para pensar que la pieza cumplirá con la aplicación y que no se deformará en su aplicación o vida útil.
Siguiendo con el ejemplo del POM, aquellos que han fabricado piezas con este material conocen bien el comportamiento de postcontracción que este material presenta. Esto hace que normalmente no se estabilicen las dimensiones y también las deformaciones finales hasta pasadas 24 – 48 horas de su fabricación, de esta manera se habrá obtenido cierto equilibrio estructural permanente que permitirá definir las cotas o dimensiones finales. Esto es debido al alto grado de cristalinidad de este tipo de materiales, del orden del 75%, que hacen que su estructura tienda a formar gran cantidad de cristalitas o esferulitas agrupándose las cadenas moleculares hasta alcanzar el equilibrio comentado.
En el caso de fabricar piezas con POM con moldes a temperaturas más bajas, las consecuencias son un bajo nivel de cristalinidad, menor nivel de propiedades mecánicas, y potenciales posteriores alabeos, grietas, etc.. debidas a la postcontracción producida en entornos de temperatura que permita el movimiento molecular.
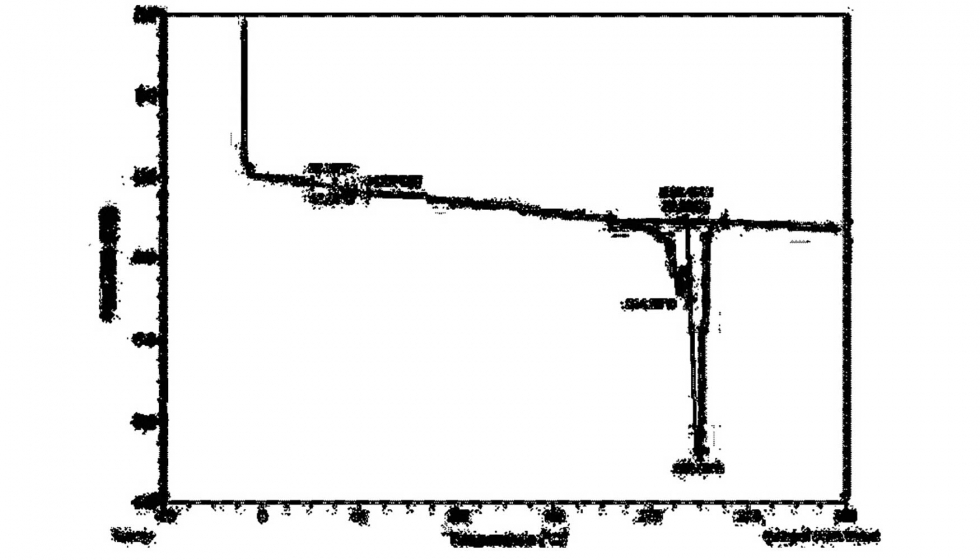
Ejemplo de gráfica de un DSC.
Este test básicamente se lleva a cabo con una muestra de la pieza inyectada en cuestión y se calienta en unas condiciones controladas hasta que la muestra llega a la fusión. La gráfica que genera este test indica con un pico la temperatura de fusión asociada a una propiedad denominada “calor latente de fusión".
El calor latente es la cantidad de energía requerida por una sustancia para cambiar de fase, de sólido a líquido (calor de fusión) o de líquido a gaseoso (calor de vaporización). Se debe tener en cuenta que esta energía en forma de calor se invierte para el cambio de fase y no para un aumento de la temperatura.
Latente, en latín, quiere decir escondido, y se llamaba así porque, al no notarse un cambio de temperatura mientras se produce el cambio de fase (a pesar de añadir calor), este se quedaba escondido.
Cuando se aplica calor a un trozo de hielo, va subiendo su temperatura hasta que llega a 0 °C (temperatura de cambio de estado). A partir de ese momento, aunque se le siga aplicando calor, la temperatura no cambiará hasta que se haya fundido del todo. Esto se debe a que el calor se emplea en la fusión del hielo. Una vez fundido el hielo la temperatura volverá a subir hasta llegar a 100 °C. Desde ese momento, la temperatura se mantendrá estable hasta que se evapore toda el agua.
En las gráficas DSC el pico de fusión indica el nivel de cristalinidad de la muestra. Cuanto mayor es el nivel de calor latente de fusión mayor nivel de cristalinidad teníamos en la estructura de la pieza moldeada.
Posteriormente, siguiendo con el ensayo DSC, una vez alcanzada la fusión, se enfría controladamente la muestra produciéndose en la gráfica un pico que tiende a ser un pico inverso o una imagen de espejo del pico de fusión de la gráfica, este pico invertido es el calor extraído por el proceso de cristalización.
Estos calentamientos y enfriamientos de la muestra borran la huella dejada, desde el punto de vista de la cristalinidad de la muestra, durante el proceso de inyección o moldeo.
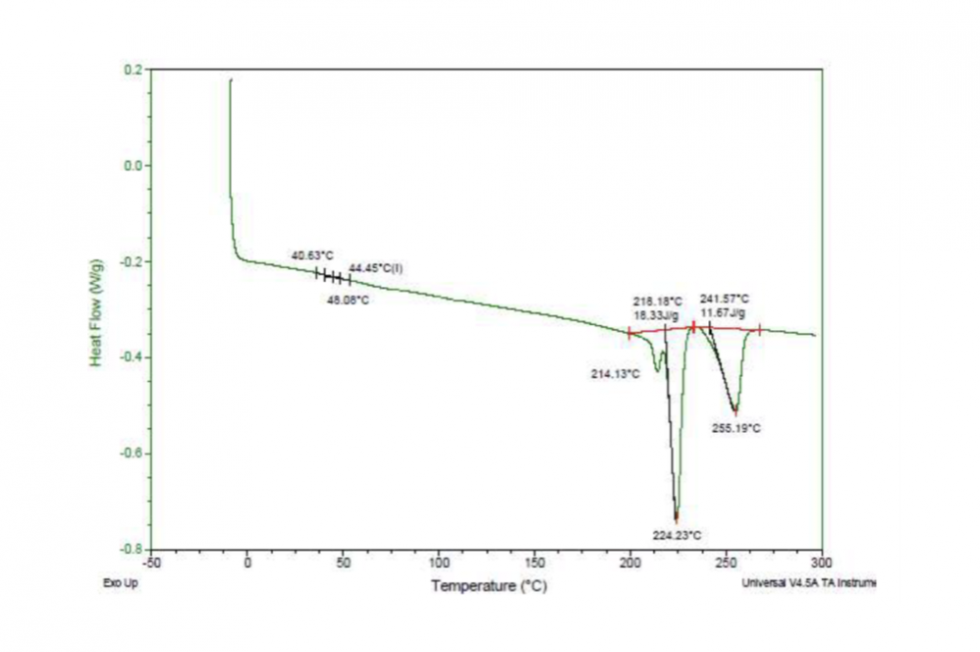
Cuando en el ensayo DSC se calienta una segunda vez la muestra anterior podremos observar que el pico de fusión de genera a la misma temperatura ya que es la temperatura de fusión del polímero, pero tendrá un pico mayor que el del primer calentamiento. Esto es debido a que durante el primer enfriamiento, hemos enfriado la muestra muy lentamente, mucho más que durante el proceso de inyección, y por tanto al material le ha sido posible generar un alto grado de cristalinidad que es lo que nos indica la curva con el pico de fusión mucho mas grande.
El ratio entre el calor de fusión del pico del primer calentamiento respecto al pico del segundo calentamiento no dará el porcentaje de cristalinidad obtenido en la pieza inyectada.
En el mundo industrial, como decía, no podemos enfriar las piezas inyectadas tan lentamente como en el ensayo DSC. Debemos estar en un compromiso entre estructura, funcionalidad, propiedades mecánicas y productividad, coste y competencia. Un ratio del orden del 90% de cristalinidad obtenida (porcentaje del 100% que permita cada material, no un 90% de cristalitas) es un ratio un valor correcto.
En materiales de ingeniería los porcentajes deberían estar en esos niveles, sin embargo en semicristalinos más 'commodity' como el PP los valores son mucho más bajos ya que tienen menos tendencia a cristalizar.
En conclusión, los bajos niveles de cristalinidad obtenida darán lugar a deformaciones posteriores, alabeos, roturas, mal funcionamiento, etc.
En el caso de los materiales amorfos, el alabeo o postdeformación suele ser menor dado su menor nivel de contracción. Esto hace que su equilibrio final este más cerca de las condiciones de salida de molde. En estos materiales la postcontacción es baja y no suele provocar deformaciones posteriores.
Es más frecuente observar alabeos causados en materiales amorfos (además del diseño) por la orientación viscosa molecular del polímero durante el llenado.
Durante el llenado, el gradiente de velocidad del polímero fundido, entre las cadenas moleculares que van por el exterior del frente de flujo, entrando en contacto con en acero de la cavidad y las cadenas moleculares que van por el centro del flujo. Estas últimas van a mayor velocidad, disminuyendo esta a medida que nos acercamos a la pared de la cavidad. Ese diferencial de velocidades, rápido en el centro y más lento en los extremos, hace que la cadenas moleculares choquen unas con otras, alineándose en la direccion del flujo debido a la influencia de este gradiente de velocidades.
Esta alineación es mayor cuanto más alta sea la velocidad de inyección. Este alineamiento u orientación en la direccion del flujo, si bien facilita el llenado de la cavidad, es una situación de no equilibrio de la masa fundida. Esta masa fundida a medida que se vaya enfriando intentará alcanzar el equilibrio y las cadenas moleculares empezarán a replegase y hacer unos ovillos desordenados, sin forma, entre ellas.
La capacidad de ordenación y relajación de estas tensiones de orientación molecular la controlamos también a través de la temperatura del molde.
Si congelamos esta relajación natural del polímero, las piezas tendrán un stress interno que en cualquier momento y en determinadas circunstancias serán liberadas, es lo que se denomina estrés de moldeo. Por ello, se recomienda permitir esta relajación. Igual que ocurre con los materiales semicristalinos, dentro de un proceso industrial, no podemos enfriar tan lentamente el material de modo que no seamos industrialmente competitivos pero no es recomendable ir demasiado deprisa para evitar o minimizar el estrés de moldeo.
Este estrés motivado por la orientación molecular puede ser muy acusado en zonas de estrechez de sección, donde el material se acelera mucho durante el llenado, en piezas con llenados a alta velocidad de inyección, en áreas cerca de las entradas, en zonas del molde con temperatura baja, etc.
Estas piezas moldeadas con estrés, además de que tendrán menos resistencia química, podrían deformarse a posteriori en la aplicación de uso si alcanzan determinada temperatura cercana a la Tg que permita a las moléculas relajarse y por tanto moverse.
En ocasiones se recurre al horneado, acondicionado o 'annealing' de piezas con stress para eliminar el mismo.
Este horneado acondicionado dependerá en temperatura y tiempo de cada material y del espesor de la pieza en cuestión ya que el calor aplicado debe llegar al núcleo de la pared de las piezas para que sea efectivo. Con este calentamiento controlado y la aplicación de la temperatura durante un tiempo y muy importante un enfriamiento controlado para permitir la relajación de las piezas podemos obtener piezas con un bajo nivel de stress para aplicaciones que lo requieran.
Este tipo de acondicionamiento o 'nnealing' es aplicable también cuando tanto materiales semicristalinos como amorfos han pasado por una fase de mecanizado. Estos mecanizados aplican tensión y calor en zonas muy concretas de las piezas generando estructuras con estrés que requieren esta operación comentada de annealing para eliminarlo.
José Ramón Lerma es autor de los libros: 'Libro Manual Avanzado de Inyección de Termoplástico', que tiene como objetivo ser, por un lado, una herramienta para la formación y, por otro, un manual de ayuda para todo el personal de una empresa de inyección de plásticos y, del recientemente editado, 'Scientific Injection Molding Tools. Productividad a través del dominio del proceso'. Ambas publicaciones, comercializadas por Plásticos Universales / Interempresas (libros@interempresas.net), consta de detallados casos prácticos, amplia información de moldeo científico y un ‘pendrive’ con 20 hojas de cálculo y herramientas de SC Molding o Scientific Injection Molding, además de optimización y definición de proceso, lo que lo hacen único en el mercado. Página web sobre Scientific Injection Molding: www.asimm.es